Sanitary Sewer...
Description...
A. General...
This work consists of furnishing and installing sanitary sewer mains, manholes, service lines, and appurtenances. This includes all equipment, tools, materials, labor, and other incidentals to provide sewer mains and service lines complete
and ready for use. The work includes, but is not limited to, all necessary excavation, backfilling, compaction, testing, clean up, and restoration.
B. Definitions...
1. Collector sewer means a sewer main to which one or more branch sewers are tributary. 2. Interceptor sewer means a sewer that receives many tributary branches and serves a large territory. 3. Sanitary sewer mains are sewer pipes of at least
eight (8) inches in diameter, which will be installed in public right-of-way or easements, will become a part of the City sewer system and will be owned, operated, and maintained by the CITY OF RAPID CITY. 4. Sanitary sewer service lines are the lines from the sewer main to within five (5) feet of the building and are owned and maintained by the owner of the property being served. 5. Private sanitary sewer collection system may consist of multiple sewer service lines and sewer collection pipes that are owned, operated, and maintained by the owner of the property being served.
C. Related Work...
Section 7 - General Conditions
Section 8 - Water Piping Systems
Section 11 - Utility Excavation and Backfill
Section 41 - Utility Trench Resurfacing
Section 56 - Concrete for Incidental Construction (Class M)
Section 90 - Traffic Control
Section 112 - Select Granular Backfill
Section 200 - Controlled Low Strength Material
D. License and Permit Requirements...
Refer to Section 11.
E. Submittals...
Submittals shall be required unless otherwise specified in the Detailed Specifications or Special Provisions. The term "Submittals" includes, but is not necessarily limited to, manufacturer's product data sheets of pipe, manholes, appurtenances, and fittings. Submittals shall be submitted for, but not limited to, the following items: Manholes, manhole frames and covers, pipe, pipe fittings and their appurtenances, and any other pertinent information concerning construction materials that the Engineer deems necessary for the review of the materials used on the project in accordance with the specifications and drawings. All submittals shall be made in accordance with Section 7. Resubmittals shall be made the same as for original submittals, with changes from the previous submittal clearly shown.
Materials...
A. Pipe...
Sanitary sewer pipe 21 inches in diameter and smaller shall be PVC unless indicated otherwise on the drawings or in the Detailed Specifications.
1. PVC pipe and fittings, 4 in. through 15 in. diameter, shall conform to the requirements of ASTM D-3034, Type PSM, SDR-35 (PS 46) minimum. PVC pipe 18 in. through 36 in. diameter shall conform to the requirements of ASTM F-679, PS 46. PVC pipe shall be manufactured in a continuous extrusion process employing a prime grade of un-plasticized PVC plastic material that meets the requirements for this product as specified in ASTM D-1784. PVC Sewer Pipe shall have a flexible elastomeric seal (O-ring or rubber sealing elastomeric gasket joint), and conform to the latest revisions of ASTM D3212. Solvent cement
joints will not be allowed for sewer pipe and fittings. Nominal laying lengths shall not be less than 12.5 feet, except shorter lengths may be used adjacent to manholes. Each length of pipe shall be marked, as a minimum, with size, SDR, "Sewer Pipe" and ASTM number.
2. Reinforced concrete pipe (RCP) and fittings, in sizes 12 in. through 108 inches in diameter, shall conform to the requirements of ASTM C-76 and shall be manufactured using Type II cement. The pipe and fittings shall be manufactured at a precast facility that is certified by the American Concrete Pipe Association and is approved for supplying products to the South Dakota Department of Transportation. Class of pipe shall be as shown on the Drawings or specified in the Detailed Specifications. Joints for RCP pipe shall meet the requirements of ASTM C-361 for concrete joints and confined rubber
O-ring gaskets.
3. Ductile iron pipe shall be as specified for pressure pipe in Section 8, Water Mains. All ductile iron pipe shall be furnished with a ceramic Protectal 401 lining or equal. The lining shall have a minimum thickness of 40 mils. All ductile iron pipes shall be installed with polyethylene encasement in accordance with AWWA C105 unless otherwise directed by the Engineer. Ductile iron pipe thickness class shall be as specified on the drawings and/or in the specifications.
4. Sanitary Sewer Force Main: a. Polyvinyl Chloride (PVC) Pipe - All pipe and fittings shall conform insofar as appropriate, to Section 8 Water Mains and to AWWA Standards C-900, C-905, and C-605. b. Ductile Iron Pipe (DIP) - All pipe and fittings shall conform insofar as appropriate, to Section 8 Water Mains and to AWWA Standards C-150, C600, and C-151. All ductile
iron pipe shall be furnished with a fusion-bonded polyethylene lining in accordance with ANSI/ASTM D1248. The lining shall have a minimum thickness of 60 mils. All ductile iron pipes shall be installed with polyethylene encasement in accordance with AWWA C105 unless otherwise directed by the Engineer. Ductile iron pipe thickness class shall be as specified on the drawings and/or in the specifications.
5. Sewer Service Pipe and Fittings - All pipe and fittings shall conform to the requirements of ASTM D-3034, SDR-35 (PS 46).
B. Miscellaneous Pipe Materials...
1. Pipe Couplings: PVC repair couplings or clamp style couplings shall be used on all pipe equal to and greater than 8
inches in diameter. Clamp style couplings shall be “Power Seal Model 3541” as manufactured by Power Seal, Fernco-Strong
back RC series repair couplings, or approved equal Nonshear reinforced banded style couplings shall be as manufactured by
DFW Plastics, Inc.; adjustable repair coupling with 300 series stainless steel shear ring as manufactured by Mission Rubber Company, Inc., PVC repair couplings, or approved equal shall be used on all pipe 6 inches in diameter or less. All couplings shall bear the manufacturer’s identifying mark and size. Reducing couplings will not be allowed. Pipe couplings are incidental to the pipe or shall be considered as a subsidiary component to the bid item for connection to the sewer main.
2. Caps/Plugs: PVC caps and plugs shall be the gasketed or solvent welded sewer fitting type. Caps and plugs for clay pipe shall be made using non-shrink grout placed continuously for a one-foot or one pipe diameter, which ever is greater, into
the pipe.
3. Sewer Main Insulation: Type IV Styrofoam Brand—“Square Edge” or “Score Edge” as manufactured by Dow Chemical Company
or approved equal shall be used for insulating sewer pipes where required. The total thickness and dimensions shall be specified on the drawings or in the Specifications. The minimum insulation thickness however shall not be less than 2
inches. Approved equal products from other manufacturers shall be Extruded-Polystyrene Board Insulation formed from polystyrene base resin by an extrusion process using hydrochloro-fluorocarbons as blowing agent to comply with ASTM C578, Type IV, with 1.60 lb./cu. Ft. minimum density and a compressive strength of 25 lb./ sq. in as specified in ASTM D1622
and ASTM D1621 respectively. The maximum thermal conductivity of the insulation shall conform to ASTM C518, C177, and
C578. The maximum water absorption percentage by volume shall be 1% in accordance with ASTM D2842. The range of water
vapor permeance shall be 0.4 to 1.0 perm in accordance with ASTM E96.
4. Polyethylene Encasement: Polyethylene Encasement (poly-wrap) shall meet AWWA C-105. For ductile iron pipe, the
encasement shall be 8-mil thickness, seamless tube, black ASTM D-1248, Type 1, Class C, Grade G-1. Joint tape for
encasement shall be 3M Scotch wrap 50, or equal. For fittings, the encasement shall be 8-mil thickness sheet
polyethylene meeting AWWA C-105. Off the shelf, polyethylene sheeting typically does not meet AWWA C-105. Joint
tape for encasement shall be 3M Scotch wrap 50, or equal.
C. Concrete Manholes...
1. General : Manholes shall be pre-cast reinforced concrete, manufactured using Type II cement, and shall have diameters
as shown on the Drawings. The manholes shall be manufactured at a precast facility that is certified by the American
Concrete Pipe Association and is approved for supplying products to the South Dakota Department of Transportation.
Manholes 48 inches in diameter shall meet the current requirements of ASTM-C-478. Manholes with diameters larger than 48 inches shall have steel reinforcing that meets the requirements of ASTM C-76, Class 2. Upon request from the Engineer, the Contractor and/or supplier shall supply a test report from an independent testing laboratory showing compliance with this specification.
2. Manhole bases shall be integral (monolithic) with the barrel section and shall be cast to a minimum thickness of six
(6) inches. When specified in the Detailed Specifications or shown on the Drawings, cast-in-place bases may be installed
and shall have a minimum thickness of 8 inches with concrete conforming to the requirements of Class M6, Section 56. Cast-in-place bases shall incorporate a water stop between the base slab and manhole barrel. The water stop material
shall be American Colloid “Water stop – RX”, 1 in. x 3 / 4 in. Size or equal.
3. Cone sections shall be eccentric type with 27 in. opening.
4. Flat cover slabs, when shown on the Drawings or specified in the Detailed Specifications, shall be designed for H-20 loading and shall have an offset 27 in. diameter opening.
5. O-ring gasketed joints, joints between manhole sections shall be O-ring gasketed joints conforming to the requirements
of ASTM C443.
6. Manhole joint sealant shall be pre-molded flexible butyl joint sealant conforming to Federal Spec. SS-S-210A and AASHTO M-198B and shall be ConSeal CS-302, or equal.
