Secondary Treatment...
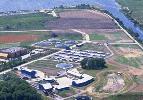
In an average strength wastewater the total solids may be classified as being organic or inorganic in origin. In terms of
the size of the solids, the distribution is approximately thirty percent suspended, six percent colloidal and about
sixty-five percent dissolved solids. The function of primary treatment is to remove as much of the suspended solids as
possible. Primary treatment utilizes clarifiers or settling tanks which remove the settleable organics and settleable
inorganic solids from the wastewater. The effluent from primary treatment therefore contains mainly colloidal and dissolved
organic and inorganic solids. Recent effluent standards and water quality standards required a greater degree of removal of
organics from wastewater than can be accomplished by primary treatment. This additional removal of organics can be
accomplished by secondary treatment. The secondary treatment process consists of the biological treatment of wastewater by
utilizing many different types of microorganisms in a controlled environment. In the biological treatment of wastewaters, a
mixed population of microorganisms utilizes the colloidal and dissolved organics found in the effluent from the primary
treatment as their man food supply. In consuming these organics, the microorganisms utilize part of the organic substances
to obtain the energy needed for their life activities. When the oxidation of organics occurs in the presence of dissolved
oxygen the end products include carbon dioxide, water, sulfates, nitrates, and phosphates. The remainder part of the
consumed organics are used as building blocks in a series of synthesis (reproduction) reactions that result in an increase
population of microorganisms. Therefore, the colloidal and dissolved organics originally present in the wastewater have
been transformed in part into a stable form, such as carbon dioxide, and part into a viable biological mass. This
biochemical reaction is active in all biological treatment processes. The biological mass must subsequently be separated
from the wastewater to ensure a proper degree of treatment within effluent and water quality standards. If this biological
mass is not properly removed from the waste stream, usually by final clarification, effluent quality will be degraded and
a higher BOD and S.S. load will be placed on the receiving waters. In the activated sludge process the microorganisms are
dispersed throughout the water phase. While in trickling filters or biodiscs the microorganisms are attached to a fixed
surface forming a biological film. In either, the microorganisms are doing the treatment and therefore all precautions must
be taken to assure a favorable environment for their life cycle.
Trickling Filters...
A trickling filter consists of a bed of highly permeable media on whose surface a mixed population of microorganisms is
developed as a slime layer. The word "filter" in this case is not correctly used for there is no straining or filtering
action involved. Passage of wastewater through the filter causes the development of a gelatinous coating of bacteria,
protozoa and other organisms on the media. With time, the thickness of the slime layer increases preventing oxygen from
penetrating the full depth of the slime layer. In the absence of oxygen, anaerobic decomposition becomes active near the
surface of the media. The continual increase in the thickness of the slime layer, the production of anaerobic end products
next to the media surface, and the maintenance of a hydraulic load to the filter, eventually causes sloughing of the slime
layer to start to form. This cycle is continuously repeated throughout the operation of a trickling filter. For economy and
to prevent clogging of the distribution nozzles, trickling filters should be preceded by primary sedimentation tanks
equipped with scum collecting devices. Primary treatment ahead of trickling filters makes available the full capacity of the
trickling filter for use in the conversion of non-settleable, colloidal and dissolved solids to living microscopic organisms
and stable organic matter temporarily attached to the filter medium and to inorganic matter temporarily attached to the
filter medium and to inorganic matter carried off with the effluent. The attached material intermittently sloughs off and
is carried away in the filter effluent. For this reason, trickling filters should be followed by secondary sedimentation
tanks to remove these sloughed solids and to produce a relatively clear effluent.
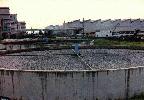
Construction and Design...
The primary factors that must be considered in the design of trickling filters include : ( 1 ) The type of filter media to
be used, ( 2 ) The type and dosing characteristics of the distribution system, and ( 3 ) The configuration of the underdrain
system.
( 1 ) Filter Media : The ideal filter medium is a material that has a high surface area per unit volume, is low in cost, has a high durability, and does not readily clog. The choice of filter media is more often governed by the material
locally available which may include field stone, gravel, broken stone, blast furnace slag and antracite stones. Stones less
than one inch in diameter do not provide sufficient pore space and may therefore result in plugging of the media and
ponding. The tendency is to use larger sizes with 2 1/2 inches in diameter now considered the minimum size. Large diameter
stones tend to avoid ponding situations but also limit the surface area per unit volume available for the slime layer to
grow. An upper size limit of about 4 inches is therefore recommended.
