Chemical Treatment - 13...
Chapter 13 - P / C / F System Costs, Startup, and Operations...
13-1. Introduction...
Basic equipment for a hydroxide precipitation system consists of an
equalization tank, piping system, precipitation reactor, chemical feed system, flocculation / clarification unit, sludge
storage tank, and sludge dewatering equipment.
13-2. System Costs...
EPA developed the capital and operation and maintenance (O&M) cost information detailed below. They calculated direct
costs, indirect costs, and working capital as a percentage of the purchased equipment and installation (PE&I) costs.
The assumptions made by EPA are summarized in Table 13-1.
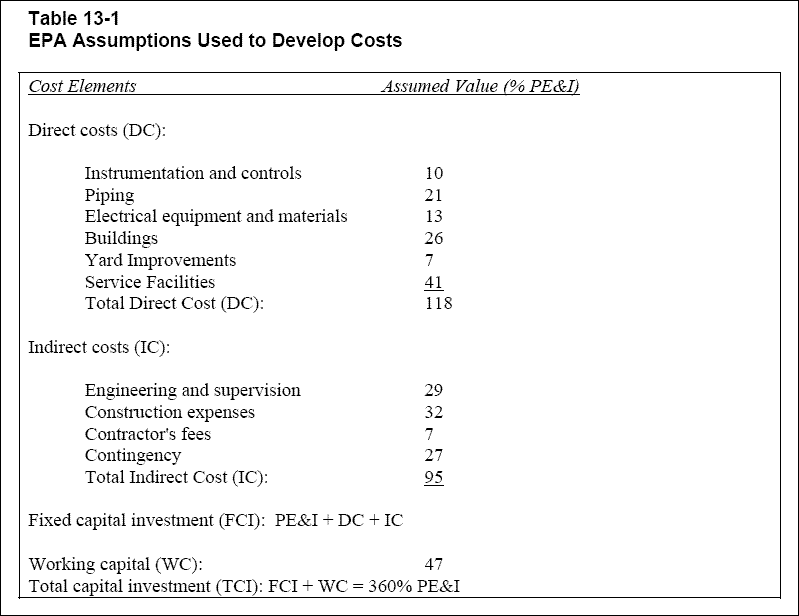
( a ) Annual O&M costs include variable costs, plant overhead costs, general administrative costs, and fixed costs.
Variable costs include costs for labor, maintenance, materials, chemicals, and contracted sludge disposal. Fixed costs
include taxes and insurance.
( b ) Chemical requirements for each treatment were based on stoichiometric requirements. To further obtain annual O&M
costs, the following assumptions were made :
• Plant overhead costs are 6% of the total capital investment costs.
• Taxes and insurance costs are 1% of total capital investment costs.
• Labor costs are based on 4 hr/shift at $20/hr.
• Power costs are at 2% of total capital investment.
• Nonhazardous contracted sludge disposal costs are based on $440/metric ton ($200/ton).
• Sludge transportation costs are based on $0.35/metric ton-km ($0.25/ton-mile) and a transportation distance of 25 km
(15 miles).
• All hazardous wastes generated by the treatment processes would be encapsulated and disposed of as nonhazardous wastes.
Other assumptions included in the cost model are :
• Treatment system will handle 200 mg/L of heavy metal ions.
• There will be two different flow rates : 3.8 and 38 m 3 / hr (1,000 and 10,000 gal/hr).
• The system will operate 24 hr/day, 300 days/year.
• Equalization tank is sized for 1-hour retention time and is made of reinforced concrete.
• Reagent feed and storage system is sized for a 1-week supply.
• Hydroxide precipitating agent is lime.
• Sulfuric acid capability is included in case of pH overshoot.
• Precipitation reactor is sized for 30-minute retention time.
• Flocculation/clarification unit has a separate flocculation tank, a polymer feed system, and an inclined plate separator
with a separate sludge collection zone.
• Solids concentration is 2% before dewatering stage.
• Sludge holding tanks are sized for 10 hours of clarifier underflow.
• Plate and frame filter press is provided for sludge dewatering. The cake solids concentration is 20% with an 8-hour press
cycle.
