Mechanical and Electrical Design of Pumping Stations - 05...
Chapter - 05 : Pumping Equipment...
5-1. General...
The following types of centrifugal class of pumps are
used for flood-protection pumping stations:
( a ) Axial-flow impeller type.
(1) Fixed-blade, vertical type.
(2) Adjustable-blade, vertical type.
(3) Fixed-blade, horizontal type.
( b ) Mixed-flow impeller type.
(1) Fixed-blade, vertical type.
(2) Volute type.
( c ) Centrifugal volute or radial-flow type.
The type that should be used for any particular installation
is dependent upon the service conditions, head
requirements, and station layout. Chart B-1, Appendix
B, shows the approximate useful range of capacity
and head for each type of pump that is described. The
appropriate pump type should be chosen only after a
detailed study of the possible choices.
5-2. Pump Characteristics and Types...
( a ) General.
(1) Pumps are usually classified by their specific
speed. Specific speed is defined as the speed a pump
would have if the geometrically similar impeller were
reduced in size so that it would pump 1 gallon per minute
(gpm) against a total head of 1 foot. In SI, Ns is
called type number with Q in liters per second and H in
meters. Specific speed is expressed as:
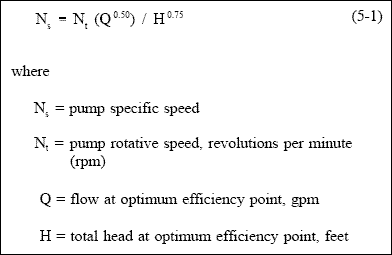
(2) Suction specific speed is a dimensionless quantity
that describes the suction characteristics of a pumping
system, designated as available, or the suction
characteristics of a given pump, designated as required.
The suction specific speed required must exceed the
suction specific available to prevent cavitation. The
suction specific speed available, based on the lowest head
pumping condition, is often used to determine the maximum
permissible speed of the pump.
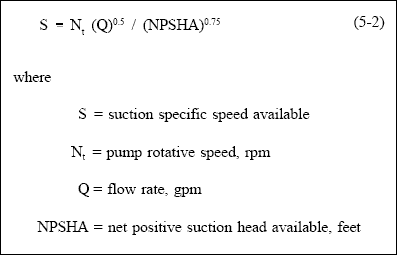
( b ) Axial flow.
The impellers of these pumps have
blades shaped like a propeller. This type of pump develops
most of its head by lifting action of the blades on the
liquid. The pumped fluid travels in a direction parallel
to the shaft axis, hence the name "axial flow." It can
also be constructed as an adjustable blade pump in which
the pitch of the blades is varied to provide different
pumping rates and/or reduced starting torque. Axial flow
pumps are primarily used to pump large quantities of
water against low heads and are typically used in open
sump pumping stations in a vertical configuration. The
value of Ns for this type of pump is typically above
9,000.
( c ) Mixed flow.
The impeller of these pumps develops
head or discharge pressure by a combination of both
a lifting action and a centrifugal force. The path of flow
through the impeller is at an angle (less than 90 degrees)
with respect to the pump shaft. This pump can be constructed
with multistages; however, for most Corps stations,
a single stage will develop sufficient head to satisfy most head requirements. The pump can be constructed
similar to an axial flow pump with water flowing
axially from the pumping element, or the impeller
can be placed in a volute (spiral casing), where the water
flows from the pump radially. The volute design would
be used either for large pumps where a volute would
allow the pump to operate at lower heads or for small
pumps where it is desirable to have a dry pit installation
with the discharge pipe connected near the pumping
element. The value of NS for this type of pump should
be limited to 9,000.
( d ) Centrifugal.
The impeller of these pumps develops
head only by centrifugal force on the water. The
path of flow through the impeller would be at a
90-degree angle with respect to the pump shaft. A
special design of this pump has a non-clog impeller
which makes it very useful for pumping sewage. This
type of pump is used for pumping small flows and in
applications where a dry pit sump is desirable. It is
generally used in a vertical configuration and can be
constructed to operate in a wet or dry sump. The value
of the NS is typically less than 4,000.
( e ) Net positive suction head.
This term is used to
describe the suction condition of a pump; it is commonly
abbreviated with the letters NPSH. Two forms of NPSH
are used. One is used to describe what suction condition
is available to the pump and is called Net Positive Suction
Head Available (NPSHA), and is a function of the
station layout and suction water levels. NPSHA is
defined as the total suction head in feet of liquid absolute,
determined at the suction nozzle and referred to
datum, less the absolute vapor pressure of the liquid in
feet of liquid pumped. See Appendix B for formula and
terms used. The other term Net Positive Suction Head
Required (NPSHR) is a property of the pump and indicates
what suction condition is required for the pump to
operate without cavitation. NPSHR is determined by the
pump manufacturer by running cavitation tests on the
pump.
5-3. Pump Arrangements...
( a ) Vertical.
