Biofilm Process - 1...
Biofiltration Packings...
Introduction...
As aquaculture slowly shifts to more intensive farming methods, the use of biofiltration becomes more common. Broadly
stated, the purpose of biofiltration is to help maintain water quality. There are many different methods of maintaining
good water quality and biofiltration is only one component of the total picture. It is, however a very important and essential component especially for recirculating systems.
Biofiltration has the ability to accomplish the following functions :
1. Convert ammonia to nitrites and then to nitrates and finally to nitrogen gas
2. Remove BOD
3. Add oxygen
4. Remove carbon dioxide
5. Remove excess nitrogen and other inert gasses
6. Remove turbidity and clarify the water
7. Remove various organic contaminants
Most aquaculture biofilters are designed for the purpose of converting and removing ammonia and nitrites from the system.
All of the other process may or may not occur depending on the design and operation of the filter and the rest of the
system.
There are literally dozens of different types of biofilters used for aquaculture applications. While many have common features, some are fundamentally different from the rest. The purpose of this article is to educate the reader about the types of packings used for fixed film biofilters.
The type of biofilter under discussion is a filter that employs a non-moving surface area to provide a substrate for
various bacteria to attach and grow. The substrate remains in place while the water flows through the system. The heart
of these biofilters is the packing or media used to provide the surface area. The type of packing used strongly influences both the capital and operating costs of the biofilter.
It is important to emphasize however, that the packing merely provides surface area for bacteria to colonize. It is the bacteria that do the actual work of the biofilter. In order for the bacteria to do their job effectively, the biofilter and packing design must provide an even distribution of nutrients and oxygen while removing dissolved and suspended waste products. Most biofilters utilize aerobic bacteria but it is also possible to design and operate anaerobic systems for special purposes.
The technology used for fixed film biofilters is not unique to aquaculture. While some minor application details are different for aquaculture, the solutions to efficient and economical water quality management have been identified and developed by several other industries. The intent of this article is to acquaint the aquaculture practitioner with the
pros and cons of the various types of packings that are available for biofiltration.
Characteristics of the "Ideal Packing"...
Since the heart of any biofilter is the packing or filter media, it is useful to describe the characteristics of the
ideal or perfect packing. In practice, some characteristics may be mutually exclusive and it may be necessary to trade off one feature for another. The following list contains most of the pertinent features of a good biofiltration media.
( 01 )High specific surface area - Specific surface area is the measure of how much biologically active area is contained
in a given volume. Typical units of measurement are square feet per cubic foot or square meters per cubic meter. Specific surface areas vary widely but generally speaking, most packings will fall between 30 and 250 sq.ft./cu.ft. or 100 and 820 m2/m3. Specific surface area is often referred to as the "packing density".
It is important to distinguish between total claimed surface area and surface area that is available as a substrate for biological growth. Surface area that is contained in very fine crevices or pores may not always be available to living organisms. As a biofilter matures, the biomass of bacteria steadily increases and the layer of bacteria that covers all available surfaces becomes thicker. Since the organisms inside the layer can only receive food and oxygen by diffusion,
they receive less and less food and oxygen as the layer grows thicker. Generally speaking, only the outermost layer of bacteria will be operating at peak efficiency.
If the layer of bacteria becomes thick enough, the inside of the layer may become anaerobic. When this happens, the layer will lose adhesion to the substrate and can be sloughed off. If the dead bacteria is contained in a small crevice, it can
not be sloughed off and it will be retained within the biofilter. This can add to the overall load on the biofilter.
The total surface area available for bacterial growth is a good predictor of the capacity of the biofilter to convert ammonia. The specific surface area is an important variable that influences the cost of the biofilter vessel and support mechanisms. If packing A has twice as much surface area per unit volume as packing B then packing B will need a vessel twice as large to accomplish the same task as packing A. From an economic standpoint it makes sense to use the smallest vessel possible to accomplish a given task. Provided there are no other overriding factors, using a packing with most surface area per unit volume will allow the vessel costs to be minimized.
( 02 ) High void fraction - Void fraction is the percentage of open space or volume in the packing. To phrase it another
way, void fraction is the space not occupied by the packing itself. Void fractions vary from 15% to 98%. High void
fractions allow free and unrestricted flow of water or air and water. A modern packing for aquaculture applications should have a void fraction of 90% or greater.
( 03 ) Large free (or clear) passage diameter - The best way to understand free passage diameter is to imagine a marble or ball bearing being dropped through the packing. The size of the largest ball that will pass through the packing is the free passage diameter.