7. Manhole steps shall not be provided unless specifically noted on the drawings or specified in the Detailed
Specifications. When steps are required they shall be plastic coated or rubber coated and conform to the requirements
listed in ASTM C478 with an overall width of 12 inches and equally spaced vertically, however such vertical spacing shall
not exceed 16 inches.
8. Lifting holes penetrating through the manhole sidewalls are not permitted.
9. If an interior lift system is used, inserts shall be grouted flush with the interior of the manhole after placement. Manhole lift system shall be “PressSeal Gasket Corp.”, or equal and grout shall be a non-shrink grout.
10. Non-Shrink Grout shall conform to the following requirements: Premixed compound consisting of no-metallic aggregate, cement, water reducing and plasticizing agents; capable of developing minimum compressive strength of 2,400 psi in 48
hours and 7,000 psi in 28 days.
11. Manhole Inverts shall be U-shaped with a channel depth equal to the diameter of the pipe exiting the manhole and with
the channel sides vertical or slightly laid back at a slope not to exceed (1/10, horz./vert.) above the spring line, Refer
to Standard Details. Manhole inverts shall be Class M-6 concrete per Standard Specification Section 56. a. New manhole benches and inverts shall be precast with the manhole. The same manufacturer that produces the precast monolithic base
shall also produce the precast manhole inverts. Precast manhole inverts shall be per SD Concrete Product’s Rapid City
Plant or equal. Hand formed inverts will not be allowed for new manholes unless pre-approved by the Engineer. The
manhole invert shall have a smooth steel trowel finish and the bench shall have a broom finish. b. Existing manhole
benches and inverts may be reconstructed with hand formed inverts and benches provided the other components of the specification are still met. The manhole invert shall have a smooth steel trowel finish and the bench shall have a broom finish.
12. Pipe Connections to new Manholes shall be constructed with a compression-type flexible connector cast into the manhole wall, as manufactured by A-Lok Products, Inc., or equal. Alternatively shall be constructed with a boot-type flexible connector consisting of a rubber gasket or boot, metal expansion ring, and double metal take-up clamps, as manufactured by Press Seal Gasket Corporation, or equal. A stainless steel “power sleeve” shall be supplied for connecting the boot to the manhole. The boots shall be type PSX as manufactured by Press Seal Gasket Corporation or approved equal. Rubber boots and gasket material shall meet or exceed ASTM C-923.
13. Pipe Connections to Existing Manholes shall be made by coring the existing manhole and installing a boot-type flexible connector consisting of a rubber gasket or boot, metal expansion ring and double metal take-up clamps, as manufactured by Press Seal Gasket Corporation, or equal. A stainless steel “power sleeve” shall be supplied for connecting the boot to the manhole. The boots shall be type PSX as manufactured by Press Seal Gasket Corporation or approved equal. Rubber boots and gasket material shall meet or exceed ASTM C-923. Alternatively, with Engineer’s approval the pipe connection may be made
by cutting a hole into the manhole wall, fitting a water stop gasket over the pipe, placing a bentonite based water stop
on the concrete manhole barrel (full circumference around the breakout), inserting the pipe, and grouting it into place.
The bentonite based water stop shall be American Colloid “Waterstop – RX”, 1 in. x 3 / 4 in. Size or equal. Refer to the specification section regarding “Construction Requirements” and the standard detail for further guidance with this installation.
14. Water stop gaskets for use in “Pipe Connections to Existing Manholes” shall be made of elastomeric PVC and be corrosion proof. For pipe connections 4 in. – 12 inches in diameter the water stop gasket shall be a “Concrete Manhole Adapter” as manufactured by Fernco, or equal. For pipe connections larger than 12 inches in diameter, the water stop gasket shall be a “Large Diameter Waterstops” as manufactured by Fernco, or equal.
15. Coating for Concrete Manholes and Lift Station Wet Wells: When indicated on the drawings or specifications a corrosion resistant interior grout liner shall be provided on manholes or lift station wet wells. The liner shall be “Kretekote 200”
as manufactured by Kretekote LLC, or equal. This product is specifically formulated for coating the interior of concrete manholes or wet wells for corrosion protection. Coating color shall be the Earthcoat gray for manholes and Earthcoat white for wet wells unless otherwise indicated on the drawings or detailed specifications.
D. Manhole Frames and Covers...
1. All frame and covers shall be constructed with gray iron having a tensile strength of not less than 35,000 pounds per square inch. The frame and covers shall conform to ASTM A48, Class 35B. The castings shall be heavy-duty type, designed
for H20 loading conditions. The castings shall be free from cracks, blowholes, porosity, shrinkage distortion
or other imperfections. They shall be true to pattern and free from warpage. The frame and covers shall fit together in a satisfactory manner. Machined bearing surfaces shall be provided to prevent rocking and rattling. Manhole frames and covers shall be as follows. a. Standard frames and covers shall be Neenah 1733, Deeter 1260, Municipal Castings (MC) 301 or equal unless otherwise indicated on the drawings or specifications. b. Extra deep frames and covers shall be installed where manholes are located in PCC pavement thicker than 7 inches. A casting height corresponding to or exceeding the PCC pavement thickness (up to 10 in.) shall be selected. Extra deep frames and covers shall be Neenah 1733-A; 1733-B; or 1733-C, Deeter 1261, or equal. c. Bolt down frames and covers shall be installed as specified but will mainly be used in areas, which are without hard surfacing and are subject to flooding. Bolt down frames and covers shall be Neenah R1916F, Deeter 1247, or equal.
2. All covers shall be supplied with concealed pick holes as specified in the standard plates. All covers shall be marked with the letter "S" formed in the center of the cover. The cover style shall be a Neenah Type “k” Lid, indented top design
or equal. All covers shall be supplied with self-sealing type “T” or O-Ring gaskets as manufactured by Neenah Foundry Company, machined groove continuous O-Ring gasket as manufactured by Deeter Foundry Inc., or approved equal. The covers
shall be delivered from the manufacturer with pre-installed glued-in gaskets. The gasket shall be installed in a machined groove and be continuous around the perimeter. The gasket material shall be oil resistant Nitrile (60 DURO) glued in the groove, and have a maximum swell of 90 percent when tested in accordance with ASTM D471 using ASTM No. 3 oil. The glue
shall be Lock-rite Black Max as manufactured by 3M Products or equal.
E. Manhole Adjusting Rings...
1. Concrete Adjusting Ring Materials: a. Masonry bricks, masonry blocks, or masonry shimming devices will be allowed for
use in adjusting manhole castings. Wood blocking or wood shimming devices greater than one inch in thickness will not be allowed. Any blocking or shimming device, when used, will not extend to the interior of the manhole. b. Adjusting rings: Concrete adjusting rings shall be in accordance with ASTM C478. The adjusting rings shall be sized to conform to the
standard manhole 27-inch cone opening, frame, and cover. c. Mortar: Mortar shall be Standard Portland Cement Type 1,
hydrated lime, and clean, sharp, well-graded sand, free from foreign materials. The minimum design compressive strength shall be no less than 4,000 psi.
2. Plastic Adjusting Ring Materials: a. Sealant: Butyl Rubber Sealant in trowelable form shall be used. EZ-STIK #3 as manufactured by Pre-seal Gasket Corporation or approved equal. The material must meet or exceed the requirements of Federal Specification TT-S-001657, ASTM C-990 and AASHTO M-198. b. Plastic Adjusting Rings: The adjusting rings shall be injection molded HDPE as manufactured by Ladtech, Inc. or approved equal. The adjusting rings shall be manufactured from polyethylene plastic as identified in ASTM D-1248 (Standard Specification for Polyethylene Plastic Molding and Extrusion Materials). Material properties shall be tested and qualified for usage in accordance with the ASTM Test Methods referenced in ASTM D-1248. The plastic adjusting rings shall be manufactured utilizing the injection molding process as defined by SPE (Society of Plastic Engineers). The adjusting rings shall be tested to assure compliance with impact and loading requirements in accordance with the AASHTO Standard Specification for Highway Bridges. The adjusting rings shall meet and exceed the static load requirements of ASSHTO highway Bridge Specification HS-25 (21,280 lbs). The rings must withstand 1,000,000 plus full load cycles of 10 seconds or less duration. The rings must perform without failure to a minimum of 150 percent of these load values. The adjusting rings shall be sized to conform to the standard manhole 27-inch cone opening, frame, and cover.
3. Rubber Adjusting Ring material a. Sealant: Sealant shall be polyurethane, formulated specifically for use with
rubber adjusting rings and shall be manufactured by GNR Technologies, or approved equal. b. Rubber Adjusting Rings:
Rubber adjusting rings shall be Infra-Riser multipurpose rubber adjustment riser as manufactured by GNR Technologies,
or approved equal.
F. Manhole Internal Frame Seal...
Manhole internal frame seals shall be installed with all manholes, unless pre-approved by the Engineer to be installed without a chimney seal. Manhole internal frame seals shall be CRETEX Internal Manhole Chimney Seals as manufactured by
CRETEX Specialty Products, NPC Flexrib Seal, or approved equal. Internal frame seals shall consist of a flexible internal rubber sleeve and extension that completely covers all rings from cone to casting and stainless steel compression bands.
