Activated Sludge Process - 6...
Extended Aeration Activated Sludge Plant...
By : Jay Blevins...
I. Activated Sludge - Extended Aeration (General)...
The activated sludge process is the biological process by which non-settleable substances occurring in dissolved and colloidal forms are converted into settleable sludge which is removed from the liquid carrier (water). At a plant the activated sludge is settled out along with the suspended solids present in the wastewater. The activated sludge process provides one of the highest degrees of treatment obtainable within the limits of practical economy and present knowledge
of the art and science of waste treatment.
The process depends upon groups of microorganisms, mainly bacteria, along with protozoan, fungi and rotifers, being
maintained in contact with the organic matter in the waste in an aerobic (oxygen containing) environment. Many forms of organic matter carried in the wastewater serve as a food supply for these microorganisms. The mass of microorganisms
present in the system is referred to as biological solids or mixed liquor suspended solids (MLSS).
In practice, MLSS represents all suspended matter in the activated sludge system including inert matter, non-biological
organic matter, as well as active microorganisms. The basic reactions involve the breakdown of the organic matter (represented by 5 day Biochemical Oxygen Demand - BOD5) and the formation of cell mass (activated sludge) and by-products (carbon dioxide and water).
The basic purpose of the activated sludge system is to establish and maintain a viable population of microorganisms by supplying food (BOD5) and the proper environment. In the proper environment the microorganisms convert the
soluble and colloidal material present in the wastewater into new cells (activated sludge) and end products (CO2 and water). During their life cycle, the microorganisms undergo a continuously changing cycle of growth and decline.
Figure 1 given below shows an ideal growth curve for microorganisms growing in a batch activated sludge system. A batch system is one in which a specific volume is placed under aeration in a container with no inlet or outlet; therefore there is no flow through the system. A batch system is contrasted to a continuous system in which new liquid is continuously added to
the system and an equal volume is withdrawn.
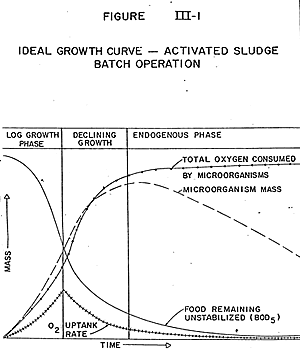
Figure 1 shows that the ideal growth curve is divided into 3 major phases: logarithmic growth phase, declining growth
phase, and the endogenous phase. This type of curve would develop if 100 mL of activated sludge were added to a liter of wastewater and the mixture was aerated for a given length of time.
The first phase indicated on Figure 1, the logarithmic growth phase, shows that the population of microorganisms increases
rapidly during the initial period of contact with the waste (microorganisms go into an eating and multiplying frenzy). There is a proportional increase in the rate of oxygen consumed by the microorganisms and the amount of food (BOD5) present in the wastewater decreases rapidly. During the logarithmic growth phase there is a high food to microorganisms
ratio (F/M). That is to say, the BOD5 concentration measured in the system is much greater than the MLSS
concentration and the F/M is greater than 1. In this phase of growth the emphasis is on production of new microbial cellular material (increase in activated sludge mass). The total oxygen requirements for the biological mass are smallest during this phase but are continuously increasing.
The second phase indicated in Figure 1 is that of declining growth. As the microorganisms continue utilizing the food
supply, a point is reached where the amount of food remaining limits the growth rate of the microorganisms (number of new cells). Essentially there are too many microorganisms and not enough food to maintain them. This phase begins at the point
of change in curvature on both the food and microorganisms curve. At this point the F/M is exactly equal to 1. The growth rate of the microorganisms as well as their oxygen utilization begins to taper off. This phase marks the beginning of a period when the remaining live organisms starts to cannibalize the nutrients available in their dead neighbors. The living organisms must work harder to obtain food, requiring more energy, with the result that more end products are produced.
In this phase the amount of new cell producing from the food and complete oxidation of the food to end products for energy for the existing microorganisms are becoming equal. The total amount of oxygen consumed is obviously greater, as seen from the curve.