( 2 ) Distribution System : The rotary distributor has become standard for the trickling filter process because of
its reliability and ease of maintenance. The rotary distributor consists of a hollow vertical center column carrying two or
more radial pipes or arms, each of which contains a number of nozzles or orifices for discharging the wastewater onto the
bed. All of these nozzles point in the same direction at right angles to the arms and the reaction of the discharge through
them causes the arms to revolve. The necessary reaction is furnished by a head of 18" to 24". The speed of revolution will
vary with the flow rate, but it should be in the range of one revolution in 10 minutes or less for a two-arm distributor. A
dosing tanks and siphon should be provided for standard rate trickling filters to shut off the flow when the head falls
below that necessary to revolve the arms at the required speed. In some cases positive drive mechanisms are being
used.
A clearance of 6 to 9 inches should be allowed between the bottom of the distributor arm and top of the bed. This will
permit the waste streams from the nozzles to spread out and cover the bed uniformly, and it will also prevent ice
accumulation from interfering with the distributor motion during freezing weather. Fixed spray nozzles were used when
trickling filters were first developed. The nozzles were attached to pipes laid in the filter medium and were fed
intermittently from a siphon controlled dosing tank. By this method, wastewater is applied to the filter for short
periods of time. Between applications the filter has rest periods while the dosing tank is filling. Many types and
shapes of nozzles were developed and the siphon dosing tank was designed to attain the best possible even distribution
of wastewater over the entire surface of the filter. At best, the distribution was not even and there were areas of the filter on which very little wastewater was sprayed. In addition, due to the greater number of nozzles used for the
distribution of the wastes, clogging and increased operational and maintenance problems were encountered.
( 3 ) Underdrain System : The underdrain system in trickling filters serves two purposes: (a) to carry the
wastewater passing through the filter and the sloughed solids from the filter to the final clarification process, and
(b) to provide for ventilation of the filter to maintain aerobic conditions. The underdrains are specially designed
vitrified clay blocks with slotted tops that admit the wastewater and yet support the media. The blocks are laid directly
on the filter floor, which is sloped toward the collection channel at a 1 to 2 percent gradient. Since the underdrains also
provide ventilation for the filter it is desirable that the ventilation openings total at least 20% of the total floor area.
Normal ventilation occurs through convection currents caused by a temperature differential between the wastewater and the
ambient air temperature. In deep filters or heavily loaded filters, there may be some advantage in force ventilation.
Filter Classification...
Trickling filters are classified by hydraulic or organic loading, as high-rate or low-rate. The organic load on a filter is
the BOD content in pounds applied to the filter. This is usually expressed as pounds of BOD per day per 1000 cubic feet of
filter medium or pounds of BOD per day per acre foot. The hydraulic load, including recirculation flow if used, is the
gallons of flow per acre of filter surface per day. Low-rate filters are relatively simple treatment units that normally
produce a consistent effluent quality even with varying influent strength. Depending upon the dosing system, wastewater is
applied intermittently with rest periods which generally do not exceed five minutes at the designed rate of waste flow.
With proper loadings the low-rate trickling filter, including primary and secondary sedimentation units, should remove from
80 to 85 percent of the applied BOD. While there is some unloading or sloughing of solids at all times, the major unloadings
usually occur several times a year for comparatively short periods of time. High-rate filters are usually characterized by
higher hydraulic and organic loadings than low-rate filters. The higher BOD loading is accomplished by applying a larger
volume of waste per acre of surface area of the filter. One method of increasing the efficiency of a trickling filter is to
incorporate recirculation. Recirculation is a process by which the filter effluent is returned to and reapplied onto the
filter. This recycling of the effluent increases the contact time of the waste with the microorganisms and also helps to
"seed" the lower portion of the filter with active organisms. When recirculation is used, the hydraulic loading per unit
area of filter media is increased. As a result, higher flow velocities will usually occur causing a more continuous and
uniform sloughing of excess growths. Recirculation also helps to minimize problems with ponding and restriction of
ventilation. Recirculation can be continuous or intermittent. Return pumping rates can either be constant or variable.
Sometimes recycling can be practiced during periods of low flow to keep the distributors in motion, to prevent the drying
of the filter growths, and to prevent freezing during colder temperatures. Also, recirculation in proportion to flow may be
utilized to reduce the organic strength of the incoming wastes, and to smooth out diurnal flow variations. Recirculation
can be accomplished by various techniques. Some of which are as follows :
Biofilter : The bio-filter is a high-rate filter, usually 3 to 4 feet in depth, employing recirculation at all
times. The recirculation in this case involves bringing the effluent of the filter or of the secondary sedimentation tank
back through the primary settling tank. The secondary settling tank sludge is usually very light and can be continually
fed back to the primary settling tank where the two types of sludges are collected together and pumped to the
digester.
Accelo - Filter : The accelo-filter includes recirculation of unsettled effluent from the filter back to the inlet
of the filter distributor. It is used for both low-rate and high-rate filters, the former being applicable if a well
nitrified effluent is required.
