Chemical Treatment - 04...
Chapter 4 - Sulfide Precipitation...
4-1. Introduction...
Sulfide precipitation works under the same basic principle as does hydroxide precipitation. The precipitation process
converts soluble metal compounds into relatively insoluble sulfide compounds through the addition of precipitating agents,
such as :
Sodium sulfide (Na 2 S).
Sodium hydrosulfide (NaHS).
Ferrous sulfide (FeS).
Calcium sulfide (CaS).
This technology is an effective alternative to hydroxide precipitation (Bhattacharyya et al., 1979; Ku and Peters, 1986;
EPA 625/8-80-003; EPA 600/8-80-042c). Over a broad pH range, sulfides (S - 2 , HS - ) are extremely
reactive with heavy metal ions. Sulfide precipitation is used to remove lead, copper, chromium (+6), silver, cadmium, zinc,
mercury, nickel, thallium, antimony, and vanadium from wastewaters (EPA, 1987). The precipitation reaction is generally
induced under near neutral conditions (pH 7.0 to 9.0). In a way that is similar to hydroxide precipitation, metalsulfide
precipitates most often must be physically removed from solution (through coagulation, flocculation, and clarification or
filtration), leaving a metal-sulfide sludge.
( a ) Figure 2-2 shows the relative solubilities of metal-sulfides versus metal-hydroxides, in water, as a function
of pH. Increases in the sulfide ion concentration directly cause more metals to be precipitated (EPA, 1987). Sulfides,
theoretically, will precipitate metals in preferential order (i.e., from lower Ksp to higher Ksp) (Talbot, 1984). For
example, copper and lead (K SP CuS = 1.2 ื 10 37 and K SP PbS = 7.0 ื
10 29 ) are some of the easiest metals to precipitate as sulfides, whereas manganese and iron (+2)
(K SP MnS = 7.0 ื 10 16 and K SP FeS = 4.0 ื 10 19 ) are some
of the most difficult (Benefield et al., 1982).
( b ) Consider the sulfide precipitation reaction below, where soluble nickel is precipitated using sodium sulfide
(Na 2 S). Nickel sulfide (NiS) is the solid precipitate formed from this reaction. Again, equations are
simplified by showing metals in their uncomplexed state.

The initial step in this process is to prepare a sodium sulfide solution. The solution is then added to a reaction tank,
in excess, to precipitate the pollutant metal (Ni + 2 ). Detention times vary; however, 30 minutes is common.
( c ) A feedback control loop, using ion selective electrodes, typically controls this process (EPA, 1987). Thickeners or
clarifiers, or both, are often used to help separate the metal sulfides from the effluent. A final step typically employed
in this process is to oxidate the excess sulfide ions in the supernatant using aeration or by adding hydrogen
peroxide.
( d ) Two major sulfide precipitation processes exist: soluble sulfide precipitation (SSP) and insoluble sulfide
precipitation (ISP or "Sulfex"), the difference being the way in which the sulfide ion is introduced into the treatment
process. SSP uses water-soluble reagents such as sodium hydrosulfide (NaHS) or sodium sulfide (Na2S),
whereas ISP uses ferrous sulfide (FeS), which is only slightly water-soluble. Calcium sulfide (CaS) is sometimes
used as an alternative to FeS.
4-2. Advantages and Disadvantages of Sulfide Precipitation...
Sulfide precipitation offers several advantages over hydroxide precipitation. As earlier discussed, the principal
advantage is the low metal-sulfide solubilities that can be obtained (see Figure 2-2). Secondly, with sulfide
precipitation, good heavy metal removal is possible even with weak chelating agents present. Strong chelating agents such
as EDTA will hinder the sulfide precipitation process somewhat; however, metal will still be removed (Ku and Peters, 1986;
Peters et al., 1985). Third, sulfide precipitation can be operated over a wide pH range, typically from pH 2 to 12.