• Cost items not included are high pressure feed pumps, filtrate return lines to clarifier, and cake solids handling
equipment.
( c ) Table 13-2 outlines the cost estimate for a continuous hydrated lime hydroxide precipitation / coagulation
/ flocculation system.
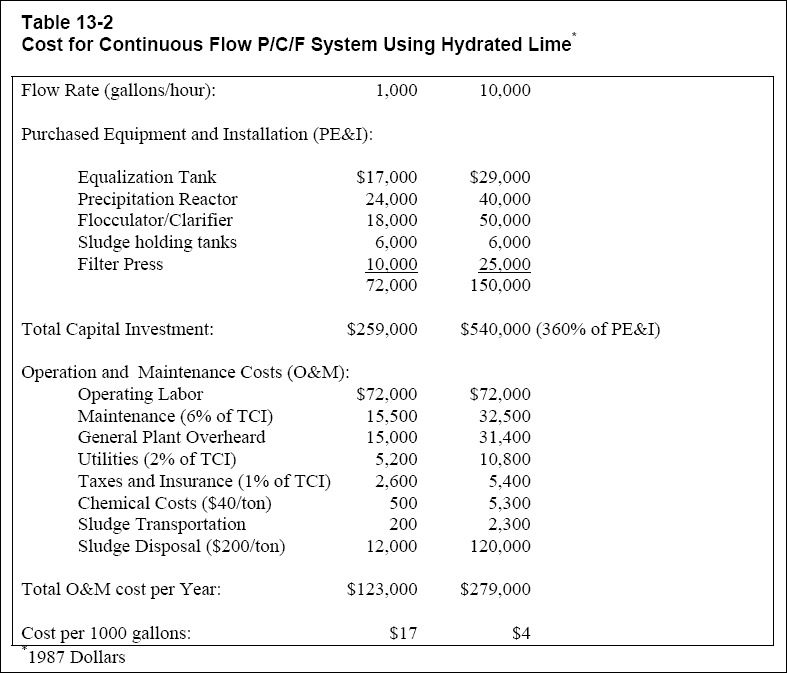
( d ) Table 13-3 presents cost data for a continuous soluble sulfide precipitation system. An additional aeration vessel,
consisting of a reinforced concrete reactor, four–six acid resistant spargers ($82/sparger), and 30 ft of 6-in. pipe
($2.40/ft), was included in the treatment train to reduce H 2 S gas evolution. In addition, operating labor
requirements have increased from 4 to 6 hours per shift because greater process control is necessary. Also, reagent
chemical costs have greatly increased from $90/metric ton ($40/ton) for lime to $900/metric ton ($410/ton) for sodium
sulfide.
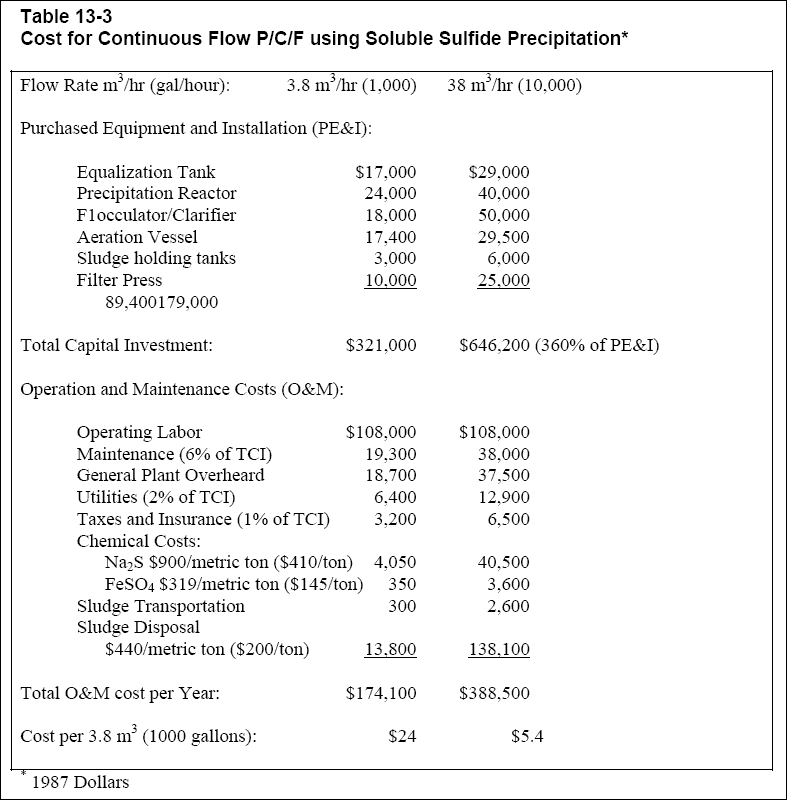
( e ) Table 13-4 presents estimated cost data for a continuous sodium carbonate precipitation system. The purchased
equipment and installation costs are equivalent to those of the hydrated lime system with the exception of retention
time. Because of the slower reactivity of sodium carbonate, a retention time of 1 hour was used in lieu of 30 minutes.