G. Tracer Wire System...
Tracer Wire shall be a direct bury wire that meets or exceeds the following requirements: a. Conductor: 12 AWG solid strand soft drawn copper per ASTM B-3, or B-8. The breaking pounds of the wire shall be a minimum of 124 with an O.D. of 0.154. All wire shall be spark tested at 7500 VAC. b. Insulation: Conductor shall be insulated with low density high molecular weight polyethylene insulation suitable for direct bury applications per ASTM D-1248. The minimum insulation thickness shall be 0.045. The color of the insulation shall be green with a print line saying “SEWER”. c. Splices and or Connectors: Splices and or Connectors should be capable of handling from 2 to 4 wires per connector and designated as “water-proof”. PVC adhesives or sealing compounds are not acceptable. d. Tracer Wire System Manufactures :
• Tracing Wire – Kris Tech Wire Co. Inc., Paige Electric Corporation, or equal.
• Splice Kit/Connectors -3M epoxy type compounds, fusible heat shrink tubing, 3M DBY connectors, or Snaploc LV 9000 direct bury wire connectors, or equals.
Construction Requirements...
A. Wastewater Flow Modifications...
1. Interruption of Service : The Contractor shall provide continuous, uninterrupted sanitary sewer service to all users in
and upstream of the project area.
2. Flow Handling Plan : Prior to beginning work on any manhole or sewer main requiring flow modification the Contractor
shall present a plan for handling wastewater flows to the Engineer for his approval. The plan shall describe the methods
to be used and shall identify all materials and equipment that will be required for flow handling. The Contractor's plan shall also identify a contingency plan and procedures to be implemented in the event of an equipment failure or other emergency.
3. Methods : Bypass pumping is required during construction hours and temporary connections, between existing and new sewer mains are required during non-working hours. Wastewater flows shall not be conveyed in open ditches nor in the trench excavation, and at no time shall wastewater be allowed on the ground surface, streets, gutters, storm sewers, or other places, which may constitute a health hazard. Whenever, in the opinion of the Engineer, a health hazard exists because of actions or inactions of the Contractor, the Contractor shall immediately correct the situation to the satisfaction of the Engineer. If not corrected in a timely manner, the City may cause to take any actions necessary to remove the health hazard and charge the Contractor one and a half (1 1 / 2) times the cost incurred.
4. Damages to Property : Any damages to private or public property due to backups, overflows, or surcharging resulting from work under this section shall be the responsibility of the Contractor and shall be corrected as soon as practical and at no cost to the City. If not corrected in a timely manner, the City will take the necessary action and charge the Contractor one and a half (1 1 / 2) times the cost incurred.
B. Materials Handling and Storage...
The Contractor shall be responsible for the safe handling and storage of all materials furnished by him, and shall replace, at his own expense, all such materials found defective in manufacture or damaged in transportation, handling, or storage. Pipe, manholes, castings, and accessories shall be loaded and unloaded by lifting with hoists or skidding to avoid shock or damage. Under no circumstances shall such materials be dropped. All material shall be stored in a neat and orderly manner. Pipe shall be stored, to the greatest extent possible, in unit packages or bundles and shall be handled to prevent stress
to bell joints and prevent damage to bevel ends. In addition, materials shall be handled and stored in accordance with manufactures’ recommendations.
C. Underground Obstructions...
The Contractor shall expose existing underground obstructions shown on the plans or located in the field and shall
determine their elevations far enough in advance of pipe laying that the proposed sewer main can be adjusted. Wherever obstructions not shown on the plans are encountered during the progress of the work and interfere with the proposed horizontal or vertical alignment of the sewer, the contractor shall notify the Engineer so that the Engineer may modify
the plans and order a deviation in the line and/or grade, or may arrange for the removal or relocation of the
obstruction(s). The Contractor shall not deviate from plan line or grade without the Engineer's approval.
D. Sewer Main and Water Main Crossings...
1. Vertical Separation : Sewer mains may cross below water mains with a minimum vertical distance of eighteen (18) inches between the invert of the water main and the top of the sewer. In these cases, where the water main is above the sewer and there is at least 18” of separation, then at the crossings one full length of sewer pipe shall be centered below the water.
A sewer main may cross below a water main with a vertical separation of less than eighteen (18) inches or above the water main if either the water or sewer main is encased in PVC, ductile iron, or six (6) inches of concrete for at least ten (10) feet each side of the crossing. If PVC or ductile iron is utilized as encasement material, the ends shall be sealed with
six (6) inches of concrete. The 10 ft. each side shall be measured from the outside wall of the water to the end of the encasement and is not measured from the centerline of the water main.
2. Horizontal Separation : Sewer mains shall be constructed with minimum 10 ft. of horizontal separation from any existing water main or proposed water main. The 10 ft. horizontal separation shall be the clear distance (water pipe sidewall to
sewer pipe sidewall) and not the centerline distance between the utilities. The following installation requires Engineer’s approval and is appropriate for installations where the 10 ft. minimum separation physically is not possible. A sewer main may be constructed closer than 10 ft. to a water main if it is laid in a separate trench or it is laid in the same trench
and the water main is located on the opposite side on a bench of undisturbed earth. In both cases, the elevation of the
crown of the sewer has to be at least 18 in. below the invert of the water main. The sewer main shall be constructed of
water main pipe (pressure class pipe) meeting the requirements of Section 8.2 or equal and pressure tested for water tightness in accordance with AWWA standards for leakage testing. As an alternative to constructing the sewer with water
main pipe (pressure class pipe) and pressure testing the sewer, it is permissible to either encase the water or sewer
main with 6 inches of concrete or to encase either the water or sewer within a PVC or cast iron casing.
E. Protection of Existing Sewers...
The Contractor shall take necessary precautions to ensure that dirt, debris, and foreign materials do not enter existing sewers. Where new sewer mains are to be extended from and connected to existing sewers, the Contractor shall give, the
City Utility Maintenance Division 24 hour notice in order that City personnel may install a temporary plug at the terminal manhole on the existing sewer. Said plug shall remain in place until all work on the new sewer has been completed and the Engineer is satisfied that the new sewer is free of dirt, debris, and foreign materials. Any costs incurred by the City
due to the Contractor allowing dirt, debris, foreign materials, trench water, or storm water to enter an existing sewer
shall be charged to the Contractor at one and a half (1 1 / 2) times the cost incurred.
F. Installation of Pipe...
1. Trenching, Bedding, and Backfill shall comply with the requirements of Section 11, Utility Excavation and Backfill.
Trench dewatering discharges shall not be allowed to enter the sanitary sewer collection system at any time.
2. Alignment and Grade: Pipe shall be laid true to the line and grade established on the Drawings. Pipe shall be installed within 1/2 inch of the specified alignment and within 1/4 inch of the specified grade. These tolerances apply to any point along the entire pipe length. The Contractor shall carry line and grade into the trench by means of an approved laser beam system and by surveying level instrument. At no time shall the Contractor change the grade without approval from the Engineer. If an underground obstruction is encountered at the assigned grade, the Contractor shall notify the Engineer and wait until the revised grade for the sewer has been determined, if necessary. As a secondary check to the laser beam device, the Contractor shall check the grade from a surveyed grade stake to the pipe invert a minimum of every 100 feet using a surveying level instrument. The Contractor shall record all grade checks and produce the grade stake record if requested by the Engineer.
3. Cleaning shall be done as necessary so that the interior of all sewer pipe is free from all dirt, cement, or other
foreign material before installation. Contact surfaces shall be wire brushed immediately prior to jointing.
4. Pipe Cutting shall be done without damage to the pipe with saw or abrasive wheel and shall be smooth, straight, and at right angles to the pipe axis. Ends of pipe shall be dressed and beveled to remove roughness and sharp corners.
5. Laying and Joining of pipes shall be in accordance with the pipe manufacturer's instructions, unless specifically
required otherwise by these Specifications. c. Each pipe length shall be inspected for defects prior to being lowered
into the trench. All pipes shall be carefully lowered into the trench piece by piece by means of pipe slings to prevent damage to the pipe and/or coating. b. Sewer pipe shall not be installed in frozen ground or in water, and no water will
be allowed to run into or through the pipe. c. Pipe shall be carefully installed to line and grade in accordance with
line and grade stakes so that the finished sewer will present a uniform grade. Any noticeable variations from true
alignment or grade will be cause for rejection of the work. d. All pipe shall be installed upgrade with spigot ends
pointing in the direction of flow. The bottom of the trench shall be freed of all rocks and stones and shall be hand
shaped and bedded and the pipe shall be in firm contact with the bedding material for its entire length. e. At every
bell and spigot pipe joint, a hole shall be dug of sufficient size so that the weight of the pipe will rest on the
barrel of the pipe and not on the bells, and the bell hole shall not be compacted. All pipe must be properly fitted
together. f. During the course of construction, a suitable stopper shall be kept in the end of the pipe to prevent
any dirt and or water from entering during the progress of the work at all times. Any dirt, loose material or cement
mortar, which may accumulate in the pipe, shall be removed as the work progresses. g. Standard length pipe shall be
utilized for all installations. Shorter lengths will only be allowed for use at manhole terminations. A full standard
length pipe shall be used upstream of all manholes. h. Joint surfaces shall be cleaned and lubricated immediately before completing the joint. Lubricant other than that furnished with the pipe shall not be acceptable. Pipe jointing shall be accomplished in a relatively dry trench condition. i. At manhole connections the Contractor shall take extra care to
ensure the pipe is properly bedded to prevent shifting, settlement, deflection or other failures. j. Joints in PVC
Sanitary Sewer Pipe: 1) All PVC Sanitary Sewer Pipe shall be jointed utilizing elastomeric gaskets as specified. All pipe, fittings and joints shall be installed in full compliance with the recommended practices of the pipe manufacturer and as specified in the latest revision of ASTM D2321. 2) The joint surfaces (external and internal) shall be wiped free of all foreign materials, and the spigot end shall be centered on grade into the bell end and the joint shall be properly seated
in accordance with the manufacturer’s recommendations. 3) Any pipe that is field cut shall have a square end with beveled edge equal to a factory cut and all field repairs shall be performed per manufacturer’s recommendations. k. Joints in
Ductile Iron Pipe (DIP) 1) All Ductile Iron Pipe shall be jointed utilizing a push-on type joint in accordance with the specifications. All pipe, fittings and joints shall be installed in full compliance with the recommended practices of the pipe manufacturer and the latest revision of the ANSI/AWWA C600 standard. 2) When making joints, the gasket and gasket seal inside the socket shall be wiped clean before the gasket is inserted. A film on lubricant shall be applied to the gasket and the outside of the spigot end of the pipe. The spigot shall then be positioned inside the socket and pushed home. Lubricant other than that furnished with the pipe shall not be acceptable.