Metal-sulfide precipitates are less amphoteric than corresponding metal-hydroxides, and, therefore, less likely to
resolubilize because of changes in pH. Fourth, with the ISP process, there is no need to pretreat chromium (+6), as
reduction of hexavalent chromium is catalyzed by the ferrous ions (EPA 625/8-80-003, EPA 600/8-80-042c). Last, the sludge
produced using sulfide precipitation is typically easier to dewater, and is less subject to leaching than metal-hydroxide
sludges (Peters et al., 1984).
( a ) Sulfide precipitation also has a few disadvantages. Although sulfide precipitation processes do not produce
significant air emissions, they must be controlled (pH must be high enough) to prevent the release of toxic
H2S gas to protect workers health. The Occupational Safety and Health Administration (OSHA) workplace
concentration limit for H2S gas is 10 ppm.
( b ) Sulfide precipitation does not effectively treat the trivalent states of iron or chromium. As earlier discussed,
chromium (+6) may be reduced to chromium (+3) by ISP; however, the process must be carried out under high pH conditions
to allow the hydroxide precipitate of chromium (+3) to form. In addition, the ISP process does not treat manganese, as
manganese sulfide has a higher solubility than ferrous sulfide. Also, sulfide precipitation does not adequately treat
cyanide compounds. Therefore, pre-treatment of such compounds is required. A major concern with sulfide precipitation is
the generation of metal-sulfide sludge. This sludge is considered toxic and hazardous under 40 CFR 261 (RCRA Waste Code
F006). ISP produces more sludge (as much as three times) than does hydroxide precipitation.
4-3. Soluble Sulfide Precipitation (SSP)...
The SSP process uses two main precipitating agents :
Sodium sulfide (Na 2 S).
Sodium hydrosulfide (NaHS).
( a ) Commercial sodium sulfide (light yellow or pink) crystallizes from aqueous solutions as nonahydrate
(Na 2 S . H 2 O). Sodium sulfide is sold as 30 to 34 % fused crystals and 60 to 62 %
flakes (EPA, 1987). Owing to its corrosive nature, sodium sulfide can cause severe burns to eyes or skin, and can
form toxic H 2 S gas when in contact with acid. The material is nonflammable, noncombustible, and nonexplosive
(EPA, 1987).
( b ) Commercial sodium hydrosulfide is highly soluble in water. When exposed to air, it is converted to sodium
thiosulfate and sodium carbonate. In the presence of organic matter, it can burn. Toxic H 2 S gas can be
released by heating sodium hydrosulfide. Sodium hydrosulfide is sold as 70 to 72 % by weight flakes (EPA, 1987). Tank
trucks are typically used to ship the product in solution form, whereas drums are typically used when the product is
in flake form.
( c ) Because sodium sulfide and sodium hydrosulfide are highly soluble, there is no need for slaking and slurrying
equipment. Liquid form reagents are typically added from storage, whereas solid reagents are added from rapid-mix tanks
(EPA 600/2-77-049). Reagent demand is typically determined through a specific-ion sulfide reference electrode pair, which
is set to a selected potential (Kim, 1981). Sulfide reagent demand generally depends on the total metals concentration.
For continuous operations, where metals concentrations are fairly constant, electrode set points can be set at the
potential, which corresponds to the maximum electrical potential sulfide concentration gradient (Kim, 1981). As with all
precipitating agents, jar testing should be used to determine optimal sulfide dosages.
( d ) In the SSP process, high sulfide concentration typically causes rapid precipitation of metal sulfides, which results
in small particulate fines and colloidal particles that have poor settling characteristics and poor filterability. Through
the effective use of coagulants and coagulant aids, separately or combined, this problem may be solved by forming large,
fast-settling floc.
( e ) The potential for excess sulfide is greatest when SSP is employed. Excess soluble sulfide in the treated effluent may
result in taste and odor problems, or present health or biotoxic hazards. The rate of evolution of H 2 S from a
sulfide solution per unit of water/air interface depends on :
Solution temperature (which determines the H 2 S solubility).
Concentration of dissolved sulfide.
pH (EPA 625/8-80-003).
Because measurement instruments typically have a lag in their response, and because reagent is added incrementally,
fine-tuning and rigorous maintenance are required to control the concentration of dissolved sulfide and pH to prevent an
H 2 S problem (EPA, 1987). H 2 S problems can be eliminated by enclosing and vacuum evacuating the
process tanks.
