Mechanical and Electrical Design of Pumping Stations - 08...
Chapter - 08 : Engines and Gears...
8-1. General...
Internal combustion engines used for pump drivers are of
the diesel or gas-fueled type. Engine drives offer the
advantage of variable speed, which may be a benefit
when compared with other types of pump drives that
operate at essentially constant speed. Selection criteria
for internal combustion engines and electric motors are
provided in Chapter 10.
8-2. Engines...
Engines of the two- or four-cycle type are used for pump
drives. Natural gas engines are preferred where a
dependable natural gas supply is available; otherwise,
diesel-operated engines should be used. Skid-mounted
engines should be used when possible with all the auxiliaries
except fuel tank, mounted thereon. Engines for
flood control pumping service should be rated in accordance
with the Diesel Engine Manufacturer Association.
All rating should be based on continuous duty operation.
The engine should be rated 10 percent in excess of the
maximum operating requirements that would include the
maximum pump horsepower requirement and losses
through the drive system. The engine should also be
capable of operation at 110-percent full-load rating at
rated speed with safe operating temperatures for periods
of 2 hours in 24 hours. Engine speed should be as indicated
in the table below.
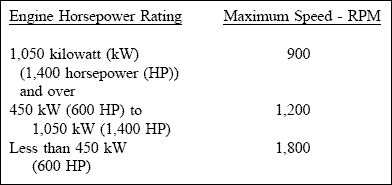
( a ) Cooling systems.
Two basic types of cooling
systems are radiator and heat exchanger. Selection criteria
include engine size, space availability, raw or sump
water supply, initial cost, operation and maintenance cost,
and environmental concerns. A radiator system may
have the radiator mounted on the engine base or remotely
mounted. The radiator will always be located where an
adequate supply of cooling air is available. For larger
engines, the physical size of the radiator may make it an impractical choice. The selection of the fan and radiator
location would include the noise level, heat produced,
and size requirements. The heat exchanger cooling
system will be the closed type. It can be an elaborate
system with raw or canal water supply pumps, a shell
and tube heat exchanger, and a traveling water screen
(screen the raw water to the supply pumps) to cool the
engine’s jacket water. It could also be a simplified submerged
pipe type. This type circulates engine jacket
water through pipes submerged in the pump sump.
Selection will be based on engine cooling requirements
and the recommendation of the engine manufacturer.
Some problems associated with heat exchanger cooling
are freezing climates, foul cooling water, rejecting heated
raw water to the canal, and engine testing restrictions
when the sump or entering ditch is dry.
( b ) Control equipment.
All engines will be designed
for manual starting. Manual and automatic control
devices should be of the types regularly furnished by the
engine manufacturer for similar service. Automatic
engine shutdown is required for engine overspeed.
Visual and audible alarms and automatic engine shutdown
(as a minimum) should occur for high jacket water
temperature, high lubricating oil temperature, low lubricating
oil pressure, gear reducer high lubricating oil
temperature, or gear reducer low lubricating oil pressure.
The type of speed control devices will depend upon the
desired scheme of operation, but a governor to maintain
speed and a suitable speed indicator should be provided
in all cases. Consideration can be given to an engine
shutoff method for low sump water elevation. Engine
controls are generally located adjacent to the engine.
Redundant remote read-out of critical engine, pump, and
gear parameters may be located in an operating office for
large pumping stations. The control system should be
designed so that the engines can be started and operated
when the electric power to the station is interrupted and
automatic engine shutdown should not occur due to
minor fluctuations in commercial power. A control system
for engines less than 300 kW (400 HP) rating can be
equipped with a rechargeable battery system for its operation.
Larger sized engines will require a separate
engine-generator to provide electrical power for the control
system. The controls should permit operation of the
engine’s jacket water pump to allow cool down of the
engine if required by the engine manufacturer. If the
jacket water pump is engine driven, then an auxiliary
motor driven jacket water pump should be considered for
cool down, if required. A means needs to be furnished
to manually shutoff the intake air supply to the engine to
provide for critical shutdown. Crankcase explosion relief
valves should be provided for diesel engines.
( c ) Engine equipment and auxiliaries.
(1) Clutches. Engines less than 450 kW (600 HP)
may be equipped with a manual clutch mechanism,
which allows the engine to be started and operated without
running the pump. This permits testing of the engine
without regard to water levels that may not allow pump
operation.
