Trickling Filter...
The History of Fixed - Film Wastewater Treatment Systems...
Introduction...
The Science and 'art' of wastewater engineering stretches only slightly beyond one hundred years. Within this period, the
applied technology has certainly made significant strides in promoting disease control and environmental protection. Fixed-film
treatment unquestionably plays an important role in this history, particularly since it represented the original biological
mechanism. Beginning with options like the trickling filter, intermittent filter and contact bed, fixed-film systems dominated
the technology of wastewater treatment for several decades. And although this status has subsequently been assumed by suspended
growth process, there is unquestionably a resurgence of interest in fixed-film applications. Given the relative historical
significance, and projected future of fixed-film systems, a chronological review of the associated progressive developments
should be both interesting and informative. This paper will, therefore, explore the genealogy behind our current fixed-film
technology, condensing the relevant yesteryear literature into twenty-five year increments. While attempting to limit this
synopsis to a reasonable length, every effort has been made to facilitate a thorough documentation of the associated
literature.
"Flow - Chart of the Trickling Filter Process - 1"...
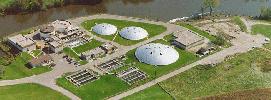
1850 - 1875 : As described by the classic Dickens tale in 1859, "It was the best of times, it was the worst of times...".
This literary image poignantly portrays a mid-nineteenth century era freshly endowed with the blessings of an Industrial
Revolution, yet virtually helpless in the face of rampant, epidemic disease. Cholera, alone, flared through the British
Isles in four deadly outbreaks within one terrifying ten year period. Without question, these problems with communicable
disease provide a sad reflection on the existing deficiencies in environmental sanitation. However, the concurrent infancy
of bacteriology yielded only vague clues regarding the dangerous correlation between fecal contamination and disease
transmission. Existing efforts towards sewage disposal, let alone treatment, were virtually non-existent. Certainly it was
fortuitous, then, that legislation (i.e., the Nuisance Removal Act) was enacted in 1858 to control sewage discharge, albeit
more so a function of safeguarding aesthetics rather than a perceived health hazard. This emphasis quickly shifted towards
disease control, though, following Dr. John Snow's monumental publication on epidemiology within the same year. England shortly
organized a series of Royal Committees charged with the study of problems relating to sewage disposal and treatment. Their
initial findings categorized the existing state-of-the-art according to chemical precipitation, filtration and irrigation,
with the latter two procedures generally associated with land treatment. While land systems carried a traditional background
extending several centuries, some of the other available options were rather curious. One such precipitation procedure, the
ABC process, employed a bizarre mixture of alum, blood and clay.
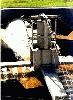
None of the available treatment mechanisms were, however, recognized as biologically-related systems. Hence, Dr. Alexander
Mueller's demonstration in 1865 that sewage could be purified by living organisms in a filtration column provided a major
revelation. Dr. Mueller, a prominent City Chemist of Berlin, subsequently patented his biological purification process
several years later. Unquestionably avant-garde, neither the patent nor the fundamental concept attracted much attention,
though. In 1868, one of the Commission members, Sir Edward Frankland, began an epic study of filtration performance on raw
London sewage in laboratory columns packed with media ranging from coarse gravel to peaty soil. Using a twice daily dosing
pattern, Sir Frankland maintained successful filtration performance for over four months. Although the filter's treatment
capability was solely credited to physical-chemical means, the associated establishment of the intermittent filtration
concept had notably introduced a necessity for resting or aeration periods between sewage applications. Based on these
results, the Royal Commission began to place considerable emphasis on the use of intermittent land filtration. In 1871,
J. Bailey-Denton initiated the first full-scale operation at Merthyr Tydvil, Wales. Success at this facility, and others
subsequently developed by Bailey-Denton, soon promoted several engineers to apply Frankland's concept. Unfortunately, these
engineers oftentimes neglected critical factors such as soil permeability and/or the necessity for intermittent dosing,
such that failures became commonplace. And with subsequent documentation of 38 such failures, technical interest in the
intermittent concept quickly faded.
1875 - 1900 : Following upon the singular work by Mueller over a decade earlier, several researchers successively
explored the microbial aspect of sewage purification. Five years later, Warrington confirmed that sterilized solutions lost
their nitrifying ability until inoculated by fresh soil. And in 1890, Winogradsky succeeded in identifying Nitrosomonas
bacteria. These pioneers were, however, still uncertain as to the pragmatic application of these bacterial mechanisms to
effective treatment. Up to this point, Europe had dominated the developments in wastewater treatment technology. Within the
United States, though, comparable concern for pollution control resulted in the establishment of the Lawrence Experimental
Station by the Massachusetts State Board of Health. Organization of the Lawrence facility was handled by Hiram F. Mills, a
distinguished hydrologist, and Professors Sedwick and Drown from the Massachusetts Institute of Technology. Under the direction
of Allen Hazen, the Lawrence group began a series of filtration experiments in 1887 which were comparable to the prior Frankland
tests on intermittent dosing. In this case, however, the filters were significantly larger, at 1/200th acre per
unit. While their results subsequently verified the treatment potential afforded by an intermittent filtration mechanism,
the Lawrence group's first publication in 1890 provided a monumental analysis of the associated microbial activity. Indeed,
their findings truly furnished the hallmark demonstration that microorganisms carried within the filter media could degrade
sewage in an aerobic environment facilitated by intermittent dosing.

