Chemical Treatment - 10...
Chapter 10 - Treatability Testing...
10-1. Introduction...
Treatability testing is required to obtain the following necessary design and operating parameters :
Optimum pH levels for maximum removal of target metals.
Chemical reagent dosage rates and application points.
Mixing requirements.
Settling rates.
Sludge volume.
Sludge characteristics.
Before bench-scale testing begins, representative influent samples should be analyzed for the following parameters :
pH.
Temperature.
Total suspended solids (TSS).
Total dissolved solids (TDS)including specific heavy metals and respective concentrations.
Oil and grease (O&G).
Alkalinity.
Conductivity (TDS).
Turbidity.
Note that many vendors of pre-packaged P/C/F treatment systems offer treatability testing capabilities.
10-2. Determination of Optimum pH Level...
A series of jar tests should be conducted to determine optimum pH levels for effective precipitation. Note that using
hydroxide precipitation in mixed-metal applications may require more than one precipitating stage. These tests are
conducted by adding differing amounts of precipitating agent, thus varying the pH levels. After the precipitates settle
out, the metal concentrations of the supernatants are measured. The pH levels at which all the target metals have the
lowest concentrations, or which are within the required regulatory limits, are chosen as the optimum reaction pHs. For
hydroxide precipitation, this testing is typically conducted using lime or sodium hydroxide. Sodium hydroxide, from a
maintenance viewpoint, is generally easier to add. However, with dilute metals concentrations (typical in ground water
remediation work), lime adds bulk to the solution and can thereby enhance sedimentation. During these tests, it is
important to note the volume of chemicals used to increase the pH to optimum levels as these data will be used to size
such items as chemical feed pumps and chemical storage facilities, as well as to estimate operational expenses. It is
also important to note precipitate characteristics (e.g., size, settling characteristics, etc.).
10-3. Determination of Coagulant and Coagulant Aid Dosage Rates...
If after pH adjustment, the solid precipitates settle rapidly and leave a clear supernatant, it may not be necessary
to add coagulants and coagulant aids. This, however, is not typical and adding a coagulant or a coagulant aid, or both,
usually becomes necessary. Two types of treatability testing commonly conducted include :
Jar testing.
Zeta potential measurements.
( a ) Jar Testing. Jar testing is the most commonly used and reliable treatability test to select the most effective
coagulant or coagulant aid, as well as respective optimum dosage rates. The objective of the test is simply to simulate
the plant-scale coagulation and flocculation processes. To do jar testing, a series of jars or beakers containing
pH-adjusted influent samples are lined up beneath a series of mixers. Optimal pH has already been established as described
in Paragraph 10-2. To each jar is added simultaneously either different coagulants with the same dosage, or a different
dosage of the same coagulant. The samples are then mixed for a pre-determined time. Resulting supernatants with the best
visual appearance are then analyzed for residual metals concentrations. The desirable performance characteristics of a
coagulant are that it produce a dense, rapid settling floc, and that the resulting supernatant be clear with little
residual metal remaining in suspension. Adding a coagulant aid may be necessary if adding the coagulant alone is not
satisfactory. A suggested jar testing reference is ASTM D2035-80. Step-by-step jar testing procedures for determining
optimum pH, as well as for determining optimum coagulant and coagulant aid dosages, are as follows :
( 1 ) Place 1000 mL of sample in each beaker. Note that jar testing equipment typically has enough capability for six
beakers per jar test run.
( 2 ) On the basis of the operating range of a precipitating agent and the solubility characteristics (see Figure 2-2) of
the target metal or metals, select an appropriate range to test for optimum pH (e.g., if using hydroxide precipitation for
removal of target metal zinc, use a pH range of 8.5 to 11 in 0.5 pH unit increments). Note that mixed-metal wastes may
require more than one precipitation stage.
( 3 ) Rapidly mix (80100 rpm) each sample for 3 minutes, followed by 1215 minutes of slow mixing (1530 rpm). Then allow
samples to settle for 2030 minutes.
( 4 ) Take a representative sample (about 100 mL) from the midpoint of the supernatant layer of each beaker and measure the
target metal concentration.
( 5 ) Plot the residual target metal concentration versus pH and select the optimum pH. Figure 10-1a shows that, for a
particular jar test, more than 95% of the target metal was removed at a pH of approximately 10.3.