The final phase indicated in Figure 1 is the endogenous phase which begins when the amount of food used in producing energy
and forming end products is greater than the amount used in forming new cellular material. The food to microorganism ratio
is much less than 1 and indicates the beginning of starvation for the microorganisms that are not strong enough to obtain their food requirements. More and more end products are being produced while the production of activated sludge cell mass
is at its minimum rate. The rate of oxygen utilization decreases in this phase while the total amount of oxygen consumed obviously reaches its largest total value.
In actual operation the activated sludge process is run as a continuous process. The growth process just described in
Figure 1, however, is a batch process. Therefore, Figure 1 must be modified in order to apply it to the actual activated sludge process occurring at the sewage treatment plant.
Figure 2 is the modified growth curve for a continuous microbiological system and can be applied to the activated sludge
process. The curve shows that for a particular modification of the activated sludge process (i.e. high rate, conventional, extended aeration) the plant theoretically operates at one given point on the curve. Therefore, the plant would
theoretically operate at one particular food to microorganism ratio and one particular detention time in the aeration
chamber. Unfortunately, due to the normal variations in sewage flow and strength during the day, it is almost impossible
to run a plant at a single point on the curve. The best that can be accomplished is to hold the process within a given
range of operating F/M ratios. The narrower the range about the optimum F/M ratio, the more efficiently the process will operate. This plant works in the range indicated by "Extended Aeration" on Figure 2.
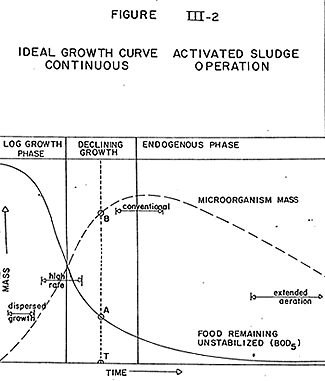
Since the plant will be operating in the endogenous phase, the production of cell matter will be at a minimum, thereby
producing a minimum of excess sludge to be wasted from the system. The actual range of values of F/M which will produce the best plant operation is determined by measuring the activated sludge unit response. Therefore, the range of F/M's to use is that which produces the least BOD5 and suspended solids in the effluent while producing sludge with good settling characteristics.
When operating in the proper F/M range, the activated sludge will flocculate and settle well while the BOD5
removal through the plant will also be at a maximum. Any deviation from the proper F/M range will make it difficult to operate and control the plant. The microorganisms will not be help under the proper environmental conditions for which the plant was designed, causing bulking sludge or other operational problems. The F/M ratio required for proper plant operation is controlled by measuring BOD5 and MLSS and adjusting the MLSS by sludge wasting until the proper ratio of food to microorganisms is obtained. In actual practice this ratio can be related with other more rapid measurements than 5 day
BOD test (i.e. COD - Chemical Oxygen Demand).
It is obvious that there are many conditions to be met to insure proper plant operation. The following conditions are
essential to insure that the microorganisms present in the floc or activated sludge are in a state of proper growth and, therefore, working at maximum efficiency.
- A continuous supply of sewage with a uniform and nutritionally adequate organic content. A highly variable organic load
to the plant would be undesirable.
- A complete mixing of incoming wastewater and the microorganisms present in the aeration basin (diffused aeration).
- A continuous supply of dissolved oxygen as supplied by the blower (diffused aeration).
- A settling tank (clarifier) where separation of mixed liquor solids from the liquid carrier is completely and
efficiently carried forth.
The extended aeration process has been shown to run properly at an F/M ratio of 0.042 to 0.153 lbs BOD5/lb of MLSS. Experience has also shown that the MLSS range should not fall below 2,500 mg/L or exceed 6,000 mg/L. Therefore, for
the design case of 240 mg/L influent BOD5, the MLSS concentration should be within the range of 2,500 mg/L to
5,700 mg/L. This corresponds to an F/M range of 0.042 to 0.096.
Previous experience with extended aeration plants has shown that plants that fed domestic sanitary sewage will require only periodic sludge wasting. At a plant there are two ways to determine when to waste solids :
- Waste when F/M ratio falls out of desired range.
- Waste when analysis of suspended solids in plant effluent shows a deterioration in effluent quality.
