Biofilm Process - 2...
The Attached Growth Process – An old technology takes on new forms...
In 1869, Sir Edward Frankland began his groundbreaking study of filtration performance on raw London sewage by packing laboratory columns with various combinations of coarse gravel and peaty soil. This experiment was the first scientific proof that intermittent sand filtration is an effective treatment for wastewater. The concept of flowing wastewater across some natural material for treatment is the basis of attached growth processes, also referred to as fixed film. Generally, these processes are low maintenance, have low energy requirements, and, overall, are ‘low tech’– making them good wastewater treatment technology for small communities, as well as individual homes.
In contrast to activated sludge processes where the waste-consuming bacteria grow in suspension in water tanks, the active bacteria in attached growth processes cling to some surface, natural or manmade, to perform the cleaning.
Attached growth technologies work on the principle that organic matter is removed from wastewater by microorganisms. These microorganisms are primarily aerobic, meaning they must have oxygen to live. They grow on the filter media (materials such
as gravel, sand, peat, or specially woven fabric or plastic), essentially recycling the dissolved organic material into a film that develops on the media. In all cases, attached growth filters act as secondary treatment devices following a septic tank or other primary treatment. Raw wastewater must be treated first to remove the larger solids and floating debris, because these solids can plug the filter.
There are two basic designs of attached growth or fixed film systems: those that hold the media in place, allowing the wastewater to flow over the bed (such as trickling filters), or those where the media is in motion relative to the
wastewater ( e.g., rotating biological disks). In most cases, drains under the media collect the effluent and either
send it back through the filter or send it on for further treatment.
The main advantages of attached growth processes over the activated sludge process are lower energy requirements, simpler operation, no bulking problems, less maintenance, and better recovery from shock loads (Metcalf & Eddy, 2003). Attached growth processes in wastewater treatment are very effective for biochemical oxygen demand (BOD) removal, nitrification,
and denitrification. Disadvantages are a larger land requirement, poor operation in cold weather, and potential odor problems.
Many small communities, housing developments, and individual homeowners are discovering that the use of filters or rotating biological contactors (RBCs), either alone or in some combination with other technologies, provide low-cost, low-maintenance wastewater treatment.
There are many variations and combinations of these processes, sometimes referred to as hybrids, that use the attached
growth process in combination with other technologies. This issue of Pipeline will describe some of the more common types
of attached growth filters: sand, peat, and textile filters; trickling filters and rotating biological contactors; and subsurface flow wetlands. We will also explain how these systems work and advantages and disadvantages of using them.
Trickling Filters...
Trickling filters are by far the oldest attached growth process. This simple technology has been used for nearly 100 years
to provide low-cost, low-maintenance, biological wastewater treatment. Trickling filters offer simple, reliable treatment
in areas where large tracts of land are not available. Because of their high design flexibility, trickling filters are able to handle a wide variability of wastewater strengths. But, these types of filters generate sludge, which must be treated and disposed of, and the treatment unit may need to be covered in cold climates for effective operation. Trickling filters also require regular attention from an operator.
The most common design is the nonsubmerged trickling filter. The wastewater is applied to the surface of the filter (a bed of rocks, gravel or plastic). The wastewater percolates down through the bed to a drain where it collects and discharges, or sent for further cleaning. The composition, size, uniformity and depth of the media all affect performance.
How Trickling Filters Work ?...
A jelly-like biological film forms on the gravel or plastic where the bacteria break down the organic matter. The film becomes very thick and eventually falls off of the supporting surface, and a new slime layer begins to grow in its place. This dropping off is called ‘sloughing’ (pronounced ‘sluffing’) and should be a continuous process if the system is managed properly. Without the sloughing action, the media will clog and develop anaerobic conditions. The collected liquid is
passed to a sedimentation tank where the solids are separated from the treated wastewater. The bacteria clumps that drop
off must be treated as suspended solids.
Sometimes called biological filters, trickling filters were developed from attempts at filtering municipal wastewater. The microbial growth clogged the filters; larger and larger filter media were used until the clogging was minimized. In the 1950s, plastic packing began replacing rock in the U.S. Plastic media allows high loading rates and taller filters that use less land area.
