Sequencing Batch Reactors - 3...
Introduction...
Batch processes are not a new or innovative wastewater treatment technology, since the first reported fill/draw systems
are at least a century old. The sequencing batch reactor (SBR) process has been successfully applied to more than 1,300 plants in the U.S., Canada, and Europe within the last 25 years. In particular, the number of SBR plants in North America
is growing rapidly. Many of these facilities have been constructed for small communities, producing less than 1.0 million gallons per day (mgd) of wastewater, although larger plants (up to 230 mgd in Dublin, Ireland) have used SBR technology
with similar effluent quality results.
Both municipal and industrial wastewater has been successfully treated in SBR systems. A general overview of SBR reactor systems and the technology is presented here, along with a discussion of the additional enhancements of a hybrid SBR
designed by Pacific Advanced Civil Engineering, Inc. (PACE) and constructed by Pacific Environmental Resources Corporation, Inc. (PERC). A real-world application using the PACE/PERC design is evaluated.
Benefits of Using SBR Treatment...
- A higher degree of operational flexibility with respect to effluent quality and dissolved oxygen (DO) controlled aeration system
- Complete quiesct settling for improved total suspended solids (TSS) removal
- Effluent quality meets current and anticipated future nitrogen requirements for surface discharge
- No seperate clarifiers
- Proven treatment process capacity upgrades and phasing do not require modification or interruption of current treatment process
- A high degree of automation reduces operational staff requirements
- Significantly smaller footprint requires less site work on yard plumbing
- Lower initial capital cost
- Power consumption is typically less than that of a conventional plant with substantial pwer savings at lower flows
(i.e., greater turndown capability)
Limitations of SBR Systems...
Limitations of SBRs are generally related to the education of the operating staff and do not focus on the process
elements. Therefore, SBRs often require :
- A higher level of control sophistication
- Knowledgeable operators
- Some retraining of existing operations staff
- Two or more basins or a pre-equalization tank for process operation and redundancy
History and Evaluation of SBRs...
The use of batch processes for treating wastewater is not a recent development; batch processes have been in development
and use since the turn of the century. However, facility design moved to continuous flow or "conventional" systems after
1920 due to the high degree of operator attention and automation required for SBRs. The clogging of air diffusers caused
by periodic settling of sludge on the air diffusion systems in SBRs also increased the complexity of their operation.
In the early 1960s, interest was revived in batch systems with the development of new technology and equipment, most significantly the micro-processor. In addition, improvements in aeration devices and control systems have allowed the development of the "fill-and-draw" systems to their present level of efficiency and now enable SBRs to successfully
compete with, and in most cases outperform, conventional activated sludge systems.
The biological and physical unit processes involved in the SBR and conventional activated sludge systems are essentially
the same. Aeration and sedimentation/clarification are performed in both systems. However, there is one important
difference. The processes in the conventional plant are carried out simultaneously in separate tanks; whereas, in the SBR process, treatment takes place sequentially in a common "reactor" tank.
The reactor in an SBR system has five basic operating modes. Listed sequentially in the treatment process, they are
( 1 ) fill, ( 2 ) react, ( 3 ) settle, ( 4 ) draw, and ( 5 ) idle. These modes of the SBR are controlled by time to
achieve the effluent quality and treatment capacity objectives.
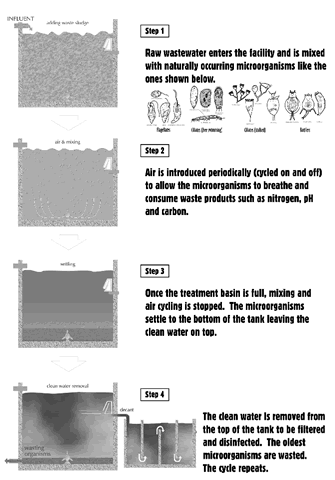
A major advantage of the SBR system compared to the conventional system is its flexibility to adapt and modify reactor conditions through time controls or dissolved oxygen settings during the operational phases. The computer controls allow
the operator the ability to change the effective size/volume of the aeration, anoxic, and clarification processes to
achieve effluent goals. This allows SBR facilities to adapt to changing influent loading conditions and consistently
maintain the objective effluent water quality. A description of the different modes follows (see Figure 1 and Figure 2).
