Recommended Design Criteria for Sedimentation...
General Considerations...
Sedimentation is a process used for various stages within a wastewater treatment plant to reduce the concentration of settleable and suspended matter. Sedimentation tanks, commonly referred to as clarifiers, are described as primary, intermediate and final clarifiers dependent upon the process stage. Primary clarifiers are installed to reduce organic loadings and floatables to the downstream treatment processes. Intermediate and/or final clarifiers are utilized after biological treatment processes to separate chemical and/or biological floc from the treatment process.
1. Multiple units capable of independent operation shall be provided for plants having an average design capacity greater than 0.1 MGD unless temporary removal of a single unit from service for repairs will not result in an adverse
effect to the quality of the receiving stream.
2. Clarifiers shall be arranged to facilitate operating flexibility and maintenance, assure continuity of treatment,
and ease of installation of future units.
3. Provision shall be made for dewatering and bypassing each unit independently. The bypass should provide for redistribution of the wastewater to an appropriate point in the remaining process units. Due consideration shall be given
to the possible need for hydrostatic pressure relief devices to prevent structure flotation.
4. Effective flow measurement devices and controls shall be provided to permit proper flow distribution to each unit.
5. The anticipated flow pattern should be considered in the selection of clarifier configurations and location and
type of inlets and outlets. Consideration should be given to flow equalization.
6. Primary clarifiers are required prior to trickling filters and rotating biological contactors (RBC). Bar screening and comminution are not suitable as the sole means of primary treatment.
Design Considerations...
1. Performance : Unless laboratory and/or pilot plant data are available, primary settling shall be assumed to
remove one- third of the influent BOD and 55 percent of the influent suspended solids. It is not recommended to return
waste activated sludge to the primary clarifier. This sludge should be returned to the aeration basin or a separate
thickener unit.
2. Inlets : Inlets should be designed to dissipate the inlet velocity, to distribute the flow uniformly and to
prevent short-circuiting. Provisions shall be made for removal of floating materials in inlet structures having submerged ports. Orifices placed in walls at the inlets should be sized to produced velocities from 0.5 to 1.0 fps. Orifices passing wastewater containing floc should not be smaller than 0.3 to 0.5 inches, to minimize floc breakup.
3. Dimensions :
a. The minimum distance from the influent inlet to effluent weirs shall be at least 10 feet for all clarifier configurations unless special provisions are made to prevent short-circuiting. The sidewater depth (SWD) of mechanically cleaned clarifiers shall not be less than 7 feet for primary clarifiers and those following fixed film reactors. Final clarifiers shall have sidewater depths of at least 10 feet and those following an activated sludge process shall have sidewater depths of at least 12 feet. If depth limitations due to ground conditions are less than the minimum recommended, the overflow rate should be reduced by 100 gpd/sq.ft. for each foot of sidewater depth under the recommended for clarifiers. It is preferable that the sludge collector scraping mechanism be at least 6 feet below the water level. Clarifiers having depths less than recommended will be considered on a case-by-case basis.
b. The length-to-width ratio for rectangular clarifiers should be equal to or greater than 4 to 1.
c. The maximum horizontal velocity in a rectangular clarifier shall not exceed 5 feet per minute near the sludge layer in a primary clarifier and 2 feet per minute in a final clarifier.
4. Channels :
a. Inlet channels should be designed to maintain a velocity of at least one foot per second at one-half design flow. Where minimum velocities are less, provisions shall be made for the resuspending of the solids. Corner fillets or channeling shall be provided to eliminate corner pockets and dead ends.
b. Width of effluent channels should be at least 1.0 foot. Bottom of the channels at the outlet structures shall be at least equal to or above the water levels of the downstream treatment units. The effluent channel shall be sized to prevent weir submergence at the peak hourly flow. The bottom of effluent channels should be at least one foot below water levels maintained in the clarifiers, except for small package plants.
