Trickling Filter - 3...
A trickling filter consists of a bed of highly permeable media on whose surface a mixed population of microorganisms is developed as a slime layer. The word "filter" in this case is not correctly used for there is no straining or filtering action involved. Passage of wastewater through the filter causes the development of a gelatinous coating of bacteria, protozoa and other organisms on the media. With time, the thickness of the slime layer increases preventing oxygen from penetrating the full depth of the slime layer. In the absence of oxygen, anaerobic decomposition becomes active near the surface of the media. The continual increase in the thickness of the slime layer, the production of anaerobic end products
next to the media surface, and the maintenance of a hydraulic load to the filter, eventually causes sloughing of the slime layer to start to form. This cycle is continuously repeated throughout the operation of a trickling filter. For economy and to prevent clogging of the distribution nozzles, trickling filters should be preceded by primary sedimentation tanks
equipped with scum collecting devices.
Primary treatment ahead of trickling filters makes available the full capacity of the trickling filter for use in the conversion of non-settleable, colloidal and dissolved solids to living microscopic organisms and stable organic matter temporarily attached to the filter medium and to inorganic matter temporarily attached to the filter medium and to inorganic matter carried off with the effluent. The attached material intermittently sloughs off and is carried away in the filter effluent. For this reason, trickling filters should be followed by secondary sedimentation tanks to remove these sloughed solids and to produce a relatively clear effluent.
Construction and Design...
The primary factors that must be considered in the design of trickling filters include: (1) the type of filter media to be used, (2) the type and dosing characteristics of the distribution system, and (3) the configuration of the underdrain system.
Filter Media...
The ideal filter medium is a material that has a high surface area per unit volume, is low in cost, has a high durability, and does not readily clog. The choice of filter media is more often governed by the material locally available which may include field stone, gravel, broken stone, blast furnace slag and antracite stones. Stones less than one inch in diameter do not provide sufficient pore space and may therefore result in plugging of the media and ponding. The tendency is to use larger sizes with 2 1/2 inches in diameter now considered the minimum size. Large diameter stones tend to avoid ponding situations but also limit the surface area per unit volume available for the slime layer to grow. An upper size limit of about 4 inches is therefore recommended.
Distribution System...
The rotary distributor has become standard for the trickling filter process because of its reliability and ease of
maintenance. The rotary distributor consists of a hollow vertical center column carrying two or more radial pipes or arms, each of which contains a number of nozzles or orifices for discharging the wastewater onto the bed. All of these nozzles point in the same direction at right angles to the arms and the reaction of the discharge through them causes the arms to revolve. The necessary reaction is furnished by a head of 18" to 24". The speed of revolution will vary with the flow rate, but it should be in the range of one revolution in 10 minutes or less for a two-arm distributor. A dosing tanks and siphon should be provided for standard rate trickling filters to shut off the flow when the head falls below that necessary to revolve the arms at the required speed. In some cases positive drive mechanisms are being
used.
A clearance of 6 to 9 inches should be allowed between the bottom of the distributor arm and top of the bed. This will
permit the waste streams from the nozzles to spread out and cover the bed uniformly, and it will also prevent ice accumulation from interfering with the distributor motion during freezing weather.
Fixed spray nozzles were used when trickling filters were first developed. The nozzles were attached to pipes laid in the filter medium and were fed intermittently from a siphon controlled dosing tank. By this method, wastewater is applied to the filter for short periods of time. Between applications the filter has rest periods while the dosing tank is filling. Many types and shapes of nozzles were developed and the siphon dosing tank was designed to attain the best possible even
distribution of wastewater over the entire surface of the filter. At best, the distribution was not even and there were
areas of the filter on which very little wastewater was sprayed.
In addition, due to the greater number of nozzles used for the distribution of the wastes, clogging and increased
operational and maintenance problems were encountered.
Underdrain System...
The underdrain system in trickling filters serves two purposes: (a) to carry the wastewater passing through the filter and the sloughed solids from the filter to the final clarification process, and (b) to provide for ventilation of the filter to maintain aerobic conditions. The underdrains are specially designed vitrified clay blocks with slotted tops that admit the wastewater and yet support the media. The blocks are laid directly on the filter floor, which is sloped toward the
collection channel at a 1 to 2 percent gradient. Since the underdrains also provide ventilation for the filter it is desirable that the ventilation openings total at least 20% of the total floor area. Normal ventilation occurs through convection currents caused by a temperature differential between the wastewater and the ambient air temperature. In deep filters or heavily loaded filters, there may be some advantage in force ventilation.
Filter Classification...
Trickling filters are classified by hydraulic or organic loading, as high-rate or low-rate.
The organic load on a filter is the BOD content in pounds applied to the filter. This is usually expressed as pounds of BOD per day per 1,000 cubic feet of filter medium or pounds of BOD per day per acre foot. The hydraulic load, including recirculation flow if used, is the gallons of flow per acre of filter surface per day.