Of these two methods, determination of F/M ratio provides more information on biological behavior while analysis of plant effluent provides information on plant efficiency. Therefore, it is suggested that both determinations be made and used for solids control.
II. Specific Activated Sludge Plant Information...
The activated sludge system is embodied in the aeration chambers and clarifiers. the preliminarily treated wastewater is pumped to the activated sludge system by the lift station. Flow is normally split to the 2 chambers according to the
position of the baffle plate in the flow splitter box at the influent end of the unit. An equal division of flow to the 2 chambers is achieved when the baffle plate is oriented perpendicular to the adjacent wall of the aeration chambers.
Within each aeration chamber the incoming wastewater is intimately mixed with the active biological mass and provided with the necessary dissolved oxygen by the action of the air bubbles released from the diffusers. These diffusers are located at the center (toward the center wall) and cause a spiralling flow pattern to develop which rolls the chamber contents from
the influent to effluent end. Each chamber ought to be sized to produce 24 hours of aeration detention at the design
flow.
At the end of the aeration period the wastewater biological mass mixture (mixed liquor) reaches the effluent end of the chamber and flows in a trough to the clarifier. Here the suspended solids (MLSS) and liquid are separated by gravity. The separated solids are returned to the aeration compartment as return sludge while the liquid flows over weirs into the chlorine contact tank for disinfection. Foam control sprays are provided to control frothing in the aeration chamber and skimmers are provided to remove floating material from the surface of the clarifiers.
The settled sludge and scum are returned to the aeration chambers by air lifts. Figure 3 presents a simplified flow diagram of the activated sludge system.
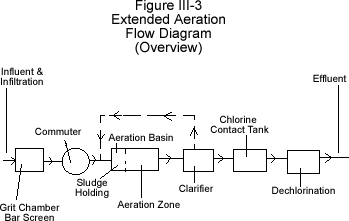
The extended aeration system is quite simple in concept. The maintenance of a favorable environment for the activated sludge (oxygen and complete mixing) and good solids separation (clarifier) are readily accomplished. The MLSS is a well operating system and should have a brown color and settle well, and have an earthy odor.
III. General Design Criteria...
Based upon flow and organic loading the design factors determining the size and volume of an activated sludge unit are the aeration volume, the total mixed liquor volume necessary to handle the biological load, and the clarification area required to obtain solids separation.
Since this unit is an extended aeration system, its BOD5/MLSS (F/M) loading is in the range of 0.042 to 0.153. Under normal conditions an average range of 0.042 to 0.096 should be used. The optimum ratio of F/M for the system must be determined by direct operation of the unit and evaluation of the results. This F/M ratio establishes the MLSS concentration in the range of 2,500 to approximately 6,000 mg/L.
Aeration compartment volume has been established to provide a detention period of 24 hours at design flow. This volume, in turn, determines the BOD5 loading to the plant at 15 lbs. BOD5/day.1,000 cu.ft. This loading is
within the normal range for extended aeration plants.
The clarifiers have been sized to produce solids separation under all hydraulic loading conditions. A good overflow rate is 520 GPD/sq ft at design flow.
Air is supplied to the diffusers by positive displacement blowers. These blowers were designed to provide sufficient air to ensure that the dissolved oxygen content of the aeration chambers can always be maintained within the range of 1.0 to 2.0 mg/L.
IV. Common Operating Problems...
The following are problems an operator could encounter in the operation of an extended aeration activated sludge plant, together with brief descriptions of the solutions. The importance of evaluating laboratory results, combined with good
common sense, cannot be overstressed.
Bulking and Rising Sludge...
Bulking sludge is evidenced by expansion of MLSS in the clarifier. Sludge appears brown in color but will not settle. The sludge volume index (SVI) increases until values well above 100 are reached. To solve this problem the laboratory data, air supply records, plant flows, etc., should be evaluated to ascertain the cause. Any conditions found to vary from typical normal values experienced should be corrected. The bulking can be corrected if the underlying cause is found and the unit
is properly maintained. In addition to normal test result logs and data sheets, it has been found that long term (1 month
or longer) charts and graphs of such things as SVI, Effluent SS, DO, F/M, and a mix of organisms will help in determining
the problems.