Given the success of the Lawrence experiments, biological treatment systems rapidly expanded in terms of application and
sophistication. Considerable controversy had arisen in the 1890's over patent rights obtained by Donald Cameron for septic
tanks, such that most municipalities were anxious to find suitable treatment alternatives. Several full-scale intermittent
filtration systems were, therefore, constructed in the New England area, most of which were successfully maintained for
several decades. In Europe, though, sanitary engineers were still hesitant to accept the intermittent filtration concept.
This opinion likely stemmed either from a lingering dissatisfaction with the Frankland-era facilities, or because of the
widespread unsuitability of European soil. Instead, they chose to intensify filtration rates using coarser media such as
coke breeze, gravel, burnt clay and coarse chalk. Scott-Moncrief probably began the first such tests, using sewage percolation
through sequential rays of 1 inch diameter coke media. In 1893, J. Corbett also employed a serial filter scheme, with an
additional wooden trough to continuously distribute influent sewage across the bed. And in the same year, F. Wallis Stoddart
reported on the use of a course media filter receiving a continuous, trickling flow. Of these two latter researchers, Corbett
acknowledged the impetus and direction provided by the previous Lawrence findings. Stoddart, however, insisted that his work
stemmed from Frankland's principles and that his continuously percolated units were the first of their kind. In either case,
the trickling filter had been conceived.
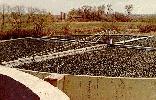
Another classic European option which developed at much the same time was the contact bed. Acting along the lines of the
Lawrence experiments, W. Santo Crimp and W. J. Dibdin decided in 1891 to experiment with a dosing pattern which flooded a
coarse media filtration bed for 8 hours, followed by 16 hours in a drained state. Of the coarse media materials tested on
chemically-treated London sewage, Dibdin found that the coke breeze provided satisfactory treatment, while sand clogged
extensively. In subsequent tests, Dibdin experimented with a double-contact approach, using primary and secondary beds
respectively containing successively smaller media. The success of this operation quickly led to several full-scale
installations, all of which maintained the cyclic fill, drain and react periods. And in their fifth report, the Royal
Commission provided extensive technical support for the installation and operation of such contact beds. Dosing strategies
for both the trickling filters and contact bed systems received intensive study in the years immediately following their
development. For uniform loading of intermittent filter units, Waring and Lowcock devised a simplistic technique in 1892
based on an overlying fine gravel layer to promote equivalent flow distribution. However, this procedure retarded desired
bed aeration. Perhaps as a consequence, Waring also devised and patented a trickling filter system which employed forced
aeration.
Stoddart's approach to flow distribution was that of corrugated sheet-metal plates with symmetrical discharge ports.
Although considered satisfactory, leveling of these horizontal plates required tedious adjustment. Corbett initially used
slotted wooden troughs and then switched to a variety of fixed-spray jets. In 1896, Carfield improved the fixed distributor
concept by adding an intermittent dosing tank. The siphon action insured an intermittent dosing procedure which prevented
localized flooding at the media. Rotary flow distributors were originally tested in 1889, with additional refinement by
Corbett in 1894. Two years later, Whittaker and Bryant introduced a rotary sprinkler equipped with a pulsometer. This
latter addition not only produced a pulsed, intermittent flow, but also warmed the influent sewage. However, their model
employed perforated pipe distribution arms prone to clogging. Rotary wooden troughs were then introduced by Mather and
Platt to avoid this plugging problem.
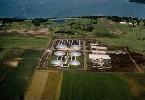
1900 - 1925 : Given the classic technical advancements made by Hazen, Stoddart, Corbett and Dibdin in the past
quarter century, the next twenty-five years could be viewed as an era of practical application and refinement. Of the
available biological treatment system (i.e., intermittent filtration, trickling filters and contact beds), it is interesting
to note that each comprised a fixed-film process. Rudimental experiments in sewage aeration were underway at the time, but
suspended growth systems did not originate for several years. Trickling filters were first introduced to the US in 1901
at Madison, Wisconsin. By 1910, several additions in mid-west and eastern cities brought the total to ten. Monumental in
size alone, the 31 acre Baltimore trickling filter system is remarkably still in operation some seventy-five years after
its initial development. Among these early US trickling filter units, and for several decades, fixed spray jets served
as the norm for flow distribution. Contemporary sewage treatment texts typically carried several pages devoted to spray
jet design and installation. In most cases, these distributions were also equipped with siphon dosing tanks. While rotating
distributors were only randomly tested in the United States (i.e. Springfield, MO in 1912 and Pontiac, MI in 1920), European
trickling filter designs favored the rotary or traveling sprinkler approach.
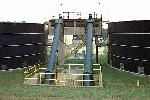
With the advent of trickling filter applications, interest in intermittent-filtration began to fade. Experimentation
continued on both options at Lawrence, demonstrating that the higher loading rates provided by coarse media design could
significantly reduce the requisite land area. Mathematical modeling of these biological filters was also initiated in 1916
by Tatham. In using a mass-balance derivation based on first-order kinetics, this study classically sought to define the
purification process according to precise chemical engineering principles. As for contact bed design, several full-scale
applications were recorded. Although a few large scale units were built in the United States, contact beds did not receive
much interest outside Europe. Because of the involved flooding routine, anaerobic conditions tended to lower final effluent
quality. This circumstance, combined with frequent clogging of the bed media by entrained sludge, certainly began to cast
doubts on the usefulness of contact bed treatment. Recognizing the desirability of an aerobic biofilm, Dibdin decided in
1904 to experiment with forced bed aeration. And to facilitate flushing solid matter from the bed, the coarse media was
replaced with slate slabs packed in horizontal layers. Operation of the modified unit still followed the phased fill-and-draw
routine. After twelve months of laboratory study, Dibdin successfully progressed to a full-scale demonstration of his slate
bed design at Devizes in 1905. However, in their fifth report, the Royal Commission indicated that the slate bed approach
should only be considered as a primary sedimentation mechanism.