Low-rate filters are relatively simple treatment units that normally produce a consistent effluent quality even with varying influent strength. Depending upon the dosing system, wastewater is applied intermittently with rest periods which generally do not exceed five minutes at the designed rate of waste flow. With proper loadings the low-rate trickling filter,
including primary and secondary sedimentation units, should remove from 80 to 85 percent of the applied BOD. While there is some unloading or sloughing of solids at all times, the major unloadings usually occur several times a year for
comparatively short periods of time.
High-rate filters are usually characterized by higher hydraulic and organic loadings than low-rate filters. The higher BOD loading is accomplished by applying a larger volume of waste per acre of surface area of the filter.
One method of increasing the efficiency of a trickling filter is to incorporate recirculation. Recirculation is a process by which the filter effluent is returned to and reapplied onto the filter. This recycling of the effluent increases the contact time of the waste with the microorganisms and also helps to "seed" the lower portion of the filter with active organisms.
When recirculation is used, the hydraulic loading per unit area of filter media is increased. As a result, higher flow velocities will usually occur causing a more continuous and uniform sloughing of excess growths. Recirculation also helps
to minimize problems with ponding and restriction of ventilation.
Recirculation can be continuous or intermittent. Return pumping rates can either be constant or variable. Sometimes
recycling can be practiced during periods of low flow to keep the distributors in motion, to prevent the drying of the
filter growths, and to prevent freezing during colder temperatures. Also, recirculation in proportion to flow may be
utilized to reduce the organic strength of the incoming wastes, and to smooth out diurnal flow variations.
Recirculation can be accomplished by various techniques. Some of which are as follows :
Biofilter...
The bio-filter is a high-rate filter, usually 3 to 4 feet in depth, employing recirculation at all times. The recirculation in this case involves bringing the effluent of the filter or of the secondary sedimentation tank back through the primary settling tank. The secondary settling tank sludge is usually very light and can be continually fed back to the primary settling tank where the two types of sludges are collected together and pumped to the digester.
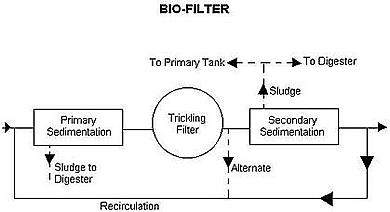
Accelo - Filter...
The accelo-filter includes recirculation of unsettled effluent from the filter back to the inlet of the filter
distributor. It is used for both low-rate and high-rate filters, the former being applicable if a well nitrified effluent
is required.
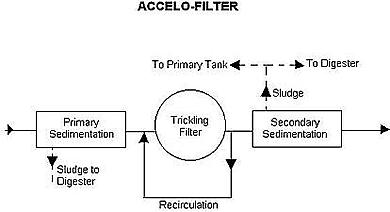
Aero Filter...
The aero-filter is still another process which distributes the wastewater by maintaining a continuous rain-like application of the wastewater over the filter bed. For small beds, distribution is accomplished by a disc distributor revolving at a
high speed of 260 to 369 rpm set 20" above the surface of the filter to give a continuous rain-like distribution over the entire bed. For large beds a large number of revolving distributor arms, 10 or more, tend to give more uniform
distribution. These filters are always operated at a rate in excess of 10 million gallons per acre of surface area per day.
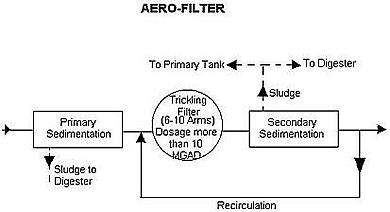
High-rate trickling filters, including primary and secondary sedimentation, should, under normal operation, remove from 65
to 85 percent of the BOD of the wastewater. Recirculation should be adequate to provide continuous dosage at a rate equal to or in excess of 10 million gallons per acre per day. As a result of continuous dosing at such high rates, some of the solids accumulated on the filter medium are washed off and carried away with the effluent continuously.
High-rate trickling filters have been used advantageously for pretreatment of industrial wastes and unusually strong wastewaters. When so used they are called "roughing filters". With these filters the BOD loading is usually in excess of 110 pounds of BOD per 1,000 cubic feet of filter medium.
Generally, most organic wastes can be successfully treated by trickling filtration. Normally food processing, textile, fermentation and some pharmaceutical process wastes are amenable to trickling filtration.
Some industrial wastewaters which cannot be treated by trickling filtration are those which contain excessive concentration of toxic materials, such as pesticide residues, heavy metals, and high acidic and alkaline wastes.
Since the organisms growing on the media are temperature dependent, climatic changes will affect the filter's performance. The organisms metabolic rate increases with increasing temperature and warmer weather. Therefore, higher loadings and
greater efficiencies are possible in warmer temperatures and climates, if aerobic conditions can be maintained in the
filter.
Common Problems...