Most pumps used in flood-control
pumping stations are of the vertical type. This type of
pump has a vertical shaft with the driver having a vertical
or horizontal shaft arrangement. A vertical motor is
usually direct connected to the pump, whereas a horizontal
motor or engine requires the use of a right-angle gear.
The vertical arrangement usually requires the least floor
space per unit of pumping capacity. While the vertical motor could cost more than the right-angle gear reducer
and higher speed horizontal motor combined, the
decreased reliability and increased operation and maintenance
costs due to the additional auxiliary equipment
involved may offset the first cost savings. One problem
associated with a vertical pump layout is that the pump
dimensions may locate the discharge elbow higher than
the minimum head required by hydraulic conditions. The
higher head will require greater energy. Other type
layouts such as a siphon discharge or volute, horizontal,
and flower pot type pumps will permit lower minimum
heads or in the case of a siphon only the discharge
system losses. Vertical pumps are used with open or
closed sumps, wet or dry, and are suspended from an
operating floor or an intermediate floor.
( b ) Horizontal.
Horizontal type pumps are usually
limited to applications where the total head is less than
6 meters (20 feet) and the quantity of water to be
pumped is large. Horizontal pumps are seldom less than
2,500 millimeters (100 inches) in diameter. Smaller
horizontal pump installations are generally more expensive
than vertical installations. The pumps are not selfpriming,
and the design must provide a separate priming
system.
( c ) Formed suction intake.
Formed suction intakes
are not really a pump type but are suction arrangements
that generally improve flow conditions to the pump.
They are applied to vertical pumps and are used in place
of the standard bell arrangement. Typical dimensions of
a formed suction intake are shown in Figure B-12,
Appendix B.
( d ) Submersible.
(1) General. Submersible pumps are considered for
stations that have pumping requirements with each pump
having a capacity less than 6 m3/s (200 cfs). These
pumps have the electric motor close coupled to the
pumping element with the entire pumping unit being
submerged in water. The size and selection of these
units are limited by the number of poles in the motor or
the size of the gear unit, if used, and its resultant
encroachment on the water passage. These types of
pumps should be removable from above the floor without
any unbolting of the discharge piping. Their use allows
the superstructure of the station to be greatly reduced.
Substructure requirements are approximately the same as
for vertical pumps. Submersible pumps used for flood
control pumping stations are of three different types:
axial flow, mixed flow, and centrifugal volute.
(2) Axial or mixed flow. These pumps consist of an
axial- or mixed-flow impeller close coupled to a submersible
electric motor. The impeller may be on the
same shaft as the motor or a set of gears may be between
the motor and the impeller to permit greater variety of
speed. The pump is suspended above the sump floor
inside of a vertical tube that extends to the operating
floor. The tube allows placement and removal of the
pump and forms part of the discharge piping. These
pumps are used in a wet pit-type sump. Some pumps of
this design are constructed so that the blades are detachable
from the propeller hub and are connected to the hub
in a manner that allows a multitude of blade angle settings.
The blade angle adjustment feature also permits
changing the pump performance characteristics very
easily. This permits a pump installation to meet a different
future hydrology condition with adjustment of the
blade angle.
(3) Centrifugal. These pumps consist of a volute
casing close coupled to a submersible electric motor.
The impeller and motor are on the same shaft. The
pumping unit is guided to its operating position from the
operating floor level by a system of guide rails or cables.
The volute attaches to the discharge piping flange by
means of a bracket using the weight of the pump to seal
the connection. These pumps are used for smaller flows
than the axial- or mixed-flow type and when pumping
heads are high. These pumps are also suitable for use in
a dry pit sump. These pumps are usually equipped with
a water jacket surrounding the motor to cool the motor
with pumped fluid. For special applications, these pumps
can also be fitted with a different diffuser which allows
them to be tube mounted similar to the axial-flow submersible
pumps.
5-4. Selection of Pump Type...
( a ) General.
Many items must be considered during
the pump selection process. Alternative station layouts
should be developed in sufficient detail so that an annual
cost of each layout over the life of the project can be
determined. The annual cost should include the annualized
first cost, operating costs which include cost of
energy, maintenance, and replacement costs. It is usually
best to consider all of the above types of pumps when
developing the station layout unless it is obvious that
certain ones are not applicable. The station layout and
pump selection should be done in sufficient detail to
permit the reviewer to follow the process without reference
to additional catalogs or other such sources.
( b ) Capacity.
The capacity requirement for the pump
is determined from the hydrology requirements of the
station. This information is provided by the H&H
engineers. The number of pumps used should be kept to
a minimum and determined as set forth in
EM 1110-2-3102. If more than one capacity requirement
exists, the pump is selected to satisfy all of the conditions.
This means that the pump will most likely be over
capacity for some of the requirements. Variable capacity
pumping units may be economically justifiable. Variable
capacity can be achieved by using variable speed drives
or pumps that are equipped with variable pitch blades.
( c ) Head.