Aero Filter : The aero-filter is still another process which distributes the wastewater by maintaining a continuous
rain-like application of the wastewater over the filter bed. For small beds, distribution is accomplished by a disc
distributor revolving at a high speed of 260 to 369 rpm set 20" above the surface of the filter to give a continuous
rain-like distribution over the entire bed. For large beds a large number of revolving distributor arms, 10 or more, tend
to give more uniform distribution. These filters are always operated at a rate in excess of 10 million gallons per acre of
surface area per day.
High-rate trickling filters, including primary and secondary sedimentation, should, under normal operation, remove from 65
to 85 percent of the BOD of the wastewater. Recirculation should be adequate to provide continuous dosage at a rate equal
to or in excess of 10 million gallons per acre per day. As a result of continuous dosing at such high rates, some of the
solids accumulated on the filter medium are washed off and carried away with the effluent continuously. High-rate trickling
filters have been used advantageously for pretreatment of industrial wastes and unusually strong wastewaters. When so used
they are called "roughing filters". With these filters the BOD loading is usually in excess of 110 pounds of BOD per 1000
cubic feet of filter medium. Generally, most organic wastes can be successfully treated by trickling filtration. Normally
food processing, textile, fermentation and some pharmaceutical process wastes are amenable to trickling filtration. Some
industrial wastewaters which cannot be treated by trickling filtration are those which contain excessive concentration of
toxic materials, such as pesticide residues, heavy metals, and high acidic and alkaline wastes. Since the organisms growing
on the media are temperature dependent, climatic changes will affect the filter's performance. The organisms metabolic rate
increases with increasing temperature and warmer weather. Therefore, higher loadings and greater efficiencies are possible
in warmer temperatures and climates, if aerobic conditions can be maintained in the filter.
Common Problems...
Due to its simple design, in actual operation the trickling filter is one of the most trouble-free types of secondary
treatment processes. It requires much less operating attention and process control than the activated sludge system, but
some problems do exist. The following is a summary of some of the more common problems and cures :
1. Ponding is normally the result of : (a) excessive organic loading without a corresponding higher recirculation rate,
(b) use of media which is too small, (c) clogging of underdrain system, (d) non-uniform media size or breaking up of
media, and (e) trash or debris in filter voids.
Ponding can cause odors and decrease filter efficiency. Minor Ponding can be eliminated by : 1. Spraying the surface with
high pressure water hose. 2. Stirring or agitating ponding area with stick, rake, etc. 3. Dousing the filter with chlorine.
Applying chlorine to a ponding filter by chlorinating at the dosing tank to produce a residual of about one to two mg/L at
the nozzles may help reduce ponding. Chlorination is continued until the filters are free. There may be some deterioration
of efficiency of the filters during chlorination. Obviously, if ponding is caused by the size of the media, chlorination
will be of no benefit. If the ponding is caused by overloading, chlorination may be of temporary benefit. If ponding was
caused by excessive growths, this deteriorating condition will usually not return until conditions, such as temperature,
that caused the excessive growth are repeated. 4. Flooding filter and keeping the media submerged for approximately 24
hours will sometimes cause the growth to slough. Growths become anaerobic and tend to release from media. 5. Shutting off
the flow to the filter. The growths will die and tend to be flushed out when the unit is put back into service.
2. Odors : Since the trickling filter is an aerobic process, no serious odors should exist. If foul odors are present,
anaerobic conditions are the most likely cause. Anaerobic conditions usually predominate next to the media surface.
If the surface of the slime growth is aerobic, odors should be minimal. If odors are present, corrective action should be
taken immediately or the condition could get worse. Some corrective measures are : 1. Try to maintain aerobic condition in
the collection system and in the primary treatment units. 2. Check the ventilation of the filter for clogging and stoppages.
3. Check the underdrain system for clogging and stoppages. 4. Increase recirculation rate; this usually provides added
oxygen to the filter and may increase sloughing. 5. Keep wastewater in filter; do not allow it to splash on exposed
surfaces, weeds, or grass. 6. Add odor-masking agents. 7. Pre-chlorination at primary tank influent or at the dosing tank.
