
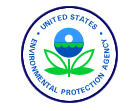
Sequencing Batch Reactor Systems...
Description...
The sequencing batch reactor (SBR) process is a sequential suspended growth (activated sludge) process in which all major steps occur in the same tank in sequential order (Figure 1). There are two major classifications of SBRs: the intermittent flow (IF) or "true batch reactor," which employs all the steps in figure 1, and the continuous flow (CF) system, which does not follow these steps. Both have been used successfully at a variety of U.S. and worldwide installations. SBRs can be designed and operated to enhance removal of nitrogen, phosphorus, and ammonia, in addition to removing TSS and BOD. The intermittent flow SBR accepts influent only at specified intervals and, in general, follows the five-step sequence. There
are usually two IF units in parallel. Because this system is closed to influent flow during the treatment cycle, two units may be operated in parallel, with one unit open for intake while the other runs through the remainder of the cycles. In the continuous inflow SBR, influent flows continuously during all phases of the treatment cycle. To reduce short-circuiting, a partition is normally added to the tank to separate the turbulent aeration zone from the quiescent area.
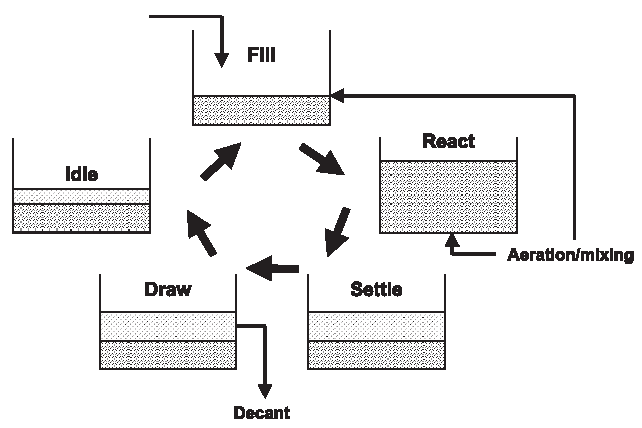
Figure 1. Sequencing batch reactor (SBR) design principle.
The SBR system is typically found in packaged configurations for onsite and small community or cluster applications. The major components of the package include the batch tank, aerator, mixer, decanter device, process control system (including timers), pumps, piping, and appurtenances. Aeration may be provided by diffused air or mechanical devices. SBRs are often sized to provide mixing as well and are operated by the process control timers. Mechanical aerators have the added value
of potential operation as mixers or aerators. The decanter is a critical element in the process. Several decanter configurations are available, including fixed and floating units. At least one commercial package employs a thermal processing step for the excess sludge produced and wasted during the "idle" step. The key to the SBR process is the
control system, which consists of a combination of level sensors, timers, and microprocessors. Programmable logic
controllers can be configured to suit the owner's needs. This provides a precise and versatile means of control.
Typical Applications...
SBR package plants have found application as onsite systems in some states and counties where they are allowed by code.
They are normally used to achieve a higher degree of treatment than a continuous-flow, suspended-growth aerobic system (CFSGAS) unit by eliminating impacts caused by influent flow fluctuations. For discharge to surface waters, they must meet effluent permit limits on BOD, TSS, and possibly ammonia. Additional disinfection is required to meet effluent fecal
coliform requirements. For subsurface discharge, they can be used in situations where infiltrative surface organic loadings must be reduced. There are data showing that a higher quality effluent may reduce soil absorption field area requirements. The process may be used to achieve nitrification as well as nitrogen and phosphorus removal prior to surface and subsurface discharge.
Design Assumptions...
Typical IF system design information is provided in Table 1. With CF-type SBRs, a typical cycle time is 3 to 4 hours, with
50 percent of that cycle devoted to aeration (step 2), 25 percent to settling (step 3), and 25 percent to decant (step 4). With both types, downstream or subsequent unit processes (e.g., disinfection) must be designed for greater capacity
(because the effluent flow is several times the influent flow during the decant period) or an equalization tank must be
used to permit a consistent flow to those processes.
Onsite package units should be constructed of noncorrosive materials, such as coated concrete, plastic, fiberglass, or
coated steel. Some units are installed aboveground on a concrete slab with proper housing to protect against local climatic concerns. The units can also be buried underground as long as easy access is provided to all mechanical parts, electrical control systems, and water surfaces. All electric components should meet NEC code and should be waterproofed and/or
sheltered from the elements. If airlift pumps are used, large-diameter pipes should be provided to avoid clogging. Blowers, pumps, and other mechanical devices should be designed for continuous heavy-duty use. Easy access to all moving parts must
be provided for routine maintenance. An effective alarm system should be installed to alert homeowners or management
entities of malfunctions.