Due to its simple design, in actual operation the trickling filter is one of the most trouble-free types of secondary treatment processes. It requires much less operating attention and process control than the activated sludge system, but
some problems do exist. The following is a summary of some of the more common problems and cures :
Ponding...
Ponding is normally the result of : (a) excessive organic loading without a corresponding higher recirculation rate, (b)
use of media which is too small, (c) clogging of underdrain system, (d) non-uniform media size or breaking up of media,
and (e) trash or debris in filter voids. Ponding can cause odors and decrease filter efficiency.
Minor Ponding : can be eliminated by :
- Spraying the surface with high pressure water hose.
- Stirring or agitating ponding area with stick, rake, etc.
- Dousing the filter with chlorine. Applying chlorine to a ponding filter by chlorinating at the dosing tank to produce a residual of about one to two mg/L at the nozzles may help reduce ponding. Chlorination is continued until the filters are free. There may be some deterioration of efficiency of the filters during chlorination. Obviously, if ponding is caused by the size of the media, chlorination will be of no benefit. If the ponding is caused by overloading, chlorination may be of temporary benefit. If ponding was caused by excessive growths, this deteriorating condition will usually not return until conditions, such as temperature, that caused the excessive growth are repeated.
- Flooding filter and keeping the media submerged for approximately 24 hours will sometimes cause the growth to slough. Growths become anaerobic and tend to release from media.
- Shutting off the flow to the filter. The growths will die and tend to be flushed out when the unit is put back into service.
Odors...
Since the trickling filter is an aerobic process, no serious odors should exist. If foul odors are present, anaerobic conditions are the most likely cause. Anaerobic conditions usually predominate next to the media surface. If the surface
of the slime growth is aerobic, odors should be minimal. If odors are present, corrective action should be taken immediately or the condition could get worse. Some corrective measures are :
- Try to maintain aerobic condition in the collection system and in the primary treatment units.
- Check the ventilation of the filter for clogging and stoppages.
- Check the underdrain system for clogging and stoppages.
- Increase recirculation rate; this usually provides added oxygen to the filter and may increase sloughing.
- Keep wastewater in filter; do not allow it to splash on exposed surfaces, weeds, or grass.
- Add odor-masking agents.
- Pre-chlorination at primary tank influent or at the dosing tank. The dose used is not sufficient to produce residual chlorine but only to destroy the odors. Chlorination to a residual of less than 0.5 mg/L normally does not interfere with
the activity of the living organisms and thus does not affect the purification obtained by the operation of a trickling
filter. However, chlorination of a trickling filter influent cannot be used until after the filter has been in active operation. Except in a large plant, the chlorine dose is generally set at about half the chlorine demand and not adjusted
for moderate variations in flow or strength.
- Induce unloading of a trickling filter. A shock dose of chlorine that will produce a residual of about 10 mg/L in the filter influent may be applied. It requires a fairly large dose of chlorine to produce this amount of residual. As it is
only to be maintained for a short period of time, it is most economical to apply during the night when the flow is low and the chlorine demand at a minimum. The chlorine is applied at the dosing tank, generally by making a slurry of liquid
hypochlorites and pouring it into the dosing tank. Two dosing discharges containing 10 mg/L residual are generally enough
to cause the filter to unload the next day. A word of caution - when a filter is made to unload it does so quickly if at all and a very large volume of secondary sludge is produced in one or two day. Addition of this large quantity of sludge to the digesters has caused foaming on occasions.
It should be noted that sometimes during hot weather odors will be noticeable even from a filter in good operating condition. This problem can be eliminated by the use of masking agents.
Filter Flies...
They are a nuisance to plant personnel and nearby neighbors. These tiny, gnat-size flies are called psychoda. They are occasionally found in great numbers, preferring an alternate wet and dry environment for development. The flies are most frequently found in low or standard rate filters with an intermittent dosing system. Control can be accomplished by :
- Increasing recirculation. A continuous waste flow to the filter will tend to wash fly larvae from the filter.
- Flushing the side walls of the filter by opening the flap valve at the end of the distributor arm.
- Flooding the filter intermittently to prevent completion of the fly life cycle. This life cycle can be as short as seven days in warm weather. Filters should be flooded for approximately 24 hours.
- The addition of chlorine, which is toxic to the flies and larvae.
- Keeping the plant grounds neat, clean and free from excessive weeds, plants, and grass, which are excellent breeding grounds for the flies.
Weather Problems...
Cold weather can cause an occasional build-up of ice on the media, walls, distributor arms and orifices, resulting in operating problems and loss of efficiency. During cold temperatures, the organism's metabolic process slow down and as a result efficiency decreases. Measures which can be implemented to reduce cold weather problems are :
- Decrease the recirculation rate to prevent splashing at distributor arm, but maintain sufficient flow to keep the filter working.
- Adjust orifices at splash plates to reduce the spraying effect.
- Construct wind screens or covers to reduce heat loss.
- Break up any ice build-up.
- Partially open flap gates at end of distributor arm to allow for a stream of water rather than a spray of water.