The dose used is not sufficient to produce residual chlorine but only to destroy the odors. Chlorination to a residual of
less than 0.5 mg/L normally does not interfere with the activity of the living organisms and thus does not affect the
purification obtained by the operation of a trickling filter. However, chlorination of a trickling filter influent cannot
be used until after the filter has been in active operation. Except in a large plant, the chlorine dose is generally set
at about half the chlorine demand and not adjusted for moderate variations in flow or strength. 8. Induce unloading of a
trickling filter. A shock dose of chlorine that will produce a residual of about 10 mg/L in the filter influent may be
applied. It requires a fairly large dose of chlorine to produce this amount of residual. As it is only to be maintained
for a short period of time, it is most economical to apply during the night when the flow is low and the chlorine demand
at a minimum. The chlorine is applied at the dosing tank, generally by making a slurry of liquid hypochlorites and pouring
it into the dosing tank. Two dosing discharges containing 10 mg/L residual are generally enough to cause the filter to
unload the next day. A word of caution -- when a filter is made to unload it does so quickly if at all and a very large
volume of secondary sludge is produced in one or two day. Addition of this large quantity of sludge to the digesters has
caused foaming on occasions. It should be noted that sometimes during hot weather odors will be noticeable even from a
filter in good operating condition. This problem can be eliminated by the use of masking agents.
3. Filter Flies are a nuisance to plant personnel and nearby neighbors : These tiny, gnat-size flies are called psychoda.
They are occasionally found in great numbers, preferring an alternate wet and dry environment for development. The flies
are most frequently found in low or standard rate filters with an intermittent dosing system. Control can be accomplished
by : a. Increasing recirculation. A continuous waste flow to the filter will tend to wash fly larvae from the filter. b.
Flushing the side walls of the filter by opening the flap valve at the end of the distributor arm. c. Flooding the filter
intermittently to prevent completion of the fly life cycle. This life cycle can be as short as seven days in warm weather.
Filters should be flooded for approximately 24 hours. d. The addition of chlorine, which is toxic to the flies and larvae.
e. Keeping the plant grounds neat, clean and free from excessive weeds, plants, and grass, which are excellent breeding
grounds for the flies.
4. Weather Problems : Cold weather can cause an occasional build-up of ice on the media, walls, distributor arms and
orifices, resulting in operating problems and loss of efficiency. During cold temperatures, the organism's metabolic
process slow down and as a result efficiency decreases. Measures which can be implemented to reduce cold weather problems
are : a. Decrease the recirculation rate to prevent splashing at distributor arm, but maintain sufficient flow to keep the
filter working. b. Adjust orifices at splash plates to reduce the spraying effect. c. Construct wind screens or covers to
reduce heat loss. d. Break up any ice build-up. e. Partially open flap gates at end of distributor arm to allow for a
stream of water rather than a spray of water. Warm weather creates its own unique problem areas as previously
discussed.
a. Ponding resulting from sloughings due to excessive organism growth. b. Odors resulting from anaerobic conditions. The
dissolved oxygen demand is higher in warmer weather due to higher organism activity. c. Filter Flies d. Degradation of
final effluent due to excessive loading from sloughings on final sedimentation tanks.
Rotating Biological Contactors (RBC)...
The rotating disc process has been used in Europe for many years to treat both municipal and industrial wastewaters. The
process operates as a fixed-film biological reactor. A biological film or bio-mass grows on the surface of a series of
discs mounted on a shaft and placed in a tank conforming to the general shape of the discs. The discs are usually of
plastic or some other non-corrosive durable material. The discs are slowly rotating while approximately one-third to
one-half immersed in the wastewater being treated. The rotation rate is usually around 2 - 4 rpm. As the disc rotates,
an attached microbial population forms a film that becomes several millimeters thick. Rotation of the disc brings the
attached biologic film into contact with the wastewater for removal of the organics and with the atmosphere for absorption
of oxygen. Excess bio-mass generated during the cycle is stripped off by shearing forces exerted as the discs rotate. The
excess bio-mass is usually then removed in a clarifier that follows the rotating disc process. The process has shown to be
effective in the treatment of wastewater with removals up to 95 percent for a disc surface loading of 2 to 3 gpd/sq.ft. of
surface area. The process is inherently stable under conditions of fluctuating hydraulic and BOD loads. The use of simple
mechanical components for the process hardware also results in very low maintenance cost. Maintenance is largely limited to
greasing of bearings and inspecting the chains and sprockets for wear and slack. The low disc speed used in the bio-disc
process achieves sufficient mixing and aeration while consuming relatively little power. This process, like all biological
treatment processes, does have its limitations. Organic and hydraulic shock loads as well as toxic discharges will tend to
decrease process efficiency. Since the metabolic rate of the bio-mass is temperature dependent, process efficiency would be
expected to decrease during colder temperatures. Therefore, RBC are usually covered or enclosed. The rotating disc process
is normally designed on the basis of hydraulic loading. At a specific hydraulic loading rate there is a specific percentage
of BOD reduction. Thus, the percentage of BOD reduction is mainly a function of the hydraulic loading rate and hydraulic
detention time. One inherent limitation of the RBC is the lack of operational flexibility. Once the plant is designed and
installed, little can be done to alter the operation. In activated sludge processes, flexibility and adjustments must be
incorporated in the design to meet changing conditions. On the other hand, the RBC's lack of flexibility (no alternate flow
schemes or modes of operation, etc.) gives the process simplicity and stability. As long as the discs and media keep
rotating and the hydraulic loading remains within the design capacity, the RBC normally will function properly.