Within the US, Dibdin's slate bed technique drew immediate interest. Experimental testing was initiated in Plainfield, New
Jersey in 1905. Historically important experimentation on slate bed treatment was also begun at Lawrence under the direction
of H. W. Clark and S. Gage. In comparing aerated slate bed units and aerated bottles containing algal suspensions, these
investigators reported in 1913 that the bottles provided better treatment efficiency. This variance was attributed to a
failure by the previously scrapped slate plates to accumulate a suitable biofilm during the short period of study. Shortly
thereafter, Gilbert John Fowler, a British Professor of Chemistry at Victoria University, visited the Lawrence labs and
witnessed these same experiments. Upon returning to England, Dr. Fowler's students Edward Ardern and William Lockett began
the historic study of suspended growth treatment. In 1914, these two students then published the first account of an activated
sludge process; sticking with the accepted intermittent (i.e. fill-and-draw) pattern, but distinctively switching to a
suspended biomass. Speaking on behalf of his students, Fowler did acknowledge the contributing and inspiration provided
by Clark and Gage, referring to Lawrence as "the Mecca of sewage purification...".
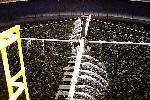
In much the same vein as Dibdin's slate bed, Dr. William Owen Travis also sought to improve upon the contact bed procedure.
As the local health officer in charge of a contact filter at Hampton, England, Dr. Travis was quite familiar with the
problem of bed clogging. His solution, introduced in 1904 as the Travis Hydrolytic or Colloider Tank, was essentially
configured as a multi-stage septic tank. Successively divided into detritus, hydrolytic and finishing tanks, the latter
two zones contained wooden colloider baffles or laths placed in a parallel array. These baffles were intended to attract
fine particulates for subsequent degradation. Only one such plant was ever built, at Norwich, England in 1909. The construction
at another Travis facility by the Emscher Drainage District Board was discontinued after the death of the involved design
engineer, Wattenberg. His replacement, Karl Imhoff, subsequently convinced the Board to switch to his personal design,
known thereafter as the Emscher or Imhoff Tank. As a footnote to this era, mention should also be made of two unique
patents obtained for rotating support media. The first, conceived by Weigand in 1900, comprised a moving cylinder with
wooden slats. Poujoulat's patent in 1916 employed agglomerated slag or porous brick fashioned as a hollow cylinder and
rotated about its horizontal axis. Flow distribution was provided using a perforated pipe placed over the cylinder.
Although neither option attracted much attention at the time, these designs could well be considered vintage predecessors
to rotating biological contactor technology.
1925 - 1950 : Over the next twenty-five years, intermittent filtration and contact bed systems were effectively
discarded in favor of trickling filter design. Within the US, extensive efforts were made to improve and upgrade trickling
filter performance, including the development and adoption of technical standards for design loading, bed construction and
system operation. High-rate designs, developed to increase hydraulic capacity, were marketed by several companies, including:
Lakeside Engineering (Aero-filter), Dorr/Link-Belt Comp. (Bio-filter) and Infilco (Accelo-filter). In most cases, fixed-spray
jets were also discarded in favor of rotating distributor systems. Much of the popularity of these trickling filter units
could certainly be attributed to their relative simplicity, ease of operation and cost-effective performance capabilities.
Activated sludge was still a somewhat innovative process, and one which prompted considerable concern regarding its intensive
energy demand for aeration. Legal problems also plagued the activated sludge process, with costly patent infringement suits
filed against several major cities by Activated Sludge, Ltd. Many municipalities consequently turned away from suspended
growth systems in favor of the more conservative trickling filter option.
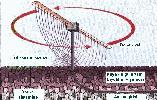
There were, however, several tangential developments in fixed-film technology which deserve considerations. The application
of one such option, the Hays process, actually rivaled the installation of trickling filters for the period of 1930 to 1940.
Developed in 1930 by Clifford Hays, a chemist from Waco, Texas, this procedure employed large asbestos-concrete sheets
vertically stacked with a 1" to 2" spacing. This design approach was physically analogous to the Dibdin slate bed (although
vertically arrayed, rather than horizontal) or the Travis colloider system (with the added feature of a diffused aeration
system). By 1942, there were 63 such units in operatoin throughout the US, many of which were located at military installations.
However, the limited availability of corrugated asbestos-concrete sheets during wartime conditions necessitated the use of
flat sheets. Lacking surface rigidity, these latter sheets frequently buckled and collapsed, resulting in process failures
which doomed its future consideration. Another such resurrected concept was that of the Nidus Rack. Developed by A. M. Buswell
in 1929, the Nidus Rack was intended to advance the Travis Colloider principle by significantly increasing the surface area
for colloid/particulate attraction. Numerous woven lattice units constructed of veneer or basket wood were placed into a
contact tank and mechanically agitated to promote deposition into an underlying settling compartment. Buswell's article
also mentions a number of related studies incorporating straw and corncob filter arrays. Following along the research line
established by Weigand and Poujoulat, a number of investigators independently studied the use of rotating support media. J.