6. Protection of the Work: At the end of each day's work, or when sewer pipe is not being laid, the Contractor shall
protect the end of the pipe by a close-fitting stopper to prevent soil, water, or other matter from entering the pipe,
and shall take adequate precautions to overcome possible uplift. The elevation of the last pipe laid the previous workday shall be checked the next day before work resumes.
7. Connections between new sewer main pipe and existing sewer mains shall be accomplished with a Fernco-Strong back RC
series repair coupling, Power Seal coupling, or a PVC repair coupling. When using the Power seal or Fernco type intallation, the Contractor shall encase the coupling in six inches of concrete for one foot either side of the coupling.
PVC couplings do not require concrete encasement.
8. Minimum Cover depth from the top of pipe to finished grade shall not be less than 4.0 feet. Refer to the Insulation Standard Detail in cases where minimum cover cannot be provided. Insulation shall only be used in those rare instances
where the pipe’s grade cannot be adjusted or the finished surfacing grade be adjusted to maintain the minimum cover. Insulation may also be required in instances where adequate separation between culverts or storm sewers cannot be
achieved.
9. Dewatering shall be accomplished per Section 11 Utility Excavation and Backfill.
G. Installation of Manholes...
1. All manhole barrel and cone sections shall be numbered and/or measured by the Contractor prior to installation to insure that each furnished manhole component is correct for that location and that the finished manhole will be to the grade specified. Placement of manholes shall be on a 4-inch (minimum thickness) leveling course of Type 1 Bedding Material. Manholes shall be set level and to the grade specified.
2. Invert Channels: a. General: Channels shall have smooth, clean surfaces and shall be semi-circular U shaped conforming
to the lower half of the adjacent pipe. Changes in size and grade of the channels shall be made gradually and evenly. In no case shall the invert width through the manhole be greater than that of the outlet pipe. Changes in direction flow and side branch connections shall be made with a full, smooth, and sweeping curve with a radius meeting the requirements per the Standard Details. Manhole inverts shall be U-shaped with a channel depth equal to the diameter of the outlet pipe and with the channel sides, above the spring line, vertical or slightly laid back at a slope not to exceed (1/10, horz./vert.), Refer to Standard Details. Manhole inverts shall be Class M-6 concrete per Standard Specification Section 56. The manhole invert shall be shaped and finished with a smooth steel trowel finish. b. Inverts for New Manholes: Bench and inverts shall be precast or formed as specified in Section 9.2 Materials. c. Inverts for Existing Manholes: Existing manhole inverts to be reconstructed shall be as specified in Section 9.2 Materials and as further described. All sewer flows shall be removed by bypass pumping or other approved methods from the manhole to be reconstructed. The existing invert and bench shall be demolished to the extent necessary to maintain a minimum new concrete invert thickness of 3 in. and side thickness of 8 in. throughout the manhole. Acceptable methods for demolishing the existing invert include the use of concrete saws, jackhammers, chisels and other hand tools. The existing concrete shall be rough and have an approved bonding agent applied to it prior to placing the new concrete. The new invert shall be constructed using a concrete mix as specified with the exception that the concrete shall be low slump. Sewer flows will not be permitted on the concrete until 4 hours after the initial set has occurred and the Engineer has inspected and approved the reconstructed invert.
3. Shelves/Benches shall be formed from the top of the channel to the manhole wall and shall slope up from the channel at a minimum rate of one (1) inch per foot and a maximum rate of three (3) inches per foot. The bench shall be constructed as specified in Section 9.2 Materials.
4. When specified/required, steps shall be inserted at least 1 in. into the manhole wall and shall be aligned straight and plumb over the outlet pipe in the manhole. Steps shall not be installed in manholes unless indicated on the drawings or in the specifications and approved by the Engineer.
5. Pipe Connections to New Manholes: Manhole connections to the sewer main shall be accomplished with a rubber boot or a gasket seal that insures a watertight seal. Ends of pipes, which enter manholes, shall be cut smooth; straight; and at
right angles to the pipe axis. The annular space between the boot or gasket and the pipe shall be grouted flush with the inside of the manhole such that a smooth, continuous channel is formed through the manhole. The annular space above the
flow channel on top of the pipe shall not be grouted. Drop manholes shall have the lower connection and 45 degree fitting, outside the manhole, totally encased in concrete, Refer to Standard Details. The interior pipe connections shall have the annular space grouted as described above.
6. Pipe Connections to Existing Manholes: a. Manhole connections shall be made by coring the existing manhole and installing a boot-type flexible connector consisting of a rubber gasket or boot, metal expansion ring and a metal take-up clamp, as manufactured by Press Seal Gasket Corporation, or equal. Rubber boots and gasket material shall meet or exceed ASTM C-923. Drop manholes shall have the lower connection and 45 degree fitting, outside the manhole, totally encased in concrete, Refer to Standard Details. The interior pipe connections shall have the annular space grouted as described for “Pipe Connections
to New Manholes”. Unless pre-approved by the Engineer, new pipe connections to existing brick manholes shall not be allowed. Brick manholes shall be replaced. b. With Engineer’s approval the Contractor may cut the necessary openings into the
existing manhole and make the connection thereto in a neat and workmanlike manner. The connections shall be made to make
the joints around the entering sewers watertight and an approved smooth channeled flow line shall be constructed as
specified for Inverts. The Contractor shall create a hole in the manhole wall using a chisel hammer or other approved
method. The hole shall have a maximum dimension of 6 inches plus the O.D. of the pipe and a minimum dimension of 3 inches plus the O.D. of the pipe. Concrete saws are discouraged for cutting the hole as they leave cuts in the existing manhole
wall and are difficult to grout shut. If a concrete saw is used, it shall be used in a manner such that there are no saw
cuts left in the existing concrete. The pipe shall be grouted into the manhole wall with non-shrink grout and a water stop gasket. The grout shall extend outside the manhole wall such that it provides a 6 in. overlap around the full circumference of the hole. The Contractor shall place a water stop on the concrete manhole barrel around (full circumference) the breakout, and grout it into place. The water stop shall be American Colloid “Waterstop – RX”, 1 in. x 3 / 4 in. size or equal. The grout shall also extend out/away from the manhole (around the pipe) for a length equal to the diameter of the pipe. Refer
to the Standard Detail. Drop manholes shall have the lower connection and 45 degree fitting totally encased in concrete. Refer to Standard Details. c. After completing the connection to the manhole, the Contractor shall test the existing manhole for water tightness as required under the Section - Manhole Tests. If the manhole does not pass the test it shall be the contractor’s responsibility to correct the deficiencies and demonstrate a passing test. The Contractor is responsible for correcting deficiencies in the manhole even if said deficiencies preexisted or resulted from activities not directly related to the connection tie-in.
7. Frames and covers: a. Grade and slope: Manhole frames and covers shall be placed at finished grade. When placed in asphalt, concrete, or gravel surfaces, frames and covers shall match both the crown slope and profile slope of the street. The cover shall be set at an elevation and slope that it is not above the pavement surface and no more than 1/4 in. below
the pavement surface at all points around the circumference of the cover. Decreasing the surfacing thickness around the manhole frame and cover, as a method of achieving the above tolerances, is not permitted. Frames and covers placed in
turfed areas shall be set from 1 - 2 inches above the finished grade. Frames shall be blocked and shimmed to correct elevations and slopes prior to placing pavement. The lid shall be adjusted to match both the cross slope of the street
and the profile of the street. Following paving, the frame shall be checked for correct placement and adjusted as
necessary. The joint between frame and adjusting ring shall then be grouted watertight with non-shrink grout. Blocks
and shims shall be placed no closer than 2 in. from the inside edge of the adjusting ring. The internal frame seal shall
be installed after the manhole frame and cover has been installed in its final position and is compete. Vertical
Adjustment of manhole frames and covers: Adjusting rings shall be installed per the Standard Details and as specified
herein, adjustments greater than those shown on the details shall be accomplished by adding additional barrel sections
rather than adjusting rings. Plastic or rubber adjusting rings may be used in lieu of concrete adjusting rings. The
plastic or rubber adjusting rings shall be installed as recommended by the manufacturer. No shims or other leveling
devices, other than leveling rings provided by the manufacturer, will be permitted with use of the plastic or rubber adjusting rings. The annular space between the adjusting rings shall be sealed using an approved butyl rubber sealant,
water stop material will not be permitted as it does not fully displace and further settlement of the frame occurs after installation. The first plastic adjusting ring on existing manholes may require leveling with concrete mortar and therefore the first plastic ring may be set in mortar. The manhole frame and adjusting rings where concrete adjusting rings are used shall be set in a full bed of mortar to the grade and slope as specified. The mortar shall be tuck pointed between rings
and shall not be applied to the inside diameter surface of the adjusting rings. Smearing of mortar on the inside of the adjusting rings will be cause for rejection of the work. When adjusting rings vary in thickness (2 in. & 4 in.) the larger ring (4 in.) shall be placed on top, directly under the frame. 1) New Manholes: New Manhole barrels and cone sections shall be manufactured to a tolerance that provides from two (2) to eight (8) inches of vertical adjustment between the top of
the cone and the bottom of the frame. Vertical adjustments, between the top of the cone and the bottom of the frame,
greater than eight (8) inches shall be accomplished by installing a new appropriately sized manhole barrel section.