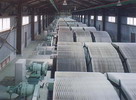
Activated Sludge...
The activated sludge process was developed in England in 1914 and was so named because it involved the production of an
activated mass of microorganisms capable of aerobically stabilizing the organic content of a waste. Activated sludge is
probably the most versatile of the biological treatment processes capable of producing an effluent with any desired BOD.
The process has thus found wide application among domestic wastewater and industrial wastewater treatment. Like the
trickling filter, activated sludge is a biological contact process where bacteria, fungi, protozoa and small organisms such
as rotifers and nematode worms are commonly found. The bacteria are the most important group of microorganisms for they are
the ones responsible for the structural and functional activity of the activated sludge floc. All types of bacteria make up
activated sludge. The predominate type of bacteria present will be determined by the nature of the organic substances in
the wastewater, the mode of operation of the plant, and the environmental conditions present for the organisms in the
process. Fungi are relatively rare in activated sludge. When present, most of the fungi tend to be of the filamentous forms
which prevent good floc formation and therefore decrease the efficiency of the plant. A high carbohydrate waste, unusual
organic compounds, low pH, low dissolved oxygen concentrations, and nutrient deficiencies stimulate fungi growths. The
other forms of microorganisms present in activated sludge play a minor role in the actual stabilization of the organics
in wastewater.
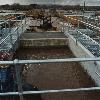
Process Design Consideration...
The activated sludge process is usually employed following primary sedimentation. The wastewater contains some suspended
and colloidal solids and when agitated in the presence of air, the suspended solids form nuclei on which biological life
develop and gradually build up to larger solids which are known as activated sludge. Activated sludge is a brownish
floc-like substance consisting of organic matter obtained from the wastewater and inhabited by myriads of bacteria and
other forms of biological life. Activated sludge with its living organisms has the property of absorbing or adsorbing
colloidal and dissolved organic matter. The biological organisms utilize the absorbed material as food and convert it to
inert insoluble solids and new bacterial cells. Much of this conversion is a step-by-step process. Some bacteria attack the
original complex substances to produce simpler compounds as their waste products. Other bacteria use the waste products to
produce sill simpler compounds and the process continues until the final waste products can no longer be used as food for
bacteria. The generation of activated sludge or floc in wastewater is a slow process and the amount so formed from any
volume of wastewater during its period of treatment is small and inadequate for the rapid and effective treatment of the
wastewater which requires large concentrations of activated sludge. Such concentrations are built up by collecting the
sludge produced from each volume of wastewater treated and re-using it in the treatment of subsequent wastewater flows.
The sludge so re-used is known as returned sludge. This is a cumulative process so that eventually more sludge has been
produced and is available to maintain a viable biological population of organisms to treat the incoming wastes. The surplus,
or excess activated sludge, is then permanently removed from the treatment process and conditioned for ultimate disposal.
The activated sludge must be kept in suspension during its period of contact with the wastewater being treated by some
method of agitation. The activated sludge process, therefore, consists of the following steps : 1. Mixing the activated
sludge with the wastewater to be treated (mixed liquor). 2. Aeration and agitation of this mixed liquor for the required
length of time. 3. Separation of the activated sludge from the mixed liquor, in the final clarification process. 4. Return
the proper amount of activated sludge for mixture with the wastewater. 5. Disposal of the excess activated sludge.
Mixing the Activated Sludge with the Wastewater to be Treated : The first step in the activated sludge process is to
bring the microorganisms in contact with the organics of the wastewater. This is generally accomplished by the rapid mixing
of the return sludge with the wastewater at the inlet of the aeration tank. In some cases small mixing chambers are
provided, but this is not the common practice.