( 6 ) Using this optimum pH, repeat steps 1, 3, and 4, varying coagulants and dosages. A method to select a starting dosage
is as follows : Using 200 mL of sample in a magnetic stirrer, add coagulant in small increments at a pH of 6.0. After each
addition, provide a rapid mix of 1 minute followed by a 3-minute slow mix. Continue adding coagulant until a visible floc
is formed. Use this as a starting dosage.
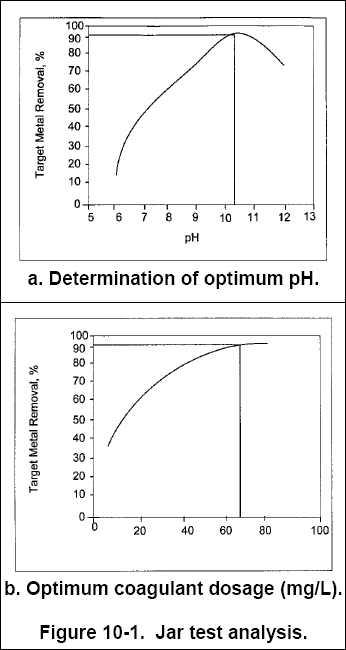
( 7 ) Plot the residual metal concentration versus the coagulant dosage and select the optimum dosage (see Figure 10-1b).
As in Figure 10-1b, the curves typically "flatten" out after a certain point, and increasing coagulant dosages beyond
45 mg/L give diminishing benefits and increasing sludge quantities. Therefore, the optimum coagulant dosage may not
correspond exactly with percentage of target metal removed.
( 8 ) If a coagulant aid is used, repeat this procedure, adding the coagulant aid toward the end of the rapid mix.
( b ) Zeta Potential Testing. Zeta potential is a measurement of particle strength surrounding the colloid. Zeta potential
relates to the repulsive force between particles and the distance over which particles (colloids) can repel each other and
thus prevent coagulation. Zeta potential measurements have been used experimentally to predict coagulant requirements and
optimum pH levels. By measuring how fast particles move across a microscopic grid toward an anode or cathode (positive or
negative poles), zeta potential defines the charge on particles and colloids in water. Zeta potential indicates the degree
of neutralization; therefore, it measures how well a coagulant is working. As discussed earlier, effective coagulation has
been demonstrated over a range of plus or minus 0.5 mV. Zeta potential is not an on-line method and cannot signal metering
pumps to alter delivery rate. Because zeta potential only measures one aspect of the coagulation process, the validity of
the measurements as a meaningful indicator is often in question. Jar testing best simulates clarification chemistry and
operation.
10-4. Determination of Settling Rates...
After optimum coagulant/coagulant aid dosage rates are determined, settling tests are required. First, the pH-adjusted
water is added to a graduated cylinder or other container designed for settling tests. Next, the optimum established
coagulant and coagulant aid are added and mixed. Immediately after mixing, the operator records the height of the sludge
interface and the time. The operator continues to record sludge heights with time until the settling rate approaches zero.
These values are then graphed to produce a characteristic settling curve, which is used to determine the overflow rate for
a sedimentation process (see the example problem in Appendix C). Metal hydroxides that are properly coagulated typically
settle quickly. However, a safety factor should be applied because of potential plant upset conditions. The calculated
overflow rate for a thick floc that settles immediately could be as high as
60 m 3 / m 2 . d (1,500 gpd / ft 2 ) (Water Environment Federation, 1994). However,
the design overflow rate should not exceed 40 m 3 / m 2 . d (1,000 gpd / ft 2 ).
For metal hydroxide sludges, values typically range between
10 and 33 m 3 / m 2 . d (250 and 800 gpd / ft 2 ) (Water Environment Federation, 1994).
Typically, maximum loading rates for metal-hydroxide precipitates, recommended by manufacturers of inclined plate
clarifiers, are less than 0.25 gpm / ft 2 (360 gpd / ft 2 ).
10-5. Determination of Sludge Characteristics...
A treatability study should be conducted to determine sludge dewatering capability. After settling, metal hydroxide sludge
is typically 96 to 99% water and can normally be dewatered to 6585% water (Water Environment Federation, 1994). The most
common methods for sludge dewatering are sand drying beds, vacuum filters, or filter presses. How well sand drying beds
perform depends on climate, but this may be partially simulated in the laboratory by setting up a sand column, applying
sludge to the surface, and monitoring the filtrate quantity, quality, and final sludge moisture content. With most new
systems, plate and frame pressure filters or belt filter presses are used; sand and vacuum filters are declining in use
(Water Environment Federation, 1994). Various manufacturers have developed bench-scale tests to simulate filter press
applications.
