Mechanical and Electrical Design of Pumping Stations - 11...
Chapter - 11 : Pump and Station Hydraulic Tests...
11-1. General...
Two types of tests are generally performed in connection
with a pumping station and its pumping equipment before
the station is built. Tests are run on pumps, either full
size or model, to determine their performance and to
demonstrate that the performance of the pump complies
with specification requirements. Physical hydraulic
model tests of the pumping station substructure may also
be conducted to assess its hydraulic performance.
11-2. Pump Tests...
( a ) General.
The pump performance tests are conducted
at the pump manufacturer’s facility. Field testing
to prove performance at the completed station is more
difficult and costly if not impossible in many cases. All
pumps should be factory tested to determine their capacity,
total head, efficiency, and horsepower requirements.
Pumps normally should also have a cavitation test performed.
This test is usually performed on a model.
Model testing specifications and parameters can be found
in Guide Specification CW 15160, Vertical Pumps, Axial
and Mixed Flow Impeller Type.
( b ) Description.
Factory pump tests are either performed
on full-size pumps or performed on a model
pump of the full-size pump. If a model pump is used, it
should be geometrically similar to that of the full-size
pump and of the same specific speed. Either type of test
is acceptable to check the ratings of the pump; however,
because of size limitations, most manufacturers limit fullsize
tests to pumps of less than 2 m3/s (75 cfs) capacity.
A pump test consists of determining the total head, efficiency,
and brake horsepower for a range of capacities.
All testing should be witnessed by the District office
design personnel performing the station design. The
dimensions of the model and prototype impellers should
be made by using drawings, measurements, and scaling
factors. The performance factors measured include
capacity, pressure head, horsepower, and suction pressure
when cavitation performance is to be determined.
( c ) Performance tests.
All pumps for flood-control
pumping stations should have their performance verified
by tests. For installation of identical pumps in a station,
only one of the pumps needs to be tested. Tests on
similar pumps used for another station will not be acceptable
as equivalent tests. The test setup should permit, and the specifications require, the pump to be tested over
a range of heads starting at least 600 millimeters (2 feet)
greater than the highest total head requirement or at shutoff
and extending down to the lowest head permitted by
the test setup. The test should, if an unstable range
("dog leg" in the head curve) exists. Sufficient test
points should be run to adequately define the unstable
range. This allows the pump manufacturer to demonstrate
that their pump does not operate in the unstable
range. The lowest head tested should be at least equal to
the total head that occurs for 95 percent of the operation
time during low head pumping conditions. For pumps
with capacities greater than 11 m3/s (400 cfs), the model
tests should be required to cover the complete head range
required by the specifications including down to the
lowest total head specified. All performance tests should
be run at the same head at which the pumps will operate
during actual duty. The readings of capacity and brake
horsepower along with the total head will be used to
determine the pump efficiency. For model tests, no
correction factor for efficiency due to size differences
will be allowed. Tests will be performed at water levels
similar to that which will occur during actual operating
conditions. An actual scale model of the station’s inlet
and discharge systems is not warranted except for pumps
over 14 m3/s (500 cfs). This requirement should also be
used when the sump is not designed by the Government
and is a part of the pump contract or has some complicated
flow passage which has not had a sump model test.
The pump test is used to ascertain the performance of the
pumps, not how it reacts in the prototype sump except in
the cases listed below. It is expected that the factory
sump would be free of vortexes and adverse flows so
that good results are obtained. Manufacturers are responsible
for furnishing a pump that conforms to the specifications
and meets the performance in the sump to be
provided by the Government. The pump manufacturer
should be held responsible for poor sump design, evidenced
by vortexing and bad flow conditions within the
sump, when the contract specifications require the sump
to be designed by the pump manufacturer. Except for
this special case, the pump manufacturer warrants performance
of the pumps only, not the sump, and the activity
within the sump would be the responsibility of the Government.
Duplicate model pump sumps should include
the sump from the inside of the trashrack. Any pump
using a formed suction intake should be tested with this
formed suction intake. Vertical pumps should be tested
only in the vertical position.
( d ) Cavitation tests.