Aeration and Agitation of Mixed Liquor : Aeration serves at least three important functions: (1) mixing the returned
sludge with effluent from primary treatment, (2) keeping the activated sludge in suspension, and (3) supplying the oxygen
to the biochemical reactions necessary for the stabilization of the wastewater. The theoretical oxygen requirement can be
computed by knowing the BOD of the waste, the amount of organisms wasted from the system per day and the degree of treatment
(whether a nitrified effluent is required). For practical purposes, enough air should be added to the waste to maintain at
least two mg/L of dissolved oxygen under all conditions of loading in all parts of the aeration tank. The air requirements
for good treatment can be satisfied either by a diffused air system or by mechanical aerators. In the diffused air system,
air under low pressure, generally not more than eight to ten pounds, is supplied by blowers and forced through various types
of porous material in plates or tubes installed near the bottom of the aeration tank. As the air is discharged into the
liquid phase it breaks up into fine bubbles thus increasing the surface area across which oxygen diffuses from air into the
wastewater. The plates or tubes are so located in the aeration tank that a rotary motion is imparted to the wastewater
mixture resulting in a considerable amount of air being absorbed from the atmosphere. Diffuser plates may be composed of
fused crystalline alumina or high-silica sand. They are set in containers usually made of reinforced concrete. Diffuser
tubes are made of similar material, or, more recently, of corrugated stainless steel pipe with multiple outlets and wrapped
with saran twisted cord. These are suspended in the aeration tank in sections and can be disconnected above the wastewater
surface and removed for cleaning or renewal. When installed on swing joint connections so that they may be brought to the
surface of the tank, they are known as "Swing Diffusers". To prevent clogging of the diffuser plates or tubes, the air
supplied to them should be filtered to remove dust, oil or other impurities, and the piping should be of non-corrosive
material. There are a number of types of filters available based on different principles which may be used alone or in
combination.
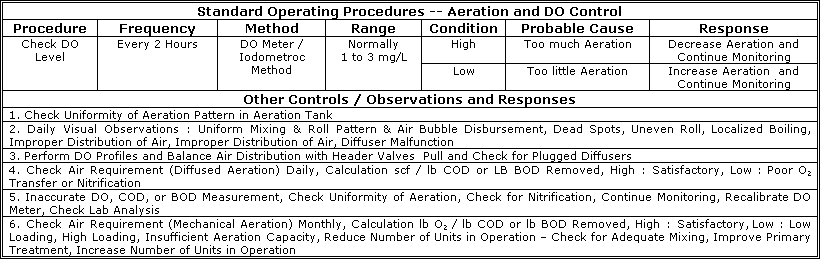
Mechanical aerators are of two general types -- surface and turbine. Surface aerators consists of submerged or partially
submerged impellers, which are centrally mounted in the aeration tank and which agitate the wastewater vigorously,
entraining air in the wastewater and causing a rapid change of the air-water interface to facilitate solution of the air.
Another type of surface aerator, more popular in Europe, consists of a paddle wheel or brush, partly submerged in the
wastewater, revolving on a horizontal axis. Air is absorbed by surface contact and by droplets thrown through the air by
the paddle mechanism. Turbine aerators are usually upflow types that rely on violent agitation of the surface and air
entrainment for their efficiency. A draft tube may be utilized to control the flow pattern of the circulating liquid within
the aeration tank. The draft tube is a cylinder with flared ends mounted concentrically with the impeller, and extending
from just above the floor of the aeration tank to just beneath the impeller. Surface aerators are rated in terms of their
oxygen-transfer rate or pounds of oxygen per horsepower-hour (hp-hr) at standard conditions. Surface aerators normally have
an efficiency from 2 to 4 lb. O 2 / hp-hr while turbine aerators vary from 2 to 3 lb. O 2 / hp-hr.
In the activated sludge process, the sludge accomplishes the major part of the removal of BOD from the wastewater being
treated in a relatively short period of aeration. It takes, however, a much longer time for the sludge to assimilate the
organic matter which it has absorbed. During this time an aerobic environment must be maintained. To effect the most
complete treatment of wastewater and the most economical operation in the conventional activated sludge process, an
aeration detention time of six to eight hours has been found to be adequate for diffused air aeration and nine to twelve
hours for mechanical aeration. Substantially shorter periods are used in some of the modifications of the conventional
process. These shorter aeration periods generally result in a lowering of the quality of the plant effluents.
Separation of Activated Sludge from the Mixed Liquor : The function of the secondary clarifier is to separate the
activated sludge solids from the mixed liquor. These solids represent the colloidal and dissolved solids that were
originally present in the wastewater. In the aeration unit they were incorporated into the activated sludge floc, which are
settleable solids. The separation of these solids, a critical step in the activated sludge process, is accomplished in the
secondary or final settling tanks. These tanks are similar in design to the mechanically cleaned primary sedimentation tanks
but with a surface settling rate not to exceed 800 gallons per square foot per day. The cycle of sludge removal from the
secondary tanks is much more important than with primary tanks. Some sludge is being removed continuously to be used as
returned sludge in the aeration tanks. The excess sludge must be removed before it loses its activity because of the death
of the aerobic organisms resulting from lack of oxygen at the bottom of the tank. Anaerobic sludges in the final clarifier
can cause "rising sludge". This should not be confused with a bulking sludge. Rising sludges are a result of denitrification
and septicity. It is possible, where facilities are available, to reactivate return sludge in separate reaeration tanks
before addition to the wastewater. However, it is much wiser to retain the activity of the sludge by prompt withdrawal from
the tank.
