Chemical Treatment - 03...
Chapter 3 - Hydroxide Precipitation...
3-1. Introduction...
In hydroxide precipitation, soluble heavy metal ions are converted to relatively insoluble metal-hydroxide precipitates by
adding an alkali-precipitating agent. The most common hydroxide precipitating agents are :
• Caustic soda, Na ( OH ).
• Hydrated Lime, Ca ( OH ) 2 .
• Magnesium Hydroxide, Mg ( OH ) 2 .
( a ) The first step is adding and thoroughly mixing the precipitating agent with the influent waste stream.
Precipitation reactions, which originate in a rapid-mix tank to form metalhydroxide precipitates, are given below,
where M + 2 is the soluble metal cation being removed. Chemical equations, for simplicity, show metals
and other ions in their uncomplexed state.
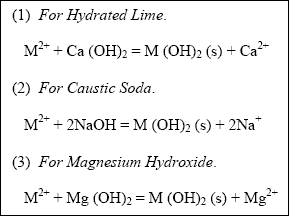
( b ) The solubilities of the metal-hydroxide precipitates vary, depending on the metal ion being precipitated, the pH of
the water, and, to a limited extent, the precipitating agent used. Typically, the solubilities of most metal-hydroxide
precipitates decrease with increasing pH to a minimum value (termed the isoelectric point) beyond which the precipitates
become more soluble, owing to their amphoteric (soluble in both acidic and basic solutions) properties. Figure 2-2 shows
the solubility of various metal-hydroxide precipitates. The extent of precipitation depends on a number of factors,
namely :
• The solubility product constant (K SP ) of the metal-hydroxide.
• The equilibrium (stability) constants (K I ) of the metal-hydroxyl constants.
• The stability constants of ligands or chelating agents (e.g., EDTA, citrate, tartrate, gluconic acid, cyanide, or
ammonia) that may be present.
Metal ions effectively removed via hydroxide precipitation include cadmium, copper, trivalent chromium, iron, manganese,
nickel, lead, and zinc.
3-2. Advantages and Disadvantages of Hydroxide Precipitation...
( a ) Removing metals via hydroxide precipitation has several advantages. Hydroxide precipitation is a well-established,
simple technology, which is relatively inexpensive. It has proven its ability to achieve regulatory effluent limits for
several metals, and it is well suited for automation. In addition to heavy metals, hydroxide precipitation can also remove
many non-metal pollutants, such as soaps and fluorides.
( b ) Hydroxide precipitation of heavy metals also has several disadvantages. Some metals, including lead, manganese, and
silver, may not be adequately treated by hydroxide precipitation. Some metals require reduction before they can be
precipitated as a hydroxide. For example, chromium (+6) must be first reduced to chromium (+3). Similarly, selenium (+6)
should be reduced to selenium (+4). Other metals may require oxidation before they can be effectively precipitated as a
hydroxide. For example, arsenic (+3) must be oxidized to arsenic (+5). Iron and manganese are other metals that require
oxidation before they can be precipitated as a hydroxide. In addition, strong chelating agents, organo-metallic complexes,
and metal-cyanide complexes inhibit the formation of the hydroxide precipitate, making it impossible to achieve minimum
theoretical solubilities. Introducing a strong oxidant (e.g., ozone) before the precipitation step may destroy some of the
metal complexes. Table 3-1summarizes the advantages and disadvantages of hydroxide precipitation.
3-3. Hydroxide Precipitation Using Lime...
Treating waste streams containing metals with lime is the most common way that industrial wastes are treated (EPA, 1987).
It is widely used because line is pumpable, has low cost, and is effective. A major disadvantage of the lime process is
that large amounts of sludge are formed.
( a ) Lime is available in either high-calcium (CaO) or dolomitic (CaOMgO) form. These pure, oxidized products are called
quicklime. Quicklime is available in lump (63–255 mm), pebble (6.3 to 63 mm), ground (1.45–2.38 mm), or pulverized (0.84
to 1.49 mm) forms. As lime particle size decreases, experimental evidence has shown that dissolution rates increase (EPA,
1987). High-calcium hydrate is much more reactive than dolomitic hydrate. However, heat and agitation can be used to
accelerate dolomitic hydrate reactivity.
