Mechanical and Electrical Design of Pumping Stations - 26...
Chapter - 26 : Appendix B - Pump Selection Method...
B-1. General...
( a ) Purpose.
This appendix provides a method to
determine the size of a pump to meet certain pumping
requirements. It also provides dimensions for the sump
and station layout once the pump is selected. Certain
information must be available before the pump selection
can be started. This information includes the pumping
requirements as determined from hydrology data, number
of pumping units, and discharge/station arrangement as
determined by EM 1110-2-3101.
( b ) Procedure.
This appendix is divided into two
major sections, selection of vertical wet pit pumps and
selection of vertical submersible propeller pumps
(Plates 23-25). Sample calculations are used to aid in
understanding the selection procedures. Chart B-1 indicates
the operating range of the various type pumps used in pumping stations. This chart indicates which pumps
should be investigated during the alternative study phase.
( c ) Selection process.
(1) Vertical wet pit pumps. The selection process
uses the model and affinity laws to obtain the performance
of a prototype pump from the various supplied
model pump performance data. Model performance data
can be obtained from pump manufacturers, existing
pumping stations, or from other Districts. The following
general steps are used in the selection process:
(a) Determine pump operating conditions using the furnished hydrology and station/discharge arrangement.
(b) Determine prototype pump performance from model performance.
(2) Submersible pumps. The selection process makes
use of typical catalog curves of head-capacity and Net
Positive Suction Head Required (NPSHR). The various curves allow direct selection of pumps after the
system design conditions are known.
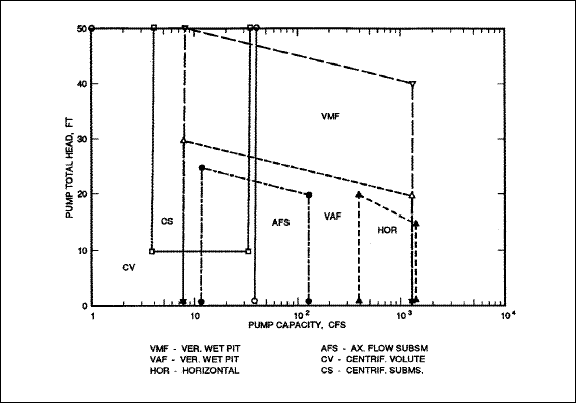
Chart B-1. Operating range of typical pumps.
( d ) Information sources.
The following is a list of information needed to perform the selection process and where it may be found :
- Number of Pumps : EM 1110-2-3102.
- Pump Discharge Configuration : EM 1110-2-3102.
- Hydrology Data : Project Hydrology Report.
( e ) Appendix results.
The application of the methods illustrated in this appendix will allow the user to determine the following pump and station
parameters.
(1) Maximum design head.
(2) Design heads at rated pumping station capacity.
(3) Capacity requirements other than those required by the hydrology requirements, such as capacity required for siphon
priming.
(4) Type of pump.
(5) Estimated pump physical size.
(6) Power required at the design points.
(7) Pump speed.
(8) Station Net Positive Suction Head Available (NPSHA) and pump NPSHR.
(9) Sump dimensions.
B-2. Vertical Wet Pit Pump Selection Sample Problem...
( a ) Design data and requirements.
(1) Pump conditions. The starting point for all
pump selection is the hydrology requirements for the
station site. The following is assumed given conditions
for each pump:
Required from hydrology report:
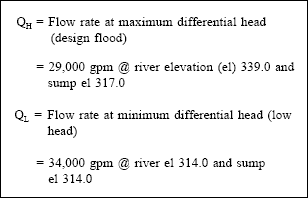
(2) Station arrangement. Station general arrangement
and discharge system are determined as presented in EM
1110-2-3102. For this example, a discharge over the
protection with siphon assist was assumed (Figure B-1).
A static head diagram (Figure B-2) should now be constructed.
The top of the discharge pipe is obtained by
sizing the pipe diameter based on an approximate maximum
velocity in the pipe of 12 feet per second (fps)
(using the greatest Q requirement) and adding the diameter
to the invert elevation. The invert elevation is usually
set equal to the top of the protection on either side of the
station so that backflow will not occur with any river
level to the top of the protection.
(3) Size discharge pipe.
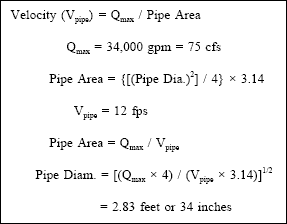
Use standard sized pipe, the next larger standard size pipe = 36 inches nominal (35.25 inches inside diameter (ID).
For this first calculation, use the following wall thickness :
1/4 inch, 12- to 20-inch diameter of pipe.
3/8 inch, 24- to 42- inch diameter of pipe.
1/2 inch, 48 inch and over *.
* : (Larger pipe sizes may require thickness greater than 1/2 inch for support considerations).
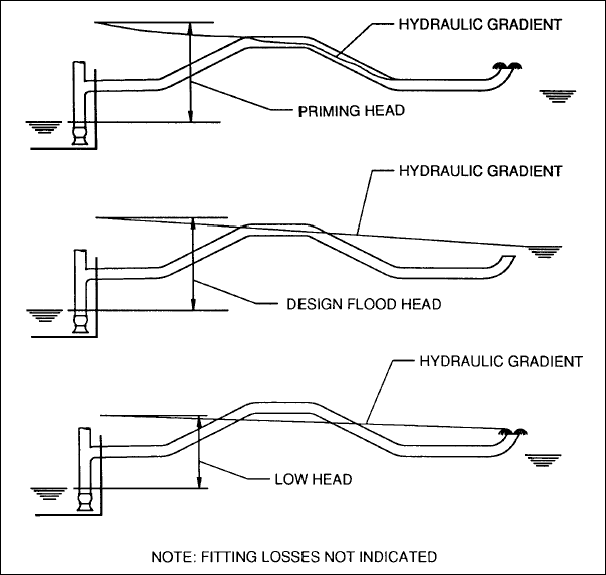
Figure B-1. Discharge pipe system.