Trickling Filter Design...
Beds of conventional trickling filters are made up of crushed rock, slag, or gravel about 2 to 3 inches in size. The bed is commonly 6 to 10 feet deep, held in place by a reinforced concrete basin. When the media is made up of plastic tubes, which are very light weight, the height can be much greater – these systems can be as tall as 30 feet. These systems are sometimes called tower trickling filters or biotowers. Most newer trickling filters use plastic packing as the working media.
Conventional trickling filters are round in shape with centrally mounted rotating arms for distribution of the wastewater. Nozzles on the arms spray the wastewater evenly across the media. Natural drafts are created by temperature differences between the outside air and air inside the filter. Deep tower filters sometimes require an additional air supply. The temperature of the wastewater is more important to the success of the process than the air temperature. Trickling filters show a high degree of reliability if operating conditions remain steady and the wastewater temperature does not fall below 55º F for prolonged periods. Sloughing tends to occur during seasonal temperature changes. Since the process is simple to operate, mechanical reliability is high. The trickling filter process is effective for removing suspended materials but is less effective for removing soluble organics.
Rotating Biological Contactors (RBCs)...
Rotating biological contactors (RBCS) were first used in Germany in the 1960s, and due to their proven effectiveness at treating wastewater, hundreds of them were built in the U.S. in the 1970s. An RBC consists of a series of closely spaced, circular, plastic disks mounted on a shaft. The disks are partially submerged in wastewater and slowly rotate through it.
The surface of the disks provides an attachment site for the aerobic bacteria. Oxygen is provided as the disks move in and out of the water. Solids are kept in suspension by the mixing action of the rotating media. Excess slime on the disks
sloughs off from time to time, just as in the trickling filter systems.
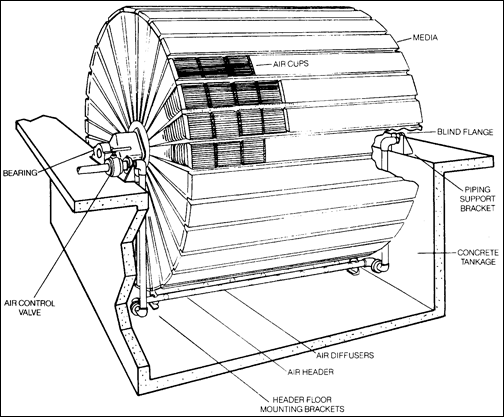
The disks are most commonly made of high-density polyethylene or styrofoam and are usually ridged, corrugated, or lattice-like to increase the available surface area. These systems must be designed carefully to avoid excessive biofilm growth and sloughing problems, which may lead to failure of mechanical parts in the treatment unit. RBCs can be arranged
in a variety of ways depending on specific effluent characteristics and the secondary clarifier design and can be designed specifically for BOD removal or nitrification.
RBCs are often covered with a fiberglass housing to protect the disks from deterioration due to ultraviolet light, to
protect the process from low temperatures, and to control the buildup of algae. Performance of this type of treatment
design drops considerably at air temperatures below 55º F.
Sand and Peat Filters...
Treatment filters using sand or peat as media make effective attached growth systems. They can be designed as either single-pass or recirculating filters, meaning that the wastewater is run across the media more than one time. Regardless of the media, the process is generally the same–wastewater from the septic tank is allowed to run through a bed of media and collected from underneath. Treatment occurs as the bacteria grows on the media.
Sand Filters...
Sand filters are constructed beds of sand or other suitable granular material usually 2 to 3 feet deep. The media is
usually contained in a liner made of concrete, plastic, or other impermeable material. Partially treated wastewater is applied to the filter surface intermittently, and receives treatment as it slowly trickles through the granules. Typically, the wastewater is collected in an underdrain and flows to further treatment and/or disposal.