5. Freeboard : The outer walls of clarifiers shall extend at least 6 inches above the surrounding terrain or 100-year flood plain and shall provide at least 12 inches of freeboard to the water surface. Where clarifier walls do not extend 4 feet above the surrounding terrain, a cover, fence, wind screen or suitable barrier shall be provided to prevent high wind currents and debris from entering the clarifier and ice buildup which inhibits scum removal and settling.
6. Baffling and Scum Removal :
a. Scum baffles shall be provided around and prior to all effluent weirs. The baffles shall be located at the water surface to intercept all floating materials and scum. Baffles shall extend at least 3 inches above the weir plate elevation and 12 inches below the water surface.
b. Circular clarifiers shall be provided with symmetrical baffling, a minimum of 6 inches inside the weir plate, to distribute the flow uniformly in all radial directions. In a circular center-feed clarifier, the inlet baffle should have a diameter of 15 to 20 percent of the clarifier diameter and should not extend more than 3 feet below the water surface. With 100 percent recirculation, circular center-feed clarifier inlet baffles should not be less than 20 percent of the clarifier diameter and have a depth of 55 to 65 percent of the SWD. The maximum inlet velocity to a center inlet well should not
exceed 3 feet per second. The outflow velocity should not exceed 15 feet per minute. In a circular peripheral-feed
clarifier, the inlet baffles shall extend at least 12 inches below the flowline of the inlet and shall be located above
the sludge blanket zone at a distance where the critical horizontal velocity will just begin to produce scour.
c. Rectangular clarifiers shall be provided with inlet ports or pipes and baffles for uniform distribution of flow across the clarifier and effluent weirs. The baffles shall extend across the width of the clarifier and upstream to the effluent weirs.
d. Effective scum collection and removal facilities, including baffling, shall be provided ahead of the effluent weirs on all clarifiers. Provisions should be made for disposal of scum with the sludge; however, other special provisions for disposal of scum and floating materials may be necessary.
e. A scum pit shall be located outside of the clarifier but adjacent to the scum collection point and located on the side of the clarifier opposite the prevailing wind direction. Provisions should be made for mixing the contents of the scum pit with such equipment as a mechanical mixer or air diffusion.
7. Submerged Surfaces : The topside of beams, troughs or similar construction components shall have a minimum slope
of 1.4 vertical to 1 horizontal; the underside of such components shall have a slope of 1 to 1 to prevent the accumulation
of scum and solids.
8. Weirs :
a. Weir plates shall be adjustable for leveling and sealed against the effluent channel. Weirs shall be located to optimize actual hydraulic detention time and minimize short circuiting.
b. Circular clarifiers, with peripheral-feed or center-feed inlets, shall be provided with a full weir. Effluent launders may be placed at points other than at the periphery. The minimum water depth below effluent weirs located near the center should be 10 feet and 12 feet if weirs are located at the periphery. These minimum water depths need not be provided for small clarifiers having low weir and surface-loading rates.
c. Double weirs to increase the length are permissible if installed sufficiently in-board for good separation of flow
to minimize velocity problems at the periphery. Experimently, circular weir troughs placed at 2/3 to 3/4 of the radial distance from the center is the optimum position to intercept well-clarified effluent. The weir length of double weirs
shall be computed as double the length of the centerline of the launder.
d. Weirs should be of the saw-tooth or serpentine type to allow for better weir overflow and flow distribution.
e. To determine the spacing of multiple weirs in rectangular clarifiers, the upflow velocity near the weir should be limited to approximately 12 to 24 feet per hour. If weirs are located at end walls in rectangular clarifiers, the minimum water depth below the effluent weir should be 12 feet.
f. Weir Loadings : ( 1 ) Weir loadings should not exceed 10,000 gallons per day per lineal foot for primary, intermediate or final clarifiers at peak hourly flows unless select design parameters are considered; (such as, depth, surface area, detention time, horizontal and/or vertical velocities, solids density) then the higher weir loadings may
be considered. Hydraulic loading criteria in clarifier design should be based on the sum of plant inflow and recycle rates.