Rings shall be vertically aligned to be straight with the top of the cone section without any offset. 2) Existing
Manholes: Existing manhole frames and lids may be adjusted to grade by adding additional adjusting rings. The vertical adjustment between the top of the cone and the bottom of the frame however shall not exceed 18 inches. Vertical
adjustments, greater than 18 inches shall be accomplished by installing a new appropriately sized manhole barrel section. Rings shall be vertically aligned to be straight with the top of the cone section and with each other without any offset. Steel adjusting rings that are inserted into the existing frame and allow the cover to be raised are not permitted. All manhole adjustments shall be done as specified above. b. Chimney Seal: Unless pre-approved by the Engineer, manhole chimney seals shall be installed in all cases. Whether an existing manhole is adjusted or a new manhole is installed, the manhole chimney shall be sealed. All manhole chimneys shall be sealed using a Manhole Internal Frame Seal. The seal shall be installed according to the manufacturers recommendations and when properly installed will prevent the inflow of water
between the manhole cone and the frame and cover.
8. Coating for Concrete Manholes and Lift Stations Wet Wells: When indicated on the drawings or specifications a corrosion resistant interior grout liner shall be provided on manholes or lift station wet wells. The liner maybe field applied or applied at the manufacture’s site. The liner shall be “Earthcoat 400P Pipe Coating” as manufactured by Earthcoat International, Appleton, WI or equal specifically formulated for coating the interior of concrete manholes or wet wells
for corrosion protection. The material shall be applied as per manufacturer's recommendations. Manhole coating color shall
be as specified in Section 9.2 Materials.
H. Sewer Main Tests...
1. General: A visual inspection, a TV inspection, a leakage test, and a pipe deflection test shall be performed as
specified herein for all sewer mains and manholes as a condition of acceptance by the City. All tests shall be performed after backfill is complete but prior to any surface restoration.
2. Pre-Cleaning: Prior to testing newly installed sewer pipe, the Contractor shall remove all accumulated construction debris, rock, gravel, sand, silt, and other foreign matter from the sewer with an appropriately sized cleaning ball. The Contractor shall be responsible for all work necessary to make the sewer acceptable for usage including removal of all mud, silt, rocks, or blockages that make said sewer unacceptable for final acceptance and usage. Also included is all work necessary in the manholes and all cleanup work required prior to final acceptance. The City will not be responsible for cleaning lines prior to televising the sewer. In the event that the line is not acceptable for televising, due to the Contractor’s operations, the Contractor will be notified. It will be the Contractor’s responsibility to arrange to clean
the sewer and make it acceptable for the television work. If not cleaned in a timely manner, the City may cause to take any actions necessary and charge the Contractor one and a half (1 1 / 2) times the cost incurred.
3. Visual Tests: All newly installed sewer main pipe shall pass a visual, or "lamping", inspection by the Engineer, and a television inspection by the City Utility Maintenance Division. Straight alignment shall be checked either with lamping or with the laser beam. Lamping shall be conducted by viewing the pipe from inside a manhole to determine proper alignment.
The television inspection shall consist of viewing the inside of all sewer main pipe installed to determine proper
alignment, joining, properly installed service connections, infiltration, etc. The Contractor shall correct, at his own expense, any defects discovered because of lamping and/or televising the pipe. Both a visual and television inspection
shall be completed unless specified otherwise in the Detailed Specifications or on the Drawings. The expense of the initial television inspection and one additional reinspection will be borne entirely by the City. If defective workmanship of material or construction is noted, the Contractor at no expense to the City, shall correct the deficiency. The City will perform additional television inspections to review if the repairs were made properly and in accordance with the specifications. The expense of any additional television inspections beyond the initial inspection and one additional reinspection will be borne entirely by the Contractor. The Contractor shall be responsible for all related costs, including concrete or asphalt resurfacing if the street has been surfaced. The Contractor shall be required to repair all areas of infiltration and other deficiencies. The City may cause to take any actions necessary for any items not completed or
repaired in a timely manner and may charge the contractor one and a half (1 1 / 2) times the costs incurred. It is the Contractors responsibility to notify both the Engineer/City Inspector and Utility Maintenance that the sewer is ready for inspection. From the time initial notification that the sewer is ready to be inspected the Contractor shall allow the City at least two (2) weeks to perform the television inspection. Any surfacing started prior to televising the sewer and said sewer being accepted is at the Contractors own risk.
4. Leakage Tests: The Contractor shall conduct leakage testing of all newly constructed or reconstructed sewer mains. The Contractor shall furnish all necessary equipment and be responsible for conducting the leakage test in the presence of the Engineer and/or project Inspector. The preferred Leakage Test method is the “Low Pressure Air Test”, provided groundwater conditions allow it. Alternative leakage tests may be the “Ex-Filtration Test” if groundwater is less than 4 ft. above the top of pipe, or the “Infiltration Test” if groundwater is 4 ft. or more above the top of pipe. a. Low Pressure Air Test:
This is the preferred testing method. The Contractor may conduct low-pressure air testing of newly installed sewer mains in lieu of ex-filtration testing if the ground water is less than one (1) foot above the top of the finished sewer main at the lowest point of the test section as determined by construction records and/or test borings. The test shall conform to the procedures outlined in Uni-Bell Specification Uni-B-6-90 or latest, Recommended Practice for Low-Pressure Air Testing of Installed Sewer Pipe. The pressurizing equipment shall include a regulator or relief valve set no higher than nine (9) psig to avoid over-pressurization. Pipeline segments between manholes shall be tested separately. Mechanical or pneumatic
plugs shall be placed in the line at opposing manholes and each plug braced as a safety precaution. An aboveground air pressurizing device including shut-off valve, pressure-regulating valve, pressure relief valve, input pressure gage and
a continuous monitoring pressure gage shall be provided and connected to the test plug at one end. Separate hoses for introducing air and for monitoring air pressure shall be provided. The monitoring hose shall be equipped with two (2) accurate pressure gauges. The monitoring gages shall read in divisions of 0.1 psi with an accuracy of plus or minus
0.04 psi.
Procedure :
( 1 ) Clean the section of sewer line to be tested by flushing or other means prior to conducting the low-pressure air test. This cleaning serves to eliminate debris and produce the most consistent results.
( 2 ) Isolate the section of sewer line to be tested by inflatable stoppers or other suitable test plugs.
( 3 ) Connect the air hose to the inlet tap and portable air control source. The air equipment shall consist of necessary
valves and pressure gauges to control an oil-free air source and the rate at which air flows into the test section to
enable monitoring of the air pressure within the test section.
( 4 ) Low pressure air shall be introduced into the line until the internal pressure reaches four (4) psig, and the supply throttled to maintain four (4) psig for at least two (2) minutes. The supply shall then be shut off or disconnected. The pressure shall be allowed to drop to about three and one-half (3 1/2) psig at which time the timing shall commence and the time accurately measured for a one (1) psig pressure drop per table given below. If the test section fails to meet these requirements, the Contractor shall, at his own expense, determine the source of leakage, repair or replace all
deficiencies, and retest the installation until passing, all in a manner approved by the Engineer. This does not mean
that the Low Pressure Air Test has to be repeated but rather a passing test has to be achieved by either the Low
Pressure Air Test or the Ex-filtration Test.
( 5 ) Upon completion of the test, open the bleeder valve and allow all air to escape. Plugs should not be removed until
all air pressure in the test section has been reduced to atmospheric pressure.
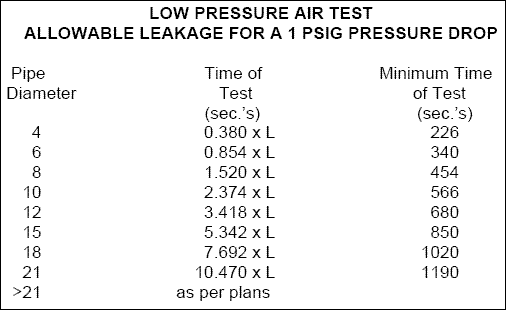
Use of table : The time of test shall be calculated using the formula presented in table. Time is in seconds and
L is in feet of pipe being tested. If the calculated time is less than the minimum time of test then the minimum test time shall govern. For example: a 200 ft. - 10 in. sewer would have a calculated time of 2.374 x 200 = 475 seconds. The minimum test time however is 566 seconds. Thus the minimum length of time for a 1 psig pressure drop would be 566 seconds not the calculated 475 seconds. If there has been no leakage (zero psig drop) after one hour of testing, the test section shall be accepted and the test considered.
d. Ex-filtration Test shall be used if groundwater is less than 4 ft. above the top of pipe as determined by construction records and/or test borings. The test shall be conducted in a manner approved by the Engineer and shall provide a minimum head of two (2) feet at the highest point in the test section, but no more than 10 feet of head at the lowest point, with head measured from top of pipe, except when the groundwater surface is above the pipe, in which case head shall be measured from the groundwater surface. Unless otherwise specified, the pipe shall not allow ex-filtration, of water, of more than 50 gallons per inch diameter per mile of pipe (50 gal./in./mi.) in any 24-hour period as per table given below.