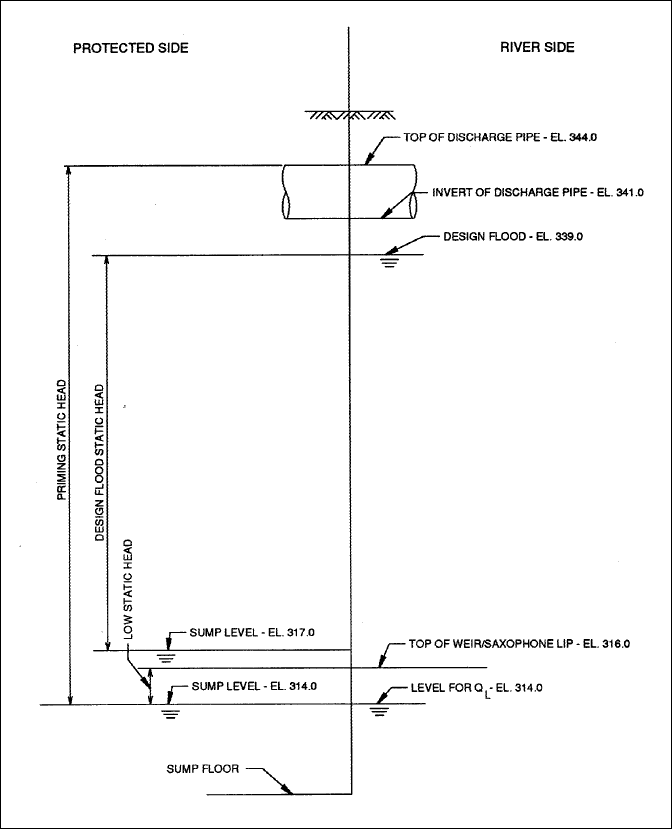
Figure B-2. Construct the static head diagram.
A diagram of the typical over the levee discharge pipe
system is shown in Figure B-1.
(4) Priming condition. Since the selected discharge
system will use a siphon assist, another condition, priming,
must be determined. The first step is to determine
the required priming flow rate QPRIME. The computation is
based on the flow required to obtain an average velocity
in the discharge pipe at its highest point of 7 fps. The
value of 7 fps will provide a prime for discharge pipe
systems with diameters of 54 inches and less having no
extra bends other than those necessary at the bottom and
top of the levee. For discharge systems with larger
diameters or unusual flow lines, consider using the
critical depth of flow elevation occurring in the pipe
instead of top of pipe. Methods used to calculate the
critical depth in a circular pipe are shown in the
Handbook of Hydraulics (King and Brater 1963).
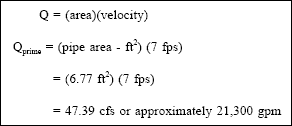
The priming static head (Figure B-2) is equal to the difference between the top of the discharge pipe at its highest point
and the lowest pump sump level used for starting the pumps.
Highest point in discharge pipe at top of protection = elevation of protection + diameter of pipe = 341.0 + 3.0 = 344.0 ft.
Priming static head = 344.0 - 314.0 = 30 ft.
(5) Siphon condition. With a siphon assist system,
it is required that the siphon recovery is not greater than
28 feet. The value of 28 feet is used to prevent possible
water vaporization and siphon priming problems. An
up-turned saxophone discharge pipe or a weir is used to
limit the recovery to 28 feet and seal the end of the pipe.
When one of these means is used, the low head must be
checked based on the saxophone or weir elevations. If,
at the pumping mode, the lowest water level on the discharge
side provides for a recovery less than 28 feet,
then a saxophone discharge or weir is not required. The
discharge end of the pipe should be submerged when a
separate vacuum priming system is provided to prime the
pump. The computation is as follows :
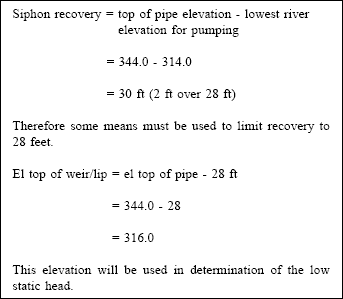
(6) Suction requirements. The other part of the
pump conditions is the pump suction requirements. This
is specified as NPSHA for the various pumping conditions.
It is computed as follows :
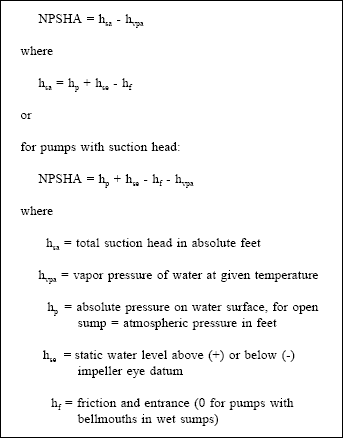
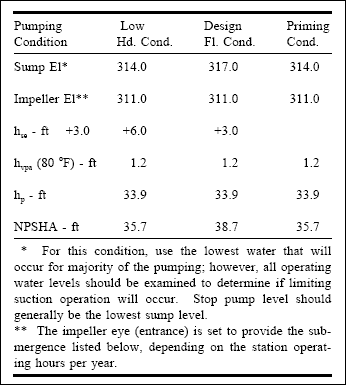
(7) Submergence requirements. The submergence
shall be for the lowest pumping level at the station where
the pumps will be operating for periods of time greater
than 2 hours. Operation below these submergence levels
is permitted as long as the operation time is less than
2 hours. In no case will any operation occur with water
levels below the impeller eye or datum. Assume for this
example that the operation time will be over 300 hours
per year; therefore, the impeller elevation is 3 feet below
lowest sump elevation for any pumping condition to
assure a flooded impeller.
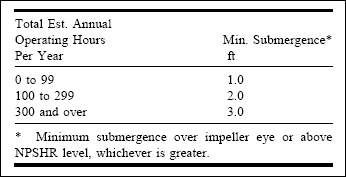
(8) Total system head. The next step is to compute
the total system head curves for each condition. The
total system curves will include all the losses plus the
static head for that condition. For the purposes of pump selection, the total system curves will be constructed to
include the losses in the pump beyond the pump bowl.