( 2 ) Weir loadings at peak hourly flows should not exceed 15,000 gallons per day per lineal foot for primary or
intermediate clarifiers; and should not exceed 10,000 gallons per day per lineal foot for final clarifiers in plants with average design flows of 1.0 MGD or less. ( 3 ) Weir loadings at peak hourly flows in plants with average design flows
larger than 1.0 MGD should not exceed 20,000 gallons per day per lineal foot for primary and intermediate clarifiers; and should not exceed 15,000 gallons per day per lineal foot for final clarifiers. ( 4 ) Rectangular primary clarifiers with
end weirs shall not exceed a weir loading of 80,000 gallons per day per lineal foot at peak hourly flow. Intermediate and final rectangular clarifiers with launder and weir at the outer wall shall not exceed a weir loading of 20,000 gallons per day per lineal foot at peak hourly flow. ( 5 ) If pumping is required, weir loadings should correspond to the pumping rates to prevent short circuiting.
9. Detention Time : Nominal detention periods should be in the 2 to 3 hour range at the average design flow rate including consideration for recirculation. Detention periods in clarifiers vary with surface-loading rates and sidewater depths. Detention periods for various surface-loading rates and depths varies as follows :
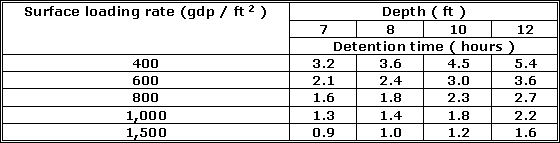
The detention periods for final clarifiers following various activated sludge processes shall be adjusted between 2 and 4 hours dependent upon the type of process, design flow, recirculation rate, and surface- loading rate.
10. Surface-Loading Rates :
a. Primary Clarifiers : Surface-loading rates for primary clarifiers should not exceed 1,000 gallons per day per
square foot at average design flow and shall not exceed 1,500 gallons per day per square foot at peak hourly flow.
Primary clarifiers not followed by secondary treatment should not exceed 600 gallons per day per square foot for plants
with average design flows of 1.0 MGD or less.
b. Intermediate Clarifiers : Surface-loading rates for intermediate clarifiers should not exceed 1,000 gallons per
day per square foot at average design flow. Clarifiers following fixed film reactor processes shall not exceed 1,500
gallons per day per square foot at peak hourly flow.
c. Final Clarifiers : ( 1 ) Surface-loading rates for final clarifiers following fixed film reactors should not exceed 800 gallons per day per square foot at average design flow and shall not exceed 1,200 gallons per day per square foot at
peak hourly flow. ( 2 ) Surface-loading rates for final clarifiers following activated sludge processes, such as : conventional, step aeration, contact stabilization or the carbonaceous stage of separate-stage nitrification, shall not exceed 1,200 gallons per day per square foot at peak hourly flow. ( 3 ) Surface-loading rates for final clarifiers
following an extended aeration process shall not exceed 1,000 gallons per day per square foot at peak hourly flow. ( 4 ) Surface-loading rates for final clarifiers following separate-stage nitrification shall not exceed 800 gallons per day per square foot at peak hourly flow. ( 5 ) Surface-loading rates recommended for various floc suspensions at peak hourly flow
are as follows :
Alum floc - 600 gpd / ft2
Iron floc - 800 gpd / ft2
Lime floc - 1,200 gpd / ft2
( 6 ) Tests should be conducted whenever a pilot plant study is warranted because of unusual waste characteristics,
treatment requirements or where design loadings exceed those limits set forth in this section.
