Sludge Recycling & Wasting...
Return Activated - Sludge Control...
The purpose of the return of activated sludge is to maintain a sufficient concentration of activated sludge in the aeration
tank so that the required degree of treatment can be obtained in the time interval desired. The return of activated sludge
from the final clarifier to the inlet of the aeration tank is the essential feature of the process. Ample return sludge
pump capacity should be provided. It is also important to prevent the loss of sludge solids in the effluent. The solids
form a sludge blanket in the bottom of the clarifier. The sludge blanket varies in thickness from time to time and
may fill the entire depth of the clarifier at peak flows, if the return sludge - pumping capacity is inadequate. Return
sludge - pumping capacities of 50 to 100 % of the wastewater flowrate are normally provided for large
plants and up to 150 % of the wastewater flowrate for small plants.
Several techniques are used to calculate the desirable return - sludge flowrate. The control strategies are based on either
maintaining a target MLSS level in the aeration tanks or a given sludge blanket depth in the final clarifiers.
The most commonly used techniques are ; (1) settleability, (2) sludge - blanket level control, (3) secondary clarifier mass
balance, (4) aeration tank mass balance and (5) sludge quality.

Settleability Test...
Using the settleability test, the return sludge - pumping rate is set so that the flowrate is approximately equal to the
percentage ratio of the volume occupied by the settleable solids from the aeration tank effluent to the volume of the
clarified liquid after settling for 30 minutes in a 1,000 mL graduated cylinder. Another settleability test
method often used to control the rate of return - sludge pumping is based on an empirical measurement known as SVI.
Sludge Blanket Level...
With the sludge blanket level control method, an optimum sludge blanket level is maintained in the clarifiers. The optimum
level is determined by experience and is a balance between efficient settling depth and sludge storage. The optimum depth
of the sludge blanket usually ranges between 30 to 90 cm.
Mass Balances...
The return sludge - pumping rate may also be determined by making a mass balance analysis around either the settling tank
or the aeration tank.
"Aeration Tank Mass Balance"...
"Secondary Clarifier Mass Balance"...
"Total Mass Balance"...
Sludge Quality...
Still another approach to return sludge control entails determining the sludge settling characteristics. Sludge settleability
curves are developed from which return sludge rates are determined.
Remote Control of Return - and Waste Activated Sludge...
The performance of most activated sludge plants mainly depends on the efficiency of the biological stage. The suspended solid
content of activated sludge, sludge volume, as well as the age of sludge plays an important role. The conventinal methods of
evaluating suspended solid and sludge volume by taking samples and laboratory analysis are subject to major time delays, and
therefore not usable for control. In addition to that the control becomes dependend on the operator.
Remote Control by MLSS and Sludge Blanket Level Measurements...
A constant percentage of return activated sludge is adjusted based on measuring the inflow of the sewage plant. Here a
changing concentration of biological substance in the areation basin and in the return activated sludge is not taken into
account. Better is the adjustment of a constant suspended solid content in the areation basin. Basing on a permanently
working suspended solid measurement in the areation basin, the amount of return activated sludge is adjusted by a step -
by - step control. In order to consider time delay in the event of rainfall, it is now useful to implement also the signal
of the inlet flow as feed - forward. That means that the control signal, which results from the measurement of suspended
solid, is effected by inflow measurement. This has the advantage, that also in cases of fluctuating inflow and changing
sludge, a constant amount of biological mass in the areation basin is available.
"Return & Waste Activated Sludge Control - 1"...
The discontinuous outlet of waste sludge can be realized according to the amount of suspended solids in return activated
sludge. The waste activated sludge pumps can be activated per suspended solid limit switch. However, a possible sludge
emission out of the secondary clarifier in case of bad settling characteristics remains unconsidered. A continous measuring
of suspended solid in the return activated sludge pipe offers also the possibility to use the signal for the optimization
of return activated sludge control. Continuously operating sludge level detection systems on the scraper bridge of the
secondary clarifier detect the sludge level. The waste sludge pumps are activated by min. / max. limit switch. Measuring
systems which provides additional to the height signalalso of an signal for suspended solid offer the possibility of
frequently monitoring a concentration profile. The settling of the sludge in the secondary clarifier becomes transparent.
Remote Control by MLSS and Sludge Volume Measurements...
Control of return activated- and waste activated sludge refering to suspended solid in the areation basin, as well as sludge
volume become more and more popular. The reason for this is, that the two stage plants (denitrification, nitrification)
requires also a certain age of sludge. The sludge volume has a relationship to sludge age.
"Return & Waste Activated Sludge Control - 2"...
Plug Flow with Recycle...
The distinguishing feature of this recycle system is that the hydraulic regime of the reactor is of a plug - flow
nature. In a true plug - flow model, all the particles entering the reactor stay in the reactor an equal amount of time.
Some particles may make more passes through the reactor because of recycle, but, while they are in the tank, they will
pass through in the same amount of time.
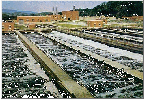
A kinetic model for the plug-flow reactor of which schematic representation is shown below, can be obtained by two
assumptions ; (1) the concentration of microorganisms in the influent to the reactor is approximately the same as that
in the effluent from the reactor and (2) the rate of substrate utilization as the waste passes through the reactor is
given by the following expression :
"Plug - Flow Reactor with Cellular Recycle"...
"Substrate Utilization"...
Sludge Wasting...
Sludge Wasting Alternatives...
The excess activated sludge produced each day must be wasted to maintain a given food - to - microorganism ratio
or mean cell - residence time. The most common practice is to waste sludge from the return sludge line because it
is more concentrated and requires smaller waste sludge pumps.
"Sludge Wasting Alternatives"...
The waste sludge is discharged to thickening tank, or to dewatering units such as belt filter, press filter. An alternative
method can be used to withdraw mixed liquor directly from the aeration tank or from the aeration tank effluent pipe, where
the concentration of solids is uniform.
Wasting Flowrate...
The actual amount of liquid that must be pumped to achieve process control depends on the method used and the location from
which the wasting is to be accomplished. In addition, because the solids capture of the sludge - processing facilities is
not 100 percent and some solids are returned, the actual wasting rate will be higher than the theoretically determined
value. If the mean cell - residence time is used for process control and wasting is from the sludge return
line, the waste sludge flowrate must be computed using equation shown below.
"Waste Sludge Flowrate - 1"...
If the mean cell - residence time is used for process control and wasting is from the aeration tank, the
rate of pumping can be estimated using the following relationship.
"Waste Sludge Flowrate - 2"...
If the food - to - microorganism method of control is adopted, the wasting flowrate from the sludge return
line can be determined using the following relationship.
"Waste Sludge Flowrate - 3"...
If process control is based on one of the other loading criteria, the quantity of solids to be wasted must be established
by successive trials.
Process Control with SCADA...
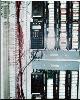
SCADA is an acronym for Supervisory Control And Data Acquisition. It is a technology which allows the treatment plant
operator to get continuous information on the plant's processes and to exercise programmatic control over those processes.
For example, a bar screen can be programmed to operate more frequently under high influent flow conditions, or a valve
actuator can be made to maintain a certain flow through a flow meter. SCADA systems can also log real-time data for later
reference. Historical data is very important to the treatment plant operator. It is used to help understand the plant's
operating characterics, and how it responds to changing conditions.