This will permit the subsequent pump selection to be
done on the basis of bowl heads. Bowl head is considered
the head produced by a pump if it were measured
immediately after the discharge vanes. Bowl heads
therefore do not include any losses in the transition piece
and elbow of the pump which is supplied with the pump.
The bowl heads permit the user to use any type of discharge
system beyond the pump bowl. For this example,
there would be three system curves: design flood, low
head, and priming. It should be noted that any system
total head curves used for procurement of pumping
equipment would only include system losses which
would be external to the pump equipment being furnished
by the pump manufacturer. Generally, the pump manufacturer
would subtract the column pipe and discharge
elbow losses from his bowl performance, thereby producing
a performance curve referenced to the discharge point
of the equipment being supplied. For this design the
pipe lengths are as follows :
Priming - 175 ft, operating - 250 ft.
The total system head required by the pump to deliver
the minimum and the maximum flow rates required
should be calculated and tabulated as shown in
Table B-1. The total system head should include the
discharge loss, pipe and elbow losses, and static head.
The next step is to use this table and develop system
head (pump bowl) loss curves as shown on Figure B-3.
( b ) Pump selection.
(1) Formulas used. The method of pump selection
consists of computing the performance of a larger prototype
pump from the performance a model pump or a
small prototype pump. The following relationships are
used for these computations. All relationships are based
on pump bowl performance.

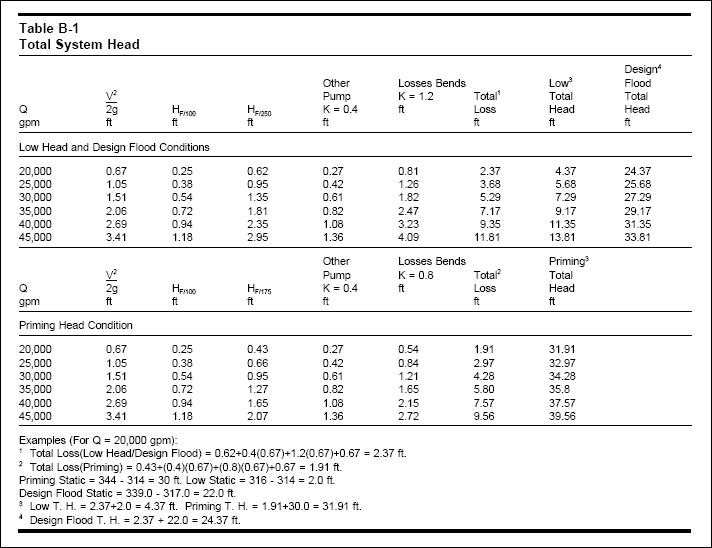
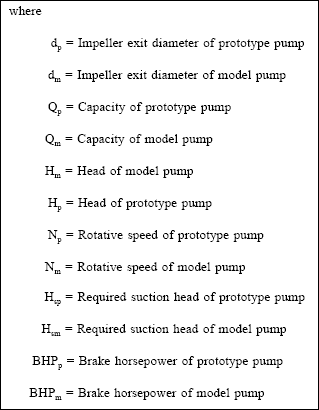
(2) General. The performance of a prototype pump
can be determined by the use of the above equations
applied to the model pump performance. As can be seen
from the above formula, the two variables are impeller
diameter and rotative speed. The selection of these two
factors should be to obtain a prototype unit which has the
smallest impeller diameter and the highest rotative speed,
while still meeting all of the performance requirements of
head, capacity, and NPSHA. The impeller diameter is shown on each model pump curve. For mixed-flow type
pumps, the maximum impeller diameter is indicated on
the curves. On mixed flow pumps, it is possible to
reduce the impeller diameter by up to 5 percent, thereby
changing the performance of the pump from that shown
on the curves for full diameter performance. Blade
pitches are taken into account and shown as different
model pump curves.
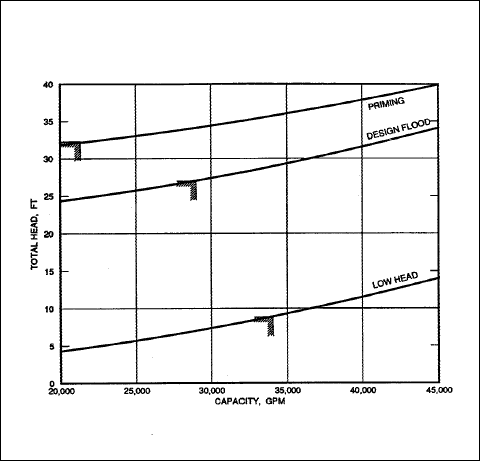
Figure B-3. System head (pump bowl) loss curves.
(3) Calculation method. The actual calculations of
the prototype pump performance is best done by trial and
error. A personal computer using a spreadsheet type
program simplifies and speeds these calculations and the
pump selection. CECW-EE can furnish information of
various Districts where different programs are available
to perform these computations.
(4) Sample calculations. The following is an example
of computations used to select a prototype pump. It is usually best to start with a model pump that has a
head range near that of the required condition points. As
a first try, use model curve MF-1 (Figure B-4) and calculate
prototype performance. A mixed-flow impeller was
tried because highest head requirement was over 20 feet.
The selected prototype impeller is usually smaller than
the discharge pipe diameter. The maximum prototype
pump speed can be estimated by applying the following
formula based on suction specific speed (S).