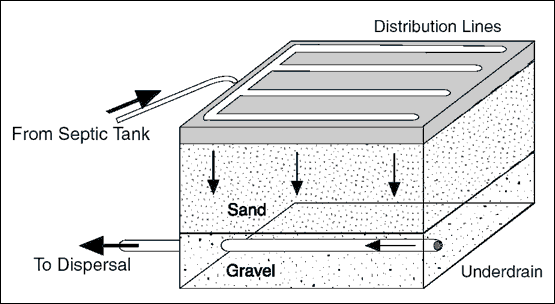
The media must be as clean and uniform in size as possible to allow the wastewater to flow through it properly. The wastewater must also flow freely through the media because the filter doesn’t work properly if it is saturated. Oxygen is critical to the biological and chemical treatment processes that take place inside the filter. The wastewater is applied intermittently, allowing the media to drain between doses, ensuring that oxygen is allowed to flow between the media particles. It is also important that the wastewater be applied evenly across the filter surface. This uniformity is accomplished either by flooding the surface completely with a thin layer of wastewater or by spraying or by applying the wastewater through a network of distribution pipes within the bed itself.
Treatment occurs by physical, biological, and chemical processes in combination. Most treatment occurs in the first 6 to
12 inches of the filter surface. Some of the organic matter sticks to the surfaces or gets caught in the crevices between
the sand grains. Chemical bonding takes place as certain particles come in contact with and react with the media. Biological processes occur when the bacteria consume the particles in the wastewater in the thick layer called the biomat. This area near the surface of the filter is where the protozoa feed on the bacteria and help prevent the bacteria colony from becoming so dense that it clogs the filter. It is important that this balance between the various life forms is kept constant.
Sand filters are ideally suited for serving small populations, less than 1,000 people. Sand filters are generally low-cost and require minimal operator attention, although the top layer of sand may need to be removed or replaced if clogging
occurs. Sand filters do require a certain amount of land area that may restrict their use. Single-pass sand filters for single-family homes typically require between 300 and 400 square feet of surface area. Sand filters are built on-site
using locally available sand that might be reasonably priced but is often of inferior quality. If good quality sand must
be shipped in, the high cost of transporting it must be considered.
Due to the concern of overloading the sand and requiring difficult or expensive replacement, buried onsite sand filters are usually designed for low loading rates, which ensures homeowners of 10 to 20 years of continuous usage with minimal maintenance required.
Peat Filters...
Peat filters use a two-foot-thick layer of sphagnum peat moss for wastewater treatment. Unsterilized peat is home to a
number of different microorganisms, including bacteria, fungi, and tiny plants, making peat a reactive and effective
filter. Similar to the previously discussed filters, peat filters are designed to accept wastewater from a septic tank
where it has been screened to remove solids and grease. This effluent is then pumped to the peat filter. A peat filter is made up of three parts: the peat bed, a distribution system for the wastewater, and a drain. The distribution system,
usually pressurized, applies the water evenly over the surface of the peat. The effluent is collected at the bottom of the filter by the drain where it is sent to a soil treatment system. Some peat filters are designed without a drain and, in
fact, are bottomless. The treated effluent goes directly into the soil below. Due to the organic nature of the peat, the filter media must be replaced periodically. Normal life expectancy is between 10 and 15 years. Peat filters may be
purchased as pre-assembled package plants or built on-site from purchased materials.
New Filter Technologies...
In the quest for the perfect media, several new technologies have been developed. These innovative materials lend
themselves to being sold as pre-packaged systems, providing quick installation and a high quality product.
Textile Filters...
The use of manmade textiles for wastewater treatment is a fairly recent development. The textile is a synthetic fiber and
is durable and resistant to biodegradation. The engineered fabric is packed into a watertight fiberglass basin, providing
a large surface area for biological breakdown, but taking up a much smaller space. The footprint area for a textile filter serving a four-bedroom, single-family home is only about 20 square feet. The lightweight filter medium and small filter
size make pre-manufactured treatment units practical, eliminating possible construction errors. These package systems are particularly suited for sites that are remote or have limited yard area for wastewater treatment. Textile systems are
capable of high removal rates for BOD, total suspended solids (TSS), fecal coliforms, ammonia, and nitrate concentrations comparable to municipal treatment plants. Unfortunately most of these textile systems have been unsuccessful at attaining significant biological phosphorus removal. High levels of phosphorus increase the growth of nuisance plants in neighboring lakes and streams, so textile filters may not be the best treatment choice near sensitive bodies of water. The town of Warren, Vermont, needed to replace their elementary school’s failing septic system, but there wasn’t enough adjoining property for a conventional drainfield. After some research, the city officials approached the engineers at Orenco Systems Incorporated, manufacturers of textile systems for help.