11. Solids Loading Rate :
a. The solids loading rate, excluding chemical additives applied to final clarifiers, shall not exceed 25 pounds per square foot per day at peak flow rate with 100 percent recirculation. Clarifiers following an extended aeration process or
an oxidation ditch should not exceed this loading rate.
b. The solids loading rate for final clarifiers following most activated sludge processes shall not exceed 50 pounds
per square foot per day at peak hourly flow. The designer should assure that the clarifier area is equal to or greater than that required by surface-loading or solids loading rates based on the maximum sludge volume index (SVI) anticipated or mixed-liquor suspended solids (MLSS). The solids-loading rate for an activated-sludge clarifier may be computed by dividing the total solids applied by the surface area of the tank as follows :
L SOLIDS kg MLSS / m 2 . hour = ( C MLSS kg / m 3 ) ( v SURFACE
m 3 / m 2 . hour ) ( In metric units )
The solids-loading rate is expressed in pounds per square foot per hour in order that the factor is evaluated for both
peak hourly and design average flow conditions to determine which values may govern in a 24-hour period. Due consideration must be given to the duration of peak hourly flows.
12. Sludge Storage :
a. The floors of circular clarifiers shall be sloped at one-inch per foot (1:12) to form an inverted cone to a central sludge hopper. Floors of sludge thickners should be sloped 2:12 or greater. Simple mechanical collectors are recommended
over the suction or siphon type since rapid recirculation of solids is not required.
b. The floor of a rectangular clarifier should be sloped at approximately 1 percent (1:100) toward the cross collectors or sludge hopper(s) located at the influent end. If a header type suction sludge removal mechanism is used, then the slope should be sufficient only to provide for drainage.
c. The sludge or settled solids in clarifiers shall be scraped or drawn to a hopper or sump appropriately located for removal. Where cross-collectors or screw conveyors are not provided, multiple hoppers shall be installed for rectangular clarifiers or multiple clarifiers.
d. The minimum slope of the side walls of sludge hoppers shall be 1.7 vertical to 1.0 horizontal. Hopper bottoms shall have a maximum dimension of 2 feet. Hopper walls shall be smooth with rounded corners. Extra depth sludge hoppers for sludge thickening are not permissible.
e. Vertical sludge draw-off systems shall be considered on a case-by-case basis.
f. Sludge draw-off pipes located on the side or bottom, shall be flush with the hopper bottom. Each sludge hopper shall have an individually valved sludge draw-off line that is at least 6 inches in diameter, if gravity flow, and, if pumped, 4 inches in diameter. The static head available for withdrawal of sludge shall be at least 30 inches to maintain a three foot per second (3 fps) velocity when removal is dependent upon gravity flow.
Sludge Handling and Withdrawal...
1. Mechanical sludge collection and withdrawal equipment is required and shall provide complete and continuous removal of settled sludge for intermediate and final clarifiers. The sludge collection equipment and the drive assembly shall be designed to withstand the maximum anticipated loads of transporting sludge to a hopper. The peripheral speed for circular flight mechanisms should be in the range of 0.02 to 0.05 revolutions per minute but shall not exceed 8 feet per minute in final clarifiers. The straight line flight speed should be in the range of 2 to 4 feet per minute but shall not exceed 1
foot per minute in final clarifiers.
2. Positive displacement pumps shall be provided for pumping primary sludge intermittently and continuously. A
positive head should be provided on pump suctions. If motor driven return sludge pumps are used, the maximum return sludge capacity shall be obtained with the largest pump out of service. Pumps shall have at least 3 inch suction and discharge openings. Automatic controls shall be provided to separately activate sludge pumps and sludge collection mechanisms.
Sludge pumping in large plants should be controlled by timers and valve activators to provide continuous "on-off"
operation. A means of measuring the sludge withdrawal rate shall be provided for each unit. It is recommended that sludge-pumping stations have a standby pump and serve two or more units. Air lift systems for sludge removal shall not
be used for removal of primary sludges. Air lift pumps should be at least 3 inches in diameter and be designed with a
minimum of 80 percent static submergence.
