Sludge Digestion...
Aerobic Sludge Digestion...
Aerobic digestion may be used to treat waste sludge from extended aeration plants. Aerobic digestion has been used
primarily in plants of a size less than 0.2 m3/sec. Advantages claimed for aerobic digestion as
compared to anaerobic digestion are as follows ; (1) volatile solids reduction is approximately equal to that obtained
anaerobically, (2) lower BOD concentrations in supernatant liquor, (3) production of an odorless, humus - like,
biologically stable and product, (4) recovery of more of the basic fertilizier values in the sludge, (5) operation is
relatively easy and (6) lower capital cost. The major disadvantages of the aerobic digestion process are that ; (1) a
high power cost is associated with supplying the required oxygen, (2) a digested sludge is produced with poor mechanical
dewatering characteristics, (3) the process is affected significantly by temperature, location, and type of tank
material and (4) a useful by - product such as methane is not recovered.
As the supply of available substrate is depleted, the microorganisms begin to consume their own protoplasm to obtain
energy for cell maintenance recations. When this occurs, the microorganisms are said to be in the endogenous
phase. In actuality, only about 75 to 80 % of the cell tissue can be oxidized, the remaining is composed
of inert components and organic compounds that are not biodegradable.
"Cell Oxidation"...
Two proven variations of the process are most commonly used ; (a) conventional aerobic digestion and (b) high - purity
oxygen aerobic digestion. Two other variations, thermophilic aerobic digestion and cryophilic digestion, have been
investigated, but few full - scale facilities are in operation.
"Design Criteria for Aerobic Digesters"...
Anaerobic Sludge Digestion...
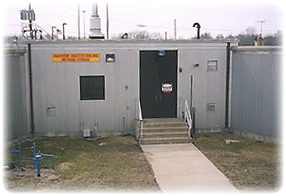
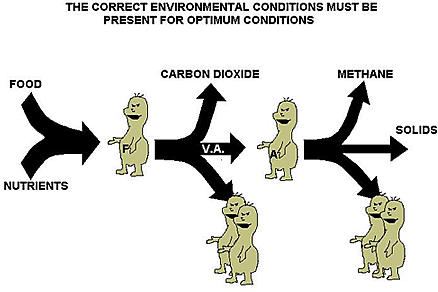
Anaerobic sludge digestion...
The design of anaerobic sludge digestion processes should be based on an understanding of the fundamental principles of
biochemistry and microbiology. Because these principles have not been appreciated fully in the past, a number of emprical
methods have also been used in the design of digesters. Methods are based on ; (1) the concept of mean cell - residence
time, (2) the use of volumetric loading factors, (3) observed volume reduction and (4) loading factors based on population.
"Flow - Chart of the Anaerobic Sludge Digesting"...
Mean Cell - Residence Time...
The respiration and oxidation end products of anaerobic digestion are methane gas and carbon dioxide. The quantity of
methane gas can be calculated using equation given below :
"Quantity of Methane Gas"...
For a complete - mix high - rate digester without recycle, the mass of biological solids synthesized daily, can be
estimated using equation shown below :
"Synthesized Biological Solids"...
Suggested mean cell - residence times for use in the design of complete - mix digesters are listed below :
"Mean Cell - Residence Times"...
Loading Factors...
Although a number of different factors have been proposed, the two that seem most favored are based on ; (1) the kilograms
of volatile solids added per day per cubic meter of digester capacity and (2) the kilograms of volatile solids added per
day per kilogram of volatile solids in the digester. The recommended solids loadings for standard - rate digesters
are from 0.5 to 1.6 kg/m3.day of volatile solids. For high - rate digesters, loading rates
of 1.6 to 4.8 kg/m3.day of volatile solids and hydraulic detention times of 10 to 20
days are practicable. Mixing has proved to be a problem at sludge loading rates greater than about 4.0
kg/m3.day. The effect of sludge concentration and hydraulic detention time on the volatile solids
loading factor is listed in the table given below :
"Volatile Solids Loading Factor"...
Volume Reduction...
If the supernatant is withdrawn and returned to the head end of the treatment plant, the volume of the remaining sludge
decreases approximately exponentially.
"Volume of Digester"...
Population Criteria...