4-4. Insoluble Sulfide Precipitation (ISP)...
The ISP process, first patented as the "Sulfex" Process (Scott, 1979), removes dissolved metals by mixing the wastewater
with an FeS slurry in a solid/liquid contact chamber. The FeS dissolves to maintain a sulfide ion concentration of
approximately 2 mg/L (EPA 600/2-77-049). Because of its instability, ferrous sulfide has to be generated on-site from
sodium sulfide and ferrous sulfate. When other metals with lower equilibrium constants (KSP) are present, the
sulfide ion is released from the ferrous ion. The liberated ion will form a hydroxide, as well as a precipitate, when the
pH is maintained between 8.5 and 9. The excess (unreacted) is then settled or filtered out of solution with the metal
sulfide precipitate, leaving the effluent practically sulfide free (EPA, 1987). Coagulants and coagulant aids may be used
to aid in the settling process. When FeS is added to a solution containing dissolved metals and metal hydroxide, the
following reactions occur.
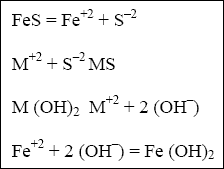
( a ) Typically, the ISP process requires 2 to 4 times the stoichiometric amount of FeS (EPA 625/8-80-003). Because of the
very low solubility of FeS, using excess FeS stops toxic H 2 S gas from forming. However, the use of an excess
amount of FeS adds significantly to the chemical cost of the process as well as sludge volumes. A considerably larger (up
to 3 times that of lime precipitation) quantity of sludge is produced from this process because ferrous ions are added to
the wastewater and they subsequently precipitate as ferrous hydroxide, Fe ( OH ) 2 (Cushnie, 1984). Although
FeS has a low solubility, residual sulfide levels could be in the range of 1 to 10 ตg/L, possibly exceeding water quality
criteria for marine organisms or drinking water (EPA, 1987).
( b ) The following results were reported during jar test studies and pilot plant demonstration tests that compared the
Sulfex process to hydroxide precipitation (EPA 600/2-77-049) :
(1) The Sulfex process produces lower residuals for copper, cadmium, nickel, and zinc than the hydroxide process.
(2) Satisfactory effluent quality is usually obtained with the Sulfex process within the 8.5 to 9.0 pH range, which is
within the 6.0 to 9.5 pH range generally permitted by EPA for discharge.
(3) A particular metal is more effectively removed when it is in a solution containing other heavy metals rather than when
it is the only metal in solution.
(4) The Sulfex process can be applied at loading rates up to 2.0 gpm / ft 2 when tube or lamella type settlers
are used.
(5) The required dosage of ferrous sulfide depends on the type of waste being treated. Typically, for wastes free of
complexing agents, dosage is normally 1.5 to 3 times the theoretical requirement. For wastes containing complexing agents,
typical FeS dosages are 3, or more, times the theoretical dosage.
(6) The following factors are important to obtaining satisfactory results with the Sulfex process :
Concentration of ferrous sulfide solids in the mixing zone.
pH.
Effective use of coagulants and coagulant aids.
(7) It may be more economically prudent to pre-treat wastes containing high concentrations (above 50 mg/L) using hydroxide
precipitation before polishing with the Sulfex process.
4-5. Calcium Sulfide Precipitation...
As an alternative to using FeS, calcium sulfide (CaS) can be used as the precipitating agent (Kim, 1981; Kim and
Amodeo, 1983). Using calcium sulfide as the sulfide source can minimize some of the problems associated with soluble
and insoluble sulfide precipitation (i.e., H 2 S evolution and excess reagent requirements). Solid calcium
sulfide is typically slurried before it is added and it produces easily settable precipitates. Calcium particles act as
nuclei for producing metal-sulfide precipitates and the dissolved calcium functions similarly to a coagulant. Calcium,
added as CaS, is mostly dissolved after reaction and does not significantly add to the sludge volume. For this same
reason, the CaS dosage requirement, unlike FeS, is near stoichiometric (EPA 600/2-77-049).