3. Rapid sludge withdrawal pipes shall return sludge to a sludge well at the water surface that enables visual observation of the flow. The return sludge withdrawal pipes shall be at least 4 inches in diameter with a hydraulic differential between the clarifier water level and the return sludge well level sufficient to maintain a velocity of 3 feet per second. The discharge piping should be designed to maintain a velocity of at least 2 feet per second when return sludge facilities are operating at normal return sludge rates. Each sludge withdrawal pipe shall be accessible for rodding or backflushing when the clarifier is in operation. Cleanouts and couplings shall be provided in sludge piping to facilitate pipe cleaning and removal of pumping equipment. High points in piping shall be provided with air releases. All sludge piping shall be metallic material.
4. Sludge recirculation from the secondary clarifier to the aeration basin shall be variable within 25 to 100 percent
of the average design flow. Sludge wasting from the activated sludge process may be from the mixed liquor or the return sludge. Sludge wasting shall be variable to enable zero wasting to 50 percent of the total system solids daily.
5. The minimum permissible return sludge rate of withdrawal from the final clarifier is a function of the
concentration of suspended solids in the mixed liquor (MLSS) entering it, the sludge volume index (SVI) of these
solids, and the detention time that these solids are retained in the clarifier. The rate of sludge return for
activated sludge processes expressed as a percentage of the average design flow of wastewater should generally be
variable between the limits set forth as follows :

6. The rate of sludge return shall be varied by means of variable speed motors, drives, or timers to pump sludge as
set forth in this section.
7. Waste sludge control facilities should have a maximum capacity of not less than 25 percent of the average rate of wastewater flow and function satisfactorily at rates of 0.5 percent of average wastewater flow or a minimum of 10 gallons
per minute, whichever is larger.
8. Sludge wells/scum pits shall be provided adjacent to the basin and equipped with suitable devices for viewing, sampling and controlling the rate of sludge withdrawn. Metering devices shall be installed and located to indicate flow
rates of all influent and effluent points, return sludge and waste sludge lines. Meters shall be accurate to within + 5 percent of the actual flow rates.
Safety and Servicing...
1. All clarifiers shall be equipped with appropriate safety features for the protection of operators. Such features shall include drive mechanism enclosures, life lines, lighting, stairways, walkways, handrails, deck gratings and slip-resistent surfaces. Effluent pipes larger than 12 inches in diameter shall be provided with bars to prevent entry of
an operator if a fall should occur.
2. If side walls are extended some distance above the water level to provide flood protection or for other purposes, convenient and safe walkways must be provided to facilitate housekeeping and maintenance. For plants having an average
design capacity greater than 0.1 MGD, meters shall totalize and record.
3. Clarifier facilities shall include a convenient and safe means of access to routine maintenance items such as baffles, weirs, channels, scum equipment, gear boxes and pumping facilities. Hoisting or other means of equipment removal shall be provided. As a safety precaution, it is recommended that telescoping valves with tees and blow-off valves at the base be provided in sludge wells to unplug draw off lines.
4. Pressurized wash water facilities shall be provided for washing scum boxes, tanks and other equipment. Potable wash water facilities may be used but shall have backflow preventors. If wash water is non-potable, all outlets shall be permanently posted to indicate water is not safe.
5. Electrical equipment and controls shall comply with the National Electrical Code for Class I, Groups C and D, Division l locations. The equipment, fixtures, lighting, and controls shall be located to provide convenient and safe
access for operation and maintenance. A positive means of locking out each mechanical device shall be provided.
6. Treatment plant operators should be supplied with a complete set of operation procedures, including maintenance schedules, tools, sampling equipment and spare parts as may be necessary.
7. Due consideration shall be given to the selection of materials because of corrosive conditions present.
Deviations From Design Criteria...
The Department may consider and allow deviations where adequate documentation is provided to prove the need for such deviation.