Doman reported in 1929 on the development of a contact filter using partially submerged rotating plates constructed from
galvanized steel. The schematic overview provided with this report bears a striking resemblance to modern RBC designs.
One further option on rotating media, the Biological Wheel, was patented by A. T. Maltby shortly before 1930. The unit
consisted of a series of paddle wheels partially submerged in, and rotated by, sewage flowing through a surrounding channel.
Biofilm attached to these wheels consequently rotated in alternating fashion through the sewage and into the atmosphere.
1950 - Present : Mohlman's Sewage Works Journal editorial entitled, "Revival of the Trickling Filter,"
provides an excellent commentary on the mid-twentieth century state-of-the-art for fixed-film systems. Despite referencing
the relative advantages of system reliability and economy, this editorial acknowledged that trickling filters, "were almost
relegated to limbo". Indeed, over the next few years, conventional tricking filter construction using rock media was
unquestionably surpassed by activated sludge. Mohlman also provided a timely reference to the related technologies recently
developed by Buswell, Maltby, Doman and others. In essence, he collectively defended fixed-film treatments a worthy alternative
to the rapidly advancing suspended-growth concept. At much the same time, significant developments were occurring with the
incorporation of plastic-based support media into various fixed-film treatment systems. These synthesized media forms offered
several advantages over naturally available materials particularly in terms of surface contact area, voidage fraction, packing
density, and construction flexibility. Research and development on plastic media proceeded along two distinct lines during the
early 1950's. In America, bundled plastic units were being proposed and tested as innovative packing for stationary filter
applications. Investigators in Europe, though, began testing rotating plastic discs in much the same manner as Doman's rotating
cast iron system. These latter researchers at Stuggart University, West Germany, conducted extensive testing on wooden and
plastic discs, 1 meter in diameter. Further improvement by Popel and Hartman led to the use of expanded polystyrene media
which then opened the door for commercial application.
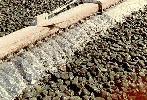
By 1957, the J. Conrad Stengelin Company in Tuttlingen, West Germany had begun manufacturing expanded polystyrene discs 2
and 3 meters in diameter for use in wastewater treatment plants. The first commercial installation went into operation in
1960, and soon thereafter the process began to attract considerable interest through Europe. During the early 1960's, the
research division of Allis Chalmers Corporation also investigated the use of rotating discs in various chemical processing
applications. Their disc was called a two-phase contactor (TPC), and was tested for applications of gas absorption and stripping,
liquid-liquid extraction, liquid-liquid heat transfer, and other mass and energy transfer applications. Eventually, the device
was considered for oxygen transfer. In the summer of 1965, three-foot diameter metal discs were evaluated at the Jones Island
treatment plant in Milwaukee, Wisconsin. These units were initially employed for oxygen transfer in an extended aeration
process, and then tested without sludge recycle and with an attached biomass (i.e. as a biological contactor). [In retrospect,
the Jones Island site was an ironic location, as it represent the original application of activated sludge on a large
commercial basis.] To confirm the favorable results of these initial tests and to learn more about the treatment process,
laboratory tests were subsequently conducted using a synthetic dairy waste and 3-foot diameter aluminum discs. After
learning of the European activities, Allis-Chalmers reached a licensing agreement in 1968 with the German manufacturer
for production and sales distribution in the US. The treatment process was marketed under the trade name Bio-Disc. The
first commercial installation in the US went into operation at a small cheese factory in 1969.
In 1970, Allis-Chalmers sold its rotating biological contactor technology to Autotrol Corporation. At that time, polystyrene
discs were still not competitive with the activated sludge process, primarily due to the high capital cost of the polystyrene
discs. However, in 1972, Autotrol announced the development of new rotating contactor media constructed from corrugated sheets
of polyethylene. Until then, the RBC unit consisted of a series of parallel, flat 0.5 inch thick expanded polystyrene sheets,
each separated by a 0.75 inch space. The new arrangement used 1/16 inch thick polyethylene sheets with a 1.2 inch space. At
much the same time (i.e. early 1950's) that the West German researchers began exploring plastic RBC's, American investigators
at Dow Chemical Company were initiating their experiments with the production and use at plastic packing media. Two initial
plastic units were devised at Dow including a modified "berl-saddle" (trademarked as Dowpac FN-90) and bundled arrays
of nested, corrugated sheets (trademarked as Dowpac HCS). Dow subsequently reassigned the Dowpac term, substituting
it with "Surfpac". Pilot-scale tests were conducted on both Dow packing materials using various types of industrial wastes.
Both performed acceptably well, but future emphasis was given to the bundled form (i.e. Dowpac HCS) because of its
perceived cost-effectiveness and operational flexibility. This material was designed to distribute falling liquid wastes in
thin films over large surface areas to that maximum efficiency of contact with aerobic microorganisms was attained. It
provided a high percentage of void space for unimpeded draft circulation and waste flow. It provided large surface area
adherence of biological slimes. The material produced by Dow Chemical Company consisted of individual sheets of polystyrene
or Saran plastic material, corrugated in two directions, having dimensions of 3 ft. by 1.75 ft.
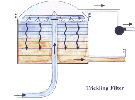
The individual sheets were typically shipped stacked in bundles, and then assembled into structurally self-supporting
modules at the point of use. In assembly, the sheets provided approximately 1 inch of free space. These modules were laid
in the filter structure in a layered grid pattern to provide good distribution of flow of liquid, and to assist in structural
stability. Void space within the assembled filter bed was about 94 percent. Assembled weight of the individual modules was
4 to 6 lb/ft3. This enables the modules to be stacked to depths of 30 to 40 feet, conserving the use of land
space. Generally operated as aerobic systems, these latter packed bed units typically receive a trickling flow which facilitates
desired tower ventilation. Submerged contact has been recently tested, though, both for aerobic and anaerobic treatment.