( a ) To determine the filterability of a sludge, a specific resistance test is normally conducted. Before filtering, the
sludge is typically chemically conditioned with a compound such as lime, polymer, or ferric chloride. This test is used to
determine what chemical to use and the optimum dosage for filtering particular sludges. The optimum dosage provides the
lowest specific resistance value. A sample of conditioned or MP unconditioned sludge is applied to a Buchner funnel
apparatus under vacuum, and the quantity of filtrate is measured versus time. The initial and final sludge moisture
contents are also measured. The specific resistance can be obtained by plotting filtrate volume versus time divided by
volume (Water Environment Federation, 1994).
( b ) Sludges should also be evaluated under the Resource Conservation and Recovery Act (RCRA) regulations for hazardous
waste classification. For example, metal-plating sludge is an RCRA-listed hazardous waste, category F006, and may not be
transported to a landfill permitted for non-hazardous waste only.
10-6. Oxidation Considerations ( Iron and Manganese Removal )...
In waters containing dissolved oxygen, iron (+3) and manganese (+4) are the only stable oxidation states for these metals.
These chemical forms are highly insoluble and, therefore, waters containing dissolved oxygen contain very little soluble
iron or manganese. Conversely, significant levels of iron and manganese can be found in the bottom levels of lakes or in
ground water, where anaerobic conditions favor the reduction of iron (+3) and manganese (+4) to the soluble iron (+2) and
manganese (+2) forms. Although, not considered hazardous or toxic, significant levels of iron and manganese can create
problems for a treatment system. For example, iron precipitates promote the growth of gelatinous iron bacteria, which can
clog process piping and valves or can foul subsequent treatment units (e.g., air stripping towers or UV-oxidation systems).
( a ) Soluble iron and manganese can be effectively precipitated through simple oxidation techniques. Commonly used
oxidizing agents are oxygen, chlorine, and potassium permanganate (KMnO 4 ). Oxidation rates depend on the
oxidant used, pH, the alkalinity of the waste stream, and the presence of organic matter. Generally, potassium
permanganate oxidizes the quickest, followed by chlorine, and finally oxygen. However, regardless of the oxidant used,
manganese (+2) oxidation is always slower than iron (+2) oxidation. A pH of near 10 is required to completely oxidize
manganese (+2) within a reasonable (less than 1 hr) reactor retention time. Permanganate will oxidize manganese (pH 11) to
MnO 2 within 5 minutes over a broad pH range.
In situations where only iron removal is necessary, the reaction is typically conducted at a near neutral pH (78). Studies
have shown that low alkalinity levels can lessen oxidation rates because the buffer system is slow to respond to acidity
changes induced by the oxidation reaction. Further studies have shown that the presence of organic matter may also lessen
the oxidation rates. The presence of complexing and chelating agents can also slow oxidation rates. So-called organic iron
and manganese are not effectively removed by oxidation; in these cases, studies have shown that coagulation with alum
followed by sedimentation can be effective.
( b ) By far, the most common method used to remove soluble iron and manganese is aeration (oxidant is O 2 )
in conjunction with sedimentation or filtration. By stripping carbon dioxide, aeration raises the pH of the water and
introduces the oxygen required for oxidation of iron (+2) and manganese (+2). In designing aeration systems, small or
slow settling floc may actually indicate success rather than failure. Aeration adds no extra precipitating agents and,
therefore, the floc formed is typically pure metal, thus reducing sludge volumes, oftentimes dramatically. Small and slow
settling floc problems can often be solved through adding polymers and gentle stirring to produce larger, denser floc.
When an aeration precipitation system is designed, it low production of suspended solids should be the primary goal.
( c ) Typically, in an iron and manganese removal system, an oxidation-reduction potential (ORP) probe connected to an ORP
controller is used to continually monitor iron and manganese ion concentrations. On the basis of these concentrations, the
controller adjusts the rate of oxidant addition to ensure that iron and manganese are sufficiently oxidized to form the
hydroxide precipitates.
( d ) Suggested references for iron and manganese removal systems are EPA 625/8-80-003, and 600/8-80-42c.