Mechanical and Electrical Design of Pumping Stations - 10...
Chapter - 10 : Pump Drive Selection...
10-1. General...
Several options are available to the designer when considering
the selection of a pump drive for floodprotection
pumping stations. The two factors that must
be investigated when making this selection are reliability
and cost. Alternative studies should be made considering
these two factors. The two types of drives to be considered
are electric motors and internal combustion engines.
Gear drives are required as part of the drive system when
using engines. Gear drives can also be used with electric
motors permitting the use of a less expensive higher
speed motor and allowing a greater variation of the pump
speed than permitted with direct drive.
10-2. Reliability...
The primary consideration in the selection of any pump
drive is reliability under the worst conditions likely to
prevail during the time the station will be required to
operate. The reliability of the electrical power source
should be determined from power company records of
power outages in that area and their capability to repair
any outages. Consideration of power from two different
power grids within a company may be advisable for large
pumping stations. The reliability of the various different
types of equipment must also be studied. Electric motors
and engines are usually very reliable while the necessary
accessories to operate these units are less reliable. The
complexity to operate and repair the piece of equipment
by the operating personnel should also be considered.
Equipment repair requiring specialized service personnel
may require much greater time to put it back into service.
10-3. Cost Considerations...
( a ) General.
Unless reliability considerations are
important enough to decide what type of drive to use,
annual cost comparisons should be made of all systems
under study. The annual costs should include the
installed, operating, maintenance and replacement costs.
After all costs have been established, a life-cycle cost
analysis can be performed.
( b ) Installed costs.
The installed costs include the
construction costs of all the equipment and the electric
power supply costs, which usually would include the cost
of the substation plus the power line to the station. These costs should be figured on an annualized basis
using the number of years determined for the project life.
( c ) Operating costs.
The operating costs would
include the cost for energy and manpower expenses. To
accurately estimate the total energy costs, an estimate of
the amount of pumping required for each month of the
year must be obtained. The source of pumping time
should be obtained from hydrology period-of-record
routing studies. The current price schedule for electric
power from the supplying utility or the market price of
engine fuel can be used to determine the costs for all
stations except for large stations. For large stations, a
study of future energy costs over the life of the project is
justified. In determining the total cost of electricity, it is
important to include both the cost for the energy used
(kilowatt hours) plus any demand (capacity) charges.
Demand charges by some power companies may be a
major part of the energy costs.
( d ) Maintenance costs.
Maintenance costs include
manpower and materials for both preventative and major
repairs. Unless the station has specialized equipment,
these costs are usually estimated using the following
percentages of the installed equipment costs:
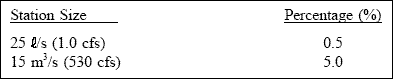
Percentages for intermediate station sizes are determined
proportionally with the above values. The maintenance
cost of unusual or specialized equipment would be determined
separately and would be an additional amount.
( e ) Rehabilitation and replacement costs.
Rehabilitation
and replacement costs include those costs required to
keep the station operable for the project life. For a normal
50-year station life, most of the equipment would be
rehabilitated or replaced at least once, except for very
large pumping stations. The periods between the rehabilitation/
replacement could be shorter if the operating time
were great. Major items such as pumps, drivers, and
switchgear are figured to be rehabilitated or replaced
once during the 50-year life. This major equipment
rehabilitation or replacement is usually estimated to occur
between 20 and 40 years after placing the station into
operation. Rehabilitation costs for major equipment can
be estimated to be 35 to 45 percent of replacement costs
depending on the condition of the equipment. Other
items of equipment may be replaced several times during
the project life depending on their use or may require only partial replacement. It is most likely that equipment,
except for the pump and motor, may not be
replaced in kind. Therefore, the replacement cost should
include all engineering and structural modification costs
as well as the equipment costs. In any event, the equipment
removal costs including the cost of all rental equipment
plus the installation cost of all new equipment
should be included.