The minimum test period shall be for two (2) hours and the values derived from table given below will need to be adjusted
for the actual test time. If the test section fails to meet these requirements, the Contractor shall, at his own expense, determine the source of leakage, repair or replace all deficiencies, and retest the installation until passing, all in a manner approved by the Engineer. This does not mean that the Ex-filtration test has to be repeated but rather a passing test has to be achieved by either the Ex-filtration Test or the Low Pressure Air Test. It is not recommended to conduct the pipe leakage test concurrently with the manhole ex-filtration test, as the allowable parameters for head (H) in the two tests differ. However, a separate manhole ex-filtration test will not be required when manholes are tested simultaneously with
the sewer pipe ex-filtration test. The Contractor shall anticipate the need to conduct multiple tests in order to meet the above requirements and shall conduct testing in such a manner and sequence that the requirements indicated above are achieved. Water used to test ex-filtration shall be clean potable water and will not be allowed to discharge to the sewer system. Such water shall be pumped from the system and discharged at an approved location.
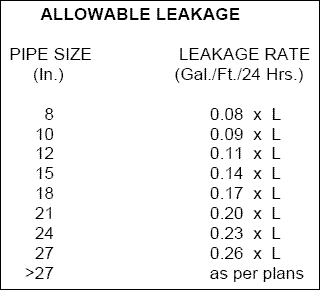
Use of table : The length of time for the test in the table is given as a 24-hour period and will need to be adjusted for the actual test time. The allowable leakage shall be calculated using the formula presented in table and L is in feet of pipe being tested. It is not recommended to conduct the pipe leakage test concurrently with the manhole ex-filtration test, as the allowable parameters for head (H) in the two tests differ. If the Contractor wishes to concurrently test the pipe and manhole then 4th table may be used to assist in measuring the pipe loss for a concurrent test. For example the calculated loss for 350 ft. - 12 in. sewer would be 0.11 x 350 = 38.5 gals in a 24-hour period. To adjust this loss to the actual test time or if a manhole test is being conducted concurrently the 38.5 gals would need to be converted, to say, two (2) hours; then (38.5 / 24 hrs) x 2 hrs = 3.2 gals. The 3.2 gals would be the permitted loss or if testing concurrently would have to be added to the loss calculated for the manhole.
c. Infiltration Test shall be used if ground water is four (4) feet or more above the top of the finished sewer main at the highest point of the test section as determined by construction records and/or test borings. Test methods and infiltration measurements shall be conducted in a manner approved by the Engineer. The allowable leakage from the pipe shall not exceed that set for Ex-Filtration in 2nd table. The minimum test period shall be for two (2) hours and the table values will need to be adjusted to accommodate for the actual test time. If the test section fails to meet these requirements, the Contractor shall, at his own expense, determine the source of leakage, repair or replace all deficiencies, and retest the installation until passing, all in a manner approved by the Engineer. This does mean that the Infiltration test has to be repeated as the other test methods would not be permitted because of the groundwater conditions.
5. Pipe Deflection Test : Deflection tests shall be performed by the Contractor on all PVC sewers. Deflection tests
shall be conducted after the final backfill has been in place at least 30 days. Deflection tests shall be made using a deflection gauge (mandrel) device or other approved method. The diameter of the deflection gauge device shall be 95% of
the undeflected inside diameter of the flexible pipe. The deflection test shall be performed without mechanical pulling devices. The Contractor shall be required to install the pipe in such a manner so that the diametric deflection of the pipe shall not exceed five (5) percent. All pipes exceeding the five (5) percent deflection within the two-year warranty period shall be re-laid or replaced by the Contractor at no additional cost to the Owner.
I. Manhole Tests...
General: Manhole tests shall be performed on all newly installed manholes and on existing manholes where new sewer main connections have been made. The preferred Manhole Leakage Test method is the “Manhole Vacuum Test” rather than the “Ex-Filtration Test”.
1. Visual Test : The project Engineer/Inspector will visually inspect each manhole exterior and interior for flaws,
cracks, holes, or other deficiencies, which may affect the operation or watertight integrity of the manhole. Should any deficiencies be discovered, the Contractor shall correct them to the satisfaction of the Engineer and at no cost to the Owner.
2. Manhole Vacuum Test shall be performed in accordance with ASTM C1244. The following procedure is summarized
from ASTM C1244 and shall be followed in conjunction with ASTM C1244 unless modified by the Engineer. The vacuum test
shall include testing the top of the manhole, excluding the adjusting rings and manhole frame and cover. Testing will be allowed after backfilling has occurred, manhole vacuum tester assembly and vacuum pumps shall be as manufactured by Cherne Industries, Inc. or approved equal. Repair of leaks may require the removal and replacement of manhole sections. The use
of grout to repair leaks will not be allowed.
Procedure :
a. All lift holes shall be plugged. b. All pipes entering the manhole shall be temporarily plugged, taking care to securely brace the pipes and plugs to prevent them from being drawn into the manhole. c. The test head shall be placed at the top of the manhole in accordance with the manufacturer’s recommendations. d. A vacuum of 10 in. of mercury shall be drawn on the manhole and then the vacuum line shall be throttled to maintain the 10 in vacuum for at least two (2) minutes. After the two minutes the valve on the vacuum line of the test head shall be closed, and the vacuum pump shut off. The time shall then be measured for the vacuum to drop to 9 in. of mercury. e. The manhole shall pass if the time for the vacuum reading to drop from 10 in. of mercury to 9 in. of mercury meets or exceeds the values indicated in table given below. f. Two (2) accurate vacuum pressure test gauges shall be installed to monitor the test. g. If the manhole fails the initial test, necessary repairs shall be made by an approved method. The manhole shall then be retested until a satisfactory test is obtained. This does not mean that the Manhole Vacuum Test has to be repeated but rather a passing test has to be achieved by either the Manhole Vacuum Test or the Ex-filtration Test.
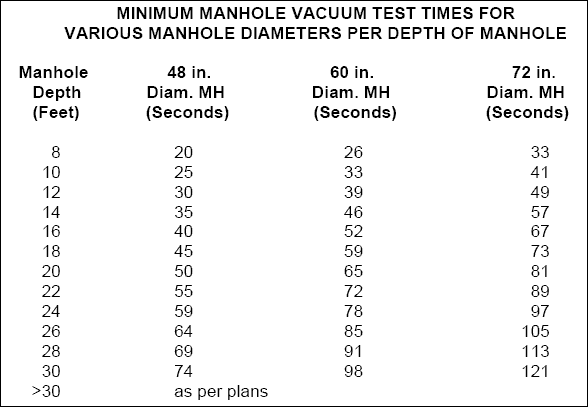
3. Ex-filtration Test : The Contractor shall furnish all necessary equipment and materials and shall be responsible for conducting, in the presence of the Engineer/Inspector, an ex-filtration test on each manhole. A separate manhole ex-filtration test will not be required when the manhole is tested simultaneously with the sewer pipe during an
ex-filtration test. It is not recommended to conduct the pipe leakage test concurrently with the manhole ex-filtration
test, as the allowable parameters for head (H) in the two tests differ. However, a separate manhole ex-filtration test
will not be required when manholes are tested simultaneously with the sewer pipe ex-filtration test. If the Contractor
wishes to concurrently test the pipe and manhole then Table 9–2 may be used to assist in measuring the pipe loss for a concurrent test. The manhole shall not allow ex-filtration of water of more than 0.10 gallons per hour per foot diameter
per foot head (0.10 gal/hr/ft dia/ft head) with head being measured from the top of the water surface in the test manhole
to groundwater level outside the manhole or to the bottom of the manhole, whichever is less. All pipes leading into or
out of the manhole shall be plugged to provide a watertight seal and the manhole filled with water to a level three (3) to four (4) inches below the casting rim or lid. The water shall be allowed to stand for two (2) hours prior to beginning the test to allow for absorption into the manhole. If the water has dropped at the end of the two (2) hour stabilization period, additional water shall be added to bring the water level to at least three (3) to four (4) inches below the casting rim or lid, as initially was done. If the head is greater than 30 feet refer to the plan drawings for ex-filtration testing requirements. The minimum test period shall be for two (2) hours and the values derived from Table 9–4 will need to be adjusted for the actual test time. If the test fails to meet these requirements, the Contractor shall, at his own expense, determine the source of leakage, repair or replace all deficiencies, and retest the installation until passing, all in a manner approved by the Engineer. This does not mean that the Ex-filtration test has to be repeated but rather a passing
test has to be achieved by either the Ex-filtration Test or the Manhole Vacuum Test. The Contractor shall anticipate the
need to conduct multiple tests in order to meet the above requirements and shall conduct testing in such a manner and sequence that the requirements indicated above are achieved. Water used for ex-filtration testing shall be clean, potable water and shall not be discharged into the sewer system. Such water shall be pumped from the manhole being tested and discharged at an approved discharge site.