In addition, chemical reagent costs as well as usage rates are higher for sodium carbonate than for hydrated lime. The
advantage of this technology, as discussed earlier, is the lower pH requirements (usually 8–9) for carbonate precipitation.
The lower pH requirements result in lower alkali demand for neutralization and consequently less sludge generation (EPA,
1987).
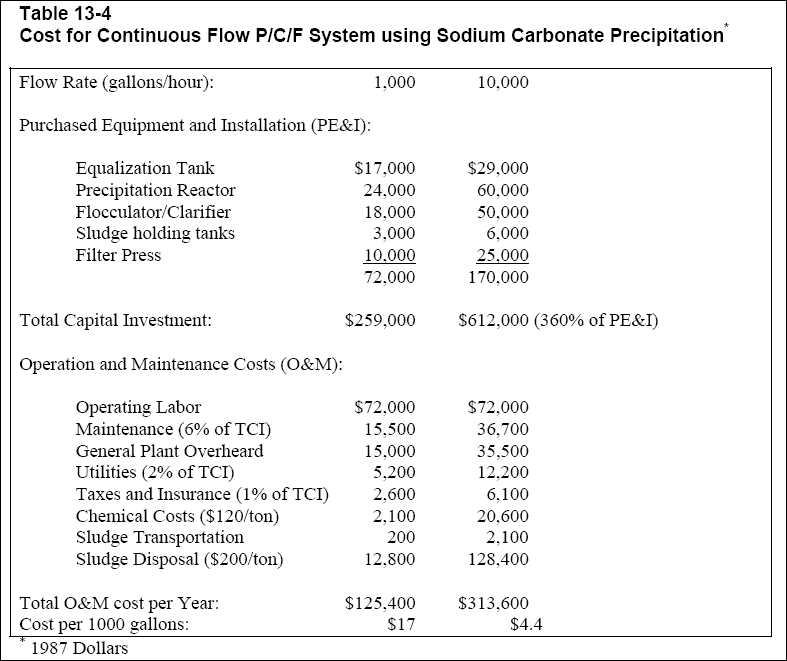
( f ) The following cost data for pre-packaged systems were obtained from NEESA (1993). Capital costs of
0.8-m 3 / min (20 gpm) and 0.246-m 3 / min (65 gpm) pre-packaged hydroxide metals precipitation
systems are approximately $85,000 and $115,000 respectively. Operating costs, excluding sludge disposal, are typically in
the range of $0.08 to $0.175 / m 3 ($0.30 to $0.70 per 1,000 gal.) of ground water containing up to 100 mg/L
of metals. Sludge disposal costs can increase operating costs by approximately $0.12 / m 3 ($0.50 per
1,000 gal.) of ground water treated. Actual sludge disposal costs (including fixation and transportation) have been
estimated at approximately $660 / metric ton ($300 per ton) of sludge. Operating costs for removal of iron (initial
concentration of 15 mg/L) and manganese (original concentration of 6 mg/L) from ground water to levels of 0.04 and
0.3 mg/L, respectively, have been estimated at approximately $0.1 / m 3 ($0.40 per 1,000 gal.) of ground
water. This assumes 2 hours per shift of operating labor.