Detention times range from 10 to 20 days for high - rate digesters and 30 to 60 days
for standard - rate digesters. These detention times are recommended for design based on total tank volume plus
additional storage volume, if sludge is dried on beds and weekly sludge drawings are curtailed because of inclement
weather.
"Design Criteria"...
Design...
Anaerobic digestion tanks are either cylindrical, rectangular, or, egg - shaped. The most common design is a low, vertical
cylinder and egg - shaped.
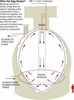
Why egg - shaped ?...
Cylindrical tanks are seldom less than 6 m or more than 40 m in diameter. They should have a water depth of
not less than 8 m at the sidewall and may be as deep as 15 m or more. The purpose of the egg - shaped design
is to eliminate the need for cleaning. Other advantages cited for the egg - shaped design include better mixing, better control of the scum layer, and smaller land area requirement.
Operational Steps in Digester Starting...
Two general methods of start - up usually are considered. Both have been used successfully and both have sound basis in
theory. The first of these might be called controlled natural process and the second the pH control process.
The controlled natural process might be better suited for starting a digester in a plant where close laboratory control is
difficult. The pH control method would appear to need closer laboratory control.
Controlled Natural Process : (1) These procedures are recommended either for starting a new digester or for
restarting a sour one. However, if an existing sour digester is to be restarted, it is recommended that the
contents be removed completelt and that the inside bottom and walls be cleaned throughly. (2) Use the least starting
volume available. In a multiple tank installation, start the digestion in one tank only. In a floating cover installation
fill the tank only sufficiently to float the cover. Use fresh raw wastewater or water for filling if digesting seed sludge
is not available. (3) Initially heat the added sewage or water to 35 °C and maintain temperature within +- 1.7 °C
throughout the period of the starting process. (4) Seeding culture is recommended if available; it will hasten the start
of the normal digestion. Recommended seed quantity is about 0.5 % (dry weight) of weight of liquid in the tank or
about 15 % by volume. (5) Raw sludge feed should be no more than 10 percent of the anticipated ultimate
daily load each day. When the gas produced is about 50 percent of that calculated to be available normally from
the volatile solids added and the volatile acids do not rise sharply, increase the feed by 50 to 100 % of
the initial daily feed until the ultimate design load is reached. (6) Recirculate tank contents daily. (7) Make volatile
acids determinations daily before adding feed. Continue daily analyses until the design load is reached. If volatile acid
concentrations show a continued increase, or if digestion does not start, reduce or interrupt feed of raw sludge. (8)
Measure and record gas production daily. Check the CO2 content of the gas. The volume of gas collected
should be about 0.6 m3/kg added in raw feed per day. The CO2 ultimately should be between
30 and 35 % by volume. (9) After one digester is operating properly at its design load, digested sludge
and overflow liquor then can be used to seed other tanks in a multitank system. (10) Digestion usually is established
within 30 to 40 days in this manner.
pH Control Process : (1) These procedures can be used either for starting a new digester or for restarting
a sour one. It usually is not considered necessary to empty the sour sludge for this process in restarting a unit.
(2) For a new digester fill the tank with fresh raw wastewater or water and bring the temperature up to about 35 °C.
Maintain this temperature +- 1.7 °C until digestion is established. (3) When raw sludge is added, also add hydrated lime.
The raw sludge feed probably would be less than the design load at first, but full loads are usually possible within
30 to 40 days. (4) When a mass of sour sludge already exists in a restarting situation lime should
be added to bring the pH up to 6.8 to 7.0 prior to addition of more raw sludge. (5) During the daily feeding
of raw sludge, use 4.5 to 6.8 kg of lime per 1,000 connected population, or more importantly, just enough to
maintain the pH at 6.8 to 7.0. It is important that mixing be complete so that false low pH readings will
not result in excess lime addition. Lime should be added in a slurry form. (6) Recirculate the sludge mass daily.
The entire tank contents should be overturned from bottom to top. (7) Keep a constant check on the pH at as many points
in the tank as is possible so that it is reasonably certain that the 6.8 to 7.0 range is maintained throughout
the sludge mass. (8) Digestion usually is established within 30 to 40 days. However, if too much lime was
used many upsets can occur over a period of several months.