Tunick et. al. and Hines and Weeter have accordingly reported on the behavior of upflow anaerobic contact systems packed
with selected media materials. A down-flow submerged contact process has also been marketed by Cytox, incorporating a
parallel array of vertically stacked plastic sheets. Continuous fluid recycle within the vessel is directed towards a
splash pad above the tank which then promotes oxygen transport. Aside from this latter aeration mechanism, the Cytox system
could well be considered a resurrected Hays process. Another option for submerged media will be presented by a subsequent
author, Li and Whang. This unique approach employs a synthetic ribbon media design which is then unfurled and weighted to
maintain extension.
"Flow - Chart of the Trickling Filter Process - 2"...
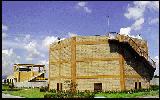
Trickling Filter - Introduction...
As aquaculture slowly shifts to more intensive farming methods, the use of biofiltration becomes more common. Broadly
stated, the purpose of biofiltration is to help maintain water quality. There are many different methods of maintaining
good water quality and biofiltration is only one component of the total picture. It is, however a very important and
essential component especially for recirculating systems. Biofiltration has the ability to accomplish the following
functions ; (1) Convert ammonia to nitrites and then to nitrates and finally to nitrogen gas, (2) Remove BOD, (3) Add
oxygen, (4) Remove carbon dioxide, (5) Remove excess nitrogen and other inert gasses, (6) Remove turbidity and clarify
the water and (7) Remove various organic contaminants.
Most aquaculture biofilters are designed for the purpose of converting and removing ammonia and nitrites from the system.
All of the other process may or may not occur depending on the design and operation of the filter and the rest of the
system. There are literally dozens of different types of biofilters used for aquaculture applications. While many have
common features, some are fundamentally different from the rest. The purpose of this article is to educate the reader
about the types of packings used for fixed film biofilters. The type of biofilters under discussion are filters that employ
a non-moving surface area to provide a substrate for various bacteria to attach and grow. The substrate remains in place
while the water flows through the system. The heart of these biofilters is the packing or media used to provide the surface
area. The type of packing used strongly influences both the capital and operating costs of the biofilter.
It is important to emphasize however, that the packing merely provides surface area for bacteria to colonize. It is the
bacteria that do the actual work of the biofilter. In order for the bacteria to do their job effectively, the biofilter
and packing design must provide an even distribution of nutrients and oxygen while removing dissolved and suspended waste
products. Most biofilters utilize aerobic bacteria but it is also possible to design and operate anaerobic systems for
special purposes. The technology used for fixed film biofilters is not unique to aquaculture. While some minor application
details are different for aquaculture, the solutions to efficient and economical water quality management have been identified
developed by several other industries. The intent of this article is to acquaint the aquaculture practitioner with the pros
and cons of the various types of packings that are available for biofiltration.
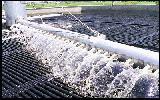
Characteristics of the "Ideal" Packing...
Since the heart of any biofilter is the packing or filter media, it is useful to describe the characteristics of the ideal
or perfect packing. In practice, some characteristics may be mutually exclusive and it may be necessary to trade off one
feature for another. The following list contains most of the pertinent features of a good biofiltration media.
1. High specific surface area : Specific surface area is the measure of how much biologically active area is
contained in a given volume. Typical units of measurement are square feet per cubic foot or square meters per cubic meter.
Specific surface areas vary widely but generally speaking, most packings will fall between 30 and 250 ft2 /
ft3 or 100 and 820 m2 / m3. Specific surface area is often referred to as the "packing
density". It is important to distinguish between total claimed surface area and surface area that is available as a substrate
for biological growth. Surface area that is contained in very fine crevices or pores may not always be available to living
organisms. As a biofilter matures, the biomass of bacteria steadily increases and the layer of bacteria that covers all
available surfaces becomes thicker. Since the organisms inside the layer can only receive food and oxygen by diffusion,
they receive less and less food and oxygen as the layer grows thicker. Generally speaking, only the outermost layer of
bacteria will be operating at peak efficiency.
If the layer of bacteria becomes thick enough, the inside of the layer may become anaerobic. When this happens, the layer
will lose adhesion to the substrate and can be sloughed off. If the dead bacteria is contained in a small crevice, it can
not be sloughed off and it will be retained within the biofilter. This can add to the overall BOD and ammonia load on the
biofilter. The total surface area available for bacterial growth is a good predictor of the capacity of the biofilter to
convert ammonia. The specific surface area is an important variable that influences the cost of the biofilter vessel and
support mechanisms. If packing A has twice as much surface area per unit volume as packing B then packing B will need a
vessel twice as large to accomplish the same task as packing A. From an economic standpoint it makes sense to use the
smallest vessel possible to accomplish a given task. Provided there are no other overriding factors, using a packing with
most surface area per unit volume will allow the vessel costs to be minimized.
2. High void fraction : Void fraction is the percentage of open space or volume in the packing. To phrase it another
way, void fraction is the space not occupied by the packing itself. Void fractions vary from 15% to 98%. High void fractions
allow free and unrestricted flow of water or air and water. A modern packing for aquaculture applications should have a void
fraction of 90% or greater.