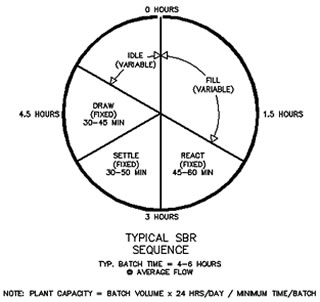
Fill Mode...
The purpose of the fill operation is to add substrate (raw wastewater or primary effluent) to the reactor. The time
allocated to the fill mode is variable and depends on the influent flow rate. Typically, SBRs are designed to have a
minimum fill time that corresponds to the peak hour flow (PHF) rate of the facility. Aeration and mixing are typically
cycled on and off during fill to provide a substantial amount of substrate reduction, nitrification, and denitrification.
React Mode...
Air is introduced periodically to the process to allow the microorganisms to breathe and consume waste products.
The purpose of the react mode is to complete the reactions that were initiated during fill. The SBR tank is isolated from
receiving any new substrate while in react, usually through an influent control valve. The remaining raw influent wastewater
is directed to the next SBR in series while the first SBR completes react, settle, and draw. As with fill mode, performance
considerations might require alternating periods of high and low dissolved oxygen (DO) concentrations.
Settle Mode...
All aeration and mixing is terminated during the settle and draw modes, and the reactor tank is allowed to dissipate
all hydraulic energy developed due to the mixing operations.The purpose of settle mode is to allow solids separation to
occur, which provides a clarified supernatant to be discharged as effluent. In an SBR, this process is normally much more efficient than in a continuous flow system because the influent flow to the reactor is zero; therefore, the effective clarification overflow rate is zero gallons per day per square foot (i.e., the reactor is allowed to settle in a completely quiescent environment). The SBR has the ability to provide optimum settling conditions and eliminate hydraulic influences.
Draw Mode...
The purpose of draw mode is to remove clarified or treated water from the reactor. Many types of decant mechanisms are in current use, the most popular being floating or adjustable weirs. The decanting rate can be controlled by automatic valves
in a gravity system or by pumping.
Idle Mode...
The purpose of idle mode in a multi-tank system is to provide "park" or stand-by time for the SBR just completing its
batch cycle while waiting for the other SBR reactor to complete its fill mode. Idle is not a necessary phase and can be eliminated if variable volume batches are included in the design of the system. Length of time in idle is determined by
the flow rate of wastewater into the plant.
Important...
A key element in understanding the SBR process and operation is that a reactor is never completely emptied during the
batch process. Typically, 25 percent of the volume of the tank is decanted during the draw phase, retaining nearly 100 percent of the activated sludge within the tank. The advantage is that this establishes a population of microorganisms uniquely suited to treating the waste-water without the need for a return activated sludge (RAS) pump station. The microorganisms are subject to high and low oxygen and to high and low food availability during the process. This operating condition in the SBR develops a population of organisms that are very efficient at treating site-specific waste-water constituents.
Sludge wasting is another important step in the SBR operation that greatly affects performance and effluent water quality.
It is not included as one of the five basic basin modes because wasting strategies differ between SBR designs. Sludge
wasting usually occurs during the settle or draw phases and depends upon the desired sludge age and process requirements.