Return Sludge Requirements : The purpose of return sludge is to maintain a concentration of activated sludge in the
aeration tank sufficient for the desired degree of treatment. Ample return sludge pump capacity should be provided since the
return sludge volume may range from 10 to 50 percent of the volume of wastewater being treated and sometimes more. For a
conventional plant, the percentage is usually between 20 and 30 percent. The best concentration must be determined for each
plant by trial operation and should be carefully maintained by controlling the proportion of return sludge. The maximum
concentrations is limited by the air supply and wastewater load. If solids area allowed to build up, the air and food
requirements will exceed those available and an upset will occur.
Sludge Wasting from Activated Sludge : Excess activated sludge should be wasted as required to maintain the desired
solids concentration in the aeration tank. This can be done by either withdrawing mixed liquor directly from the aeration
tank or to waste from the sludge return line. The wasted mixed liquor can then be discharged to a thickening tank or to the
primary tanks where the sludge settles and mixes with the raw primary sludge. The waste sludge, usually from the sludge
return line, is further thickened by final sedimentation, centrifuging, or flotation thickening and then treated by
biological or chemical means. The above steps are essential in the operation of an activated sludge process. Nevertheless,
the operator of a plant should have a large degree of freedom or flexibility to modify the operation of an activated sludge
plant to achieve the required treatment. The modifications are expressed in terms of the level of solids in the aeration
tank, concentration of the solids, method of wastewater introduction into the aeration tank, and in terms of aeration time.
Aerated Lagoons & Stabilization Ponds...
Aerated Lagoons...
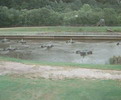
Aerated lagoons are relatively shallow lagoons in which wastewater is added at a single point either at the edge or middle
of the lagoon and the effluent is removed from another point. The retention time is a function of the percent removal of
BOD. The retention time may vary from 6 to 18 days as the removal of BOD from domestic wastewater varies from 75 to 90
percent. Oxygen is supplied by means of surface aerators or by diffused aeration units. The action of the aerators also
maintains the solids of the lagoon in suspension. Depending on the degree of mixing, lagoons may be operated as either
aerobic or as aerobic-anaerobic systems. In aerobic lagoons all biological solids are in continual suspension and
stabilization of the organics occurs under aerobic conditions. In the case of the aerobic-anaerobic lagoon a large portion
of the solids settles to the bottom of the lagoon. As the solids build up, a portion will undergo anaerobic decomposition.
Therefore, stabilization in this case occurs partly under aerobic conditions and partly under anaerobic conditions.
Stabilization Ponds...
A stabilization pond or "oxidation pond" as it is often called, is usually a shallow earthen basin of controlled shape,
which is designed for treating wastewaters from small communities or industrial plants. The ponds are usually 2 to 4 feet
deep, although much deeper ponds have been used quite successfully. Stabilization ponds have been applied singly as part of
a treatment scheme or as the sole process, providing complete treatment. The process involves two major steps in the
decomposition of organic matter in wastewater. The carbonaceous matter is first oxidized by the aerobic microorganisms with
the formation of carbon dioxide and the inorganic forms of nitrogen and phosphorous. These inorganic forms are then used by
algae in their photosynthetic reactions. Photosynthesis is a natural process carried on by green plants in the presence of
light. One of the end products of photosynthesis is oxygen which becomes available to the aerobic microorganisms. As a
result of the reactions in the ponds, the organics in wastewater are partly oxidized and partly converted to algae cells.
Algae has been harvested in some of the locations and used for animal feed as a protein source. Therefore, treatment of
wastewater with the production of a useful by-product is possible in stabilization ponds. Most stabilization ponds are
designed for loadings of one acre per 400 persons, 50 pounds of BOD per acre per day or 15 pounds of BOD per acre foot per
day with detention periods generally greater than 30 days. The natural soil in which they are located should be fairly
impervious so that seepage will not materially affect the surface level of the wastewater in the pond. These ponds are low
cost in construction and require a minimum of operation. The requirement that large, fairly isolated areas be provided
limits their use to relatively small populations in areas where land is available.

Pond Performance...
The treatment efficiencies that can be expected by ponds vary more than most other treatment devices. Some of the many
variables are :
Physical Factors : ( a ) Type of soil, ( b ) Surface area, ( c ) Depth, ( d ) Wind action, ( e ) Sunlight, ( f )
Temperature, ( g ) Short circuiting and ( h ) Inflow variations.
Chemical Factors : ( a ) Organic material, ( b ) pH, ( c ) Solids and ( d ) Concentration and nature of
waste.
Biological Factors : ( a ) Type of bacteria, ( b ) Type and quantity of algae, ( c ) Activity of organisms, ( d )
Nutrient deficiencies and ( e ) Toxic concentrations.

Operation and Maintenance...