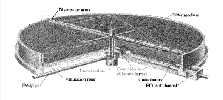
3. Large free (or clear) passage diameter : The best way to understand free passage diameter is to imagine a marble
or ball bearing being dropped through the packing. The size of the largest ball that will pass through the packing is the
free passage diameter.
4. Resistance to plugging or clogging : This parameter is very important but difficult to quantify. Plugging or
clogging of a filter can happen through mechanical trapping of particles in the same way a screen or other particulate
filter works. Plugging can also result from the growth of the biomass and bridging across the spaces within the packing.
Plugging tendency for various packings can be predicted or compared by looking at the void fraction and free passage diameter.
The free passage diameter is the more important variable. Plugging is a very serious problem for biofilters. At best it is a
continuous maintenance problem and at worst it completely destroys the ability of the filter to perform according to design.
Another cause of plugging is non uniformity in packing density. If some areas of the bed are packed denser than others, it
can lead to partial plugging. The high density areas of the filter bed can become plugged and inoperable while the rest of
the bed experiences channeling or localized high flow regions. This can lead to major decreases in filter performance.
Some biofilter systems are designed to accommodate plugging. The filter is operated until performance goes below acceptable
levels and then the bed is cleaned. This can lead to cyclical water quality problems with resultant stress on the fish.
The correct solution is to use a conservative design with a packing that is resistant to plugging for the operating life
of the filter. On the other hand it may not be possible to accommodate a packing that is open enough to insure that it will
never plug. If space is limited it may be necessary to choose a packing that has a very high specific surface area. In this
case it would be wise to use a packing that will be resistant to plugging for at least the amount of time it takes to bring
the crop to marketable size. The packing should be of the type that can be easily removed, cleaned and replaced with a minimum
of effort and labor. Another option is to have a packing that can be removed in sections. A small part of the packing can be
removed and replaced with a spare section while the plugged section is cleaned. If only a small section of the overall system
is removed, the disruptive effect on the whole system will be small. A removable packing is also convenient if one desires
to clean and sterilize the system between crops.
5. Inert material of construction : Wood, paper or other biologically degradable materials are not suitable for
biological filters. Similarly, metals such as steel, aluminum or copper are not usable because they corrode and will
inhibit biological growth. Virtually all commercial available biofiltration packings are non-corrosive, resistant to rot
or decay and generally impervious to chemical attack. However, some plastic packings are susceptible to attack from ultraviolet
radiation. Unprotected plastics that are exposed to sunlight rapidly become brittle. This phenomenon is familiar to anyone
who has left a milk jug outside for a couple months. This problem is entirely preventable through the use of UV inhibitors
that can be incorporated into the plastic. UV protection should be incorporated in any plastic biofiltration packing.
6. Low cost per unit surface area : As we noted above, a biofilter is nothing more than a given amount of surface area
that provides space for bacteria to grow. All things being equal, it makes sense to use the packing with the lowest cost per
unit surface area.
7. Good mechanical strength : One of the features of better biofiltration packings is good mechanical strength. In a
large filter, it is very desirable that the media be able to safely support the weight of one or more workers. Aside from
supporting maintenance traffic, good mechanical strength means better dimensional stability, reduced vessel support requirements
and longer life.
8. Light weight : In addition to freight costs, the weight of a packing can affect costs for other parts of the
system. Heavier packings typically require stronger and more expensive supports and vessels. If the packing or the whole
biofilter must be moved it helps if the media is light weight.
9. Flexible in overall shape : Since biofilter vessels come in all shapes and sizes, the packing should fit into any
shape vessel.
10. Ease of maintenance : A good packing should have little or no maintenance requirements. If maintenance is required
due to plugging or the need to sterilize the system between crops, the packing should be easily moved with a minimum of labor
and specialized equipment. The ability to quickly and easily clean the packing can be important.
11. Low energy consumption : While biofilters do not consume energy directly, their overall design determines the
pump head required to move water through them. Keeping the bacteria supplied with oxygen also requires energy. As biofilters
become more sophisticated and the aquaculture industry becomes more competitive, energy costs will be a major factor in overall
profitability. The biofilter that gets the job done with a minimum of labor and energy consumption will eventually become the
industry standard.
12. Light Attenuation : Nitrifying bacteria are sensitive to light. The packing should be opaque and the shape
should prevent light from penetrating into the interior of the packing.
The "ideal" packing provides the low cost solution to our biofiltration needs because it : ...
(a) Gives use the most surface area for the lowest price, (b) Gives us the lowest cost vessel because of high specific
surface area (high packing density), low weight, high mechanical strength and the ability to conform to any vessel shape,
(c) Keeps maintenance costs low due to resistance to plugging and (d) Keeps pumping and other energy costs low due to
flexibility of design.
Types of Packings...
1. Rock and Gravel : Various sizes of gravel and rocks have been used since the nineteenth century in biofilters
for various applications. They can be used in both submerged filters and trickling filters. They are still used for a
variety of applications including aquariums, aquaculture and municipal sewage treatment plants. Earthen materials are
readily available, inexpensive and can have relatively high specific surface areas. Rocks and gravel are typically very
inert and durable with excellent mechanical strength. The main disadvantage to gravel type filters is their very low void
fraction. As a natural consequence of the low void fraction, these types of filters tend to plug rapidly. In order to avoid
plugging, the amount of space between the pieces of gravel must be relatively large. In general, the free passage diameter
is directly related to gravel size. Unfortunately, the specific surface area is inversely related to gravel size. If we use
a size of gravel with openings large enough to avoid plugging, the specific surface area would be too low. With low specific
surface areas, the size of the tank required to hold the packing becomes too large.