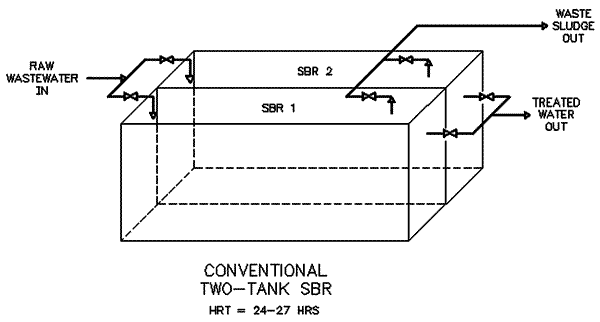
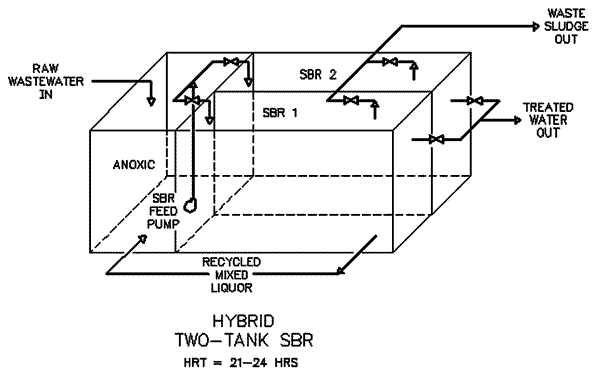
Description and Advantages of a Hybrid SBR...
Many significant advantages have been identified for application of a conventional SBR process; however, new hybrid
designs have improved the benefits of this system and the potential applications. The hybrid SBR combines the advantages
of the batch process with a conventional anoxic prereactor. This hybrid design adds the prereactor as an additional
facility element in the system. The prereactor may be configured to act as a surge basin (e.g., Fluidyne Surge Anoxic Mix)
or as a high F/M Bio-Selector (e.g., Austgen Biojet ICEAS). The major advantage of the hybrid configuration is in the aeration system sizing and bio-nutrient removal capacity. Air is cycled on and off with conventional SBRs during fill and react modes to create aerobic and anoxic conditions within one reactor tank. Since the same tank is used for clarification (i.e., settle and draw), the aeration time available per day is described by the following equation :
Aeration Time (per day) = ( 1,440 min / day ) x ( Settle Time + Draw Time + Anoxic Time ) ( batches / day )
This amount of time equates to about 8–9 hours/day of aeration in most SBR designs. If the design process is required to nitrify and denitrify, then the oxygen requirement is the same as conventional nitrification/denitrification in a
biological nutrient removal facility. The oxygen demand must be delivered in one third of the time; therefore, conventional
SBRs would typically have two to three times the installed horsepower for aeration, which leads to higher capital investment
in mechanical and electrical equipment.
Mixed-liquor suspended solids (MLSS) in the hybrid design are recycled back from the SBR to the anoxic prereactor for denitrification. This allows the SBR reactor to remain fully aerobic, and simultaneous nitrification (in the SBR) and denitrification (in the anoxic prereactor) can occur, reducing the installed aeration horsepower requirement. In addition, the denitrification kinetics are increased substantially, as the recycled, nitrified MLSS is contacted with raw wastewater, constituting a high carbon source, in a smaller, completely mixed reactor. This condition ensures that the process is not carbon limited and eliminates the need for chemical addition (e.g., methanol or acetate) to meet stringent total nitrogen limits imposed for some facility discharge permits. The figures below present the process schematics for both the conventional and hybrid SBR designs. As can be seen from the figures, the footprint and operation are only slightly different, while performance is greatly enhanced.
Application of a Hybrid SBR...
Barona Valley Ranch Resort and Casino is located just outside of the City of San Diego, in Lakeside, California. It is one
of the largest Indian-owned and operated casino facilities in California and began operation in 1994. The complex has undergone considerable expansion since that time and has required the tribe to invest in wastewater infrastructure to
support its very successful enterprise. In 1999, Barona broke ground on a massive expansion that included a 400-room resort hotel, an 18-hole championship golf course, an events center, and a new 300,000-square-foot casino. Barona retained PACE and PERC as a design/build team to determine the best course of action for their waste-water treatment needs. PACE and PERC conducted extensive meetings with the Barona Band of Mission Indians to obtain information concerning the following utility needs : ( 1 ) financial issues, ( 2 ) future growth possibilities, ( 3 ) land use, ( 4 ) aesthetic impacts, ( 5 ) water quality, and ( 6 ) environmental concerns. Determining the best design alternative to meet Barona’s need for compliance
with tough California regulations involved analyzing two treatment technologies that provide nitrogen removal : oxidation ditch and SBR. The feasibility evaluation focused on cost of construction, anticipated effluent quality, and cost of operations and maintenance.