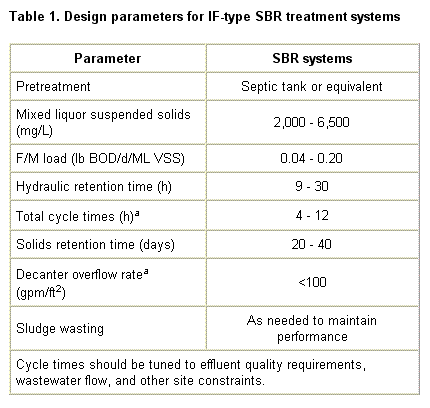
Performance...
With appropriate design and operation, SBR plants have been reported to produce high quality BOD and TSS effluents. Typical ranges of CBOD5 (carbonaceous 5-day BOD) are from 5 to 15 mg/L. TSS ranges from 10 to 30 mg/L in well-operated systems. FC removal of 1 to 2 logs can be expected. Normally, nitrification can be attained most of the time unless cold temperatures persist. The SBR systems produce a more reliable effluent quality than CFSGAS or FFS owing to the random nature of the wastewater generated from an individual home. The CF/SBR is also capable of meeting secondary effluent standards (30 mg/L
of CBOD and TSS), but more subject to upset by randomly generated wastewaters than the IF/SBR (Ayers Associates, 1998) if short-circuiting cannot be minimized.
Management Needs...
Long-term management (including operation and maintenance) of SBRs through homeowner service contracts or local management programs is an important component of the operation and maintenance program. Homeowners do not typically possess the skills needed or the desire to learn to perform proper operation and maintenance. In addition, homeowner neglect, ignorance, or interference (e.g., disabling alarm systems) has contributed to operational malfunctions. No wasting of biomass should be practiced until a satisfactory concentration has developed. Intensive surveillance by qualified personnel is desirable
during the first months of startup.
Most operating parameters in SBR package systems can be controlled by the operator. Time clock controls may be used to regulate cycle times for each cycle, adjusted for and depending on observed performance. Alarm systems that warn of
aerator system failure and/or pump failure are essential.
Inspections are recommended three to four times per year; septage pumping (solids wasting) is dependent upon inspection results. Routine maintenance requirements for onsite SBRs are given below. Operation and maintenance requires semiskilled personnel. Based on field experience, 5 to 12 person-hours per year, plus analytical services, are required. The process produces 0.6 to 0.9 lb TSS/lb BOD removed and requires between 3.0 and 10 kWh/day for operation. Operating personnel prefer these systems to CFSGAS for their simplicity of O/M tasks. The key operational components are the programmer and the decanter, and these must be maintained in proper working order. The primary O/M tasks are provided in Table 2.
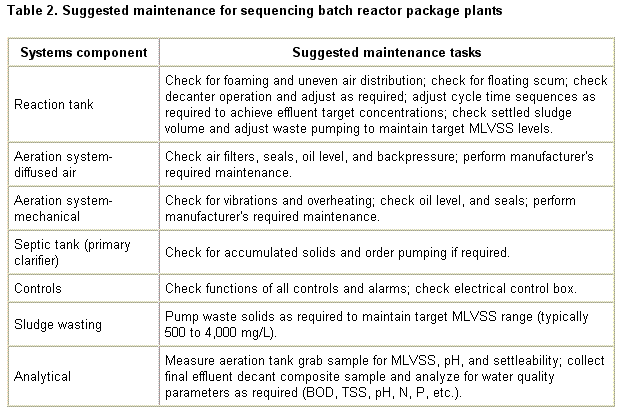
Risk Management Issues...
With proper management, a package SBR system is reliable and should pose no unacceptable risks to the homeowner or the environment. If neglected, however, the process can result in environmental damage through production of poor quality effluent that may pose public health risks and can result in the premature failure of subsurface systems. Odor and noise
may also create some level of nuisance. SBRs are less susceptible to flow and quality loading changes than other aerobic biological systems, but they are still not suitable for seasonal applications. They are similarly susceptible to extreme
cold and should be buried and/or insulated in areas subjected to these extremes. Local authorities can provide guidance on climatic effects on equipment and how to prevent them. The controller should be located in a heated environment. Long power outages can result in odors and effluent degradation, as is the case with other aerobic biological systems.
Costs...
For residential applications, typical system equipment costs are $7,000 to $9,000. Installation costs vary depending on site conditions; installation costs between $1,500 and $3,000 are typical for uncomplicated sites with good access. It should be noted that additional system components (e.g., subsurface infiltration system) will result in additional costs. Annual operation and maintenance costs include electricity use (<$300/year), sludge removal (>$100/year), and equipment servicing. (Some companies are providing annual service contracts for these units for $250 to $400.) Actual costs will vary depending
on the location of the unit and local conditions.