Fitting into less than half the area of a conventional system, the AdvanTex system with its pressurized, shallow, narrow drainfield was installed. The treatment units (water-tight fiberglass basins filled with an engineered textile material)
sit less than ten feet away from the school’s playground. A remote control system monitors performance and system functions and reports via modem to the city offices, freeing the school staff from worry about another septic system failure. The unit has been very effective, producing effluent, with BOD and total suspended solids reductions of up to 90 percent.
Foam Filters...
The physical properties of the plastic foam media allow for outstanding treatment with a single pass of the filtered wastewater. The media provides large open pores and high surface area for higher performance and long-term low maintenance. The absorbent foam chips or blocks provide consistent treatment with no plugging problems.
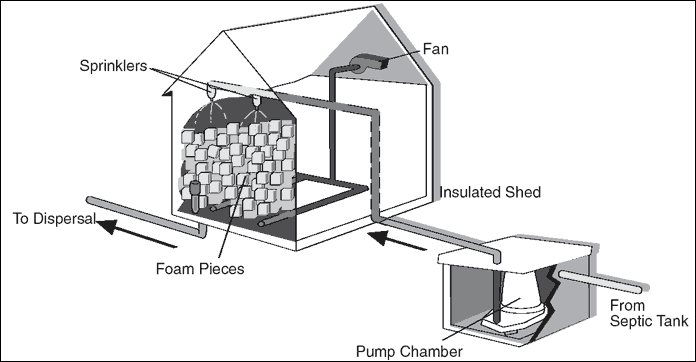
These foam media systems require a small amount of space for installation and can be scaled for different sized
applications by adding additional modules. The resulting effluent is often of high enough quality to be discharged
into short shallow trenches without further treatment.
Subsurface Flow...
Constructed wetlands consist of one or more rectangular treatment basins, called cells, filled with gravel, soil and/or plants that provide the filtering effect. Wetland systems are commonly designed with multiple cells operated in parallel
to allow the system to be alternated and rested during maintenance.
The bottoms of subsurface flow cells may be slightly sloped (up to 0.5 percent) to encourage the flow of wastewater through the system, and a natural clay or synthetic liner may be necessary for certain sites with high groundwater or soil restrictions.
Subsurface flow wetlands are natural systems that don’t require energy to perform treatment. When possible, the treatment cells are located near and down slope from the septic tank, avoiding the need for a pump. Most subsurface flow wetlands are designed so that wastewater travels through the length of the cell one time to receive treatment. Typical wastewater retention times range from two to six days.
Each cell is filled with rock or gravel placed on top of the soil or a lining on the cell bottom. The depth of the media
is usually one to two feet. Water-loving plants are rooted in the gravel. In properly working systems, the wastewater flows just below the surface of the gravel and remains unexposed to the atmosphere. Although the media is saturated, the wetland plants’ roots provide oxygen to create conditions conducive to treatment.
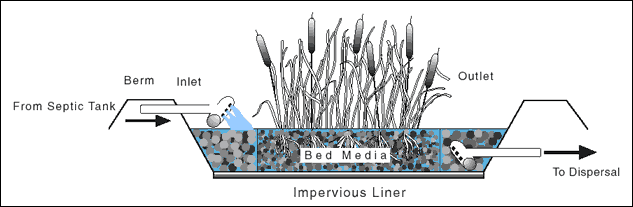
Cattails, bulrushes, and reeds are able to grow extensive roots and improve the treatment effectiveness by providing additional surfaces where bacteria can reside and where waste materials can be trapped. Plants also take up and store
some of the metals and other pollutants in the wastewater. Properly designed, operated, and maintained constructed
wetlands can effectively reduce BOD, suspended solids, nitrogen, metals, and other pollutants. However, phosphorus
removal is minimal. Depending on the level of treatment and local requirements, effluent from constructed wetlands may be disinfected, discharged directly into the environment, or directed to a soil absorption field for further treatment.