Cavitation tests are performed to
indicate the operating conditions in which the pump will
start cavitating. For purposes of design, it is assumed that cavitation starts when the pump performance starts
to decrease as the effective sump level is reduced. The
inception of cavitation definition has not been agreed
upon by all the pump suppliers and users. A typical
pump test consists of operating the pump at a fixed
capacity while reducing the pressure on the suction side
of the pump. As the suction pressure is reduced, a point
is reached where a plot of the head-capacity curves deviates
from a straight line. The Corps specifies the start of
cavitation at a point where the curve starts to deviate
from the straight line. Others use as the start of cavitation,
a point where a 1- or 3-percent deviation in performance
from the straight line occurs. Submergence
requirements, as used in this manual, are based on the
Corps criterion of zero deviations from the straight line
portion. In most cases, some cavitation has already
started at either point; therefore, a design allowance of
extra submergence should be provided in addition to that
indicated by the tests results. The submergence allowance
is based on the estimated number of operating hours
expected annually. The amounts of allowance are indicated
in Appendix B. In all cases, the cavitation tests
should be performed in a test setup that uses a variation
of water levels on the suction side of the pump.
11-3. Station Tests...
( a ) General.
Hydraulic model tests of pumping station
sumps and discharge systems should be performed
by WES for stations with unique or unusual layouts.
The procedure in ER 1110-2-1403 should be followed
when requesting model tests. A decision should be made
on the requirement for model testing during the General
Design Memorandum stage so that the results of any
testing are available during the design of the station.
Test results are usually not available until 6 to 9 months
after forwarding a work order to the test agency.
( b ) Sump model tests.
The primary purpose for performing
a model test of a pumping station sump is to
develop a sump design that is free of adverse flow distribution
to the pump. Optimal flow into a pump impeller
should be uniform without any swirl and have a steady,
evenly distributed flow across the impeller entrance.
However, it is usually not possible to obtain the optimal
flow conditions without considerable added expense.
Acceptable pump operation will occur when a deviation
in the ratio of the average measured velocity to the average
computed velocity is 10 percent or less and when the
swirl angle is 3 degrees or less. Swirl in the pump
column is indicated by a vortimeter (free wheeling propeller
with zero pitch blade) located inside the column.
Swirl angle is defined as the arc tangent of the ratio of the blade speed at the tip of the vortimeter blade to the
average velocity for the cross section of the pump
column. There should not be any vortex formations
allowing entrance of air into the pump. In order to accurately
simulate the field conditions, the model should
include sufficient distance upstream of the station to a
location where changes in geometry will not affect flow
conditions in the sump. The prototype-to-model ratio is
usually determined by the testing agency, but it should
not be so large that adverse conditions cannot be readily
observed. Normally the model should be sized to ensure
that the Reynold’s number in the model pump column is
equal to or exceeds a value of 1 × 105. Reynold’s
number is defined by the following equation:
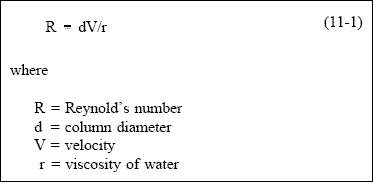
( c ) Discharge model tests.
(1) General. These tests are performed to evaluate
the performance of a discharge system. Usually two
types of systems are investigated, discharges which form
a siphon and/or through the protection discharges for
large stations where the friction head loss would be a
substantial portion of the total head of the pump.
(2) Siphon tests. The siphon tests are run to determine
that a siphon will prime the system in the required
time. This test is recommended when the down leg of
the siphon system is long or it contains irregular flow
lines and for pumps of 20 m3/s (750 cfs) or greater
having a siphon built into the station structure.
(3) Discharge tests. A head loss test should be
considered only for pump discharges with capacities of
20 m3/s (750 cfs) or greater and where the accuracy
deviation for estimating the total head exceeds 20 percent
of the total head. Other considerations would be the
sizing of the pump and its driver. In some cases, a
safety factor of 10 to 20 percent of the total head may
not change the pump unit selection, and therefore the
expense of a discharge test may not be warranted. For
those stations where the size of the driver is close to its
rating, a test may be in order to ensure that the driver
would not be overloaded due to error in head determination.
(4) Other tests. Additional tests may also be
required to fully prove the station acceptable. These
could include energy dissipation tests of a saxophone
outlet and a stilling basin or apron. Tests can also be
made on models of existing pumping station sumps
where operating difficulties have been experienced.