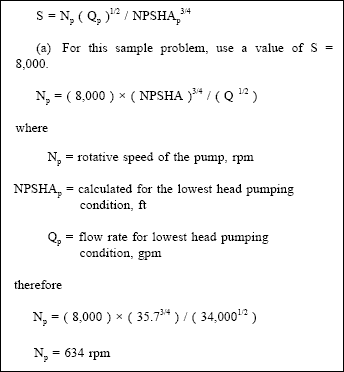
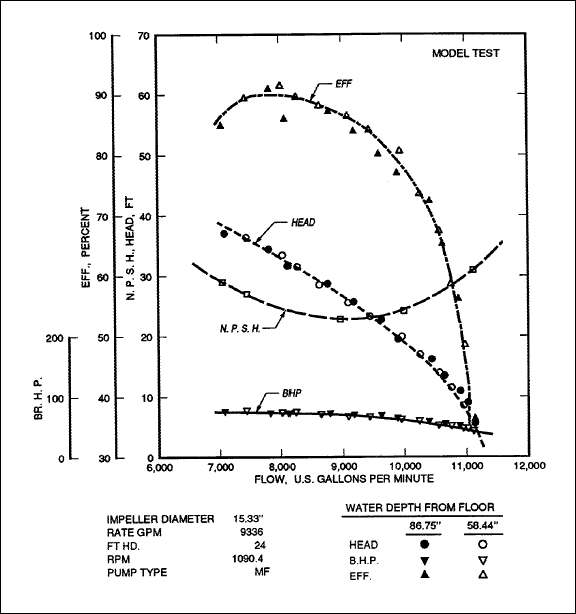
Figure B-4. Pump model curve MF-1.
(b) The pump speed should not in general exceed
this calculated rotative speed. The speed used must also
meet the restrictions of the pump driver. If using an
electric motor that is directly connected to the pump,
then the synchronous speed of the motor must be
considered. When using an induction motor, the full-load speed can
be estimated to be 97 percent of the synchronous speed.
The synchronous speed can be calculated using the following
formula for electricity with a frequency of
60 cycles.
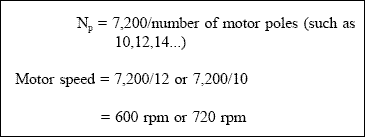
(c) Since 720 rpm is over the calculated maximum of
634 rpm, the lower synchronous speed of 600 rpm is
used. Assuming an induction motor is to be used, the
running speed when operating at full load is estimated to
be 97 percent of 600 rpm or 582 rpm.
(d) Try Model MF-1. Based on the Pump Model
Curve MF-1 (Figure B-4), calculate the diameter of the
prototype impeller using the model law (constant specific
speed and equal heads.
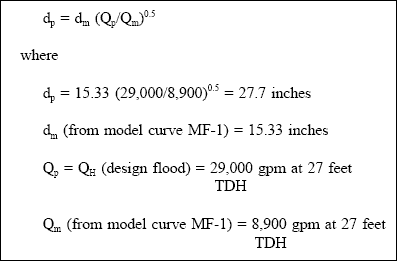
(e) Develop prototype performance curve based on
model curve MF-1 and verify that design conditions have
been met (Figure B-5).
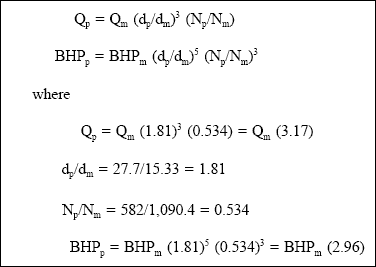
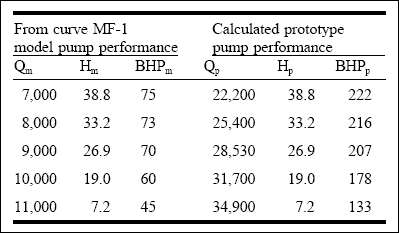
(f) The results of the first prototype pump computation
are plotted on the system head loss curves. Results
show that a pump with a 27.7-inch impeller rotating at
582 rpm will satisfy the design requirements. Next,
other model pumps and different prototype speeds would
have been tried to find other prototype pumps that will
meet the requirements. An average prototype pump size
could then be calculated. All station layout dimensions
would be based on the corresponding standard size pump.
The NPSH required by the prototype or model is then
checked against the NPSH available. Cavitation curve
MF-1 (Figure B-6) confirms that there is adequate
submergence.
(5) Pump dimensions.
(a) General. Determine the dimensions for all the
model pumps selected. Since the sump dimensions and
elevations used depend on the pump dimensions, some
means must be used to determine the dimensions to use
for the station layout from the range of pumps selected.
The selection of dimensions to allow the maximum number
of pumps to meet the guidelines is given below.
(b) Bell diameter.
The bell diameter = D.
Average D, (DA) = Sum of bell diameter for all selected pumps divided by number of selected pumps.
Largest bell diameter (DLARGE), but not larger than 1.2 times DA.
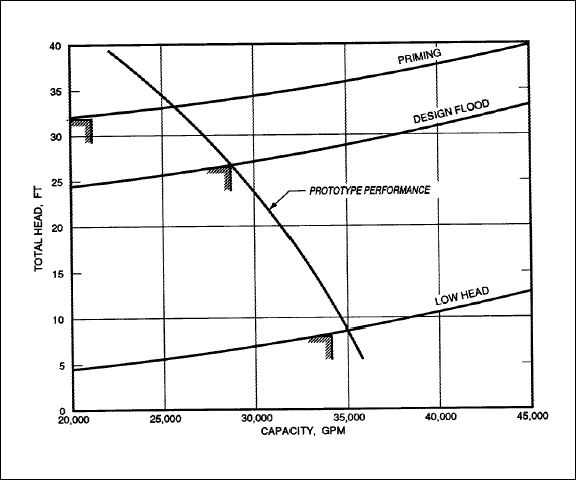
Figure B-5. Prototype performance curve superimposed on the system head curves (pump bowl) pump MF-1.
- Smallest bell diameter (DSMALL), but not less than 0.9 times DA
- Sump width1 = 2 times DLARGE.
- Sump width2 = 2.5 times DSMALL.
- Sump width is the larger of sump width1 or width2.
- D = 1/2 of the sump width from the above step.
(c) Impeller elevation. The impeller eye (entrance) is
set to provide the submergence indicated above in the
paragraph on pump conditions. In this example, the
impeller was set at el 311.0. The bottom of the bell and
sump floor elevation are set as follows :
- Bottom of pump bell = impeller eye elevation minus 1/2 D.