Most problems that arise from ponds area result of the operator's neglect and poor housekeeping practices. Some operation
and maintenance problems associated with ponds are :
Scum Control : Scum is a common characteristic usually present in the spring when the water warms and the biological
activity resumes. Scum can promote a blue-green algae growth which can give rise to disagreeable odors. If scum is allowed
to accumulate, it can cut off the sunlight from the pond which would affect the dissolved oxygen produced from
photosynthesis.
Odor Control : Odors are usually associated with overloading and poor housekeeping. Most odors usually occur during
the spring warm-up when biological activity resumes. Reduction of odors can be accomplished by the use of surface aerators
and the addition of chlorine. In some cases, sodium nitrate has been used as a supplemental source of oxygen.
Weed Control : Weeds are mostly objectionable because they can promote mosquito breeding and scum accumulation.
Aquatic weed roots may puncture pond linings and hinder pond circulation.
Insect Control : Mosquitoes will breed in sheltered areas of standing water, where there is vegetation or scum to
which female mosquitoes can attach their eggs. Mosquitoes are a nuisance to plant personnel and nearby residential areas
and may pose public health problems. There are also many minute, shrimp-like predators which feed on algae, usually during
the warmer months, and may clear the pond of algae, reducing the dissolved oxygen content in the pond and producing noxious
odors. This condition is normally temporary. Effective insect control is usually accomplished by good housekeeping practices
and the use of insecticides.
Intermittent Sand Filters...
The intermittent sand filter is a specially prepared bed of sand on which effluents from primary treatment or from
trickling filters or secondary settling tanks may be applied intermittently by using troughs or perforated pipe
distributors. The effluent from the filter is removed by an underdrainage system.
Bed Construction...
The filter bed should have a depth of clean sand of at least 24 inches overlying clean, graded gravel. The gravel should
be placed in at least three layers around the underdrains and to a depth of at least six inches over the top of the
underdrains. The sand itself should have an effective size of 0.3 to 0.6 millimeters and have a uniformity coefficient of
not more than 3.5. The center to center spacing of underdrains should not be more than 10 feet. Capacity. When treating a
primary effluent from normal sewage, the rate of application on the filter should not exceed 125,000 gallons per acre per
day, which should be reduced if the sewage is strong. With trickling filter and secondary settling tank effluent, the
loading should not exceed 500,000 gallons per acre per day. The intermittent sand filter is a true filter which strains out
and retains fine suspended solids and also acts an an oxidizing unit. The major portion of the straining and oxidation is
effected at or near the surface of the sand. Straining results from the fine nature of the sand medium with small voids and
from a biological slime growth of organisms which develops on the surface of the sand. Oxidation is effected, as in all
secondary treatment devices, by the living aerobic microorganisms which develop primarily at the surface, forming a slime
layer, but also extending into the sand medium.
Operation...
It is important that the filter be allowed to empty itself and obtain a fresh air supply at intervals. This is accomplished
by intermittent dosing of the sewage onto the filter. Sewage is applied from two to six times a day in quantities sufficient
to cover the surface down through the sand, air is drawn in from the surface. Sand filters are constructed in two or more
units which are used in rotation. Eventually the slime layer on the surface causes the top layer of sand to become clogged
and necessitates the removal of the top layer of sand in order to put the unit back into efficient operation. Pooling should
not be allowed to develop on the beds as this tends to produce septic action, obnoxious odors and an effluent of poor
quality. Pooling indicates that cleaning is necessary. The surface of the beds should be kept level to afford uniform
distribution of the sewage and weeds, grass, etc., should not be allowed to grow on the beds. For winter use, the open air
beds in the northern part of the State should be ridged every two feet in order to hold the ice off the main body of sand.
An alternate method is that of raking up small four to six inch piles of the top surface every three feet over the surface
of the bed. The bed should be cleaned and leveled as early as possible in the spring. Where natural sand percolation beds
are used it is sometimes advisable to shallow harrow the beds after careful removal of all organic deposits. Such harrowing
is not advisable with underdrained beds because of possible damage to the underdrainage system.
Efficiency and Use...
A well operated intermittent sand filter will give a clear, sparkling stable effluent almost completely oxidized and
nitrified. Over-all plant removals of 95 percent or more of the BOD and suspended solids in the raw sewage can be expected.
This exceeds other accepted secondary treatment processes. When compared with other sewage treatment processes, large areas
of land are needed, construction costs per unit of sewage treated are high and maintenance in keeping the filters clean is
considerable. The use of filters of this type is restricted to situations where the volume of sewage to be treated is small,
or where an exceptionally high grade of plant effluent is necessary. They have been used effectively for the additional
treatment of secondary treatment effluents. Modification of the sand filters have been proposed in the past but, in general,
have not proven practical for treatment of large volumes of sewage.