Wastewater Treatment Plant of Littleton & Englewood...
Headworks...
The existing headworks, placed into service in 1977, provided influent flow measurement, screening, influent pumping, and
grit removal. This building was renovated in 1991 during the Phase 1A project to upgrade the existing treatment systems,
improve ventilation, and provide odor control facilities. The ventilation system provides approximately 30 air changes per
hour through the headworks building. This exchange rate scours odorous gases out of the building and maintains a good
working environment for operations staff. The exhaust air from the headworks building is used to supply oxygen to the
biological treatment process in the nearby trickling filters. The combined exhaust from the headworks and trickling filters
is chemically treated to remove odorous compounds prior to release to the atmosphere.
Influent Flumes...
An average of 26 million gallons per day (mgd) of wastewater from the cities of Littleton and Englewood enters the plant
separately through two 60-inch pipes. Two Parshall flumes located at the entrance to the headworks building measure flows.
One flume is dedicated to measuring City of Englewood flows and the other flume measures City of Littleton flows. Each flume
has a rated free-flow capacity of 80 mgd. Influent flows are measured, and recorded on a continuous basis. Several manual
gates upstream of the flumes allow the two separate influent flows to be combined and routed through either flume.
Screening...
Following the influent flumes, flow passes through three mechanically cleaned bar screens. The screens have a ¾-inch clear
opening between bars, and effectively remove most rags, large debris, and stringy materials from the liquid flow stream.
Screenings are automatically collected and discharged into a trough. A high velocity flow of recycled effluent carries the
screenings through the trough to a grinder and pump. The ground screenings are pumped to a single, fine-mesh rotary screen
which discharges into an open hopper. An open-bed dump truck receives the ground, dewatered screenings which are transported
to final disposal at a sanitary landfill. It is important to remove these materials to prevent damage or clogging of the
plant's equipment.
Influent Pumps...
After screening, raw sewage pumps lift the flow approximately 30 feet into two grit basins. Raw sewage pumping is provided
by five dry well, vertical shaft centrifugal pumps. Four of the pumps have a rated capacity of 20.1 mgd, and the remaining
pump is rated at 9.4 mgd. Each pump discharges individually just above the water level of the grit basin distribution channel.
An air gap of several inches precludes reverse flow when the pumps are shutdown, eliminating any need for check valves on
the pump discharge piping.
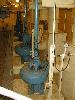
The raw sewage pumps are each equipped with electronic pulse-width modulation (PWM) type variable speed drives. Pump speed
is varied to maintain a constant level in the headworks wetwell. The pumps start and stop automatically in an operator
selectable sequence. Operation with a constant wetwell level achieves several purposes including ;
- Reduces the drop downstream of the influent flumes minimizing turbulence and air entrainment. Minimal turbulence
reduces stripping of H2S and other odorous compounds to the air.
- Eliminates frequent pump cycling associated with a variable level control strategy.
- Minimizes static lift on the existing pumps to achieve the rated capacity of the existing units.
- Increases submergence of existing pumps to minimize potential for vortexing and air entrainment.
The wetwell water surface level is set as high as possible while mainlining scouring velocities at low flow. The barscreen
rake mechanism operates frequently enough to avoid high headloss or breakthrough of rags and debris at high flow. The diurnal
flow peaking factor of 1.5 does not cause excessive velocities through the barscreens.
Grit Basins...
Removal of high density solids is accomplished in two mechanically cleaned, grit removal tanks equipped with chain and
flight collectors. Each tank is 20.7 feet wide by 60 feet long with a side-water depth of 16.6 feet. The grit basins can
be isolated upstream by slide gates. Grit is collected and pumped to two cyclones for grit classification, and then to a
final washing and dewatering unit. Washed grit is combined with screenings and transported by truck to a landfill for final
disposal. The wastewater then flows into a junction box and flow by gravity to the primary clarifiers.
Trickling Filter...
The existing secondary treatment process has two 105-foot diameter trickling filters each containing 16 vertical feet of
plastic cross-flow media. A rotary 4-arm distributor sprays primary effluent over the media at a rate of approximately 1
gpm / sf. The trickling filter is elevated above the plant hydraulic gradient to allow the effluent to flow to the solids
contact tanks by gravity. The filters are covered with aluminum domes to contain foul air. A forced air ventilation system
transfers foul air exhausted from the headworks building into the space below the dome enclosure. Air moves downward, concurrent
with the wastewater flow through the trickling filter media to provide oxygen for the biological process. Foul air collected
from the plenum area below the media is discharged to a chemical scrubber system to remove odorous compounds prior to discharge
to the atmosphere.
Three variable speed 24 mgd vertical column pumps are available to lift primary effluent to the top of the trickling filter.
The pump station wetwell will accommodate five pumps to allow for future expansion. Trickling filter effluent can be recycled
through the pump station to maintain minimum wetting for the fixed-film process. Electric variable speed drives and motor
control centers for the trickling filter pumps are housed inside the headworks building.