13-3. Pre - Startup Checkouts...
The pre-startup checkouts are designed to verify the integrity of the system components before pre-startup testing. The
following items components must be tested :
( a ) Check any foundations to verify that they are placed and sealed properly.
( b ) Verify that all equipment has been installed.
( c ) Check rotating equipment that requires lubrication to ensure that manufacturer’s procedures have been followed.
( d ) Check equipment for proper alignment, attachment, and level, particularly if it has level controls.
( e ) Check piping and hoses to ensure that connections are tight, and make sure that they are flushed clean.
( f ) Check valves for position and operability and make sure that they are flushed clean.
( g ) Check electrical wiring and lighting to verify that wiring has been completed correctly.
( h ) Check the continuity of wiring loops.
( i ) Check high liquid level alarms on tanks, as well as pump on/off level controls, for proper installation.
( j ) Check chemical feed system for proper installation.
( k ) Check reagents for proper type and required supply quantity.
( 1 ) Check lockout devices and site security devices for proper installation.
13-4. Pre-startup Testing...
The pre-startup testing of a system is designed to verify the integrity of the whole system before it is actually started.
Test each component of the system as described below :
( a ) Pressure-test piping and hoses transporting liquid with clean water for at least 1 hour, with no loss of pressure at
1.5 times the working pressure; pressure-test tanks at the maximum hydraulic head using clean water.
( b ) Test electrical wiring to verify that there is no wiring damage or deterioration that could harm personnel or
equipment.
( c ) Turn on power to test equipment and control systems only after the electrical systems are tested and certified by
the contractor as being ready for operation.
( d ) Test lighting and put it in service to support work in all areas of the plant.
( e ) Test all rotating equipment, such as pumps, mixers, and blowers, with hand switches to examine rotation and
operability.
( f ) Operate each pump for a period of time, at a point of maximum horsepower required under operating or simulated test
conditions. Assure that the units and appurtenances have been installed correctly, and that there is no over-heating,
vibration, or excessive noise from any parts.
( g ) At this point test the control system to verify that manual and automatic controls function properly, depending on
their complexity.
( h ) Test safety shutdown sequences, controls/alarms, and interlocks in the control system to ensure that they are
installed properly and functioning as intended.
( i ) Test an emergency shutoff switch, clearly labeled, at all machinery units, to verify operability.
( j ) Test electrical "lockout" facilities with padlocks to ensure that accidental starts are prevented when machinery and
equipment are being worked on or otherwise taken out of service.
( k ) Calibrate instrumentation before systems are put into service, and test pressure and temperature gauges against
standardized gauges.
13-5. Startup...
The actual startup can begin once the pre-startup testing is complete. The startup check and functional performance tests
should be done in accordance with the vendor’s recommended procedures. The startup should proceed methodically, following
a plan prepared well in advance. Performance testing begins with equipment or components, proceeds through systems, and
ends with the complete treatment system passing its performance specifications and contractual requirements testing. Once
the system is operating at steady state , conduct a functional performance test as described in the following startup
checklist :
( a ) Check flow rates, temperatures, pH, and contaminant levels of the wastewater feeding the reactor tank.
( b ) Check pump-operating points to verify that the actual operating point matches the pump curve specification for flow
and pressure.
( c ) Start/stop pumps from all control mechanisms.
( d ) Check that current draw and voltage balance match specifications for all phases.
( e ) Check the reagent feeding systems to verify that the actual chemical feed rate is within the specified accuracy range.
( f ) Check the pH in the reactor to verify that operating values are within the design range.
( g ) Adjust the reagent feed rates and the pH control system as required to achieve maximum metal removals.
( h ) Monitor the composition of the effluent to verify that it meets the specified performance requirements.
( i ) Check the clarifier overflow rate to verify that it is within the design range.
( j ) Check the sludge-collecting device to verify that it is operating properly, and no sludge is overflowing the weir.