There have been numerous attempts to overcome the drawbacks of gravel packed filters. One method is to use a substrate that
increases the surface area available without changing the overall size of the piece of gravel. This is one of the concepts
behind pumice rock, activated charcoal and micro porous ceramic materials. The claimed surface area for these material is
often very high. The problem lies with the long term operation of these types of packings. Typically, the bacteria growing
on the outer surface of the packing will prevent sufficient nutrients and oxygen from diffusing into the inner pores of the
material. While these packings have large amounts of surface area, only a small fraction of the surface area is usable for
the aerobic bacteria. Another major drawback of gravel is weight. Vessels and under drain systems must be strong enough to
support the gravel. Also, gravel is a relatively permanent filter. Once installed in a given location it is very difficult
to move. In general, the high maintenance costs and high capital costs of the vessels for gravel biofilters makes them
unsuitable for modern commercial aquaculture.
2. Fiber Mesh Pads : Various types of mesh pads are in use today as biofilters. These pads use thin fibers similar
to air conditioning filters but are formed into heavier and thicker pads. They can act as both a physical filter and a
biological filter. They are light in weight and have more surface area per unit volume than any other type of packing.
Unfortunately, fiber mesh pads suffer from the same major drawback as gravel filters. They have very small free passage
diameters and they tend to rapidly plug and lose effectiveness under most circumstances. This tendency to plug is further
complicated by the difficulty of cleaning and regenerating the pads. Typically, fiber mesh pads require a large amount of
labor to be cleaned. Another drawback to the fiber mesh type pad is the difficulty of installing the large quantities of pad
needed for a production system. The pads need extensive supports to keep them oriented in the water flow correctly. Typically,
there are very specific requirements on how mesh pads can be used.
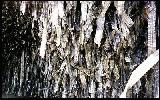
3. Brillo Pads : A packing type similar to the mesh pad is the "ribbon bundle" or "brillo pad" type packing. These
packings are light in weight and offer relatively large amounts of surface area at a low cost. While the ribbons are not
as closely spaced as the fibers in a fiber mesh pad, they still suffer from some of the same drawbacks as the mesh pads.
One of the notable drawbacks to brillo pads is their very poor mechanical strength. It is not possible to stack these
packings without compressing the bottom layers. As the bottom layers are compressed, they restrict the flow and become
easily plugged. Both "brillo pad" and mesh pads have been successful in small aquarium applications but scaling them up to
aquaculture production applications is difficult and uneconomical.
4. Random or Dumped Packings : These packings have been imported and adapted from packings used in the chemical industry.
There are literally dozens of different types of injection molded plastic shapes that are available in a wide variety of
specific surface areas. These packings are "randomly dumped" into vessels, hence the name. Typically, these packings have
a good void fraction and relatively high resistance to plugging compared to mesh pads or gravel beds. Since each piece of
packing is small, random dumped packings readily conform to any shape tank or vessel. Here are a couple typical types of
injection molded packings. Random packings must be installed over a grid or screen type support. They must be contained
because they have no intrinsic structural strength. In general, random packings have poor mechanical strength. One cannot
walk on top of random dumped packings without crushing or compacting the filter bed. Although random packings are relatively
light weight they are difficult to remove from a large vessel once they are installed. This is because the packings must be
scooped or shoveled out of the vessel. Any cleaning that is required must usually be done in place. Another disadvantage
of random packings is that their installation can be tricky. If the bed is not installed carefully, wide variances can result
in the density of the packing throughout the bed. In addition, a bed of random packings will tend to settle and compact over
time.
Another disadvantage of both gravel filters and random packings is the inability of the operator to determine what is happening
in the interior of the biofilter bed. It is very difficult to shift enough material to see what is happening throughout the bed.
The visible top part of the bed may be operating normally while the bottom of the bed is plugged and not operating correctly.
Random packings are available in stainless steel, ceramic, porcelain and various engineering thermoplastics. Most packings for
aquaculture are injection molded from PP (polypropylene) or HDPE (high density polyethylene). PP and HDPE are excellent polymers
with high heat resistance and excellent chemical resistance. Unfortunately, many PP and HDPE compounds used to mold packings do
not incorporate sufficient ultraviolet inhibitors to protect the packings from direct sunlight. While random dumped packings are
relatively modern biofilter packings, one of their major drawbacks is cost. Injection molding is an expensive way to create
surface area. Dumped packings are best used in small systems where their high cost is not a factor. They are easy to use in
small cylindrical vessels where they can fill the vessel with no special cutting or waste of material.
5. Structured Packings : Structured packings are widely used for many applications other than aquaculture biofilters.
They have virtually all of the characteristics that one looks for in the "ideal" packing. Structured packings have been used
in biofilter applications for over 25 years. In the municipal and industrial wastewater treatment fields, they are the packing
of choice. Structured packings are typically constructed of vacuum formed sheets of PVC (polyvinyl chloride). This method of
construction allows structured packings to be produced for a much lower cost per unit surface area than injection molded packings.
PVC is a relatively low cost resin with much better mechanical properties than PP or HDPE. Continuos vacuum forming is a high speed
automated process that can efficiently produce large amounts of material.
