Short - Term Control...
When a serious bulking incident occurs the first priority is to protect final water quality. Optimising clarification
performance both operationally and by the addition of coagulants can help in less severe cases. The most universally
applicable quick fix is to dose a toxicant into the return sludge. The selectivity of this treatment relies on the greater
susceptibility of the filamentous bacteria to certain biocidal chemicals. This is probably due to the filament's larger
surface area over which the chemical can act. Various forms of chlorine have been extensively used for this purpose and
when used correctly can rapidly restore sludge settleability. It is important that the correct strategy for dosing is
adopted or the treatment will have little or no effect. Dosing must be continuous, tightly controlled and into an area
of excellent mixing. The dose should start low and progressively increase until the desired improvement is achieved. Where
environmental concerns preclude the use of chlorine, hydrogen peroxide, ozone or some biocides can be used as an
alternative. It is recommended that expert advice is sought before attempting this type of treatment for the first time.
Reseeding with healthy activated sludge or bioaugmentation with freeze dried bacteria may be helpful after treatment.
Long - Term Control...
Chlorination can be helpful over the short term but it should not be seen as a long term solution to the problem. Long term
control can only come from identifying and eliminating the cause. Extensive monitoring of the plant allows the correlation
of bulking incidents with plant operating conditions which can yield valuable information about the cause. Measurement of
settlement in a stirred cylinder so that the stirred sludge volume index (SSVI) can be calculated and microscopic
examination of the sludge should be routinely carried out on all activated sludge plants. The first signs of bulking can
be detected before plant operation is effected so that control measures can be taken early and the severity of the bulking
minimised.
It has been clearly demonstrated that filamentous bulking is more prevalent in completely mixed activated sludge systems.
The high concentration gradient of available BOD along a plug flow system creates a considerable selection pressure in
favour of beneficial floc forming bacteria. It is the initial contact of the return sludge and the incoming feed that is
important so this effect will also occur when a selector tank precedes the main aeration tank allowing the return sludge
and feed to mix for about thirty minutes first. Selectors are now usually designed into new installations and can be retro
fitted to older plants.Another common cause of bulking is low dissolved oxygen. The minimum level of dissolved oxygen
required to prevent bulking depends on the nature of the feed to the plant and the growth rate of the biomass. Although
the average dissolved oxygen level in a plant may appear to be sufficient to avoid bulking, the sludge may cycle through
short or longer periods of low oxygen by, for example, overshooting set points on aeration control equipment, periodic
high loads to the plant, dead spots in the aeration tank and extended periods in the unaerated clarifier.
Where the bulking is caused by a deficiency of nutrients or micronutrients the activated sludge plant will respond
quickly to correction of the deficiency by the addition of nitrogen and phosphorus or trace elements. If nutrients are
not limiting, adding nutrients will have no beneficial effect and may contribute to the polluting load of the effluent.
The nutrient status of the plant can be determined by testing the feed to and effluent from the plant. Specifically
formulated nutrient and micronutrient solutions are available to correct any deficiency found.When faced with a bulking
incident it is important not to panic and try to make too many changes to the plant at once. First concentrate on getting
settlement under control to give time to review plant operation, examine historical monitoring data and if necessary
take expert advice. Any alterations should then be brought in one at a time, if possible, so that the plant is not upset
by sudden changes. It will also then be clear what alterations are effective. Monitoring data is a very valuable tool and
it should be viewed and graphed not just filed away. There are no magic cures for bulking but with good data, planning and
firm control in most cases the worst effects can be avoided.
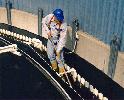
The Influence of Nutrient Levels (COD : N : P) on Floc Formation in the Activated Sludge Processes...
Activated sludge is the most widely used biological process for treating
wastewater derived from municipal and industrial sources. Moreover, microbial
floc physicochemical properties influence both the mass transport and the
effectiveness of separation of activated sludge biomass from the treated
wastewater. Nutrients are one of the important parameters affecting flocculation.