Five solids contact basins downstream from the trickling filter provide additional treatment of soluble BOD5 and
condition the biological solids for subsequent flocculation and sedimentation in the final clarifiers. All five basins are
112 feet long, 50 feet wide and have a liquid depth of approximately 13 feet. The combined volume of the five basins is 3.2
million gallons. Flow from the trickling filter is mixed with return secondary sludge at the upstream end of a 12-foot wide
influent channel. Distribution of the mixed liquor is accomplished with a series of weir gates which are located at the
entrance of each basin along the influent channel.
As bacteria begin growing, they generally develop into small chains or clumps. They are very active and motile and it is
difficult for them to settle. They have not yet developed the slime layer which aids in their sticking together. So, when
mixing occurs, the small chains or clumps are broken up and the bugs are dispersed, and they will not flocculate or settle.
As the sludge is allowed to age, the bugs lose their motility and accumulate more slime. Then the clumps and chains are
better able to stick together. The clumps grow bigger and bigger until they form a floc. If the organisms are allowed to
develop properly, under the right conditions, the floc get large and compact and begin to settle. The mixing in the aeration
tank tends to keep the floc small since, even though the bugs are sticky, the bond formed holding the organisms together is
not very strong. This is good because it allows the cells, food, and oxygen to contact each other.
Lag - phase : During this phase bacteria become acclimated to their new surroundings. They are digesting food,
developing enzymes and other things required for growth.
Accelerated growth phase : The bacteria are growing as fast as they can, since there is an excess of food. The cells
are mostly dispersed, not sticking together.
Declining growth phase : Reproduction slows down because there is not an excess of food. A lot of food has been
eaten and there are now a large number of bacteria to compete for remaining food, so the bacteria do not have enough
remaining food to keep the growth rate at a maximum.
Stationary phase : The number of bacteria is the highest possible, but not much food is left, so the bacteria cannot
increase in number. There is some reproduction, but some cells are also dying, so the number of bacteria remain relatively
constant. The bacteria have now lost their flagella and have a sticky substance covering the outside of the cell, allowing
them to agglomerate into floc. In fact, the floc get big enough that if aeration and mixing were stopped, the floc could
settle to the bottom.
Death - phase : The death rate increases with very little if any growth occurring. Therefore, the total number of
living bacteria keeps reducing. The bacteria are just trying to keep alive.
Secondary Clarifiers...
Separation of biological solids from the secondary effluent is accomplished in five final clarifiers. Each clarifier has a
diameter of 135 feet and a sidewater depth of approximately 14 feet. Secondary effluent is distributed to the five final
clarifiers from the aeration basin effluent channel. The aeration basin effluent channel has submerged isolation gates
which allow individual clarifiers to be isolated. Flow distribution to the clarifiers is unregulated. Low velocities and
similar headlosses in the piping system to each clarifier provide approximately equal flow rates through each unit. Sludge
is removed from the final clarifiers by a system of telescoping tubes that are attached to a two armed rake mechanism which
rotates along the bottom of the clarifiers. These tubes travel up to a site box which is hydraulically isolated from the
clarifier's water surface. The tubes discharge into the site box at an elevation below the clarifier's water surface
elevation. Sludge is forced up through the tubes by the hydraulic head made available by the difference in elevation
between the clarifier water surface and the tubes' discharge point. Sludge flow rates are intended to be controlled by
varying the elevation of the tube discharges. From a clarifier's site box, sludge flows by gravity to a common sludge
collection box. Weir gates have been provided where each clarifier's sludge withdrawal pipe enters the collection box.
The weir gates are intended to allow for sludge flow control if the site box tubes are flooded.
Sludge Processing...
Four 3,200 scfm blowers and two 8,000 scfm blowers provide aeration to the solids contact process. The air supply to each
tank is modulated to automatically maintain a dissolved oxygen setpoint of 1.5 to 3 mg / L. Fine bubble ceramic diffusers
mounted on a fixed-air piping grid along the bottom of the basins provide optimum air transfer efficiency and continuous
mixing of the mixed liquor. The four small blowers are located in a blower building west of the aeration basins. The two
large blowers are located inside the secondary sludge pump station.
Dissolved Oxygen...
Oxygen is required by these bugs to metabolize food for cell maintenance and growth. Although the bugs need oxygen, some
bugs can get along with less oxygen than others. Each bug must have a dissolved oxygen of at least from 0.1 - 0.3 mg / L
to function properly. So, it is important to maintain about 2 mg / L of DO in the activated sludge so that the bacteria
that are contained in the floc can get oxygen. If the DO is less than 2 mg / L, the bugs on the outside of the floc use
the DO before it can get to the center of the floc. If this happens, the bugs in the center may die causing the floc to
break up.
The Effects of Mixing...
Mixing is required to bring organisms, oxygen, and nutrients together, and to remove metabolic waste products. If there is
not enough mixing, proper treatment will not take place because of lack of contact between the bugs, their food and oxygen.
If too much mixing is provided, it can cause break up of floc or formation of unstable floc particles.