- Floor of sump = bottom of bell elevation minus 1/2 D.
(d) Minimum pump height. The minimum distance
from the floor of the sump to the centerline of the pump
discharge must be determined to establish a minimum
floor elevation. The dimension form the floor of the
sump to the bell inlet is determined above. The distance
between the centerline of the discharge to the suction bell
inlet should be provided by pump manufacturers offering
the type and size of pump indicated by the prototype.
This pump dimension will vary from one manufacturer to
another. The maximum distance found should be used to
determine the minimum operating floor. Other considerations such as local flooding due to power outage
and surrounding ground elevations may require a higher
operating floor elevation.
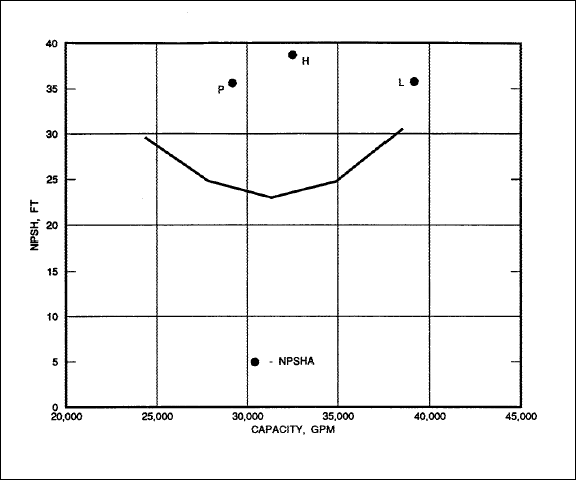
Figure B-6. Cavitation curve MF-1.
c. Station layout.
(1) Pump dimensions. For stations with up to three
equal sized pumps having capacities not greater than
5.66 m3/s (200 cfs), and with straight inflow, in front of
the station, the dimensions indicated on Chart B-2 may
be used. The flow to the station should occur in a
straight symmetrical channel with a length equal to or
greater than five times the station width (W on Chart
B-2). The invert of the channel in front of the station
should not contain any slopes greater than 10O. The
submergence indicated on Chart B-2 is the depth of
water suggested to prevent harmful vortexes. In most
cases the water depth will be greater due to the cavitation
allowance listed above. If there are any unique inflow
conditions or problems the designer should contact the Waterways Experiment Station Hydraulic Laboratory to
determine alternative layouts to correct or compensate for
the problems.
(2) Considerations for station layout.
(a) Space inside of the station is provided to set one
pump driver and disassemble one pump using the overhead
crane.
(b) Space in front, side and back of electrical equipment
is provided as required by the electrical code
requirements.
(c) Space is provided to remove any pumping unit
without disassembly of another unit or electrical gear.
(d) Space is provided for an office and sanitary
facilities for any station that will be manned.
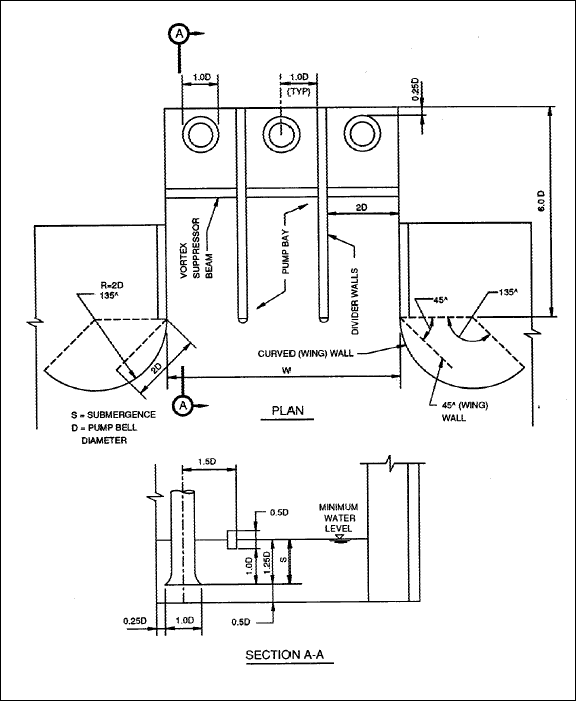
Chart B-2. Vertical pump sump dimensions.
(e) Space is provided for spare parts and maintenance equipment to be stored at the station.
(f) Location of electrical gear is coordinated with service entrance.
(g) Exit and equipment door are provided and properly located.
(h) Straight approach to pump sump is provided.
(i) Any sump closure gate is neck down at least 4D from the pumps.
(j) Access is provided to trashrack platform for trash removal by truck.
(k) Sufficient room is provided to position a truck for equipment removal.
(l) Minimum slope is provided in ditch flow line beyond the front of the trashrack.
(m) Incoming overhead power lines do not present a hazard to operation and maintenance of the station.
( d ) Pump manufacture’s selection.
Using the preliminary
layout, correct any system head curves such as
change in low head due to different elbow elevation.
Check the pump selections using the new system requirements
and refine layout as necessary. It is also best at
this time to request pump selections from the pump manufacturers
using the requirements and sump layout above.
This will confirm the pump selections. Chart B-3 is an
example of the information to be furnished and requested
from the pump manufacturer.
B-3. Vertical Submersible Pump Selection...
( a ) Design data and requirements.
(1) Pump conditions. The sample calculations are
based on a pumping station with a through-the-protection
discharge, pumping into a discharge chamber. The following
is the assumed conditions for each pump.
(a) Required from hydrology report:
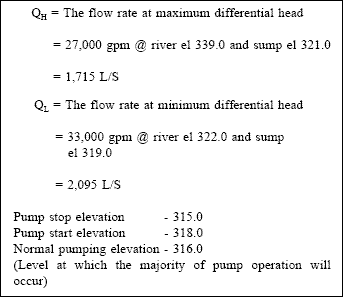
(b) Submersible propeller pumps (Plate 24) typically
are constructed in such a manner that the pitch angle of
the propeller blades can be changed; therefore, the selection
method used is different from that used with fixed
blade pumps. The selection procedure used for submersible
pumps will be to compute the system requirements,
and then select a pump from available performance
curves. After the initial selection is made, then the system
requirements can be corrected if necessary due to a
more accurate discharge tube sizing and the pump selection
confirmed or changed. In addition to the selection
based on pump head and capacity requirements, the
pump selected must also be checked to ensure that its
suction requirements are satisfied by those provided by
the station layout.