(2) Flexible drive shafts. Flexible drive shafts eliminate
the need for critical alignment of the engine to the
gear reducer. The drive shaft consists of a center section
with a flexible joint on each end. One of the flexible
joints incorporates a splined slip joint that permits
longitudinal movement to occur. The drive shaft manufacturer’s
published rating at the maximum engine speed
should be at least 1-½ times the maximum torque of the
pump that usually occurs at its maximum head condition.
A drive shaft minimum length of 900 millimeters
(36 inches) is desirable to allow for intentional or accidental
misalignment. A vertical difference of approximately
15 millimeters (0.5 inch) (for 900 millimeters
(36-inch) shaft length) should be provided between the
engine output shaft and the gear input shaft to provide
continuous exercise for the flexible joints. There are
other types of engine-to-gear connections, such as direct
through flexible couplings. This can be investigated if
site conditions prevent the use of the drive shaft
described above.
(3) Starting system. The engine starting system
should be pneumatic except for small engines. The air
system should contain a reservoir of sufficient size to
permit two starts of each unit without recharge by the air
compressor. The time for the air compressor to recharge
the reservoir should not exceed 2 hours. Two air compressors
should be provided for reliability. Unless a
standby generating unit is provided for the station, one of
the air compressors should be engine driven so that the
air pressure can be built up during electric power
outages.
(4) Prelubrication. Engine manufacturer’s should be
consulted as to any requirements for a prelubrication
pump. Factors that are normally used to determine the
need for prelubrication requirements are engine size and
the expected period of time between operations.
8-3. Fuel Supply System...
( a ) Fuel oil.
The type of fuel oil used should be
recommended by the engine manufacturer for the type of
environment the engine will operate in. An adequate supply of fuel oil is required to ensure station operation
without the need for emergency replenishment. The
volume of the storage tank system should provide for a
minimum of 2 days of continuous operation of all units
operating at maximum horsepower. The volume provided
may be increased for those stations that are remote
or of such a size that quantities required would not permit
ready replenishment. The location and type of fuel
storage should be determined after review of the applicable
local, state, and national Environmental Protection
Agency (EPA) regulations.
( b ) Natural gas.
Stations equipped with engines
operating on natural gas supplied from a utility system
need to be provided with a stored gas backup system if
reliability of the source could cause the station to be out
of operation for more than 24 hours. The volume of the
gas storage system should provide for a minimum of
2 days of continuous operation of all units operating at
maximum load. The storage usually consists of one or
more pressure tanks above ground. All gas tanks should
be installed with foundations attached to the tanks, which
preclude floating of the tank in case of flooding. A
station with natural gas-operated engines must be provided
with devices capable of measuring air content for
explosive conditions and indicating this condition with
alarms both inside and outside the station. The ventilating
system must be suitable for operating in an explosive
atmosphere and capable of being turned on from
outside the station. The sump should be ventilated in a
similar manner. All installations need to be designed and
installed in accordance with the National Fire Protection
Association (NFPA).
8-4. Gear Drives...
Most applications for pumping stations will use a vertical
pump with a right-angle gear to transmit power from the
horizontal engine shaft to the vertical pump shaft. Gear
drives may also be used with horizontal electric motors
driving vertical pumps. This permits the use of less
expensive high-speed horizontal drive electric motors.
Horizontal pump installations may use chain drive or
parallel shaft gear reducers. The gear units should have
a service factor of 1.25 when driven by an electric motor
and 1.5 when driven by an engine. The service factor
should be based on the maximum horsepower requirement
of the pump. Right-angle drives should be of the
hollow shaft type to permit vertical adjustment of the
pump propeller at the top of the gear. All right-angle
gear drives should be designed to carry the full vertical
thrust from the pump. The gear unit should be equipped
with an oil pump directly driven from one of the reducer shafts and be capable of delivering sufficient oil to all
parts when operating at less than rated speed. The transmission
of power through the gear produces significant
heating of the lubricating oil, and some means must be
provided to reject this heat. The heat removal can be
accomplished by placing an oil cooler in the engine’s
cooling water system or by using a separate oil radiator
placed in the air stream from the engine-driven fan or
located with its own fan. Engines that use heat
exchangers should also use a similar system for cooling
the reduction gearing. All gears should be equipped with
a thrust-bearing temperature thermometer, an oil pressure
gage and temperature thermometer, and oil level indicators.
Automatic shutdown of the pumping unit and
visual and audible alarms should be provided for high
thrust-bearing temperature, high oil temperature, or low
oil pressure. When cold weather operation is expected,
oil heaters should be used in the gear to reduce oil thickening
between operational periods. A backstop device
should be attached to the low or intermediate shaft of the
gear reducer to prevent reverse rotation of the pump and
engine.