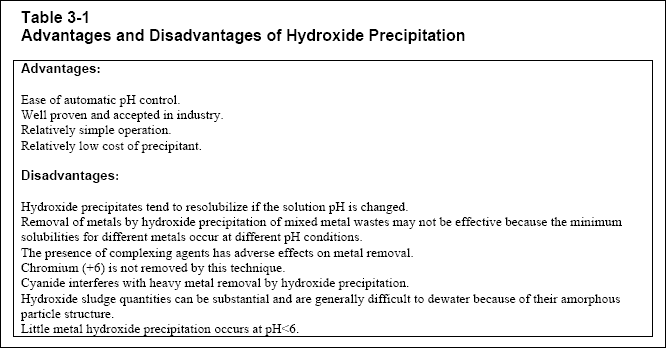
( b ) Although lime can be fed dry, it is most often slaked (hydrated) and slurried for the best efficiency. The slaking
process is carried out at temperatures of 82 to 99 O C with 10- to 30-minute retention times. After slaking, a
lime putty or paste is then slurried with water to a concentration
of 10 to 35 % (EPA, 1987).
( c ) Lime is mostly sold as quicklime, high-calcium, and dolomitic limes; however, lime is also available in its hydrated
form — either Ca ( OH ) 2 or Ca ( OH ) 2 - Mg O. It is supplied in either bulk or in 23-kg (50-lb)
bags. Hydrated lime is suitable for dry feeding or for slurrying and the resulting purities and uniformities are generally
superior to slaked lime prepared on-site (EPA,1987).
( d ) Since both quicklime and hydrated lime deteriorate in the presence of carbon dioxide and water, lime is typically
stored in moisture-proof containers and used within weeks of manufacture. Dry hydrated lime can be stored for longer periods
than can quicklime; however, carbonation may still occur, causing physical swelling, marked loss of chemical activity, and
clogging of discharge valves and piping (EPA, 1987).
( e ) Dry lime feed systems are either manually fed 50-lb bags or they have an automatic mixing and feeding apparatus. The
two types of automatic feed systems available are volumetric feed and gravimetric feed. Gravimetric systems discharge a
known weight, whereas volumetric systems deliver a known volume. Although gravimetric feeders can guarantee a minimum
accuracy of 1 % at the set rate, versus 30 % for volumetric feeders, they are roughly twice as expensive and require more
maintenance (EPA 430/9-79-18).
( f ) Lime precipitation is typically done under atmospheric conditions and at room temperatures. Adequate venting may be
required because heat and noxious gases can be produced (EPA, 1987). The precipitation unit is typically a reinforced tank
with an acid-proof lining. To promote the best mixing of the metals-containing waste stream and the lime (slurry) solution,
the unit usually has an agitator installed. Often, vertical ribs are built into the perimeter of the unit to enhance mixing
(also see Chapter 9).
3-4. Hydroxide Precipitation Using Caustic Soda...
Pure anhydrous sodium hydroxide (NaOH) is a white crystalline solid manufactured primarily through the electrolysis of
brine. Caustic soda (or caustic) is a highly alkaline sodium hydroxide solution. Caustic soda is commonly used to
precipitate heavy metals and to neutralize strong acids.
( a ) NaOH is available as either a solid or a liquid; however, it is used almost exclusively in a solution form of 50 %
or less. Caustic soda is available in lined 55-gal. drums or in bulk (tank car or truck). Caustic is easier to store,
handle, and pump than is lime. In addition, it will not clog valves, form insoluble reaction products, or cause density
control problems (EPA, 1987). However, in caustic storage areas where ambient temperatures are likely to fall below
12 O C, heated tanks should be provided to prevent reagent freezing.
( b ) Caustic, after lime, is the most commonly used hydroxide-precipitating reagent. Its main advantage is that it rapidly
dissociates into available hydroxyl (OH – ) ions, resulting in minimal holdup time, and reducing feed system and
tankage requirements. The main disadvantage of caustic is cost. Because caustic is a monohydroxide, precipitating divalent
metals (e.g., cadmium) requires two parts of hydroxide per part of divalent metal precipitated. In contrast, lime, a
dihydroxide base, only requires one part hydroxide to do the same job. Increased reagent requirements, combined with a
higher cost/mole (roughly five times that of hydrated lime), make caustic soda more expensive than lime.
( c ) Generally, lime is the reagent of choice in applications where reagent costs constitute the bulk of the operating
expenses. However, in low flow applications where a reagent is selected on the basis of limited space, rapid reaction rates,
and ease of handling, caustic is clearly superior (EPA, 1987). In addition, caustic will be a better choice when sludge
disposal costs are high.