(c) The pumping system is composed of a
discharge/support tube in which the submersible pumping
unit is located. In this example, the tube would be fitted
with an elbow section and a horizontal pipe terminating
with a flap gate. For submersible pump installations of
this type, the discharge line invert should be well above
the motor to hold the elbow losses to a minimum but low
enough to keep reasonable the static head reasonable.
(d) The first estimate of the tube diameter can be
based on the size required using a 6.5-fps velocity and
the greatest required capacity. After calculating a diameter
based on these conditions, the nearest size tube
diameter as shown on Table B-2 shall be used for the
preliminary calculations. For the example problem, the
calculated discharge is 45.4 inches. The nearest standard
tube diameter of 48 inches is used. The bottom of the
tube can be set using the minimum tube submergence
required. These submergence requirements are provided
by the submersible pump manufacturer and are based on
annual operating hours and pump tube design. For this
example, 3.0-ft minimum submergence is required.
Elevation bottom of the tube = 315.0 - 3.0 = 312.0 ft.
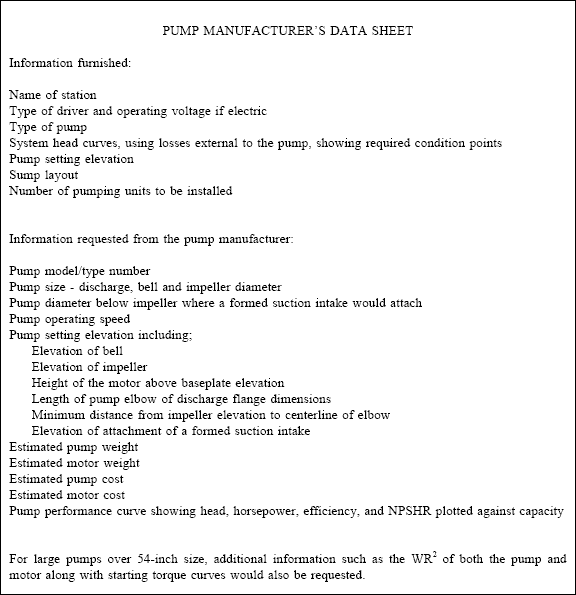
Chart B-3. Pump manufacturer’s data sheet.
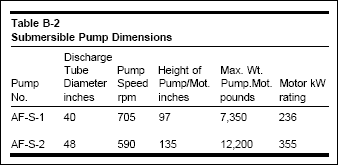
(e) The bottom of the tube elevation may need to be
lowered later to satisfy the sump velocity criteria as indicated
in Figure B-7; however, this will not affect the
pump selection.
(f) The minimum invert elevation must be above the
top of the motor. With the bottom of the tube set at
el 312.0, the minimum elevation of the elbow invert can
be determined by adding the pump/motor height indicated
on Table B-2 to the bottom tube elevation.
Minimum invert elevation of elbow = 312.0 + 135 inches = 323.25.
(g) This elevation will be used since it is above the
river elevation for the low head condition. The horizontal
discharge pipe connected to the tube is sized based on
the flow velocity of 12 fps at maximum capacity. The
calculated horizontal discharge pipe size is approximately
33.5 inches; use nominal 36-inch pipe.
(h) A static head diagram is constructed (Figure B-8)
using the given hydrology information and preliminary
information determined above on the pump tube and the
discharge piping. The floor elevation is set 1/2 tube
diameter below the bottom of the tube. This first static
head diagram will be used to make a preliminary pump
selection. In most cases, at least one or more static head
diagrams will need to be prepared after the preliminary
pump selection is made to allow the pumping unit
dimensions to agree with the static head diagram. The
pump selection process would follow the steps below :
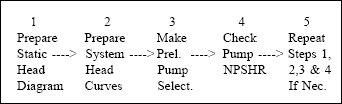
(2) System head. The next step is to compute the
system head curves (Table B-3). The system head curves include all of the losses plus the static head for
that condition (Figure B-9). The system loss curves
include all the losses beyond the pump motor, since
losses below this point are included in the given pump
curves. A loss of K = 0.7 is used for the losses in the
pump column and elbow. The other losses in this example
are considered to be equal to the velocity head.
Next, calculate the net positive suction head available
(NPSHA) for the various pumping conditions. Refer
back to the previous example problem for the definition
of terms.
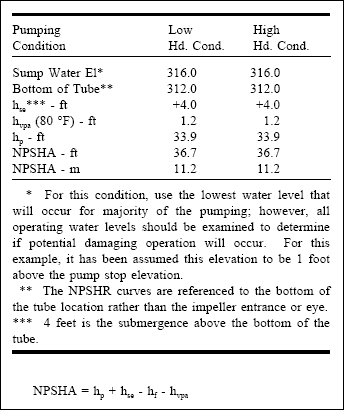
( b ) Pump selection.
(1) General. Using the pump curves AS-F-1 and
AS-F-2 (Figures B-10 and B-11) and the required condition
points from the system head loss curves, a preliminary
pump selection can be made. The pump
performance head-capacity curves are shown for the
various blade angles that are available for that pump. A
single blade angle that satisfies all design conditions
should be used. Changing blade angles during flood
events should not be considered because of the need to
remove the pumping unit and thereby taking it out of
operation. These pumps have the motors directly
attached to the pumping unit. The motors’ ratings are shown in kilowatts, which is the input power to the pump
shaft. The dashed lines running diagonally from upper
left to the lower right show the motor sizes available.
Any design condition below these dashed lines may use
the motor rating indicated for that line. The information
furnished in this manual can be used for the preliminary
layout of submersible type pumping stations; however,
information should be requested from all manufacturers
for the design memorandum.