( 04 ) Resistance to plugging or clogging - This parameter is very important but difficult to quantify. Plugging or
clogging of a filter can happen through mechanical trapping of particles in the same way a screen or other particulate
filter works. Plugging can also result from the growth of the biomass and bridging across the spaces within the packing. Plugging tendency for various packings can be predicted or compared by looking at the void fraction and free passage diameter. The free passage diameter is the more important variable.
Plugging is a very serious problem for biofilters. At best it is a continuous maintenance problem and at worst it completely destroys the ability of the filter to perform according to design. Another cause of plugging is non uniformity in packing density. If some areas of the bed are packed denser than others, it can lead to partial plugging. The high density areas of the filter bed can become plugged and inoperable while the rest of the bed experiences channeling or localized high flow regions. This can lead to major decreases in filter performance.
Some biofilter systems are designed to promote solids collection and plugging. The filter is operated until performance
goes below acceptable levels and then the bed is cleaned. This can lead to cyclical water quality problems with resultant stress on the fish. The best solution is to use a conservative design with a packing that is resistant to plugging for the operating life of the filter.
On the other hand it may not be possible to accommodate a packing that is open enough to insure that it will never plug. If space is limited it may be necessary to choose a packing that has a very high specific surface area. In this case it would
be wise to use a packing that will be resistant to plugging for at least the amount of time it takes to bring the crop to marketable size. The packing should be of the type that can be easily removed, cleaned and replaced with a minimum of effort and labor.
Another option is to have a packing that can be removed in sections. A small part of the packing can be removed and replaced with a spare section while the plugged section is cleaned. If only a small section of the overall system is removed, the disruptive effect on the whole system will be minor. A removable packing is also convenient if one desires to clean and sterilize the system between crops.
( 05 ) Inert material of construction - Wood, paper or other biologically degradable materials are not suitable for biological filters. Similarly, metals such as steel, aluminum or copper are not usable because they corrode and will
inhibit biological growth. Virtually all commercial available biofiltration packings are non-corrosive, resistant to rot
or decay and generally impervious to chemical attack. However, some plastic packings are susceptible to attack from ultraviolet radiation. Unprotected plastics that are exposed to sunlight rapidly become brittle. This phenomenon is
familiar to anyone who has left a milk jug outside for a couple months. This problem is entirely preventable through
the use of UV inhibitors that can be incorporated into the plastic. UV protection should be incorporated into any plastic biofiltration packing.
( 06 ) Low cost per unit surface area - As we noted above, a biofilter is nothing more than a given amount of surface area that provides space for bacteria to grow. All things being equal, it makes sense to use the packing with the lowest cost
per unit surface area.
( 07 ) Good mechanical strength - One of the features of better biofiltration packings is good mechanical strength. In a large filter, it is very desirable that the media be able to safely support the weight of one or more workers. Aside from supporting maintenance traffic, good mechanical strength means better dimensional stability, reduced vessel support requirements and longer life.
( 08 ) Light weight - In addition to freight costs, the weight of a packing can affect costs for other parts of the system. Heavier packings typically require stronger and more expensive supports and vessels. If the packing or the whole biofilter must be moved it helps if the media is light weight.
( 09 ) Flexible in overall shape - Since biofilter vessels come in all shapes and sizes, the packing should fit into any shape vessel.
( 10 ) Ease of maintenance - A good packing should have little or no maintenance requirements. If maintenance is required due to plugging or the need to sterilize the system between crops, the packing should be easily moved with a minimum of
labor and specialized equipment. The ability to quickly and easily clean the packing can be important.
( 11 ) Low energy consumption - While biofilters do not consume energy directly, their overall design determines the pump head required to move water through them. Keeping the bacteria supplied with oxygen also requires energy. As biofilters become more sophisticated and the aquaculture industry becomes more competitive, energy costs will be a major factor in overall profitability. The biofilter that gets the job done with a minimum of labor and energy consumption will eventually become the industry standard.
( 12 ) Light Attenuation - Nitrifying bacteria are sensitive to light. The packing should be opaque and the shape should prevent light from penetrating into the interior of the packing.
( 13 ) Wetability - In order for bacteria to attach and grow on the surface of the media, the surface must be wetable or hydrophilic. Waxy, oily or slick surfaces that are hydrophobic or water repelling are not desirable.
The "ideal" packing provides the low cost solution to our biofiltration needs because it :
a. Gives use the most surface area for the lowest price.
b. Gives us the lowest cost vessel because of high specific surface area (high packing density), low weight, high mechanical strength and the ability to conform to any vessel shape.
c. Keeps maintenance costs low due to resistance to plugging.
d. Keeps pumping and other energy costs low due to flexibility of design.
Types of Packings...
Now that the characteristics of the "ideal" biofiltration packing have been established, the next step is to compare the existing media to that standard.