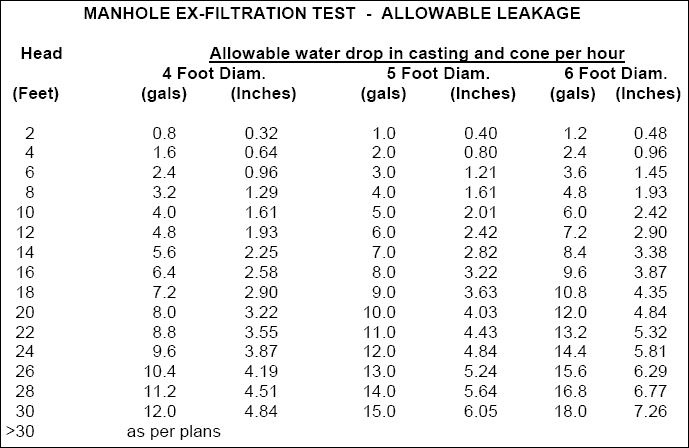
Use of table : Example of a concurrent manhole and pipe ex-filtration test : Given : 370 ft. of 10 in. sewer, groundwater approximately 2 ft. above the pipe invert at the manhole being tested, the manhole is 5 foot in diameter
and the manhole is 17 ft. deep from rim to invert. The calculated pipe loss for 370 ft. – 10 in. sewer would be (from
table 2) 0.09 x 370 = 33.3 gals in a 24-hour period. To adjust this loss to coincide with the manhole test the 33.3 gals would need to be converted, to two (2) hours; so (33.3 / 24 hrs) x 2 hrs = 2.78 gals. The 2.78 gals is the permitted loss
for the pipe in 2 hours. The calculated manhole loss for a 5 foot diameter manhole 17 feet deep with groundwater 2 ft.
above the invert would be (from table 4) 17’ – 2’ = 15’ H, round H down to 14 ft., the corresponding valve from the 5 ft. Diam. Column results in a manhole loss of 7.0 gals. per hour. This value then needs to be converted to a two hour test.
So 7.0 gals x 2 = 14 gals for two hours. The combined total loss would be 2.78 gals. (pipe) + 16 gals. (manhole) = 16.78 gals. This loss can be measured in inches of water surface drop in the cone by converting the gals in Table 9-4 to inches. The 7.0 gals. = 2.82 inches of drop, therefore 16 gals of loss equals 2 x 2.82 inches = 5.64 inches. The 2.78 gals. would
be rounded down to 2.0 gals, which is equivalent to a 0.80 inch drop. Therefore the total water surface drop for a two
hour test would be 5.64” + 0.80” = 6.44”. Another option instead of measuring the surface water drop would be to measure
the volume of water required to bring the water surface back to the original level, at the start of the test. In order to achieve a passing test the volume of water needed to fill the cone would have to be less than 16.78 gals.
J. Abandoning Sanitary Sewer Mains and Manholes...
1. Existing Sewer Mains to be abandoned between manholes shall be plugged at all open ends with concrete extending into
the abandoned pipe one foot or one pipe diameter, whichever is greater. Existing sewers to be abandoned at a manhole shall
be cut flush with the inside of the manhole and plugged as specified above. The pipe shall be grouted flush with the inside of the manhole and the manhole invert shall then be reconstructed. The reconstructed manhole inverts shall provide for the new flow scheme and comply with the standards for manhole inverts, as specified. The completed manhole shall be watertight and the inverts shall be smooth and uniform.
2. Existing Manholes to be abandoned shall have all pipes plugged with concrete extending into the abandoned pipe one
foot or one pipe diameter, whichever is greater. The upper 4 ft. of the manhole shall be broken or removed and the manhole filled with compacted Select Granular Backfill material. The Contractor shall not backfill manholes to be abandoned until
the Engineer/Inspector has inspected each plug. Unless shown otherwise on the Drawings or specified in the Detailed Specifications, the Contractor shall salvage manhole frames and covers and deliver to and unload them at the City
Utility Maintenance Shop on Steele Avenue.
K. Service Lines...
1. Permits, obtainable from the City Utility Maintenance Division, are required for all connections to the Rapid City
sewer system. Applicants must hold a City Sewer & Water Installer Contractor's License. Refer to Section 11.
2. Horizontal distance between sewer service and water service lines shall not be less than ten (10) feet.
3. Service pipe shall be laid at a minimum slope of 1/8 inch per foot or as per plans. Minimum depth of cover over service lines shall be 3 1/2 feet.
4. Cleanouts shall be installed at all changes in horizontal alignment of greater than 45 degrees and at distances not to exceed 75 feet for four (4) inch diameter pipe and 100 feet for six (6) inch diameter pipe.
5. Insulation for sewer services, when shown on the Drawings, shall be as specified for sewer mains.
6. Sewer Service New Connections : Where new service lines are to be installed for undeveloped property or future buildings, the Contractor shall furnish all materials necessary for connection of new service lines to the sewer main, except saddles which will be furnished and installed by the City, and shall obtain and pay permits and tapping fees as established by Ordinance. In-line tees may be used in lieu of saddles for 4 inch and 6 inch service lines. The use of an in-line service
tee does not waive any tapping fees or the City inspection requirements. In-line tees shall be furnished and installed by the Contractor as the sewer main is installed. New service connections and lines shall be, at a minimum, extended to the property line and the service line capped. The termination point shall be marked with a minimum three (3) foot long steel fence post. The steel fence post shall be buried below the surface at least eight (8) inches and needs to be steel to facilitate location by magnetic locators. City personnel shall tap all City sewer mains. The Contractor shall schedule all service taps between 7:30 AM to 3:00 PM, Monday through Friday.
7. Sewer Service Reconnections : The Contractor shall furnish all materials necessary for reconnecting service lines
existing prior to reconstruction of a sewer main, except saddles, which will be furnished and installed by the City.
On City projects all permits and tapping fees will be waived; however the Contractor shall obtain a no-charge "Right
to Work" permit from the City Utility Maintenance Division. In-line tees may be used in lieu of saddles for 4 inch and
6 inch service lines. The use of an in-line service tee does not waive any tapping fees or the City inspection requirements. In-line tees shall be furnished and installed by the Contractor as the sewer main is installed. In-line tees may be used
in lieu of saddles for 4 inch and 6 inch service lines. If a bid item is not provided for the in line sewer service tees,
the Contractor with the Engineers approval, may substitute in-line service tees for saddles. The substitution of tees for saddles is a “no-cost” substitution and does not waive any tapping fees or the City inspection requirements. If a bid item for in-line sewer service tees is provided, the Contractor shall use the tees in place of saddles and the payment will be made at the unit price bid for in-line sewer service tees furnished and installed, including all labor and material. On non-city projects the new account set-up / inspection permit (tap permit) will be waived, however the Right-to-Work permit and tapping fees are still applicable. The Contractor shall visually inspect the inside of each existing sewer service line to be connected to the new sewer main prior to making the reconnection. When it is discovered that an existing sewer service line beyond the edge of the excavation is not in good physical condition or is plugged, full of roots, or is otherwise not operating properly, the Contractor shall notify the Engineer so he may document the condition and notify the property owner. Connections between the new service line and existing service line shall be accomplished with a Fernco-type coupling. The Contractor shall encase the Fernco connection in six (6) inches of concrete six (6) inches each side of the coupling. City personnel shall tap all City sewer mains. The Contractor shall schedule all service taps between 7:30 AM to 3:00 PM, Monday through Friday.
8. Abandoning of service lines shall be accomplished by cutting and plugging the line at the sewer main unless directed otherwise by the Engineer. The service line shall be plugged in the same manner as specified for plugging sewer mains.
9. Inspection : All sewer service installations and abandonment’s shall be inspected by the City Utility Maintenance Division, prior to backfilling. The Contractor shall notify the City Utility Maintenance Division a minimum of four (4)
hours prior to the time he wants the inspection. Any trench backfilled without being inspected and approved by authorized City personnel shall be re-excavated by the Contractor to expose the work for the required inspection. Discrepancies shall
be corrected by the Contractor and re-inspected by City personnel.
10. Tracer wire : Tracer wire shall be installed along with all sewer lines as described below: The tracer wire shall be extended with the service line. The wire shall be installed along the top of the pipe and shall be securely anchored to
the pipe every 4 feet horizontally with an adhesive tape. The tracer wire shall be brought to the surface at each clean
out and shall terminate at the service connection point on the main. At locations where the service line is not being replaced entirely, the Contractor will splice the new tracer wire to the existing tracer wire at the point of reconnection. In instances where a service line is not being replaced entirely and the existing tracer wire is not encountered, the Contractor shall coil approximately five feet of wire at the reconnection location(s) to facilitate a future splice. All tracer wire connections shall be accomplished with “pig-tails.” All splices and “pig-tails” shall be accomplished by stripping the wires to be connected, twisting the wires together, securing the connections by using an appropriately sized wire nut, and preserving the splice or “pig-tail” by using a direct bury splice kit.
Tracer Wire System:
Tracer Wire shall be a direct bury wire that meets or exceeds the following requirements: a. Conductor: 12 AWG solid strand soft drawn copper per ASTM B-3, or B-8. The breaking pounds of the wire shall be a minimum of 124 with an O.D. of 0.154. All wire shall be spark tested at 7500 VAC. b. Insulation: Conductor shall be insulated with low density high molecular weight polyethylene insulation suitable for direct bury applications per ASTM D-1248. The minimum insulation thickness shall be 0.045. The color of the insulation shall be green with a print line saying “SEWER”. c. Splices and or Connectors: Splices
and or Connectors should be capable of handling from 2 to 4 wires per connector and designated as “water-proof”. PVC adhesives or sealing compounds are not acceptable.
Method of Measurement...