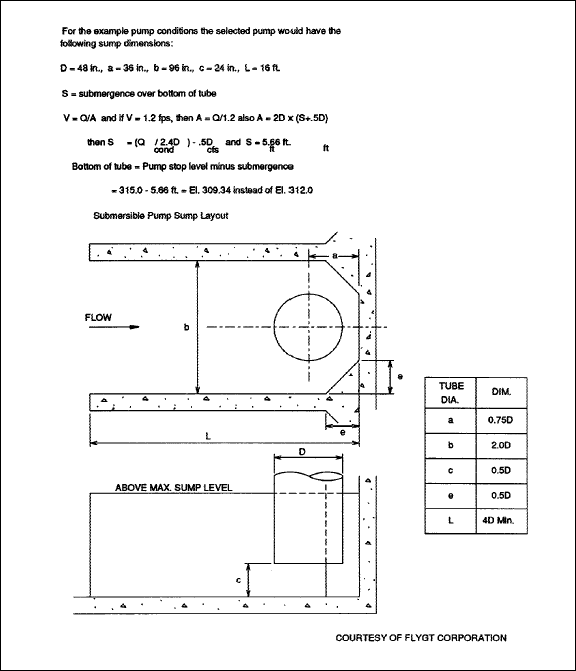
Figure B-7. Typical submersible pump sump layout.
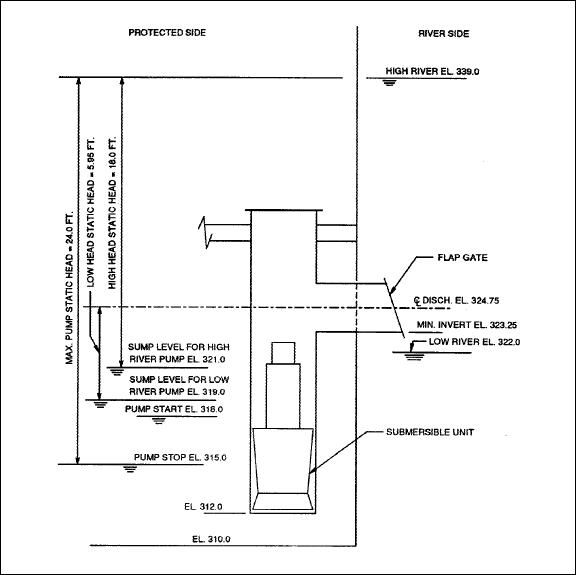
Figure B-8. Static head diagram.
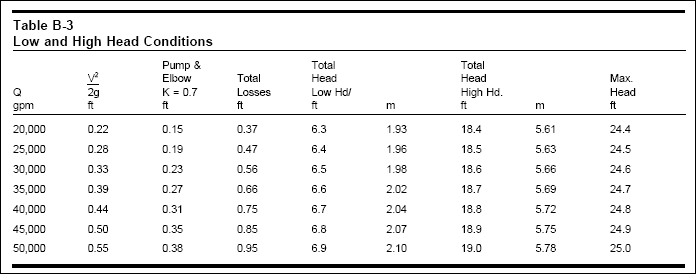

Figure B-9. System head loss curves.
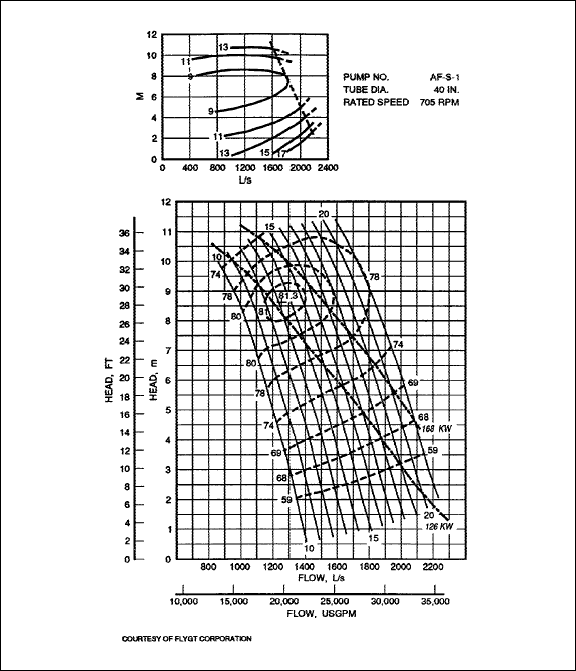
Figure B-10. Submersible pump curve AF-S-1.
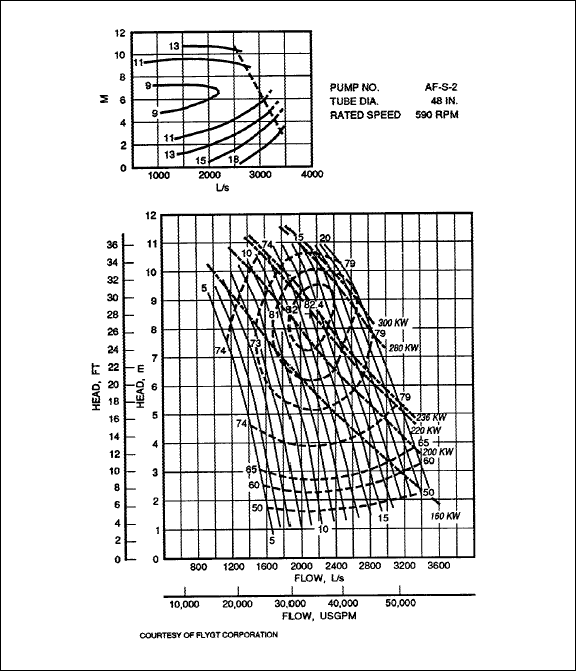
Figure B-11. Submersible pump curve AF-S-2.
(2) Selection procedure. Review of the pump curves
indicates that an AF-S-1 size pump operating at a speed
of 705 rpm and set at a blade angle of 20 degrees will
satisfy the head-capacity design conditions.