( 1 ) Rock and Gravel - Various sizes of gravel and rocks have been used since the nineteenth century in biofilters. They
can be used in both submerged filters and trickling filters. They are still used for a variety of applications including aquariums, aquaculture and municipal sewage treatment plants. Earthen materials are readily available, inexpensive and can have relatively high specific surface areas. Rocks and gravel are typically very inert and durable with excellent mechanical strength. They are usually wetable immediately.
The main disadvantage to gravel type filters is their very low void fraction. As a natural consequence of the low void fraction, these types of filters tend to plug rapidly. In order to avoid plugging, the amount of space between the pieces
of gravel must be relatively large. In general, the free passage diameter is directly related to gravel size. Unfortunately, the specific surface area is inversely related to gravel size. If we use a size of gravel with openings large enough to
avoid plugging, the specific surface area would be too low. With low specific surface areas, the size of the tank required
to hold the packing becomes too large.
There have been numerous attempts to overcome the drawbacks of gravel packed filters. One method is to use a substrate that increases the surface area available without changing the overall size of the piece of gravel. This is one of the concepts behind pumice rock, activated charcoal and micro porous ceramic materials. The claimed surface area for these materials is often very high. The problem lies with the long term operation of these types of packings. Typically, the bacteria growing
on the outer surface of the packing will prevent sufficient nutrients and oxygen from diffusing into the inner pores of the material. While these packings have large amounts of surface area, only a small fraction of the surface area is usable for the aerobic bacteria.
Another major drawback of gravel is weight. Vessels and under drain systems must be strong enough to support the gravel. Also, gravel is a relatively permanent filter. Once installed in a given location it is very difficult to move. In general, the high maintenance costs and high capital costs of the vessels for gravel biofilters makes them unsuitable for modern commercial aquaculture.
( 2 ) Fiber Mesh Pads - Various types of mesh pads are in use today as biofilters. These pads use thin fibers similar to air conditioning filters but are formed into heavier and thicker pads. They can act as both a physical filter and a biological filter. They are light in weight and have more surface area per unit volume than any other type of packing.
Unfortunately, fiber mesh pads suffer from the same major drawback as gravel filters. They have very small free passage diameters and they tend to rapidly plug and lose effectiveness under most circumstances. This tendency to plug is further complicated by the difficulty of cleaning and regenerating the pads. Typically, fiber mesh pads require a large amount of labor to be cleaned.
Another drawback to the fiber mesh type pad is the difficulty of installing the large quantities of pad needed for a production system. The pads need extensive supports to keep them oriented in the water flow correctly. Typically, there are very specific requirements on how mesh pads can be used.
( 3 ) Brillo Pads - A packing type similar to the mesh pad is the "ribbon bundle" or "brillo pad" type packing. These packings are light in weight and offer relatively large amounts of surface area at a low cost. While the ribbons are not
as closely spaced as the fibers in a fiber mesh pad, they still suffer from some of the same drawbacks as the mesh pads.
One of the notable drawbacks to brillo pads is their very poor mechanical strength. It is not possible to stack these packings without compressing the bottom layers. As the bottom layers are compressed, they restrict the flow and become
easily plugged. Both "brillo pad" and mesh pads have been successful in small aquarium applications but scaling them up
to aquaculture production applications is difficult and uneconomical.
( 4 ) Random or Dumped Packings – These packings are similar or identical to packings used in the chemical industry for various heat and mass transfer applications. There are literally dozens of different types of injection molded plastic
shapes that are available in a wide variety of specific surface areas. These packings are "randomly dumped" into vessels, hence the name. Typically, these packings have a good void fraction and relatively high resistance to plugging compared to mesh pads or gravel beds. Since each piece of packing is small, random dumped packings readily conform to any shape tank or vessel.
Here are several examples of typical injection molded packings.
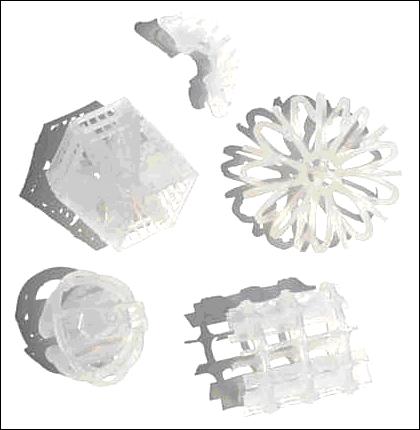
Random packings must be installed over a grid or screen type support. They must be contained because they have no intrinsic structural strength. In general, random packings have poor mechanical strength. One cannot walk on top of random dumped packings without crushing or compacting the filter bed.