The sheets of PVC are welded or glued together to form rectangular blocks. Some packings have internal "tubes" that only
allow flow along one axis of the block. Other types of structured packings known as cross corrugated packings allow flow
along 2 axis of the block. Most structured packings used in aquaculture are of the cross corrugated type. Structured packings
come in a wide range of specific surface areas (SSA) or densities. The density is primarily controlled by the sheet spacing.
The highest practical density for aquaculture applications is about 120 ft2 / ft3 which is a sheet spacing
of about 1/4 in. The lowest specific surface area typically used for aquaculture is 48 ft2 / ft3 with a
sheet spacing of 3/4 in. The void fraction changes very little with sheet spacing. The highest density structured packing
has a void fraction of about 95% while low SSA packings are usually about 98% void fraction. For both random packings and
structured packings, void fraction is usually not a good predictor of plugging potential. It is more important to look at
free passage diameter.
One of the big advantages of structured packings is their great mechanical strength combined with light weight. An intermediate
packing with a SSA of 68 ft2 / ft3 will weigh about 2.5 lbs / ft3. However, it will have a
crush strength of over 2,000 lbs / ft2 of plan area. Unlike any other type of packing, structured packings can
span distances of up to 10 ft. between supports when used in a trickling filter. It is more common however to support them
on beams that are 2 to 3 ft on center. Another advantage to structured packings is that they can be used without any containment
vessel in a trickling filter design. Blocks of packing can be stacked in layers over a sump and water merely distributed over
the top. Another important advantage of the structured packings is their ease of installation and removal. Typical block sizes
are 12" x 12" x lengths up to 10'. A clean, 10 ft3 block with 680 ft2 of surface area will only weigh about
25 lbs. 10 ft3 of gravel with a similar surface area would weigh over 1000 lbs. While it is beyond the scope of this
article to discuss overall biofilter design, structured packings allow the design of filters that operate with the lowest energy
costs in terms of water pumping head and aeration compressor pressures.
"Comparison of Different Filling Media"...
Note : 1 = Worst, 5 = Best, A = Acceptable
Click here for "Trickling Filter Ecology"...
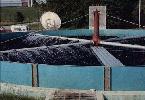
Brief Summary of the Trickling Filter...
General : Trickling filter wastewater treatment systems were once used primarily for secondary biological treatment.
Since typical effluent characteristics do not meet today's strict effluent limitations, many systems have concerted to
activated sludge. Attached growth systems still have application today when coupled with a suspended growth option.
Advantages of TF Systems : (a) simplicity of operation, (b) resistance to shock loads, (c) low sludge yield and (d)
low power requirements.
Disadvantages of TF Systems : (a) relatively low BOD removal (85%), (b) high suspended solids in the effluent (20 -
30 mg/L) and (c) little operational control.
Standard Rate and High Rate Trickling Filter : Classification of trickling filters is usually based on organic and
hydraulic loadings. Standard rate filters see a hydraulic loading of 25 - 100 gpd/ft2 and an organic loading
of 15 - 30 lbs BOD/day/1,000 ft3. Loading greater than this will put the filter into the high rate category.
Generally the higher the loading the lower the treatment (lower BOD removal). The higher the organic loading the faster the
biomass growth to a point. Nitrification usually occurs in the standard rate system.
Synthetic Media : Synthetic media in a trickling filter system results in a greater surface area available for
biological growth per cubic foot of filter volume. Because of the low weight of synthetic media, filters can be built 40
ft and higher. The result is the ability to handle greater loadings.
High Void Ratio : Void ratio refers to the physical openings in the media for water and solids to pass. A higher
void ratio allows for a greater hydraulic loading and makes the media less susceptible to plugging.
Oxygen Transfer and Detention Time : The design of synthetic media (especially crossflow) provides for greater
turbulence at the surface of the media. This greater turbulence promotes oxygen transfer. The greater the surface are per
cubic foot of media, the longer it takes for the water to "trickle" through the filter. Synthetic media with 25
- 75 ft2/ft3 provide long detention times.
Objectives of Trickling Filter Recirculation : (a) reduce strength of filter influent, (b) maintain constant wetting
rate, (c) force sloughing to occur, increase shear forces, (d) dilute toxic wastes, (e) reseed the filter and (f) increase
air flow.
Series and Parallel Flow : Parallel flow of a two-stage trickling filter system provides the greatest surface are
in the first step of treatment. Parallel flow for high hydraulic and/or organic loadings. Series flow buys more treatment
time. Shift to series for nitrification.
"Trickling Filter & Activated Sludge Process - 1"...
"Trickling Filter & Activated Sludge Process - 2"...
Nitrification in Trickling Filters : Nitrification occurs under the same environmental conditions as activated
sludge treatment systems. Low hydraulic loadings (standard rate), warm temperatures and long detention times (series flow
or synthetic media) promote nitrification. In trickling filter systems, the SBOD must be less than 20 mg/L for nitrification
to occur.
Phosphorus Removal : Some of the soluble phosphorus is removed when the BOD is removed by the biomass. Additional
phosphorus removal would have to take place in a separate tank. Either chemical precipitation or a suspended growth system
with an anaerobic tank would be needed.
SBOD : Soluble BOD is usually the test of choice for operational control of any attached growth treatment system.
To get a true measure of the BOD removal, the particulate material (sloughed biomass) must be removed from the sample. SBOD
measures the dissolved organics that need to be removed by the biomass.
Combination Systems : Combination systems such as TF/SC, TF/AS, and filtration systems are used to clean up the
effluent from the attached growth system. This takes advantage of the trickling filter's capability but still provides
final effluent to meet a 10/10 effluent permit.