(a) The next step is to check the suction requirements
of the pump. This is done by plotting the head-capacity
curve for the blade angle chosen above on the NPSHR
curve for that pump. The plotted head-capacity curve
crosses the various NPSHR curves for that pump indicating
the required suction head for different pumping
requirements. The curve shown below indicates that the
preliminary AF-S-1 pump selection requires a greater
submergence than is available; therefore, another pump
must be tried or greater submergence provided. Unless
the additional submergence required is less then 1 or
2 feet, it is usually less expensive to provide a larger,
slower speed pump than provide a deeper station. A cost
comparison can be made to more accurately compare a
deeper sump station with that station requiring a larger
area because of increased pump size.
(b) The next choice would then be the next larger
size pump operating at its the highest available speed and
meeting all the required design conditions. This would
be the AF-S-2 size pumping unit operating at 590 rpm.
The 10-degree blade angle satisfies the design conditions
and the suction requirements.
(c) Since the selected size pump of AF-S-2 has the
same size tube as that first selected, the static head diagram
and system head curves are correct.
(d) The net positive suction head requirements for
the pump are determined by plotting the selected blade
angle head-capacity curve on the cavitation curve.
Where this head-capacity curve crosses the NPSHR lines
indicates the NPSHR values for the pump.
(3) Station layout. Using the listed discharge tube
diameter (Table B-2), the sump can be sized according to
Figure B-7. Check the pump selections using the new
system requirements and refine the layout as necessary.
The sump layout is now complete, and the remainder of
the station layout can now be done. It is also best at this
time to request pump selections from the pump manufacturers
using the requirements and sump layout above.
This will confirm the pump selections and permits adequate
bidding competition. The following are considerations
for station layout :
(a) Sump velocities. The average velocity in each
pump sump in front of the pump for continuous operation
should not be greater than 0.37 meter per second
(1.2 feet per second). For intermittent operation (less
than 200 hours per year), the average velocity may be
increased to 0.49 meter per second (1.6 feet per second).
To obtain these velocities, the sump depth is varied while
the sump width is kept equal to two tube diameters.
These maximum velocities are maintained to diminish the
formation of vortices in the sump. The water levels
obtained by application of these velocities may not be
high enough to satisfy the pump’s NPSHR. The NPSHR
takes precedent, and the resultant submergence will be
greater than that necessary to prevent vortices.
(b) Superstructure. A structure should be provided
to house the motor starters, switchgear, and engine generator,
if provided, and office space for operating personnel.
Unless dictated by climatic conditions or needed
to satisfy some other specific purpose, the structure need
not cover the pump locations.
(c) Hoist. A method for removing the pumping
units should be provided. Any inspection or repair work
to the pumping unit is done with the unit removed from
the tube. Inspection which requires the removal of the
pumping unit are required at least annually to check the
integrity of the pump/motor seal system. A monorail
hoist capable of lifting the entire pumping unit should be
provided. If the maintenance organization has a truck
crane of sufficient capacity to raise the pumping unit or
such a crane would be readily available on an emergency
basis, then a permanent hoist would not be required.
B-4. Formed Suction Intakes...
( a ) General.
The formed suction intake (FSI) is used
on pumps to improve flow to the impeller of vertical
pumps. The FSI can be used on almost any pumping
application. It is, however, recommended when adverse
flow conditions occur upstream. Figure B-12 shows a
typical FSI. ETL 1110-2-327, Geometry Limitations for
the Forced Suction Intake, provides additional information.
The FSI can be used on small pumps; however, the small openings could clog or silt in during nonoperational
periods.
( b ) FSI size determination.
FSI is connected directly
to the suction flange below the impeller. This diameter,
d, will determine the size of the FSI. The selection of
the pump will be the same as that used for the vertical
wet pit pump except for the additional suction loss.
Whereas the conventional vertical pump with a bell uses
a suction loss of zero, the pump equipped with an FSI
should use a loss of K = 0.15. After the pump has been
selected, it is necessary to determine the suction flange
connection inside diameter, d. For axial flow pumps, d
will be the same diameter as that determined for the
impeller. For mixed flow impellers, d can be estimated
to be 0.85 of the impeller diameter d. After d has been
determined, the rest of the dimensions of the FSI can be
found by applying the ratios indicated in Figure B-12. In
a typical pump selection, the suction diameter will vary
with different pump manufacturers. To permit maximum
biddability, the FSI must be sized to allow sufficient
manufacturers to bid.
( c ) FSI connection.
For vertical wet pit pumps which
are suspended from the operating floor, the connection
between the FSI and the pump is determined by the
pump manufacturer after the pump manufacturer
performs a dynamic analysis of the pumping unit to
determine the critical speeds of the pump. It is recommended
that the FSI be formed or cast integral with the
sump concrete.
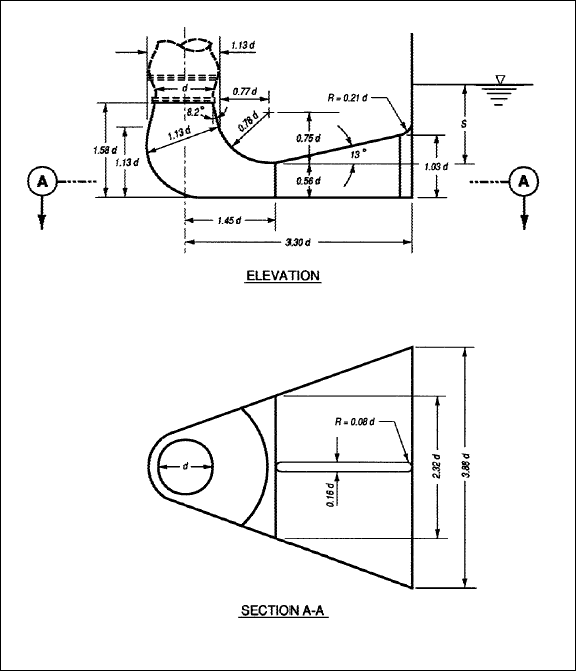
Figure B-12. Typical formed suction intake.