Although random packings are relatively light weight they are difficult to remove from a large vessel once they are installed. This is because the packings must be scooped or shoveled out of the vessel. Any cleaning that is required must usually be done in place. Installation of random packings can be tricky. If the bed is not installed carefully, wide variances can result in the density of the packing throughout the bed. In addition, a bed of random packings will tend to settle and compact over time.
Another disadvantage of both gravel filters and random packings is the inability of the operator to determine what is happening in the interior of the biofilter bed. It is very difficult to shift enough material to see what is happening throughout the bed. The visible top part of the bed may be operating normally while the bottom of the bed is plugged and not operating correctly.
Random packings are available in stainless steel, ceramic, porcelain and various engineering thermoplastics. Most packings for aquaculture are injection molded from PP (polypropylene) or HDPE (high density polyethylene). PP and HDPE are excellent polymers with high heat resistance and excellent chemical resistance. Unfortunately, many PP and HDPE compounds used to mold packings do not incorporate sufficient ultraviolet inhibitors to protect the packings from direct sunlight. The other problem with HDPE and PP is that both of these polymers are very hydrophobic. They can become wetable over time but it can take several months before they are fully wetted.
While random dumped packings are relatively modern biofilter packings, one of their major drawbacks is cost. Injection molding is an expensive way to create surface area. Dumped packings are best used in small systems where their high cost is not a factor. They are easy to use in small cylindrical vessels where they can fill the vessel with no special cutting or waste of material.
( 5 ) Structured Packings - Structured packings are widely used for many applications other than aquaculture biofilters.
They have virtually all of the characteristics that one looks for in the "ideal" packing. Structured packings have been
used in biofilter applications for over 30 years. For the municipal and industrial wastewater treatment industry, they are the packing of choice.
Here is a typical cross corrugated structured packing.
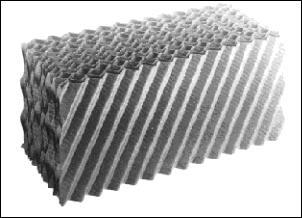
Structured packings are typically constructed of vacuum formed sheets of PVC (polyvinyl chloride). Continuous vacuum
forming is a high speed automated process that can efficiently produce large amounts of material. This method of construction allows structured packings to be produced for a much lower cost per unit surface area than injection molded packings. PVC is a relatively low cost resin with much better mechanical properties than PP or HDPE. PVC is initially hydrophobic but normally becomes fully wetable within 1 to 2 weeks.
The sheets of PVC are welded or glued together to form rectangular blocks. Some packings have internal "tubes" that only allow flow along one axis of the block. Other types of structured packings known as cross corrugated packings allow flow along 2 axes of the block. Most structured packings used in aquaculture are of the cross corrugated type.
Structured packings come in a wide range of specific surface areas or densities. The density is primarily controlled by
the sheet spacing. The highest practical density for aquaculture applications is about 120 sq.ft./cu.ft. which is a sheet spacing of about 1/4 in. The lowest specific surface area typically used for aquaculture is 48 sq.ft./cu.ft. with a sheet spacing of 3/4 in. The void fraction changes very little with sheet spacing. The highest density structured packing has a void fraction of about 95% while low density packings are usually about 98% void fraction. For both random packings and structured packings, void fraction is usually not a good predictor of plugging potential. It is more important to look at free passage diameter.
One of the big advantages of structured packings is their great mechanical strength combined with light weight. A packing with a specific surface area of 68 sq.ft./cu.ft. will weigh about 2.5 lbs./cu.ft. However, it will have a crush strength
of over 2,000 lbs. per sq.ft. of plan area. Unlike any other type of packing, structured packings can span distances of up
to 10 ft. between supports when used in a trickling filter. It is more common however to support them on beams that are 2
to 3 ft on center. Another advantage to structured packings is that they can be used without any containment vessel in a trickling filter design. Blocks of packing can be stacked in layers over a sump and water merely distributed over the top.
Another important advantage of the structured packings is their ease of installation and removal. Typical block sizes are
12" x 12" x lengths up to 10'. A clean, 10 cu.ft. block with 680 sq.ft. of surface area will only weigh about 25 lbs. 10 cu.ft. of gravel with a similar surface area would weigh over 1,000 lbs.
While it is beyond the scope of this article to discuss overall biofilter design, structured packings allow the design of filters that operate with the lowest energy costs in terms of water pumping head and aeration compressor pressures.
Summary...
Various types of packings exist for fixed film biological filters. Each different type has advantages and disadvantages but in terms of overall cost and suitability, the structured packings are the best choice for commercial aquaculture designs. Here is a simple "score sheet" to compare the various types of packing.