The understanding of nutritional requirements and its effect on microbial
flocculation have important implications for the operation and performance
of activated sludge systems. Past research on nutrient effects in activated
sludge processes has focused mostly on the growth of filamentous microorganisms
and bulking. Little attention has been paid to the floc structure and floc
physicochemical characteristics under the effects of nutrients, which are
the basic and underlying factors ultimately affecting the control and overall
treatment efficiency of activated sludge processes. Moreover, the study
of floc structure has largely been devoted to the gross scale (> 1 mm),
and the impact of sample handling and manipulation on floc structure and
its properties have not been addressed.
We have begun to investigate the influence of macronutrient ratio variation
on floc architecture (structure and physicochemical characteristics) by
a combination of wastewater analysis and microscopic examination of activated
sludge flocs while achieving minimal perturbation. The influence of nutrient
levels (COD:N:P) on floc properties is being studied using a laboratory
sequencing batch reactor (SBR) system fed a glucose based synthetic
waste. The use of a SBR system permits control of the floc thus having
utlity in studying the effect of various parameters on floc properties
and structure. Floc analysis involves a minimal perturbation approach and
correlative microscopy. Floc size distribution is measured. Floc density
and porosity are calculated from the measured settling velocity.
Preliminary results from experiments employing SBRs fed a synthetic
feed varying in COD:N:P ratio (100:5:1, 100:10:1, 100:5:2, 200:5:1) showed
that the COD:N:P ratio has no significant effect on COD removal. COD removal
(up to 90%) was achieved in less than two hours. No significant changes
in foc size distribution were observed under different COD:N:P (100:5:1,
100:10:1, 100:5:2, 200:5:1) conditions. Floc settling velocity was described
by power law equations and the power coefficients were similar to those
reported in the literature. There was no significant effect on settling
velocity when the COD:N:P ratio is shifted from 100:5:1 to 100:5:2 or 200:5:1.
A decrease in C/N ratio appeared to have an effect on floc settling. The
floc density was lower at COD:N:P ratio of 100:5:2 when compared to flocs
from the control conditions of 100:5:1. These results are being correlated
to structural information obtained from conventional optical microscopy
scanning confocal laser microscopy, and transmission
electron microscopy.
Sludge Volume Index (SVI)...
The sludge volume index of activated sludge is defined as the volume in milliliters occupied by one gram of activated
sludge after settling for 30 minutes. From this definition it may be observed that the lower the SVI, the better is the
settling quality of the aerated mixed liquor. Also, high SVI values (greater than 100) indicate poor settling
qualities and possible bulking problems in the secondary clarifier. Sludge with an SVI of less than 100 is
considered a good settling sludge. Ideally you are looking for a value that ranges from 50 to 75 for most
conventional activated sludge plants. You should be aware of the fact that SVI or SDI are classical measurements of sludge
quality, but may or may not always reflect the true sludge conditions and must be compared with other process parameters,
such as sludge units.
Equipment Needed...
Equipment needed to obtain a 30-minute settling of the mixed liquor sludge in terms of mL/L is Imhoff Cone.
"Imhoff cone"...
Equipments needed to obtain the MLSS value of the mixed liquor sludge in terms of mg/L are shown below.
"Other Equipments"...
Procedure...
- Obtain the 30-minute settleability of the mixed liquor sludge. The
value should be in terms of ml/L
- Obtain the MLSS on the mixed liquor sludge. The value should be in
terms of mg/L
- Perform the mathematical division of the MLSS value into the settlable
solids
If the MLSS value is not to , then you must use the to obtain a SVI value.
Calculations...
"SVI Calculation"...
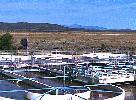
Sludge Density Index (SDI)...
The sludge density index is also a method of measuring the settling quality of activated sludge, yet it, like the SVI
parameter, may or may not provide a true picture of the quality of the sludge in question unless compared with
other relevant process parameters. It differs from SVI in that the higher the SDI value, the better the settling quality
of the aerated mixed liquor. Similarly, the lower the SDI, the poorer the settling quality of the mixed liquor. SDI is
the concentration in percent solids that the activated sludge will assume after settling for 30 minutes. SDI will range
from 2.00 to 1.33, and sludges with values of one or more are generally considered to have good settling
characteristics.
Equipment Needed...
Same as SVI. See pictures shown above.
Procedure...
Same as SVI. Read explanations given above.
If the MLSS value is not to , then you must use the to obtain a SDI value.
Calculations...
"SDI Calculation"...