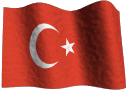
Info about the "Rocket Launchers"...
LAU - 3...
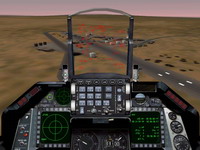
Click on the pic for larger size...
General Info...
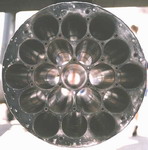
Launchers convey and provide a suitable platform from which rockets are carried and launched. The Navy 2.75 Inch Rocket
System uses the 19 round LAU-61C/A and LAU-69 series, and the seven round LAU-32 series and LAU-68 D/A rocket launchers.
These reusable launchers have an external thermal coating that greatly prolongs cook-off protection time. Full production
of these launchers began in June 1985. In the US Army, these Hydra 70 rockets are fired from the AH-64A Apache/AH-64D
Apache Longbow using M261 19-tube rocket launchers, while the Air Force uses the LAU-130/A Rocket Launcher. The AH-1G
Cobra and the UH-1B "Huey" used M200 19-tube rocket launchers. The F-5 Tiger II carried the LAU-3, which is also currently
carried by the AV-8B Harrier II.
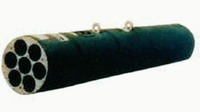
The LAU-61C/A (19 rounds) rocket launcher is thermally coated. The launcher can be fired in single (one at a time) or
ripple (one after the other in multiple shots) mode. In ripple mode, the LAU-61C/A can fire 19 rounds in about one second.
There are no service life requirements on the launcher. The launchers are mated mechanically to the aircraft by way of
suspension lugs. The 2.75 Inch Rocket launchers use 14-inch suspension. Electrical connection between the aircraft and
the launcher is made through an electrical receptacle located on top of the launcher center section to the aircraft’s 28
volt armament circuit. The launchers may be shipped and stored pre-loaded with rocket motors. The launchers are a
cylindrical construction of 19 aluminum launch tubes. These launch tubes are held together with metal ribs and are
covered by an aluminum skin. Launchers can be fitted with forward and aft frangible fairings depending on overall rocket
length and fuzing for airborne configuration.
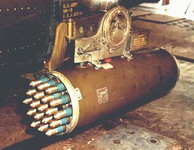
The U.S. Army Lightweight Launchers (LWL) are the M260, 7-tube and the M261, 19-tube launchers. The aluminum launchers are
inexpensive enough to be disposable, yet durable enough to be reused after as many as 32 firings. The weight savings over
the previous Army launchers allows the Army to add other features to the aircraft's rocket system for improved performance.
The launcher permits fuze-timing selection from the cockpit and will launch rockets using either the MK 40 or the MK 66
motors. The aft end of each tube in the launcher is fitted with a pivoting igniter arm which imparts the ignition current
from the firing switch to the rocket motor. A side contact is lowered inside the launch tube for MK 66 ignition with the
actuation of the pivoting arm. When the rocket is fired, the igniter arm is pushed back and a mechanical link assists in
releasing the rocket from the rocket retainer. However, the primary mode of release is rocket override of the retainer in
the launcher. The rocket retention force is specified to be between 170 and 600 pounds, easily overridden by the rocket
thrust of over 1300 pounds.
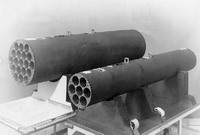
Weight saving was achieved for the LWL design by minimizing the use of rivets, welding and adhesive. Instead, the launchers
are assembled using electromagnetic force to swage the aluminum skin and tubes around the four bulkheads. The center two
bulkheads are welded to the aluminum strongback. This strongback establishes the rigidity of the launcher and is designed
in accordance with MIL-A-8591 for interface with aviation suspension racks and sway braces. The 19-tube launcher has since
been redesigned to implement a floating solid bulkhead at the front of the launcher. This solid bulkhead was necessary to
minimize the warping from heat built up during ripple launches. All other bulkheads are a laminated stack of plates. The
front bulkhead of the 7-tube launcher continues to use a laminated stack.
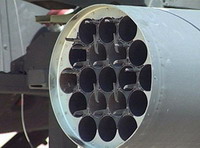
Electrical connectors are referred to as J1 and J2 connectors. The J1 connector (P/N 13048761 is a 26-pin connector for the
motor ignition circuit and the J2 (P/N 13048762) is a 23-pin connector for the fuze setting circuit. The firing interval
that the launcher normally experiences from the fire control is 0.06 seconds. Environmental Protection Devices (EPD) have
been designed to protect loaded launchers in flight from collecting ice and debris which can cause a rocket to stick in the
tube, a condition that can result in a hangfire. The EPDs are molded from an ABS plastic in one piece and mount to the face
of the launcher with captive bolts. The EPD effectively protects each tube with a dome cover that is grooved on the surface
for fragmentation upon rocket exit. Fragments are designed to not exceed one square inch and can be ingested without event
by the turbine engines of the Apache helicopter. A side benefit of the EPD is the thermal protection for the launcher face
to prevent warping, which eventually will lead to erosion of the launcher tubes. This also will minimize the heat signature
of the launcher after rocket firings.
Fuel Tanks...