A. Sewer Main Pipe : Installed pipe quantities shall be measured from centerline to centerline of all manholes and special items to the nearest even foot. Depth of pipe shall be determined from top of finish grade to flow line of pipe. Standard depth is 0-6 feet and extra depth, if so bid, shall be in increments of two (2) feet.
B. Sewer Service Pipe : Installed pipe quantities shall be measured from edge of sewer main pipe to fittings or end of pipe to the nearest even foot.
C. Standard Manhole, Shallow Manhole, and Drop Manhole, 0-6 feet, shall be measured on a per each basis for the type and diameter of the particular manhole.
D. Extra Manhole Depth per diameter of manhole being installed shall be measured to the nearest one tenth (0.1) foot from
the top of finish grade to the invert of the manhole minus the nominal six (6) foot depth measured under Standard Manhole, Shallow Manhole, and Drop Manhole.
E. Abandon Sewer Mains : No separate measurement will be made for plugging abandoned sewer mains; such work shall be incidental to the project, unless otherwise specified.
F. Abandon Manhole: Measurement will be made on a per each basis for each manhole abandoned.
G. Sewer Main Encasement : Measurement will be made on a per each basis for each encased crossing with lengths as noted on the Drawings.
H. Insulation : Measurement will be made on a square foot basis to the nearest square foot.
I. Sewer Service Connections and Reconnections: Sewer service reconnections and sewer service new connections will be
counted on a per each basis. Saddles will be furnished and installed by the City. The pipe used for connections and reconnections shall be measured and paid for under the bid item for sewer service pipe. In-line tees may be used in lieu
of saddles for 4 inch and 6 inch service lines. If a bid item is not provided for the in-line sewer service tees, then
the Contractor, with the Engineer’s approval may substitute in-line tees for saddles. The substitution of tees for saddles
is a “no cost” substitution and does not waive any of the tapping fees or the City inspection requirements. If a bid item
for in-line sewer service tees is provided, then the Contractor shall use the tees in place of saddles and the tees will
be counted on a per each basis.
J. Adjust Manhole Frame and Cover : Measurement will be made on a per each basis for each manhole frame and cover adjusted. The addition of or removal of cone or barrel sections required for adjustment will be measured and paid for as Reconstruct Manhole.
K. Reconstruct Manhole : Measurement will be made on a per each basis for each manhole reconstructed. Reconstruct Manhole consists of the removal of or the addition of a new manhole barrel(s) or cone(s) for vertical adjustment. Adjustments of
the frame and cover not associated with the addition of or removal of a barrel or cone shall be measured and paid for as Adjust Manhole Frame and Cover.
L. Reshape Manhole Invert : Measurement will be made on a per each basis for each manhole that has the invert(s) reshaped
and reconstructed.
M. Sanitary Sewer Caps/Plugs : Measurement will be made on a per each basis for each cap/plug installed.
N. Sanitary Sewer Cleanouts : Measurement will be made on a per each basis for each type and size of cleanout installed.
O. Abandon Cleanout : Measurement will be made on a per each basis for each cleanout abandoned.
P. Connection to Existing Manhole : Measurement will be made on a per each basis for each connection to an existing manhole.
Q. Remove Manhole : Measurement will be made on a per each basis for each manhole removed.
R. Remove Sewer Main : Measurement will be made on a linear foot basis and shall be measured to the nearest foot.
S. Connection to Existing Sewer Main : Measurement will be made on a per each basis for each connection to an existing
sewer main.
T. In-line Sewer Service Tee : Measurement will be made on a per each basis for each in-line sewer service tee, except as covered under the provisions for “Sewer Service Connections and Reconnections.”
U. Tracer Wire : Tracer wire and all accessory items necessary for the installation of tracer wire shall be considered incidental to the sewer service pipe installation.
Basis of Payment...
A. Sewer Main Pipe : Payment will be at the unit price bid for the appropriate size and depth of sewer pipe, furnished and installed, including wastewater flow modifications, diversions, and/or pumping, trenching, excavation, Type 1 bedding material, backfilling, dewatering, sheeting or shoring, tracing wire, compaction, testing, and connections, if any, between the new main and existing main.
B. Sewer Service Pipe : Payment will be made at the unit price bid for the appropriately sized pipe, furnished and installed, including trenching, excavation and backfilling, dewatering, tracing wire, and sheeting or shoring. The cost for any connections between the new service line and existing service lines shall be included in the unit price bid for the appropriate sized pipe.
C. Standard Manhole and Standard Shallow Manhole : 0-6 feet, Payment will be made at the unit price bid for each type and diameter, furnished and installed including adjusting rings, frame and cover. Extra payment may be allowed for bolt-down watertight frame and cover, if so specified as a bid item on the Bid Proposal. The extra payment will be the difference in cost between standard frame and cover and bolt-down frame and cover.
D. Drop Manhole : 0-6 feet, Payment will be made at the unit price bid for each diameter, furnished and installed, with adjusting rings, frame and cover. Price bid shall include the wye and the pipe installed from the wye to the floor of the manhole. No separate payment will be made for this pipe, wye, and bend. Extra payment may be allowed for bolt-down
watertight frame and cover, if so specified as a bid item on the Bid Proposal. The extra payment will be the difference
in cost between standard frame and cover and bolt-down frame and cover.
E. Extra Manhole Depth : Payment shall be made at the unit price bid for that depth, per the appropriate manhole diameter, over and above the six (6) foot, which is paid for as Standard Manhole, Shallow Manhole, and Drop Manhole.
F. Abandon Sewer Mains : Payment for plugging abandoned sewer mains shall be incidental to the project, unless otherwise specified.
G. Abandon Manhole : Payment will be at the bid unit price and shall include all labor, materials, including concrete plugs, and granular backfill.
H. Sewer Main Encasement : Payment will be at the unit price bid, furnished and installed, including materials, temporary blocking and restraint of pipe, and incidental necessary to complete the work.
I. Insulation : Payment will be at the unit price bid for insulation furnished and installed, including cushion material.
J. Sewer Service New Connection : Payment will be made at the unit price bid for connecting new sewer services to the sewer main, including fittings necessary to connect the service line to sewer. Saddles will be furnished and installed by the
City. Sewer service pipe will be paid for separately. Payment for Sewer Service New Connection shall include Right to Work permit, New Account Setup/Inspection permit (tap permit) and tapping fees, unless otherwise specified in the Detailed Specifications, including all labor and material. In-line tees may be used in lieu of saddles for 4 inch and 6 inch service lines. If a bid item is not provided for the in line sewer service tees, the Contractor with the Engineers approval, may substitute in-line service tees for saddles. The substitution of tees for saddles is a “no-cost” substitution and does not waive any tapping fees or the City inspection requirements. If a bid item for in-line sewer service tees is provided, the Contractor shall use the tees in place of saddles and the payment will be made at the unit price bid for in-line sewer service tees furnished and installed, including all labor and material.
K. Sewer Service Reconnection : Payment will be made at the unit price bid for reconnecting existing sewer services to the sewer main, including fittings necessary to connect the service line to sewer. Saddles will be furnished and installed by
the City. Sewer service pipe will be paid for separately. In-line tees may be used in lieu of saddles for 4 inch and 6 inch service lines. If a bid item is not provided for the in line sewer service tees, the Contractor with the Engineers approval, may substitute in-line service tees for saddles. The substitution of tees for saddles is a “no-cost” substitution and does not waive any tapping fees or the City inspection requirements. If a bid item for in-line sewer service tees is provided,
the Contractor shall use the tees in place of saddles and the payment will be made at the unit price bid for in-line sewer service tees furnished and installed, including all labor and material On City projects all permits and tapping fees will
be waived. On non-City projects the New Account Setup/Inspection permit will be waived, however the Right-to-Work permit
and tapping fees are still applicable.
L. Adjust Manhole Frame and Cover : Payment will be at the unit price bid for adjusting manhole frame and cover including adjusting rings.
M. Reconstruct Manhole : Payment will be made at the unit price bid for Reconstruct Manhole including new manhole barrel(s) and cones or removal of manhole barrel(s) and cone.
N. Reshape Manhole Invert : Payment will be at the unit price bid for reshaping existing manhole inverts, including all materials, labor, equipment, wastewater flow diversions, modifications, and/or pumping.
O. Sanitary Sewer Caps / Plugs : Payment will be at the unit price bid for Sanitary Sewer Cap/Plug furnished and installed, including all labor and materials.
P. Sanitary Sewer Cleanouts : Payment will be at the unit price bid for Sanitary Sewer Cleanout furnished and installed, including all labor and materials.
Q. Abandon Cleanout : Payment will be at the unit price bid and shall include all labor, materials, including concrete
plugs, and backfill.
R. Connection to Existing Manhole : Payment will be at the unit price bid and shall include all labor and materials.
S. Remove Manhole : Payment will be at the unit price bid and shall include all labor, materials, including concrete plugs, and backfill.
T. Remove Sewer Main : Payment will be at the unit price bid and shall include all labor, materials, including concrete plugs, and backfill.
U. Connection to Existing Sewer Main : Payment will be at the unit price bid and shall include all labor and materials.
V. In-line Sewer Service Tees : Payment will be Made at the unit price bid for “In-line Sewer Service Tee” furnished and installed, including all labor and material, except as covered under the provisions for “Sewer Service New Connections and Sewer Service Reconnections.”
W. Tracer Wire : Tracer wire and all accessory items necessary for the installation of tracer wire shall be considered incidental to the sewer service pipe installed.