The head requirements of the pump are
also determined from the hydrology requirements plus
the losses in the pumping circuit which are a function of
the station layout. The pump head requirement is called
total head and is a summation of all heads for a given
capacity. The method of computation of these heads is
included in Chapter 6. Selection of pumps should strive
to achieve the lowest total head requirement to provide
the smallest size driver and lowest energy cost. The best
pump operation occurs when the pump is operating at or
near the head that occurs at the pump’s best efficiency
point. With the wide range of heads that occur for floodcontrol
pumping stations, this is usually not possible.
The pump must be selected to satisfy all the required
conditions. However, if a choice exists, the pump should
be selected so that the best efficiency point is near the
head where the most pumping operation occurs. Some
pumps, particularly the axial flow type, may have a curve
which contains what is called a "dog-leg." This part of
the curve consists of a dip in head which allows the
pump to operate at as many as three different pumping
rates, all being at the same head. Pump operation and
priming at this head must be avoided due to unstable
operation.
( d ) Net positive suction head.
The suction conditions
available for the pump should be determined for all
pumping conditions. A diagram should be prepared
showing the NPSHA for the entire range of pumping
conditions. The method of computation of the NPSHA is
shown in Appendix B. The NPSHA should meet the
margins and limits indicated in Appendix B. In all cases
the NPSHA should be greater than the NPSHR for the
selected pump over the entire range of required pump
operation. Pumps not requiring the cavitation tests
should be specified to meet the suction limits developed
over the entire range of required pump operation and the
suction limit criteria as indicated in Appendix B.
( e ) Efficiency.
Higher efficiencies available from the
different types of pumping units are a consideration when
the estimated amount of operation is great enough to
affect cost considerations. Usually for stations with
capacities less than 14 m3/sec (500 cfs) and operating
less then 500 hours per year, differences in operating
efficiencies of various types of pumping equipment need
not be considered. The highest efficiency that is commercially
attainable should be specified for whatever type
of pump is selected. This will not only control operating
costs but will normally improve the operation of the
pump through less vibration, cavitation, and maintenance
requirements.
( f ) Other considerations.
Certain limitations sometimes guide pump selection.
(1) Incoming electric service. Incoming electric
service may limit the horsepower rating of the driver or
may not permit the use of electric motors.
(2) Foundation conditions. Foundation conditions
may increase the cost of excavation to the point where it
may not be feasible to lower the sump to that required
for some types of pumps.
(3) Available space. The available space at the
proposed station site may limit the size of the station.
(4) Low discharge capacity. Axial- and mixed-flow
pumps may have too small flow passages and would
therefore be subject to clogging. A centrifugal pump
would then be used because of its greater solid passing
capability.
( g ) Selection procedure.
The first step in developing
a pump selection is to determine the approximate pump
operating conditions. Total heads used for these approximate
operating conditions can be determined from adding
the static heads (discharge pool level or pump discharge
elevation minus the lowest pump suction level) to an
approximation of the system losses plus the velocity
head. Use the capacities from the hydrology requirements,
the approximate total heads, and Chart B-1 in
Appendix B to determine the types of pump that may be suitable for the conditions. Using each pump type
selected from the chart, a pump selection is made using
the method indicated in Appendix B. A station layout
for each type of pump can be developed. Dimensions for
the pumping equipment and sump dimensions can be
obtained from the procedure given in Appendix B. It
may be necessary to refine the heads and therefore the
station layout due to changes in head when the equipment
is selected and located in the station. The information
from the final pump station layout should be sent to
a minimum of two pump manufacturers requesting their
selection of recommended pumping equipment for the
given station layout. It is important that the communication
with the pump manufacturers takes place during the
design memorandum phase of the project. See Chart B-3
in Appendix B for a typical pump manufacturer data
sheet. The information thus obtained should be used to
correct, if necessary, the station layout and finalize the
alternate study layouts and costs. Operation, maintenance,
and equipment replacement costs must also be
considered in the selection of the type of station to use.
Operation costs should consider the cost of energy and
operating labor when the station is in operation. In some
cases, these costs are very small due to limited operation
and the detail in those cases can be limited. When the
estimated operating costs for a station exceed
$10,000 per year, it could be necessary to use a detailed
energy cost analysis based on pump head, cycling effect,
and any special considerations the supplier of the energy
may require. Maintenance cost should be carefully considered
since it goes on whether the station is in operation
or not. The tendency is to underestimate this
expense. Discussion with the eventual user could aid the
designer in determining the maintenance methods that
will be used. Replacement costs should be based on both
wear out and obsolescence of the equipment. Equipment
replacements are also made when the cost of maintenance
becomes excessive and the reliability of the equipment
is in doubt. Equipment manufacturers usually
provide the expected life of their equipment while operating
under normal conditions. When equipment operation
will occur beyond the normal conditions, as defined by
the manufacturer, the expected life should be adjusted
accordingly. Selection is then based on annual costs and
reliability factors.