The results from the comparison of these two alternatives indicated that the SBR, specifically the hybrid SBR, offered advantages in terms of construction costs, land required, ease of expansion, and operational flexibility that
made it the most viable treatment alternative. The treatment facility that was designed consisted of a 0.375-mgd, two-tank SBR and a dedicated, variable-volume, anoxic pre-reactor that serves as a front-end hydraulic surge tank and biological selector, as well as a high-rate denitrification reactor, tertiary filtration, medium pressure ultraviolet disinfection,
and a two-stage aerobic sludge digestion process. The facility is expandable up to 1.2 mgd with the addition of two more reactor tanks to meet future needs. The plant design was developed with control and mechanical buildings directly above
the underground tanks to confine and mitigate potential noise and odors. PACE and PERC’s innovative hybrid SBR design
allowed for accelerated construction and delivery of the project. The design/build contract was signed in February of
1999, with project completion and start-up of the turnkey design/build water reclamation facility (WRF) in January 2000
(11 months).
Design Parameters...
The design of the facility was based on having to treat extremely strong commercial wastes with varying concentrations of BOD, TSS, and ammonia. A preliminary site analysis conducted by PACE indicated that the average BOD, TSS, and ammonia were 700 mg/L, 300 mg/L, and 50 mg/L respectively. As the project progressed, modifications to the sewer collection system and waste disposal operations increased the BOD to 1,200–1,500 mg/L average, with increases for ammonia up to 80 mg/L. Most of these increases can be attributed to fats, oils, and grease (FOG), which average 250 mg/L in the incoming waste stream and additional casino customers gained by the new casino expansion. PACE and PERC were confident that the hybrid SBR design
would have the flexibility to treat the additional loading.
The facility has been operating for two and half years, and the effluent water quality has consistently exceeded the design specifications. Effluent BOD, TSS, and total nitrogen have been averaging less than 3 mg/L, less than 1 mg/L, and less than
2 mg/L, respectively. Although the facility averages less than half (150,000 gpd) of the design flow, only one of the two
SBR reactors and the anoxic pre-reactor are on-line. The other SBR reactor has been idle since start-up. Table 1 provides a summary of influent and effluent design parameters along with two-year actual influent and effluent averages.
Table 1. Description of the Influent and Effluent Parameters for the Barona WRF.
Parameter |
Design |
Two-Year Actual |
Influent |
Effluent |
Influent |
Effluent |
Flow (mgd) |
0.375 |
0.375 |
0.150 |
0.150 |
BOD (mg/L) |
700 |
< 5 |
1,250 |
< 3 |
TSS (mg/L) |
300 |
< 5 |
450 |
< 1 |
NH3 (mg/L) |
50 |
< 1 |
65 |
< 1 |
TN (mg/L) |
NA |
< 5 |
NA |
< 2 |
Turbidity (NTU) |
NA |
< 2 |
NA |
0.37 |
Operations Program and Training...
As part of the design/build contract, PACE and PERC provided a 2-week start-up and 6-month training and operations program that provided operators with the analytical tools and training to operate the new facility in compliance with the design specifications. This portion of the contract includes training in mechanical equipment service, electrical/control panel troubleshooting, biological treatment processes, laboratory analysis, sludge digestion and processing, and system
operation.
The educated staff operators were able to operate the plant more efficiently and provide preventive maintenance, thereby significantly reducing overhead costs. This properly run facility was able to use less power, produce less sludge, and provide higher quality water without additional expense. PACE and PERC provided educational experiences that allowed
Barona’s staff to operate the plant at a high quality level with minimum supervision.
The Barona Hybrid SBR wastewater treatment facility, two years after the treatment plant startup, has consistently
outperformed its design parameters while treating wastewater in excess of its design loading concentrations. The
flexibility of the hybrid SBR design ensures achievement of excellent performance results under widely varying hydraulic
and organic loading conditions. In addition, compared to conventional design, the design resulted in a more cost-effective and significantly reduced land requirement.