( d ) NaOH is approximately 100 times more soluble in water than lime (at 25 O C). This reduces the need for
complex slaking, slurrying, and pumping equipment. Typically, caustic is added through an air-activated valve controlled
by a pH analyzer (EPA, 1987). Caustic is added as long as the pH of the waste stream remains below the control set point
required for optimum precipitation. Typically, a mechanical mixer agitates the waste stream to prevent excessive lag
time between reagent addition and observable change in pH. Precipitation using caustic is typically conducted under
standard operating temperatures and pressures.
( e ) Caustic soda precipitation processes are set up on the basis of waste type, volume, and raw waste pH level and
variability. For example, a system to precipitate concentrated acidic metals out of waste streams with low dead times
(time interval between the addition of caustic—or another chemical—and its first observable effect on pH) would be set
up as follows :
• A single reactor for feeds ranging in pH between 4 and 10.
• A reactor plus a smoothing tank for feeds with pH fluctuating between 2 and 12.
• Two reactors plus a smoothing tank for feeds with pH less than 2 or greater than 12 (EPA 600/2-81-148).
Although retention times vary with the rate of reaction and mixing, 15–20 minutes is a common range for optimal, complete
precipitation. To maintain good process control, the dead time should be less than 5 % of the reactor residence time (EPA
600/2-81-148). Typically, a caustic precipitation system is designed to have most of the reagent added in the preliminary
precipitation stage, while a second stage acts as a smoothing or finishing tank. This enables the second reactor to
compensate for pH control overshoots or concentrated batch dumps, which could overwhelm the primary precipitation system
(Hoffman, 1972). Overshoot is caused primarily by a lack of buffering capacity in the solution. Figure 3-1 shows a typical
titration curve for neutralizing an acidic waste stream. The waste enters at pH 2.0, where the titration curve is steep
and a strong demand for reagent exists; over- or under-correction is often unavoidable. For continuous precipitation
systems that process a waste stream that flows in at more than 20 gpm, with a pH that lies in the portion of the curve
that is nearly vertical, pH control is often achieved in a second reactor to prevent the use of excess reagent or to
prevent effluent discharge violations.
3-5. Hydroxide Precipitation Using Magnesium Oxide...
An alternative to lime and caustic soda for hydroxide precipitation is magnesium oxide (Mg O). It is available in slurry
form typically prepared of 55 to 60 % magnesium hydroxide , Mg ( OH ) 2 . The slurry must be mildly agitated
during storage because of its low solubility (0.0009 g / 100 mL) (EPA, 1987).
( a ) Magnesium hydroxide’s main advantage is that a more dense precipitate forms (because of longer reaction times).
Thus, the sludge volumes are much smaller (about 50 % less) than those of lime and caustic. In addition, use of magnesium
hydroxide as the precipitating agent improves sludge handling and dewatering characteristics. Studies have shown that when
influent metals concentrations are low, increased chemical costs will be offset by savings from easier sludge dewatering,
compactness and greater stability (EPA, 1987). Also, mixing magnesium hydroxide with caustic in a dual reagent system can
reduce sludge amounts by almost 50 % (EPA,1987). As disposal costs for metal-hydroxide sludges increase, magnesium
hydroxide becomes a favorable choice.
( b ) The main disadvantage of magnesium hydroxide is cost, which is approximately three times as much as hydrated lime.
In addition, magnesium hydroxide precipitation systems are not as easy to operate as lime or caustic. Because of the slow
reaction times, equipment-sizing requirements may prove to be very costly owing to higher retention time requirements.
( c ) Table 3-2 compares typical physical, chemical, and filtered sludge properties after use of hydroxide precipitating
agents : caustic, lime, and magnesium hydroxide.
3-6. Process Performance...
Performance among the three hydroxide precipitation methods does not vary significantly. The minimum metal-hydroxide
solubilities attained by each method are approximately the same. However, as earlier discussed, sludge characteristics can
vary tremendously. Figure 2-2 shows solubility curves for various metal-hydroxide precipitates at 25 O C.
Hydroxide precipitation can decrease several metals (e.g., chromium, nickel, cadmium, copper, and zinc) in solution to
concentrations that are less than 1.0 mg/L. Suggested references that discuss hydroxide precipitation performance summaries
are Anderson (1994), EPA (1987), EPA 600/2-77-049, EPA 625/8-80-003, and EPA 600/8-80-042c. Anderson (1994) is especially
good for summarizing how well the precipitation methods perform for mixed-metal solutions and solutions containing various
complexing and chelating agents.