( k ) Check the filtration system to verify that the filtration rates do not exceed the design values, and the filter
backwash cycle is adequate.
( 1 ) Check the sludge dewatering system to verify that the sludge-conditioning system is functioning and that the sludge
cake solids produced meet specifications.
( m ) Check the control system to verify that the system operates within set parameters.
( n ) Check the monitoring systems and instruments to verify that they hold calibration.
13-6. Field Training...
The contract shall contain a paragraph that states that when the installation is completed, and at a time designated by the
contracting officer, the contractor must conduct a field-training course for a representative of the Government that details
how to operate and maintain the equipment furnished under the contract. These field instructions must cover all of the items
contained in the operation and maintenance instructions. Training shall be provided for a total period, as specified, of
normal working time and shall start after the system is functionally complete but prior to final acceptance tests. Field
instructions shall cover the items contained in the operating and maintenance instructions, as well as demonstrations of
routine maintenance operations. A videotape of the field-training course shall be prepared as a permanent record for future
training use.
13-7. Shutdowns...
The P/C/F system can be automatically or manually shut down to minimize hazards and or damage to the system. The P/C/F
system will shut down in the following situations :
( a ) When power fails at the site, the system will shut down automatically.
( b ) If some item of equipment fails (e.g., reactor mixer or reagent feed pump) automatic shutdown controls will terminate
the flow to the reactor.
( c ) When the control systems identify an operating condition that warrants shut down (e.g., blower amperage too high or
high level), a warning will first be issued, an alarm will sound (audible, visible, and remote dialing), and the system will
shut down if dangerous conditions are reached.
( d ) When the system requires shutdown for maintenance.
( e ) When the system requires shutdown after completion of the project.
13-8. Operation and Maintenance Manual Updates...
The O&M Manual is intended for use by operating personnel and will be adapted to the particular features of the equipment
installed; therefore, the document must be written for the operator. Only simple descriptive literature should be given,
and any material or brochures that require a specialist or research should be excluded. The following should be
included :
( a ) General description of the treatment process.
( b ) Detailed description of equipment.
( c ) Process flow and instrumentation diagram.
( d ) Certified drawings for equipment components and equipment layout.
( e ) Practical operating procedures, including performance testing, influent, and effluent concentrations, and trend
analysis of influent.
( f ) Complete set of fully updated and annotated piping and instrument diagrams, process flow diagrams, instrument indexes,
control ladder logic diagrams, description of controls, alarms, instrument interface, and maintenance procedures.
( g ) Specialty items, such as type of oil and grease, desiccants, etc.
( h ) Initial startup procedures.
( i ) Emergency and scheduled shutdown procedures.
( j ) Monitoring and quality control.
( k ) Equipment specifications.
( 1 ) List of faults and failures for each piece of equipment.
( m ) Fault/failure analysis, and trouble shooting guide.
( n ) List of spare parts.
( o ) Process safety and protective equipment requirements.
( p ) Record keeping (electronic or other) requirements.
( q ) Maintenance schedule. To plan all the inspection and maintenance activities required for plant operation, the
maintenance schedule must include : (1) Systematic checkup operations for each piece of equipment. (2) Sensor and
measurement device calibration frequency. (3) Periodic reports regarding consumption of chemicals, such as acid, caustic,
polymer, and coagulants. (4) Electronic or other recording data. (5) Personnel training requirements. (6) Time required for
each task. (7) Shutdown requirements during maintenance and repair. (8) Mothballing and preservation procedures.
( r ) Records of the entire schedule and the results of each task for future analysis. Other items shall be included as
follows : (1) Spare parts list with suppliers and costs. (2) Plant utility requirements, such as electrical, air, drinking
water, service water, and telephone. (3) Detailed safety procedures for chemical handling. (4) Name, address, and telephone
number of technical personnel to contact in case of an emergency related to the treatment system.
13-9. Operation...
After the performance testing has been accepted by the contracting officer, the contractor will continue to operate the
system for a period, as specified. The construction contractor will be responsible for operations, maintenance, chemical
testing, and record keeping in conformance with this specification until a remediation contractor takes over.